How Much Does a CNC Mill Cost?
How much does a CNC mill cost? This is a critical question for anyone looking to invest in CNC technology. The cost of a CNC mill can vary widely, influenced by multiple factors like size, capabilities, features, and even the brand. The price range can go from relatively affordable entry-level machines to high-end industrial models costing hundreds of thousands of dollars. Whether you’re a small shop looking to add CNC capabilities or a large manufacturer wanting to upgrade, understanding the cost components is key to making an informed decision.
Understanding CNC Milling Machines
1. What is a CNC Milling Machine?
A CNC Milling Machine is a precision cutting machine that uses Computer Numerical Control (CNC) to automate and control the cutting and shaping of materials. Unlike manual milling machines, CNC mills can create intricate parts without constant operator input.
- Components: A CNC mill typically includes a spindle, cutting tools, tool changer, and control panel.
- Automation: The CNC mill is programmed using G-code, which instructs the machine on how to cut, shape, and engrave the material.
Explore our selection of CNC Milling Spindles that are essential for enhancing milling performance.
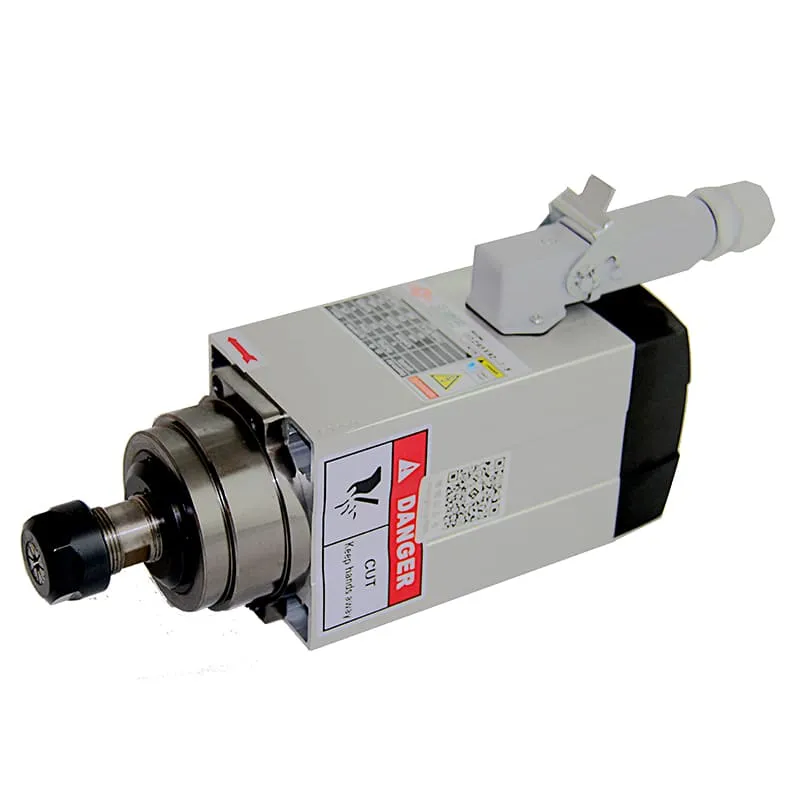
2. Factors Affecting CNC Mill Costs
The cost of a CNC mill is influenced by several factors. Understanding these factors can help determine which mill best suits your needs and budget.
- Size of the Mill: The size of the milling machine plays a big role in its cost. A small desktop CNC mill will cost significantly less than a full-sized industrial mill.
- Number of Axes: A 3-axis mill is cheaper than a 5-axis mill, but the latter provides more versatility for complex projects.
- Automatic Tool Changer: Mills with automatic tool changers (ATCs) are more expensive but save a lot of time in multi-step machining operations.
- Material Capability: The types of materials a mill can handle, such as metals, plastics, or wood, can also affect the price.
Check out our 2.2KW ER20 Square Air-Cooled Spindle to enhance the milling capabilities of your CNC machine.
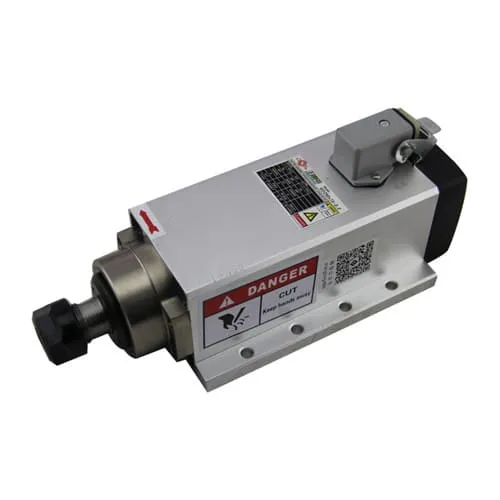
Types of CNC Mills and Their Costs
1. Entry-Level CNC Mills
Entry-level CNC mills are designed for beginners or small shops and are perfect for light machining or hobby projects.
