How Many Types of CNC Tools Are There: A Comprehensive Guide
In the world of Computer Numerical Control (CNC) machining, the variety of tools available is as vast as the range of parts they can create. From simple drills to complex multi-flute end mills, CNC tools are the unsung heroes of modern manufacturing. But just how many types of CNC tools are there? Let’s dive into this fascinating world and explore the diverse array of cutting implements that make precision manufacturing possible.
Understanding the Basics of CNC Tools
Before we delve into the various types, it’s essential to grasp what CNC tools are and their role in the machining process. CNC tools are the cutting implements used in CNC machines to remove material from a workpiece, shaping it into the desired form. These tools are designed to work with specific materials, cutting speeds, and machining operations.
The Main Categories of CNC Tools
While there are countless specialized tools, CNC cutting tools can be broadly categorized into several main types:
- End Mills
- Drills
- Face Mills
- Boring Bars
- Taps and Thread Mills
- Reamers
- Turning Tools
- Grooving and Parting Tools
Let’s explore each of these categories in more detail.
End Mills: The Versatile Workhorses
End mills are perhaps the most common and versatile CNC tools. They come in various shapes, sizes, and configurations, each designed for specific cutting operations. Some common types of end mills include:
- Flat End Mills
- Ball End Mills
- Bull Nose End Mills
- Roughing End Mills
- Tapered End Mills
High-performance spindles are crucial for maximizing the efficiency and precision of end mill operations, especially when working with harder materials.
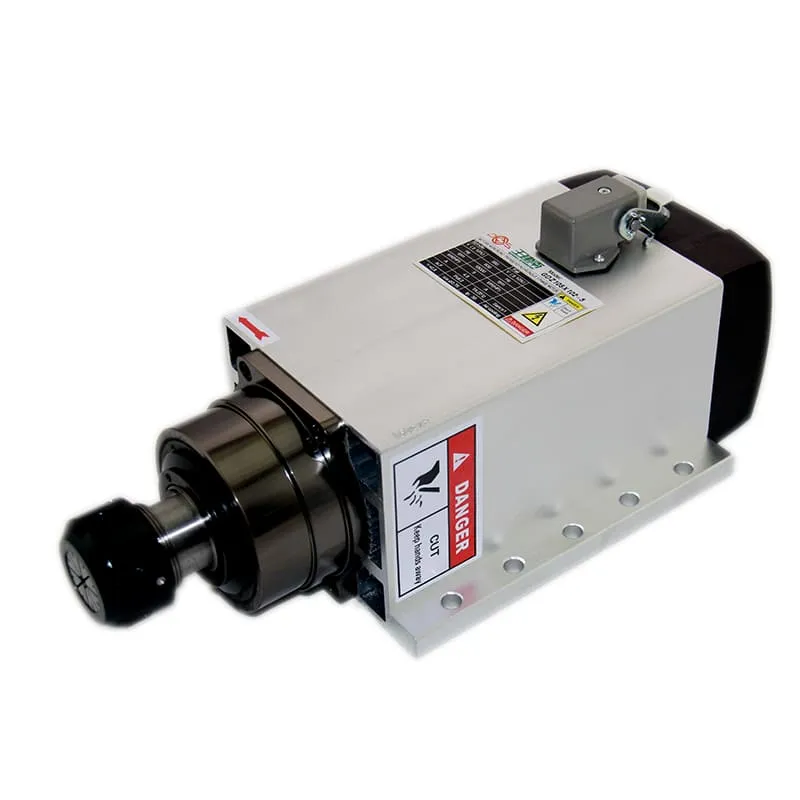
Drills: Precision Hole-Making
Drills are designed specifically for creating holes in workpieces. They come in various types, including:
- Twist Drills
- Center Drills
- Step Drills
- Spot Drills
- Gun Drills
The choice of drill depends on factors such as the material being machined, the desired hole depth, and the required finish quality.
Face Mills: Surface Finishing Champions
Face mills are used primarily for creating flat surfaces on workpieces. They excel at removing large amounts of material quickly and efficiently. Types of face mills include:
- High Feed Face Mills
- Square Shoulder Face Mills
- Round Insert Face Mills
CNC router spindles often use face mills for woodworking and plastic machining applications, where surface finish is crucial.
