Introduction
When it comes to CNC spindles, the choice of transducers and controllers is critical for optimal performance and precision. This article dives into how to justify selecting the right transducers and controllers for CNC spindles. We’ll explore the role of these components, evaluate the criteria for making informed choices, and discuss the advancements in CNC spindle control technology. Whether you’re upgrading your current system or investing in new technology, understanding these elements will help you make the best decisions for your machining needs.
The Evolution of CNC Spindle Systems
CNC spindle technology has advanced significantly over the years. Early CNC spindles were relatively simple, using basic controllers and transducers to manage their operation. Modern CNC spindles, however, incorporate sophisticated components designed to enhance performance and accuracy.
The evolution of CNC spindle systems has been driven by the need for greater precision, higher speeds, and improved reliability. Today’s CNC spindles, including those equipped with advanced controllers and transducers, are capable of delivering exceptional performance in a wide range of machining applications. This evolution has been critical in meeting the demands of industries such as aerospace, automotive, and manufacturing.
Key Components of CNC Spindles
Understanding the key components of CNC spindles is essential for evaluating the need for specific transducers and controllers. The primary components of a CNC spindle include the spindle motor, the spindle body, and the control system.
- Spindle Motor: This is the heart of the spindle, providing the rotational force necessary for machining. Modern CNC spindles often use brushless motors for greater efficiency and longevity.
- Spindle Body: This houses the spindle motor and other critical parts, ensuring stability and precision during operation.
- Control System: This includes the controllers and transducers that manage the spindle’s performance, including speed, position, and other variables.
A well-designed CNC spindle integrates these components seamlessly to provide reliable and accurate machining.
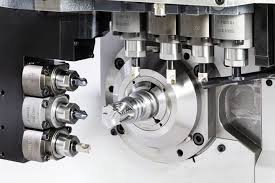
Role of Transducers in CNC Spindle Performance
Transducers are critical in CNC spindle systems as they convert physical measurements into electrical signals that controllers can interpret. There are several types of transducers used in CNC spindles, including piezoelectric and capacitive transducers.
- Piezoelectric Transducers: These transducers use the piezoelectric effect to measure changes in pressure, temperature, or acceleration. They are known for their high accuracy and responsiveness.
- Capacitive Transducers: These measure changes in capacitance caused by movement or displacement. They offer high precision and are often used in applications requiring fine measurement.
The choice of transducer affects the overall performance of the CNC spindle, impacting factors like accuracy, speed, and stability.
Assessing Control System Capabilities
When selecting a controller for a CNC spindle, it is essential to assess its capabilities in terms of precision, responsiveness, and compatibility with your spindle design.
- Precision: The controller should offer high precision to ensure accurate machining. This includes precise control over speed, position, and other critical parameters.
- Responsiveness: A responsive controller can quickly adjust to changes in the machining process, which is crucial for maintaining high-quality output.
- Compatibility: Ensure that the controller is compatible with your CNC spindle design. This includes checking for compatibility with existing hardware and software.
A well-chosen controller enhances the overall performance of the CNC spindle, leading to better machining outcomes.
Compatibility with CNC Spindle Designs
Compatibility between transducers, controllers, and CNC spindle designs is crucial for optimal performance. Not all controllers and transducers are universally compatible with every CNC spindle.
- Design Specifications: Verify that the transducer and controller match the specifications of your CNC spindle. This includes checking the type of signals they use and their operational ranges.
- Integration: Ensure that the components can be integrated into your existing system without requiring extensive modifications. This includes checking for compatibility with other components like the spindle motor and control software.
Proper compatibility ensures that the components work together efficiently, reducing the risk of issues during operation.
Importance of Precision and Responsiveness in Controllers
Precision and responsiveness are critical factors in CNC spindle controllers.
- Precision: High precision is essential for achieving accurate machining results. The controller must be able to manage minute adjustments to ensure that the spindle operates within the required parameters.
- Responsiveness: The controller should respond quickly to changes in the machining process. This is important for maintaining consistent performance and preventing issues such as vibrations or inaccuracies.
Controllers with high precision and responsiveness contribute significantly to the overall performance of the CNC spindle.
Comparing Piezoelectric and Capacitive Transducers
Both piezoelectric and capacitive transducers have unique advantages and applications in CNC spindles.
- Piezoelectric Transducers: These offer high accuracy and are suitable for applications requiring precise measurements of pressure, force, or vibration. They are often used in high-speed spindles where rapid response is needed.