- Price Range: Typically range from $2,000 to $10,000.
- Capabilities: Suitable for soft metals, plastics, and wood.
- Ideal User: Hobbyists, DIYers, or small businesses looking to prototype or produce smaller parts.
Explore our selection of 1.5KW ER11 Round Air-Cooled Spindles to add precision and reliability to your entry-level mill.
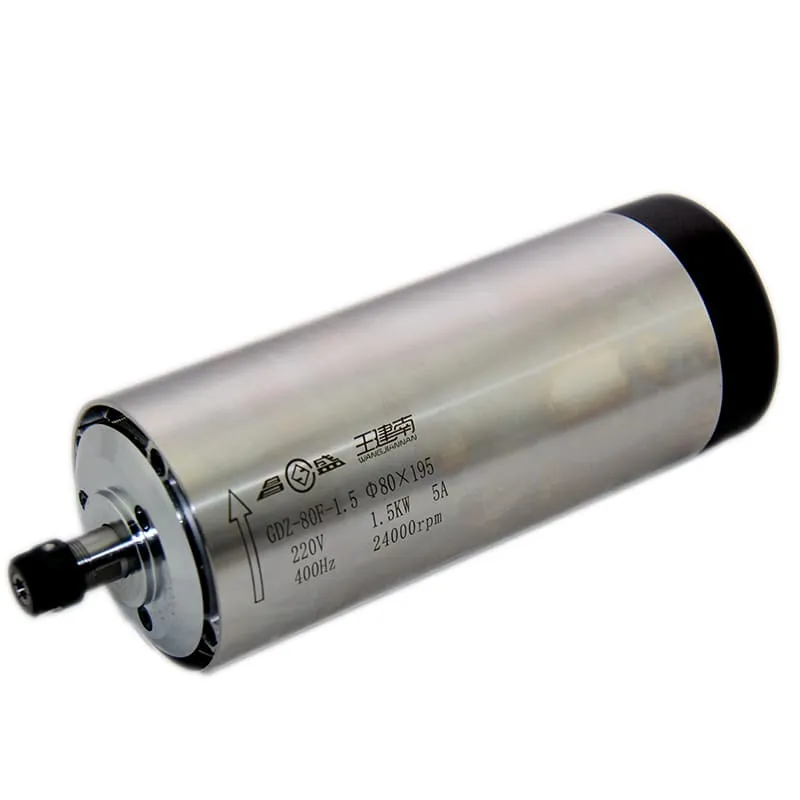
2. Mid-Range CNC Mills
Mid-range CNC mills are often found in professional shops and small manufacturing units. They provide increased versatility, precision, and a broader range of material capabilities.
- Price Range: Generally fall between $10,000 and $50,000.
- Capabilities: Can machine a wider variety of materials, including aluminum, steel, and plastics.
- Features: Often come with ATCs, and coolant systems for better heat management during cutting.
Consider our 3.5KW ER20 Air-Cooled Spindle for high-torque applications in mid-range CNC mills.
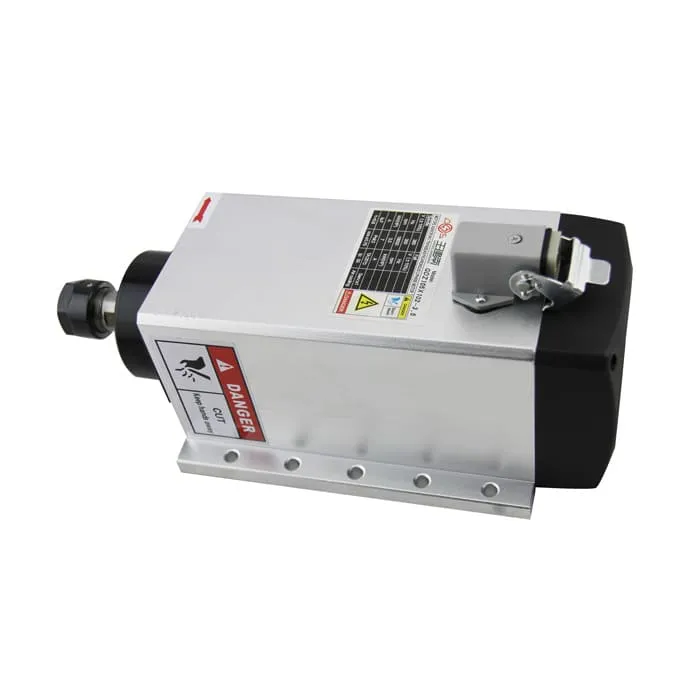
3. High-End CNC Mills
High-end CNC mills are used for industrial-grade machining and can produce highly precise components from various metals, including titanium and hardened steel.