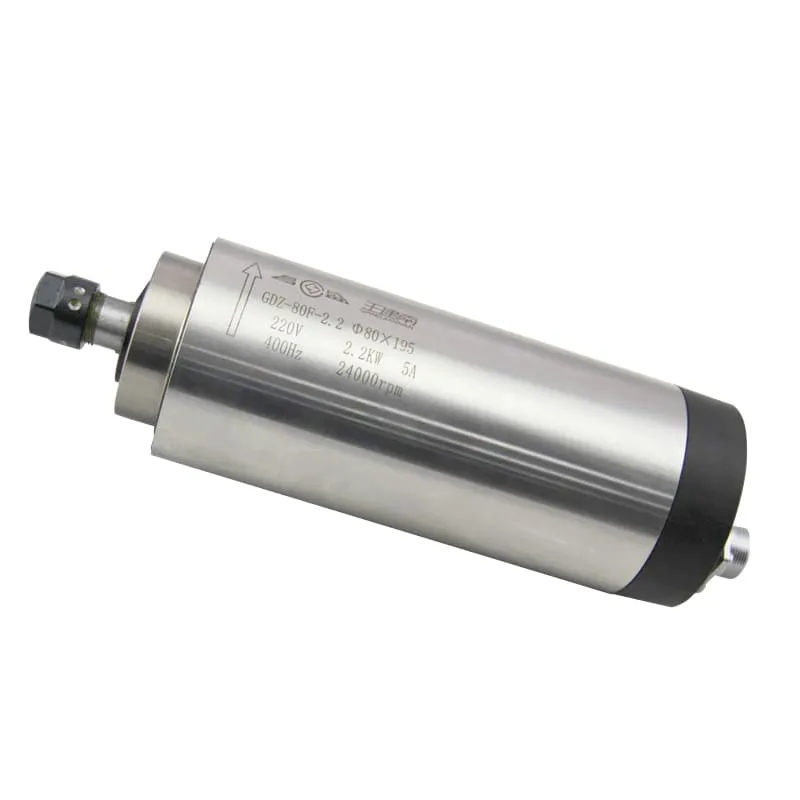
Boring Bars: Precision Internal Diameters
Boring bars are used to enlarge and finish the inside diameters of holes. They come in various configurations, including:
- Single-Point Boring Bars
- Multi-Point Boring Bars
- Adjustable Boring Bars
Precision boring operations often require high-precision spindles to maintain tight tolerances.
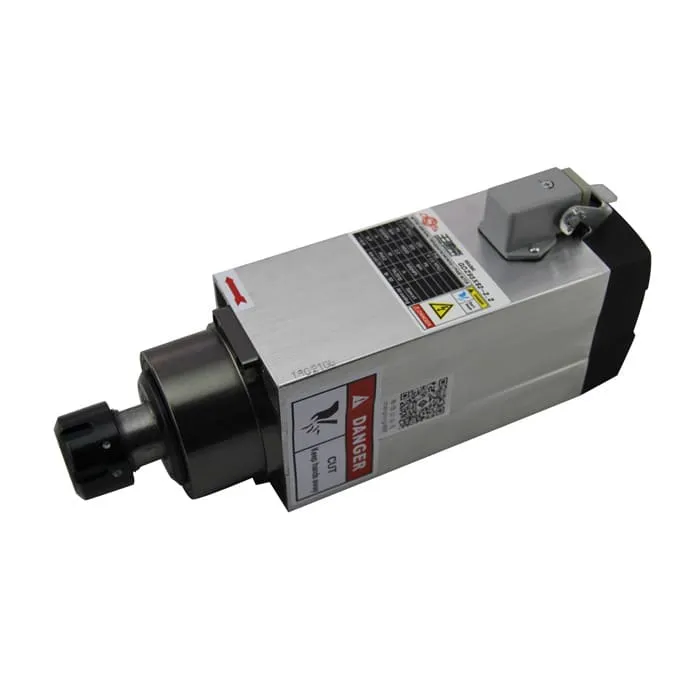
Taps and Thread Mills: Creating Internal Threads
These tools are used to create internal threads in holes. Taps cut threads in a single operation, while thread mills can create threads of various sizes using circular interpolation.
Reamers: Hole Finishing Specialists
Reamers are used to improve the size, shape, and surface finish of existing holes. They come in various types, including:
- Straight Flute Reamers
- Spiral Flute Reamers
- Adjustable Reamers
Turning Tools: Lathe Essentials
While not used in milling machines, turning tools are essential CNC tools for lathe operations. They include:
- External Turning Tools
- Internal Boring Bars
- Grooving Tools
- Threading Tools
Grooving and Parting Tools: Specialized Cutters
These tools are designed for creating grooves or separating parts from the workpiece. They come in various widths and configurations to suit different applications.
