CNC (Computer Numerical Control) machine operators play a vital role in modern manufacturing. They are the skilled individuals responsible for setting up, maintaining, and operating CNC machines, which use automated processes to create precision parts for industries like aerospace, automotive, and medical devices. If you are considering a career in this field or are curious about the compensation, understanding the factors affecting hourly wages and the job outlook is essential. In this article, we’ll explore how much CNC machine operators make per hour, the variables that influence their pay, and tips to boost earning potential.
What is a CNC Machine Operator?
A CNC machine operator is responsible for overseeing the cutting, milling, or drilling processes of a CNC machine. The CNC machine receives a program coded in G-code, which instructs it on how to move and shape materials like metal, plastic, or wood. The operator ensures that the machine runs smoothly, produces high-quality products, and troubleshoots when things go awry.
Key tasks of a CNC machine operator include:
- Machine Setup: Preparing the CNC machine, aligning tools, and setting parameters.
- Monitoring: Ensuring that parts are produced accurately and making adjustments as needed.
- Maintenance: Regular maintenance to keep the machine running efficiently.
This role is essential for manufacturing parts that require extreme precision and consistency, which cannot be easily achieved by manual means.
Average Salary of a CNC Machine Operator
The salary of a CNC machine operator can vary depending on multiple factors. According to recent industry data, the average hourly pay for CNC machine operators in the United States is around $18 to $22 per hour, but this figure can range significantly based on experience, location, industry, and certifications.
Level of Experience | Average Hourly Rate ($) |
---|---|
Entry-Level (0-2 Years) | 15 – 18 |
Mid-Level (3-5 Years) | 20 – 25 |
Senior Level (5+ Years) | 25 – 30 |
Specialized or Niche Roles | 30+ |
Tip: While the above figures are indicative, salaries can vary by state or by the company hiring. Specializing in specific CNC machine operations can increase your pay by a significant margin.
Factors that Affect CNC Machine Operator Salaries
1. Experience and Skill Level
The primary determinant of salary is the experience level of the operator. Entry-level operators, who are just learning the ropes, generally start at a lower wage, while more experienced operators are often paid more due to their understanding of complex machine operations and troubleshooting skills.
- Entry-Level Operators: Typically, individuals in their first job or training earn lower wages.
- Experienced Operators: With 3-5 years of experience, operators can expect a boost in their hourly rate.
- Specialization: Operators skilled in operating 5-axis CNC machines or advanced multi-spindle machines often command higher pay.
2. Location and Industry
The geographical location can significantly impact salaries. Areas with a high cost of living or a greater demand for CNC operators tend to pay more. For example, operators in California or New York might make more than those in rural areas due to the cost of living and a higher concentration of manufacturing businesses.
In addition, the industry where you work can influence your salary. CNC machine operators working in aerospace or automotive manufacturing might earn more than those in woodworking or consumer products.
Industry Examples:
- Aerospace: Offers higher pay due to the need for extreme precision and technical expertise.
- Medical Devices: Similar to aerospace, precision is critical, and pay rates reflect the importance of accuracy.
- Automotive: Operators in this sector also enjoy above-average wages, especially those working with specialized materials.
3. Certifications and Education
Having certifications from recognized institutions can significantly boost an operator’s salary. Certifications in CNC programming, safety, or specific CNC machines signal to employers that the operator has received specialized training.
Popular certifications for CNC operators include:
- NIMS (National Institute for Metalworking Skills) certification.
- HAAS CNC training programs.
Educational qualifications like a vocational degree in machining or manufacturing technology also play a significant role in determining salary.
4. Company Size and Benefits
Operators working for larger companies or corporations may have better opportunities for higher pay, overtime, bonuses, and benefits like health insurance or 401(k) plans. Larger companies may also offer job stability and career growth opportunities.
5. Shifts and Overtime
Many CNC machine shops operate 24/7, which means operators may work in different shifts (day, evening, or night shifts). Working night shifts or weekends can lead to higher pay rates. Additionally, working overtime is common in the manufacturing industry, and this can further increase an operator’s hourly wage.
Enhancing Earnings as a CNC Machine Operator
1. Pursue Advanced Certifications
Advanced certifications in areas such as G-code programming or machine maintenance can help you command higher wages. Specialized training on particular CNC equipment, such as 4-axis or 5-axis CNCs, is a significant plus for job candidates.
Consider certifications like HAAS training programs that cover advanced visual quick code and programming procedures. Such certifications can be incredibly beneficial for increasing your hourly pay.
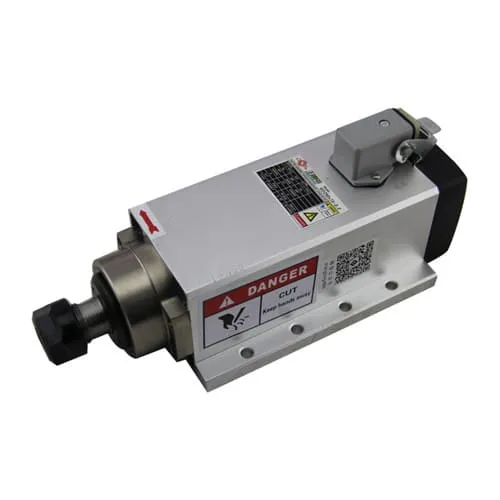
For more information on CNC spindle motors, check out CNC Spindle Motors.