- Price Range: Can cost anywhere from $50,000 to over $150,000.
- Capabilities: Capable of 5-axis machining, high-speed milling, and handling tough materials.
- Ideal for: Aerospace, automotive, and large manufacturing industries needing high-volume production.
Explore the 6KW ER32 Air-Cooled Spindle for high-end CNC mills that require robust power.
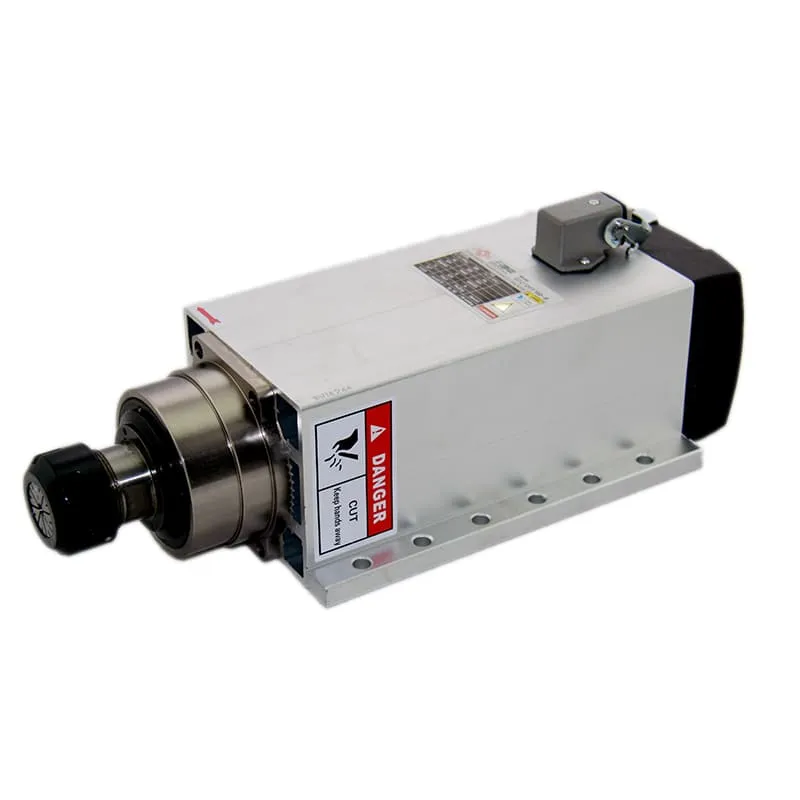
Essential Features Impacting CNC Mill Cost
1. Automatic Tool Changer (ATC)
An Automatic Tool Changer (ATC) is a vital feature in CNC mills that boosts productivity by allowing for automated switching between different tools during machining. ATCs reduce the time required to manually swap out tools, especially during complex machining processes that require multiple tools.
- Cost Addition: Adds between $3,000 and $10,000 to the base cost of the mill.
- Productivity: Significantly increases the machine’s efficiency, reducing cycle times for complex parts.
2. Spindle Power and Speed
The spindle is the core component of any CNC mill. Spindle power and speed are crucial factors that influence the types of materials the mill can process and the precision it can achieve.
- High-Speed Spindles: Essential for precision cutting and fine milling.
- Power Requirements: A higher KW rating means the mill can handle tougher materials more efficiently.
Upgrade your CNC mill with a powerful 5.5KW ER32 4-Pole Air-Cooled Spindle for increased versatility.