Specialized CNC Tools
Beyond these main categories, there are numerous specialized CNC tools designed for specific applications:
- Chamfer Mills
- T-Slot Cutters
- Dovetail Cutters
- Woodruff Keyseat Cutters
- Engraving Tools
Material-Specific CNC Tools
Different materials require different cutting tools. Here’s a brief overview:
- Steel Cutting Tools: Often made from carbide or high-speed steel (HSS)
- Aluminum Cutting Tools: Usually feature polished flutes to prevent chip welding
- Titanium Cutting Tools: Require high heat resistance and toughness
- Composite Cutting Tools: Often feature diamond coatings for abrasion resistance
The Role of Coatings in CNC Tools
Tool coatings play a crucial role in enhancing performance and extending tool life. Common coatings include:
- Titanium Nitride (TiN)
- Titanium Aluminum Nitride (TiAlN)
- Diamond-Like Carbon (DLC)
- Aluminum Titanium Nitride (AlTiN)
Choosing the Right CNC Tool
Selecting the appropriate CNC tool depends on several factors:
- Material being machined
- Desired surface finish
- Tool life requirements
- Machine capabilities
- Production volume
Understanding these factors is crucial for optimizing machining operations and achieving the best results.
The Impact of CNC Tool Selection on Machining Performance
The choice of CNC tool can significantly impact machining performance:
- Cutting Speed: Different tools allow for different cutting speeds
- Material Removal Rate: Some tools are designed for rapid material removal, while others focus on precision
- Surface Finish: The tool geometry and coating affect the final surface quality
- Tool Life: Proper tool selection can dramatically extend tool life and reduce costs
Emerging Technologies in CNC Tools
The world of CNC tools is constantly evolving. Some emerging trends include:
- 3D Printed Cutting Tools: Custom tools for specific applications
- Smart Tools with Embedded Sensors: Real-time monitoring of tool wear and cutting conditions
- Cryogenic Cooling: Using super-cooled gases to improve tool life and cutting performance
- Hybrid Tools: Combining multiple cutting operations in a single tool
The Economics of CNC Tools
Understanding the economics of CNC tools is crucial for efficient manufacturing:
- Initial Cost vs. Tool Life: More expensive tools often offer longer life and better performance
- Downtime for Tool Changes: Fewer tool changes can significantly increase productivity
- Scrap Rates: Better tools can reduce material waste and improve part quality
- Energy Efficiency: Some tools require less power, reducing overall energy costs
CNC Tool Management Systems
Effective tool management is crucial in CNC machining operations. Modern tool management systems include:
- Tool Libraries: Digital databases of all available tools and their specifications
- Tool Life Tracking: Monitoring tool usage and predicting replacement needs
- Automated Tool Changers: Reducing downtime between operations
The Future of CNC Tools
As manufacturing technology advances, we can expect to see:
- More advanced materials for tool construction
- Increased use of AI for tool path optimization
- Greater integration of tools with machine control systems
- Development of hybrid machining processes combining additive and subtractive manufacturing
Best Practices for CNC Tool Usage
To maximize the effectiveness of CNC tools:
- Always follow manufacturer recommendations for cutting speeds and feeds
- Regularly inspect tools for wear and damage
- Use proper coolant and lubrication techniques
- Invest in high-quality tools for critical operations
- Continuously educate machinists on proper tool selection and usage
Conclusion: Embracing the Diversity of CNC Tools
The world of CNC tools is vast and diverse, offering a solution for virtually every machining challenge. From the versatile end mills to specialized engraving tools, each type of CNC tool plays a crucial role in modern manufacturing. Understanding the various types of CNC tools, their applications, and their impact on machining performance is essential for anyone involved in CNC machining operations.
As technology continues to advance, we can expect to see even more innovative CNC tools emerge, further expanding the capabilities of CNC machines and pushing the boundaries of what’s possible in manufacturing. By staying informed about the latest developments in CNC tooling and adopting best practices in tool selection and management, manufacturers can ensure they’re always at the cutting edge of precision and productivity.
Whether you’re a seasoned machinist or new to the world of CNC, the diversity of CNC tools offers endless possibilities for creating complex, high-precision parts. Embracing this diversity and continually expanding your knowledge of CNC tooling will undoubtedly lead to more efficient, cost-effective, and high-quality manufacturing outcomes.
FAQs
What is the most common type of CNC tool?
End mills are generally considered the most common type of CNC tool due to their versatility in handling a wide range of cutting operations.
How often should CNC tools be replaced?
The replacement frequency depends on factors such as the tool material, workpiece material, cutting conditions, and desired surface finish. Some tools may last for hundreds of parts, while others may need replacement after just a few operations.
Can a single CNC tool perform multiple types of operations?
Yes, many modern CNC tools are designed to perform multiple operations. For example, some end mills can handle both side cutting and plunging operations.
How do I choose the right CNC tool for my project?
Consider factors such as the material being machined, the desired part geometry, required surface finish, and production volume when selecting CNC tools. Consulting with tool manufacturers or experienced machinists can also be helpful.
Are there CNC tools specifically designed for high-speed machining?
Yes, there are CNC tools designed specifically for high-speed machining operations. These tools often feature special geometries and coatings to handle the increased heat and forces associated with high-speed cutting.