How Do CNC Machines Work?
CNC machines have revolutionized the manufacturing industry, bringing unprecedented precision, efficiency, and versatility to the production process. These remarkable devices have transformed the way we create everything from simple components to complex aerospace parts. In this comprehensive guide, we’ll explore the inner workings of CNC machines, demystifying their operation and shedding light on the technology that powers modern manufacturing.
The Basics of CNC Machining
CNC stands for Computer Numerical Control, a method of automating machine tools using computers executing pre-programmed sequences of commands. This technology allows for the creation of parts with a level of accuracy and repeatability that would be nearly impossible to achieve manually.
At its core, CNC machining is a subtractive manufacturing process. This means that material is removed from a workpiece to create the desired shape, unlike additive processes like 3D printing. The CNC machine follows a set of instructions, known as G-code, to control the movement of cutting tools and the workpiece.
Components of a CNC Machine
To understand how CNC machines work, let’s break down their key components:
- Machine Structure: The frame and moving parts that provide stability and motion.
- Spindle: The rotating component that holds and spins the cutting tool.
- Cutting Tools: Various types of tools used to remove material.
- Workholding Devices: Clamps, vises, or fixtures that secure the workpiece.
- Motors and Drives: Provide movement to the machine’s axes.
- Control System: The “brain” of the machine, interpreting and executing commands.
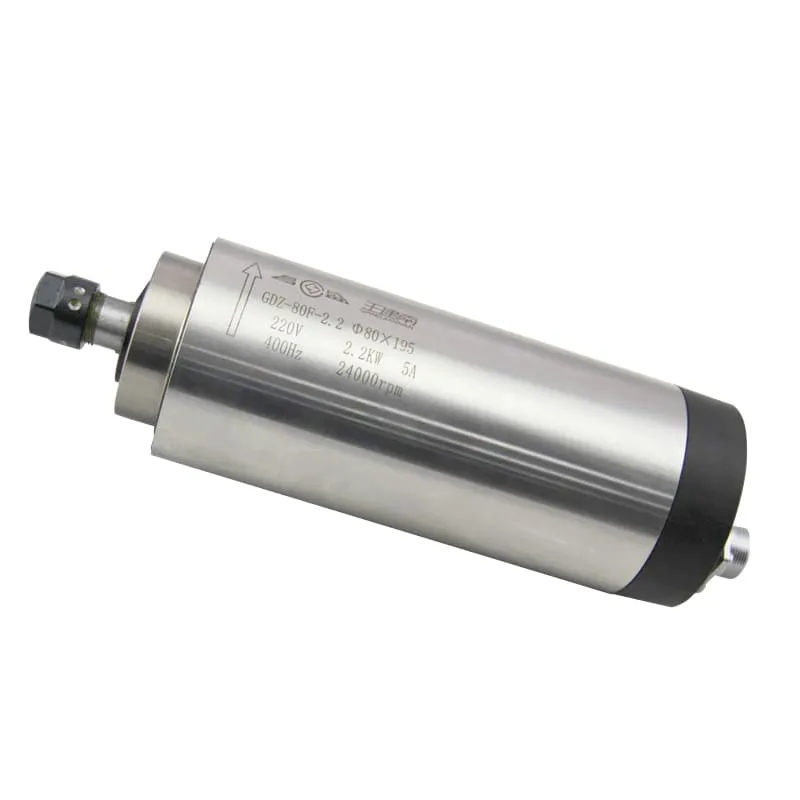
The spindle is a crucial component in CNC machines. High-performance spindles, like the 2.2KW ER16 Air-Cooled Spindle, can achieve speeds up to 24,000 RPM, enabling precise and efficient cutting operations.
The CNC Machining Process
Now that we’ve covered the basic components, let’s walk through the CNC machining process step by step:
- Design: The process begins with a 3D CAD (Computer-Aided Design) model of the part to be machined.
- CAM Programming: The CAD model is imported into CAM (Computer-Aided Manufacturing) software, where toolpaths are generated.
- G-code Generation: The CAM software converts the toolpaths into G-code, the language CNC machines understand.
- Machine Setup: The workpiece is secured, tools are loaded, and the program is transferred to the machine.
- Machining: The CNC controller reads the G-code and directs the machine’s movements to cut the part.
- Quality Control: The finished part is inspected to ensure it meets specifications.
Types of CNC Machines
CNC technology has been applied to a wide variety of machine tools. Some common types include:
- CNC Mills: Used for cutting and drilling operations on flat and irregular surfaces.
- CNC Lathes: Ideal for creating cylindrical parts through turning operations.
- CNC Routers: Often used for woodworking and sign-making.
- CNC Plasma Cutters: Used for cutting metal sheets and plates.
- CNC Grinders: For precision grinding of various materials.
Each type of CNC machine is suited for different applications and materials. For instance, a 24000RPM 3KW ER20 Water-Cooling Spindle might be used in a high-speed CNC mill for machining aluminum aerospace components.
The Role of the Control System
The control system is the heart of a CNC machine. It interprets the G-code and translates it into precise movements of the machine’s axes. Modern CNC controllers are essentially specialized computers with features like:
- Real-time motion control
- Tool management
- Error compensation
- Network connectivity for program transfer and monitoring
These advanced controllers allow for complex operations like simultaneous 5-axis machining, where the tool or workpiece can move in five different axes at once.
Cutting Tools and Their Impact
The choice of cutting tool significantly affects the machining process. Different tools are designed for specific materials and operations. Some common types include:
- End mills
- Drill bits
- Turning tools
- Grinding wheels
- Taps and dies
The material, geometry, and coating of the tool all play a role in its performance. For high-speed machining applications, tools paired with spindles like the 60000RPM 300W ER8 Water-Cooled Spindle can achieve incredible cutting speeds and surface finishes.
