How to Clean an Impeded Water-Cooled Spindle Motor: A Comprehensive Guide
Are you struggling with a clogged water-cooled spindle motor on your CNC machine? Don’t worry, you’re not alone. Many CNC operators face this common issue, which can significantly impact the performance and lifespan of their equipment. In this article, we’ll walk you through the step-by-step process of cleaning an impeded water-cooled spindle motor, helping you maintain optimal performance and extend the life of your valuable machinery.
Why is Cleaning Your Water-Cooled Spindle Motor Important?
Before we dive into the cleaning process, let’s understand why this maintenance task is crucial. Water-cooled spindle motors are the heart of many CNC machines, providing the high-speed rotation necessary for precision cutting and milling. Over time, these motors can become impeded by mineral deposits, debris, or even algae growth in the cooling system. This impediment can lead to:
- Reduced cooling efficiency
- Increased wear on bearings and other components
- Potential overheating and damage to the spindle
- Decreased overall performance and accuracy of your CNC machine
Regular cleaning ensures your spindle motor operates at peak efficiency, prolonging its life and maintaining the quality of your CNC operations.
What Tools and Materials Do You Need for Cleaning?
To clean your water-cooled spindle motor effectively, you’ll need the following items:
- Cleaning solution (descaler or mild acid solution)
- Clean water
- Protective gloves and eyewear
- Soft brushes or pipe cleaners
- Flushing pump
- Bucket or container
- Clean cloths or towels
Having these tools on hand will make the cleaning process smoother and more efficient.
How Do You Prepare Your Spindle Motor for Cleaning?
Proper preparation is key to a successful cleaning process. Here’s what you need to do:
- Power down your CNC machine and disconnect the spindle motor from the power source.
- Allow the spindle to cool completely if it has been in use recently.
- Disconnect the water cooling lines from the spindle motor.
- Place a bucket or container under the spindle to catch any draining water or cleaning solution.
Taking these precautions ensures your safety and protects your equipment during the cleaning process.
What is the Step-by-Step Process for Cleaning the Water Cooling System?
Now, let’s get into the nitty-gritty of cleaning your impeded water-cooled spindle motor:
- Flush the system: Connect your flushing pump to one end of the cooling system and run clean water through it for several minutes to remove loose debris.
- Prepare the cleaning solution: Mix your descaler or mild acid solution according to the manufacturer’s instructions. Be sure to wear protective gloves and eyewear when handling these chemicals.
- Run the cleaning solution: Using the flushing pump, circulate the cleaning solution through the cooling system for about 15-20 minutes. This will help dissolve mineral deposits and stubborn buildup.
- Rinse thoroughly: After the cleaning cycle, flush the system with clean water for at least 10 minutes to remove all traces of the cleaning solution.
- Inspect and repeat if necessary: Check the water coming out of the system. If it’s still discolored or contains visible particles, repeat the cleaning process.
- Final rinse: Once the water runs clear, perform a final rinse with distilled or deionized water to prevent new mineral deposits from forming.
Remember, patience is key during this process. Thorough cleaning now can save you from costly repairs down the line.
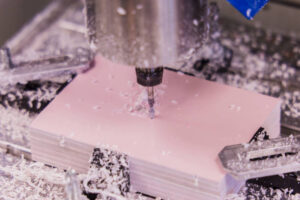
How Often Should You Clean Your Water-Cooled Spindle Motor?
The frequency of cleaning depends on several factors, including:
- Usage frequency of your CNC machine
- Quality of your cooling water
- Environmental conditions
As a general rule, perform a visual inspection of your cooling system monthly and a thorough cleaning every 3-6 months. However, if you notice any signs of reduced performance or overheating, don’t hesitate to clean the system immediately.
What Are the Signs That Your Water-Cooled Spindle Motor Needs Cleaning?
Being proactive in identifying when your spindle motor needs cleaning can prevent serious issues. Look out for these signs:
- Decreased cutting performance or accuracy
- Unusual noises coming from the spindle
- Increased operating temperatures
- Visible discoloration or particles in the cooling water
- Reduced water flow through the cooling system
If you notice any of these symptoms, it’s time to give your spindle motor a good cleaning.
Can You Use Air-Cooled Spindles to Avoid Water Cooling Maintenance?
While air-cooled spindles do offer an alternative that eliminates water-related maintenance, they have their own set of pros and cons:Pros of Air-Cooled Spindles:
- No risk of water leaks or mineral buildup
- Simpler maintenance routine
- Suitable for environments where water cooling is impractical
Cons of Air-Cooled Spindles:
- Generally lower maximum speeds compared to water-cooled spindles
- May not be suitable for high-power, continuous operation
- Can be noisier than water-cooled alternatives
The choice between water-cooled and air-cooled spindles depends on your specific application and operating conditions.
What Preventive Measures Can You Take to Reduce Spindle Motor Impediment?
Prevention is always better than cure. Here are some steps you can take to minimize the risk of impediment in your water-cooled spindle motor:
- Use high-quality, filtered water in your cooling system.
- Consider installing a water treatment system to reduce mineral content.
- Regularly check and clean filters in your cooling system.
- Maintain proper coolant levels and flow rates.
- Avoid leaving stagnant water in the system when the machine is not in use for extended periods.
By implementing these preventive measures, you can significantly reduce the frequency of major cleanings and extend the life of your spindle motor.
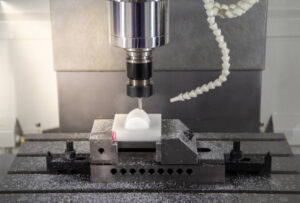
How Does Proper Spindle Motor Maintenance Impact CNC Machine Performance?
Maintaining your water-cooled spindle motor isn’t just about preventing breakdowns; it directly impacts the performance of your entire CNC machine. A well-maintained spindle motor contributes to:
- Improved cutting precision and surface finish quality
- Consistent performance across long production runs
- Reduced downtime for repairs or replacements
- Extended lifespan of the spindle and associated components
- Better energy efficiency and lower operating costs
Investing time in regular maintenance pays off in the form of improved productivity and higher-quality output from your CNC machine.In conclusion, cleaning an impeded water-cooled spindle motor is a crucial maintenance task that every CNC operator should master. By following the steps outlined in this guide and implementing preventive measures, you can ensure your spindle motor operates at peak efficiency, contributing to the overall success of your CNC operations. Key points to remember:
- Regular cleaning prevents performance issues and extends spindle life
- Use appropriate cleaning solutions and follow safety precautions
- Perform visual inspections monthly and thorough cleanings every 3-6 months
- Be proactive in identifying signs that your spindle motor needs cleaning
- Consider preventive measures to reduce the frequency of major cleanings
- Proper maintenance impacts overall CNC machine performance and productivity
By keeping these points in mind and making spindle motor maintenance a priority, you’ll be well on your way to achieving optimal performance and longevity from your CNC equipment.
- RicoCNC has a team of professionals who have been engaged in the design, production, sales, and maintenance of electro spindles for many years. Our company accepts the purchase of various types of CNC spindles.
water-cooled CNC spindle motors
Edge banding machine spindle motors.
- If you need any CNC spindle, please contact us.