- Capacitive Transducers: These are ideal for applications where high resolution is required. They provide accurate measurements of displacement or position and are commonly used in applications needing fine control.
Choosing the right type of transducer depends on the specific requirements of your CNC spindle application.
How Transducers Affect Spindle Accuracy and Speed
Transducers play a significant role in determining the accuracy and speed of CNC spindles.
- Accuracy: Accurate transducers ensure that the spindle operates within the desired parameters, leading to precise machining results. They provide essential feedback to the controller, allowing for fine adjustments.
- Speed: The speed at which a transducer can measure and transmit data affects the overall performance of the spindle. Faster transducers enable quicker adjustments, improving the spindle’s response time and performance.
High-quality transducers contribute to better spindle performance and more reliable machining outcomes.
Latest Trends in Spindle Controllers
The field of CNC spindle controllers is evolving rapidly, with several trends shaping the future of these components.
- Smart Technologies: The integration of smart technologies, such as AI and machine learning, is enhancing the capabilities of CNC spindle controllers. These technologies enable predictive maintenance and real-time optimization.
- Wireless Communication: Advances in wireless communication are allowing for more flexible and efficient control of CNC spindles. This trend is improving connectivity and data transmission in modern CNC systems.
Staying updated on these trends can help you make informed decisions about upgrading your CNC spindle technology.
Integrating Smart Technologies into CNC Systems
Integrating smart technologies into CNC spindle systems offers several benefits.
- Predictive Maintenance: Smart technologies can predict potential issues before they occur, reducing downtime and maintenance costs.
- Real-Time Optimization: Advanced controllers with smart features can optimize spindle performance in real-time, improving machining quality and efficiency.
Incorporating these technologies can enhance the capabilities of your CNC spindle system and contribute to better overall performance.
Analyzing the ROI of Advanced CNC Technologies
When considering an investment in advanced CNC technologies, it is essential to analyze the return on investment (ROI).
- Cost-Benefit Analysis: Evaluate the costs associated with upgrading to advanced transducers and controllers against the benefits, such as improved performance, reduced downtime, and increased productivity.
- Long-Term Savings: Consider the long-term savings that advanced technologies can provide. These may include reduced maintenance costs and increased operational efficiency.
A thorough ROI analysis helps justify the investment in advanced CNC technologies and ensures that you make the most cost-effective decisions.
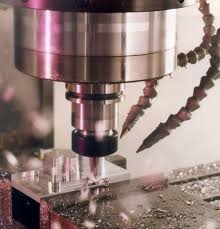
Case Studies: Success Stories of Upgraded CNC Systems
Examining case studies of successful CNC system upgrades can provide valuable insights.
- Case Study 1: A manufacturer upgraded their CNC spindle systems with advanced transducers and controllers, resulting in a significant increase in machining accuracy and efficiency. The investment led to higher product quality and reduced operational costs.
- Case Study 2: Another company integrated smart technologies into their CNC spindles, enhancing their ability to perform predictive maintenance and optimize performance. This upgrade resulted in decreased downtime and improved overall productivity.
These success stories highlight the benefits of investing in advanced CNC spindle technologies and offer practical examples of how these upgrades can lead to substantial improvements in machining performance.
Summary of Key Points
- Transducers and Controllers: These components are crucial for the performance and accuracy of CNC spindles.
- Types of Transducers: Piezoelectric and capacitive transducers offer different advantages depending on the application.
- Controller Features: Precision and responsiveness are critical for effective spindle control.
- Smart Technologies: Integrating smart technologies can enhance spindle performance and efficiency.
- ROI Analysis: A thorough ROI analysis helps justify investments in advanced CNC technologies.
Understanding the role of transducers and controllers in CNC spindles helps ensure you make well-informed decisions about your machining equipment. By keeping up with advancements and trends, you can optimize your CNC systems for better performance and greater efficiency.
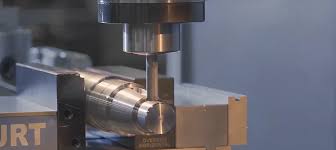
- RicoCNC has a team of professionals who have been engaged in the design, production, sales, and maintenance of electro spindles for many years. Our company accepts the purchase of various types of CNC spindles.
water-cooled CNC spindle motors
Edge banding machine spindle motors.
- If you need any CNC spindle, please contact us.