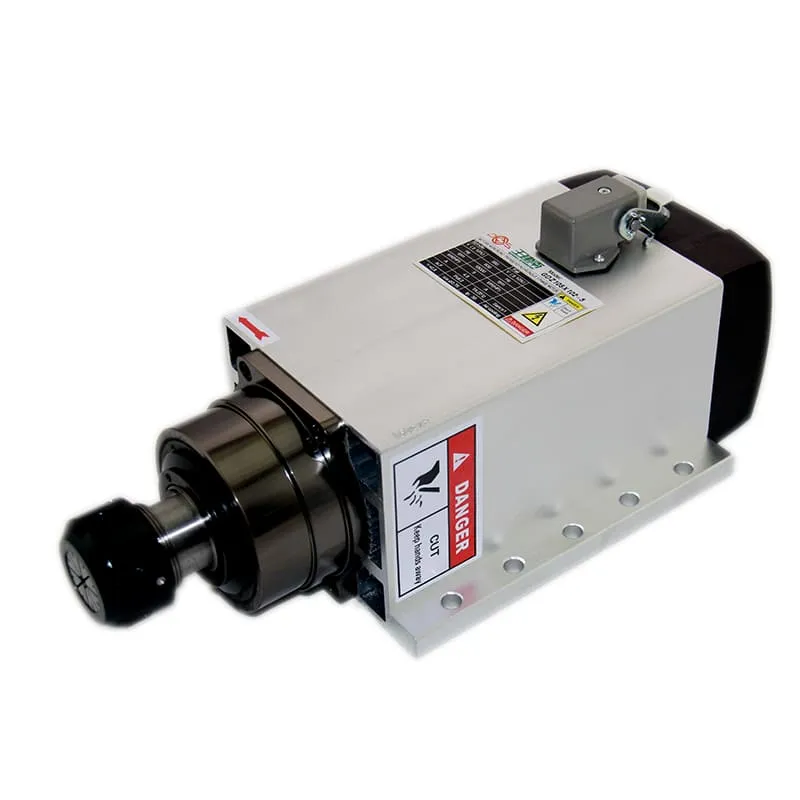
Comparing CNC Milling Costs: Budgeting Wisely
1. Initial Purchase vs. Long-Term Costs
While the initial cost of a CNC mill is a significant factor, potential buyers should also consider long-term costs, which include maintenance, power consumption, and tool replacement.
- Maintenance: The cost of regular spindle replacements, lubrication, and software updates.
- Tooling Costs: Tools wear down over time, so factoring in the costs of cutting tools, drill bits, and end mills is essential.
- Software and Upgrades: CNC mills require software updates and occasionally new software, which can be a recurring expense.
Check out the 800W ER11 Air-Cooled Spindle for a cost-effective yet efficient spindle upgrade.
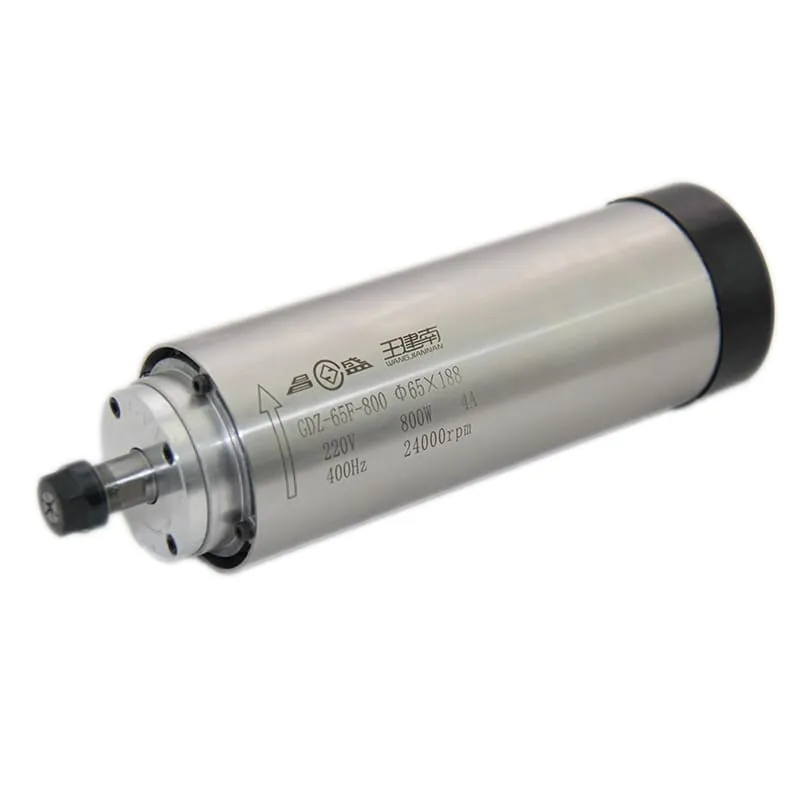
2. Financing Options and ROI
Many manufacturers offer financing plans to make acquiring a CNC mill more affordable. Understanding the return on investment (ROI) is crucial, especially for new businesses.
