Introduction to Encoders in Spindle Positioning
So, how does a CNC machine know how far the spindle has traveled? The answer lies in encoders. Encoders are electronic devices that provide feedback to the CNC system, measuring the spindle’s position by detecting its rotation. They ensure that the spindle’s movement aligns with the machine’s programmed instructions.
There are two main types of encoders used in CNC machines:
- Rotary Encoders: Measure the angle of the spindle’s rotation and convert this data into a signal that the CNC software can interpret.
- Linear Encoders: Track the linear position of the spindle along the X, Y, or Z axis, providing precise feedback on how far the spindle has moved.
The Use of Linear Scales for Enhanced Accuracy
In addition to encoders, linear scales are used in high-precision CNC machines to enhance the accuracy of spindle movement. These scales measure the exact distance the spindle has traveled along any given axis, delivering real-time feedback to the machine’s control system.
Linear scales are especially useful in industries like aerospace and automotive, where the slightest deviation in part dimensions can result in costly errors. The integration of both encoders and linear scales allows for exceptional precision, ensuring every component meets its design specifications.
From Manual to Automated Spindle Control
CNC machines have come a long way from their manual counterparts. Early machines relied on human operators to control spindle movement and tool positioning manually. This process was labor-intensive and prone to error.
Today, automated spindle control has taken over, using advanced software and hardware to ensure that spindle travel is precisely measured and monitored. The operator’s role is now primarily to set up the machine, input the desired parameters, and let the system do the rest.
Breakthroughs in Spindle Speed and Precision
Recent advancements in CNC spindle motors have drastically improved both speed and precision. High-speed spindles can now rotate at tens of thousands of RPM, allowing for faster material removal rates and more efficient operations.
Moreover, multi-spindle CNC machines have revolutionized the industry by allowing multiple spindles to work simultaneously. This not only reduces production times but also ensures consistent precision across all components being machined.
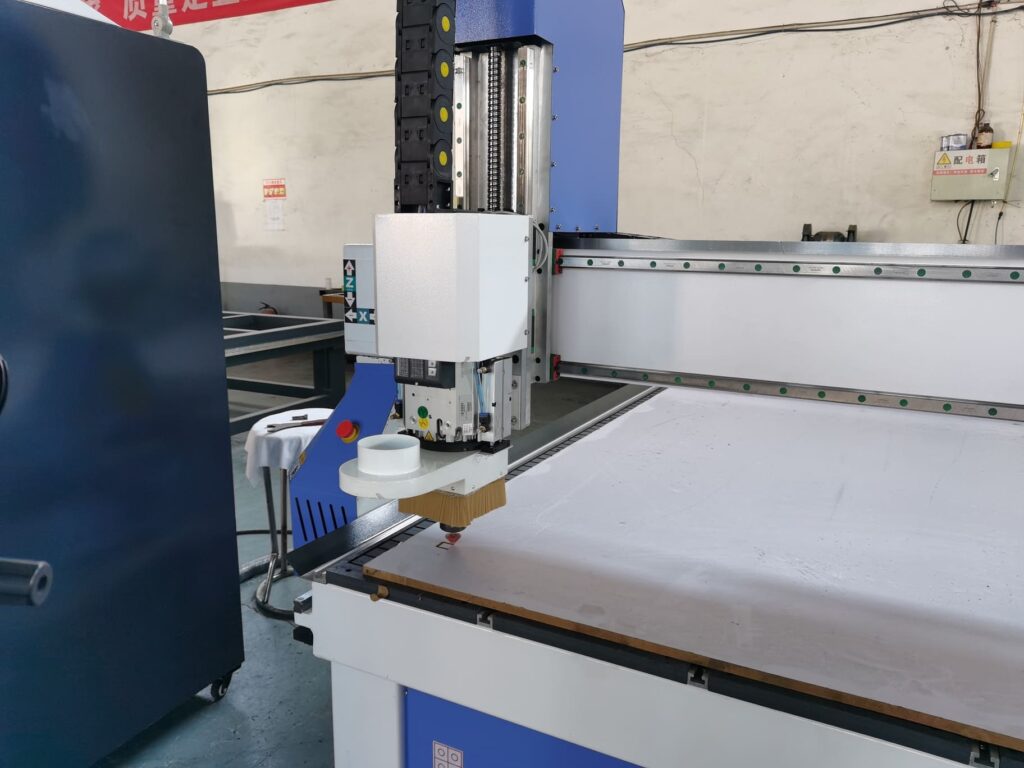
Analyzing the Relationship Between Spindle Travel and Product Quality
The precision with which a CNC machine tracks spindle travel has a direct impact on the quality of the finished product. If the spindle moves too far or not far enough, the dimensions of the machined part will be incorrect, leading to defective products.
CNC machines must maintain tight tolerances to ensure that each component is produced within the specified parameters. This is particularly important in industries such as aerospace, automotive, and medical device manufacturing, where even the slightest error can have serious consequences.