Precision and Accuracy in CNC Machining
One of the key advantages of CNC machining is its ability to produce parts with extremely tight tolerances. This precision is achieved through:
- Rigid machine construction
- High-quality bearings and guideways
- Precision measuring systems (encoders)
- Thermal compensation
- Advanced control algorithms
Modern CNC machines can achieve tolerances as tight as ±0.0001 inches (2.54 micrometers) under ideal conditions.
The Importance of Proper Workholding
Secure workholding is crucial for achieving precise results in CNC machining. Common workholding methods include:
- Vises
- Clamps
- Vacuum tables
- Magnetic chucks
- Custom fixtures
The choice of workholding method depends on the part geometry, material, and machining operations to be performed.
CNC Programming Methods
There are several ways to program CNC machines:
- Manual Programming: Writing G-code by hand (rare in modern manufacturing).
- Conversational Programming: Using a simplified interface on the machine control.
- CAM Software: Generating toolpaths from 3D models (most common method).
- Macro Programming: Creating reusable subroutines for complex or repetitive operations.
Advanced CAM software can optimize toolpaths for efficiency and tool life, significantly reducing machining time and costs.
The Role of Simulation in CNC Machining
Before running a CNC program on the actual machine, it’s common to simulate the operation. This allows programmers to:
- Verify toolpaths
- Check for collisions
- Optimize cutting strategies
- Estimate machining time
Simulation can prevent costly errors and improve the efficiency of the machining process.
Advanced Features of Modern CNC Machines
Today’s CNC machines incorporate advanced features that enhance productivity and quality:
- Automatic Tool Changers: Allow for uninterrupted machining of complex parts.
- Probing Systems: Enable in-process measurement and quality control.
- Adaptive Control: Adjusts cutting parameters in real-time based on sensor feedback.
- Multi-Tasking Capabilities: Combining multiple machining operations in a single setup.
For example, a 24000RPM 7.5KW ER32/40 Water-Cooling Spindle might be used in a multi-tasking machine capable of both milling and turning operations.
Applications of CNC Machining
CNC machining is used across a wide range of industries, including:
- Aerospace
- Automotive
- Medical devices
- Electronics
- Oil and gas
- Defense
- Consumer products
The versatility of CNC machines allows them to produce everything from tiny electronic components to large aircraft parts.
Challenges in CNC Machining
While CNC machining offers many advantages, it also comes with challenges:
- Programming Complexity: Creating efficient toolpaths for complex parts can be time-consuming.
- Tool Management: Selecting and managing cutting tools for optimal performance.
- Vibration and Chatter: Can affect surface finish and tool life.
- Thermal Effects: Temperature changes can impact machining accuracy.
- Chip Control: Proper chip evacuation is crucial for consistent cutting.
Addressing these challenges often requires a combination of experience, advanced technology, and continuous improvement processes.
The Future of CNC Machining
The field of CNC machining continues to evolve, with several exciting trends on the horizon:
- Artificial Intelligence: Machine learning algorithms optimizing cutting parameters and predicting maintenance needs.
- Internet of Things (IoT): Connected machines sharing data for improved efficiency and quality control.
- Hybrid Manufacturing: Combining additive and subtractive processes in a single machine.
- Sustainable Practices: Developing more energy-efficient machines and processes.
As these technologies mature, we can expect even greater precision, efficiency, and capability from CNC machines.
FAQs
1. How does a CNC machine differ from a manual machine tool?
A CNC machine is controlled by a computer executing pre-programmed instructions, allowing for precise, repeatable movements. Manual machines rely on human operators to control the cutting process, which can be less accurate and more time-consuming.
2. What materials can be machined using CNC machines?
CNC machines can work with a wide range of materials, including metals (steel, aluminum, titanium), plastics, composites, wood, and even some ceramics. The choice of material often dictates the type of cutting tools and machining parameters used.
3. How long does it take to create a part using CNC machining?
The time to create a part varies greatly depending on its complexity, size, material, and the specific CNC machine used. Simple parts might be completed in minutes, while complex components could take hours or even days.
4. Can CNC machines work unattended?
Many modern CNC machines are designed for lights-out or unattended operation. With proper setup, tool management systems, and monitoring capabilities, they can run for extended periods without direct human supervision.
5. How accurate are CNC machines?
High-end CNC machines can achieve tolerances as tight as ±0.0001 inches (2.54 micrometers) under ideal conditions. However, typical tolerances for most applications range from ±0.001 to ±0.005 inches.
6. What is the difference between 3-axis and 5-axis CNC machining?
3-axis CNC machines move the cutting tool or workpiece along three linear axes (X, Y, and Z). 5-axis machines add two rotational axes, allowing for more complex geometries to be machined in a single setup.
Conclusion
CNC machines have transformed manufacturing, enabling the production of complex, high-precision parts with efficiency and repeatability. From the intricate dance of the spindle and cutting tools to the sophisticated control systems that guide their movements, these machines represent the pinnacle of modern manufacturing technology.
As we’ve explored, the world of CNC machining is vast and complex, encompassing a wide range of machine types, cutting tools, and programming methods. The continuous evolution of CNC technology promises even greater capabilities in the future, with advancements in artificial intelligence, connectivity, and hybrid manufacturing pushing the boundaries of what’s possible.
Whether you’re a seasoned machinist, a curious engineer, or someone considering CNC machining for your next project, understanding how these remarkable machines work is the first step towards harnessing their full potential. As CNC technology continues to advance, it will undoubtedly play an ever-increasing role in shaping the products and technologies that define our world.