- Leasing: Leasing options make it possible to spread the initial cost over several years.
- ROI Calculation: Consider how the CNC mill will impact productivity, labor costs, and lead times.
Explore our versatile selection of CNC spindles to fit your budget and production requirements.
Benefits of Investing in a CNC Mill
1. Precision and Repeatability
One of the main reasons businesses invest in CNC mills is for their precision and repeatability. Unlike manual processes, CNC mills can achieve micron-level accuracy for thousands of parts.
- Computer Control: The use of G-code ensures the same outcome every time, reducing the margin for error.
- Complex Geometries: CNC mills can create complex parts that would be impossible or highly time-consuming using manual methods.
2. Cost Savings Over Time
Though the upfront cost of a CNC mill can be high, the savings over time can be substantial due to increased efficiency, reduced labor, and higher quality production.
- Labor Costs: One operator can manage several CNC machines at once, cutting down on labor expenses.
- Material Waste Reduction: CNC mills are known for their material efficiency, minimizing the amount of waste produced.
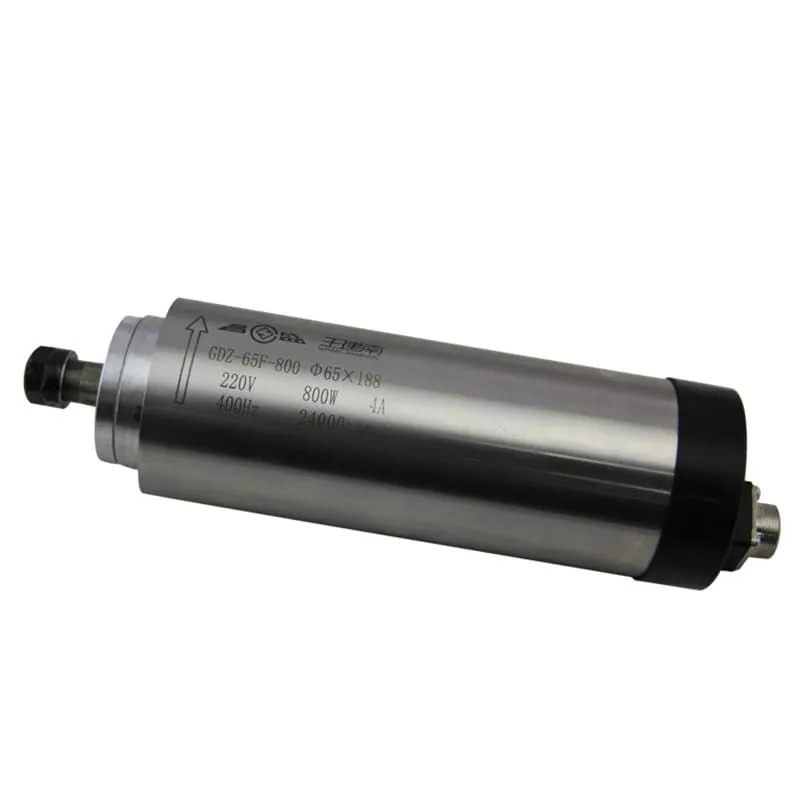
Conclusion: Is a CNC Mill Worth the Investment?
How much does a CNC mill cost? As we’ve seen, the price of a CNC mill can vary widely depending on its capabilities, features, and brand. However, the benefits—ranging from increased productivity to greater precision—often justify the investment. Understanding your production needs and long-term goals can help you determine which CNC mill is right for you. Whether it’s an entry-level mill for hobbyists or a high-end machine for an industrial setting, there’s a CNC mill out there to fit your needs.
For more resources to enhance your CNC capabilities, visit our CNC spindle selection for reliable and efficient performance.
FAQs
1. How much does a basic CNC mill cost?
A basic CNC mill can cost between $2,000 to $10,000 depending on its features and capabilities. Entry-level machines are perfect for hobbyists and small businesses.
2. What factors affect the cost of a CNC mill?
Factors such as size, number of axes, spindle power, and the presence of automatic tool changers can significantly affect the cost of a CNC mill.
3. Are CNC mills worth the investment for small businesses?
Yes, CNC mills can improve efficiency, reduce labor costs, and provide consistent quality, making them a worthwhile investment even for small businesses.
4. What are the ongoing costs of running a CNC mill?
Ongoing costs include maintenance, tooling replacement, electricity, and software updates.
5. Can I finance a CNC mill purchase?
Many manufacturers offer financing plans or leasing options to help manage the initial cost of purchasing a CNC mill.