Case Studies: Success Stories of Precision Machining
Several industries have benefited from the advancements in spindle CNC technology. For example:
- Aerospace: High-precision machining is critical for aircraft components, which must meet stringent safety and performance standards.
- Automotive: CNC machines are used to produce engine parts, where exact tolerances are necessary to ensure optimal engine performance.
- Medical Devices: Implants and surgical instruments require exceptional accuracy, which can only be achieved through advanced CNC machining techniques.
The Importance of Precision in Spindle Travel
When it comes to CNC machining, precision is everything. Ensuring that the spindle moves exactly as programmed is crucial for achieving high-quality results. The combination of CNC spindles, encoders, and linear scales allows modern CNC machines to deliver the level of precision needed for today’s demanding applications.
Without this level of accuracy, manufacturers would struggle to produce parts that meet the necessary tolerances, resulting in wasted materials, time, and money.
Technologies Behind Spindle Movement Tracking
The technologies used to track spindle movement have evolved significantly over the years. Today’s CNC machines use a combination of hardware and software to monitor spindle travel with incredible accuracy. Key technologies include:
- Digital Encoders: Provide precise feedback on spindle position.
- Advanced CNC Software: Controls the machine’s movements and ensures that spindle travel aligns with the programmed instructions.
- Closed-Loop Systems: Use feedback from encoders and linear scales to adjust spindle movement in real-time, ensuring that the machine stays within the desired tolerances.
How Encoders Work in CNC Machines
Encoders are an essential part of the feedback loop that allows CNC machines to track spindle travel. They work by converting the spindle’s rotation or movement into a digital signal that the CNC control system can interpret. This signal is used to monitor the spindle’s position and adjust its movements as needed.
In some cases, multi-spindle CNC machines use multiple encoders to track the movement of each spindle independently. This ensures that all spindles are synchronized and moving according to the machine’s programming.
Types of Encoders Used in CNC Machines
There are two main types of encoders used in CNC machines: incremental encoders and absolute encoders.
- Incremental Encoders: Measure the change in position from a known starting point. They are ideal for applications where only relative position tracking is needed.
- Absolute Encoders: Provide a unique position value for every possible spindle position. These are used in applications that require precise, absolute positioning at all times.
CNC Programming for Spindle Control