2. Gain Experience in Specialized Industries
If you’re currently working in a low-paying industry, consider moving to more specialized fields like aerospace, medical devices, or automotive sectors. These industries not only pay better but also provide the opportunity to work on cutting-edge projects.
For instance, the use of CNC machines in medical device manufacturing requires precision and consistency, which translates to higher pay for machine operators experienced in these fields.
3. Work on Programming Skills
Moving beyond just operating CNC machines to programming them is another way to increase your earning potential. Becoming proficient in using CAD/CAM software such as MasterCAM or AutoCAD will enable you to generate G-code, providing you with a significant advantage over other candidates who only have operational experience.
Programming roles usually carry higher pay and allow for greater involvement in the manufacturing process. Understanding how to program a CNC router can lead to career growth and development opportunities.
You can check more about advanced CNC spindle motors here.
4. Seek Out Overtime Opportunities
Many manufacturing companies offer overtime opportunities, especially in busy production periods. Overtime often pays time and a half or even double the standard hourly wage, making it a good way to boost your earnings.
5. Move Into Supervisory Roles
With enough experience, CNC machine operators can move into supervisory roles such as lead machinist or CNC shop supervisor. These roles not only come with higher pay but also provide career stability and added responsibilities.
Common CNC Machine Operator Responsibilities
A CNC machine operator has various responsibilities throughout the production process:
- Reading Blueprints: Operators need to be able to read and understand blueprints and part drawings.
- Loading Materials: They load raw materials into the CNC machine, ensuring alignment.
- Quality Assurance: Checking the finished product against the specifications to maintain quality.
- Troubleshooting: Detecting issues like tooling errors or machine faults and making corrections.
Being proficient in these areas requires training, focus, and experience. However, many of these skills can be learned on the job.
Career Outlook for CNC Machine Operators
The career outlook for CNC machine operators is optimistic, with continued demand due to increased reliance on precision manufacturing. As companies look to automate more processes, CNC technology is becoming more vital, and the need for skilled operators to maintain and run these machines is increasing.
According to the U.S. Bureau of Labor Statistics, the employment of CNC operators is expected to grow steadily over the next decade. This is particularly true for operators who have skills in advanced CNC technologies like multi-axis machining or those capable of programming CNC machines.
Frequently Asked Questions
1. How much does it cost to build a CNC plasma table?
The cost of building a CNC plasma table can range from $3,000 to $10,000 depending on the size, quality of components, and added features like torch height control (THC) and software. If you are using more affordable stepper motors and a basic plasma cutter, you may be closer to the lower end of that range. On the other hand, professional-grade equipment can increase costs significantly.
2. What materials can I cut with a CNC plasma table?
A CNC plasma table can cut a wide variety of metals including mild steel, stainless steel, and aluminum. The thickness capability depends largely on the plasma cutter being used. Entry-level models can cut up to 1/4 inch, while more advanced models can easily handle 1 inch or more.
3. Is torch height control necessary for a CNC plasma table?
Yes, torch height control (THC) is highly recommended for maintaining consistent cut quality, especially when cutting materials that are not perfectly flat. THC automatically adjusts the height of the plasma torch based on the material’s surface, ensuring smoother cuts and extending the life of the consumables.
4. Can I build a CNC plasma table at home?
Yes, many DIY enthusiasts successfully build CNC plasma tables at home. Basic skills in welding, mechanical assembly, and basic electrical wiring are helpful. Access to CAD software and CNC controller software is also necessary to manage the design and operation.
5. What is the role of the water table in a CNC plasma setup?
The water table helps absorb heat generated during the cutting process, reducing the risk of material warping and minimizing smoke and dust. This makes it an effective way to manage the workspace environment, though regular maintenance is needed to keep the water clean.
6. What kind of software do I need for a CNC plasma table?
You will need two types of software:
- CAD software (such as Fusion 360 or SolidWorks) to design the parts.
- CAM software (such as SheetCAM) to generate the G-code for cutting operations. You will also require CNC controller software like Mach3 or LinuxCNC to actually control the table during cutting.
Conclusion
Building a CNC Plasma Table can be an exciting and rewarding journey for both DIY enthusiasts and metalworking professionals. It offers a mix of customization and cost-effectiveness that is difficult to match with a commercial purchase. By carefully designing, sourcing quality materials, and understanding the software and components involved, you can build a highly functional CNC plasma table that fits your specific needs.
From designing the table frame and installing motors and guide rails to selecting the appropriate plasma cutter and torch height control, every step plays a crucial role in achieving the precision and efficiency that CNC technology is known for. Safety, proper ventilation, and reliable software tools are also key factors to consider to ensure smooth operation.
Remember, a CNC plasma table opens up endless opportunities in metalworking, allowing you to cut mild steel, aluminum, and stainless steel with precision. Whether you plan to use it for DIY projects, professional jobs, or large-scale production, the skills and knowledge gained from building your own CNC plasma table will make the investment worthwhile.
If you’re looking to upgrade your machine, Spindle Motorshop offers various spindle options and CNC components that can help you take your plasma table to the next level.
For more resources on building CNC equipment, visit the Guide to Spindle Motors.