Programming a CNC machine to control spindle movement requires a deep understanding of both the machine’s capabilities and the desired outcomes. Operators must input specific parameters for spindle speed, travel distance, and tool positioning, all of which are monitored by the machine’s control system.
Advanced Software Features for Enhanced Accuracy
Today’s CNC software offers advanced features that enhance the accuracy of spindle travel. These include:
- Toolpath Optimization: Ensures that the spindle moves along the most efficient path, reducing cycle times and improving precision.
- Real-Time Monitoring: Provides live feedback on spindle position, allowing operators to make adjustments as needed.
- Error Compensation: Automatically corrects for any deviations in spindle movement, ensuring that the final product meets the desired specifications.
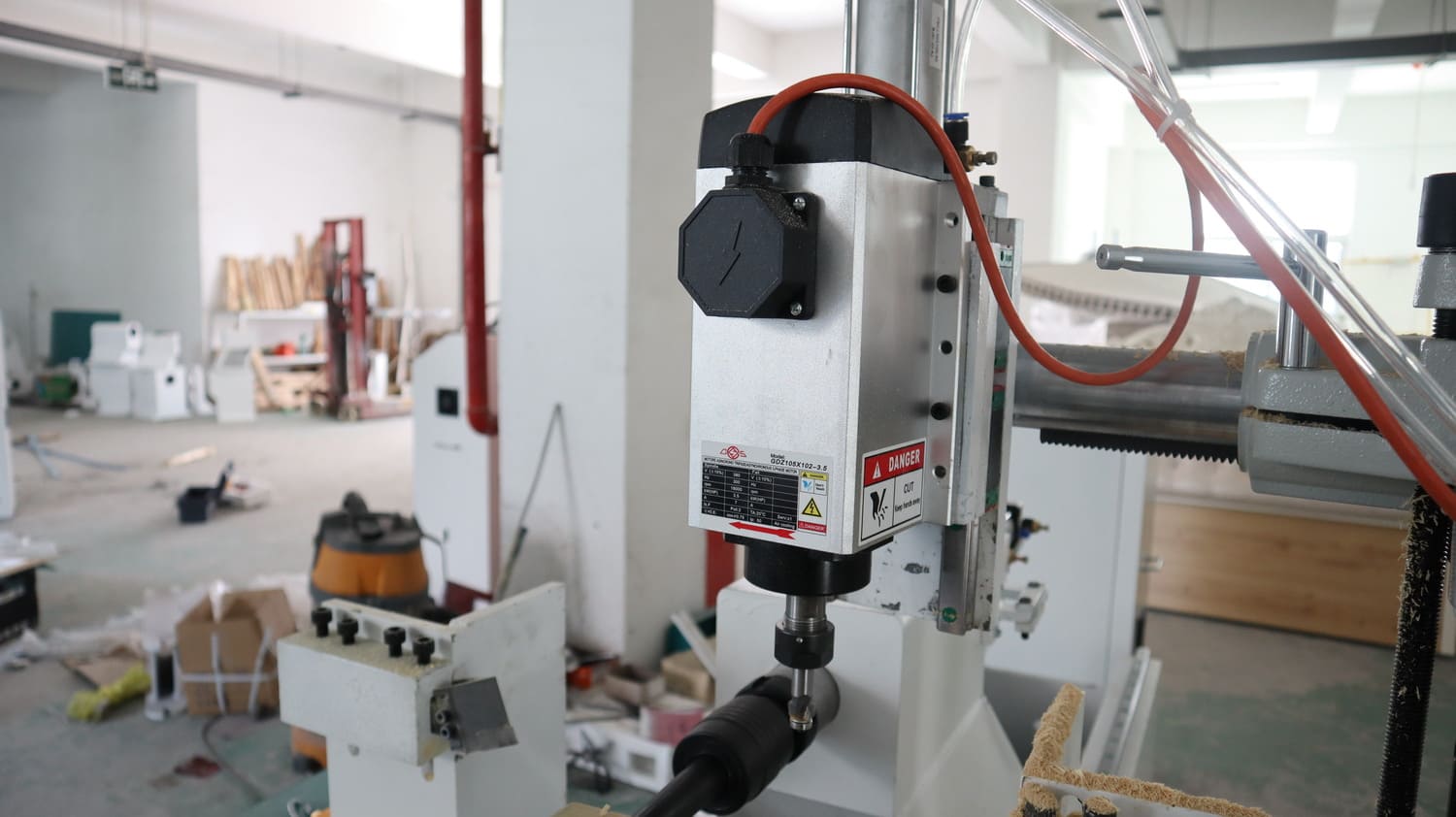
Frequently Asked Questions
- How do CNC machines measure the travel distance of a spindle?
CNC machines use encoders and linear scales to track spindle movement along the X, Y, and Z axes. - What are the signs of a failing CNC spindle?
A failing spindle may produce unusual noises, show inconsistent speed, or fail to maintain precision during operations. - Can spindle precision affect the overall CNC machine accuracy?
Yes, the precision of the spindle directly impacts the accuracy of the entire machining process. - How often should CNC spindle maintenance be performed?
Regular maintenance should be performed based on usage hours and the manufacturer’s recommendations, typically after every 1,000 to 2,000 hours of operation. - Are there any upcoming innovations in spindle technology to look out for?
Advancements in smart spindle technology, including predictive maintenance systems and AI-driven optimization, are expected to improve precision and efficiency in the coming years.
Key Takeaways
- CNC machines rely on spindle drives and encoders to track spindle movement with precision.
- Both incremental and absolute encoders are essential for accurate positioning.
- Recent advancements in spindle technology have led to improved speed, precision, and overall machining quality.
- Proper maintenance and monitoring of spindle movement are critical for maximizing the performance of CNC machines.
By understanding the technologies and components involved in spindle travel, operators and manufacturers can achieve greater accuracy, reduce errors, and improve overall efficiency in CNC operations.
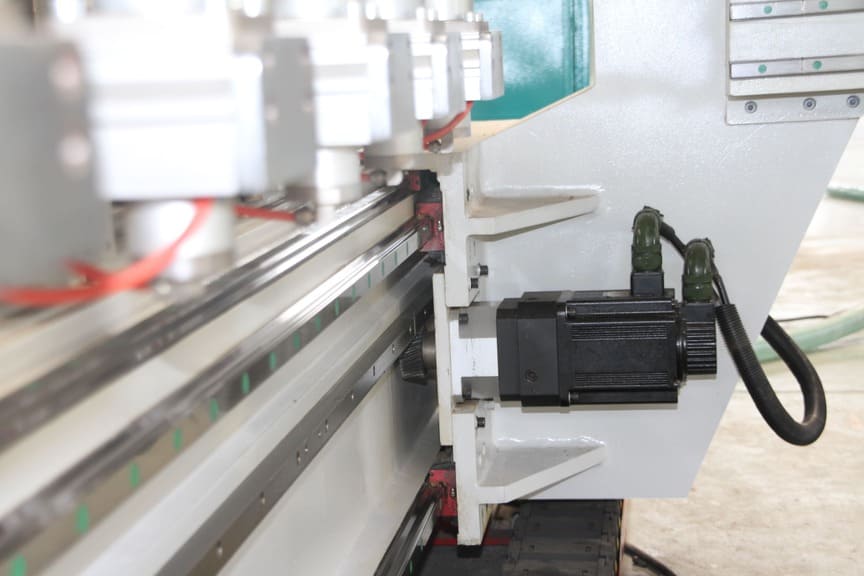
- RicoCNC has a team of professionals who have been engaged in the design, production, sales, and maintenance of electro spindles for many years. Our company accepts the purchase of various types of CNC spindles.
water-cooled CNC spindle motors
Edge banding machine spindle motors.
- If you need any CNC spindle, please contact us.