How Much Does CNC Machining Cost?
When considering any manufacturing project, one of the critical aspects to evaluate is cost. How much does CNC machining cost? This question often arises among manufacturers, hobbyists, and businesses who seek precision machining services. CNC machining, with its unmatched accuracy and reliability, can significantly vary in price based on multiple factors. This article aims to shed light on the factors influencing CNC machining costs, providing an insightful guide for those planning to undertake CNC machining projects.
Understanding CNC Machining Costs
1. Factors Influencing CNC Machining Costs
The cost of CNC machining is influenced by numerous factors, which collectively impact the final expense of a machining project. Understanding these factors can help businesses better plan their budgets and optimize manufacturing efficiency.
- Material Costs: The type of material used significantly influences the cost of CNC machining. Metals like stainless steel, aluminum, and titanium tend to cost more compared to plastics or other non-metal materials.
- Complexity of Design: The more intricate the design, the higher the cost. Complex geometries require more machine time and more sophisticated tooling, which increases the machining cost.
- Machining Time: The total machining time is a major cost determinant. Parts that require longer milling or cutting time will result in a higher overall machining cost.
- Tolerance Levels and Surface Finish: Tight tolerances and specific surface finish requirements increase the cost. Achieving a high precision level often requires additional time and specialized tools.
Explore our 2.2KW ER25 Square Air-Cooled Spindle to support high-precision machining.
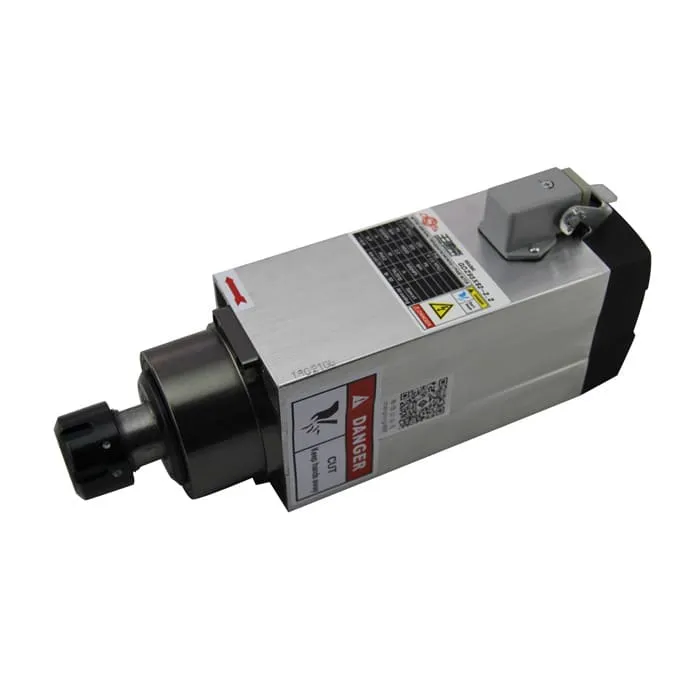
2. Material Selection and its Impact on Cost
Choosing the right material is a key component in determining CNC machining costs. Material selection not only impacts the price of raw materials but also affects machining speed and tool wear.
- Metals: The cost of machining metals like titanium or stainless steel is typically higher due to their hardness and strength. They require more cutting force, leading to increased tool wear and longer processing times.
- Plastics: Plastics are generally easier to machine, resulting in lower machining costs. Materials like ABS and nylon are commonly used for prototype production due to their low cost and machinability.
- Composites: These materials, though lightweight and durable, can be challenging to machine, leading to higher costs due to specialized tools and techniques required.
Check out our 6KW ER32 Air-Cooled Spindle to enhance your metal machining capabilities.
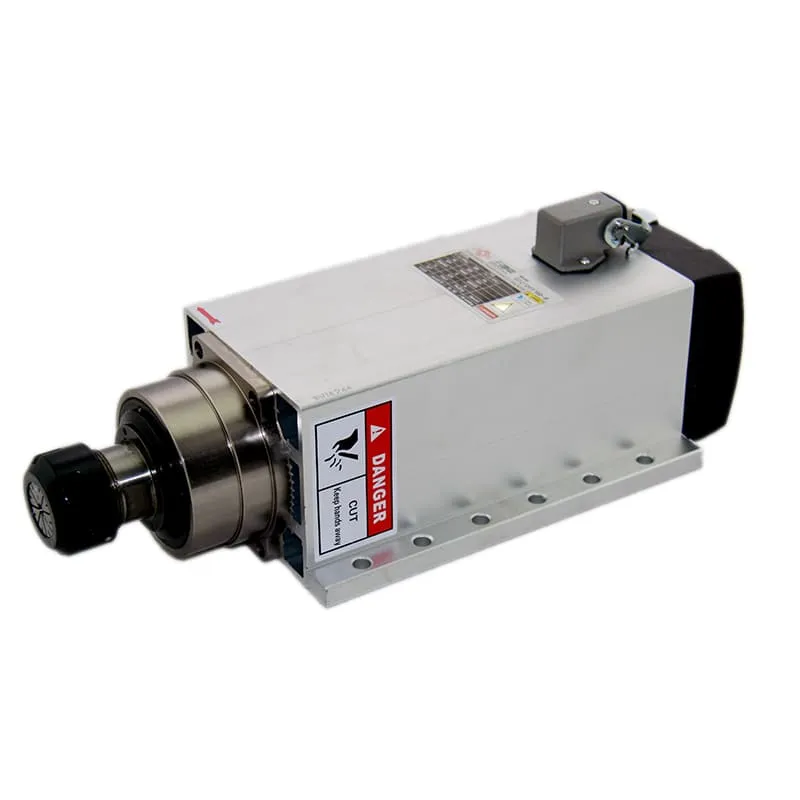
3. The Influence of Machine Type on Costs
The type of CNC machine used also has a significant effect on the overall cost. CNC mills, lathes, and routers all have different cost implications based on their capabilities and the complexity of the project.
- CNC Mills: Known for their versatility, mills can handle a wide range of materials and complex cuts. However, their machining costs tend to be higher due to the sophisticated operations they can perform.
- CNC Lathes: Lathes are generally used for cylindrical parts and tend to have lower machining costs compared to mills, especially for simpler projects.
- 5-Axis CNC Machines: These machines can perform more intricate cuts without repositioning the part, reducing machining time but increasing the setup cost.
Upgrade your machine with our 3.5KW ER25 Air-Cooled Spindle to maximize the efficiency of your milling operations.
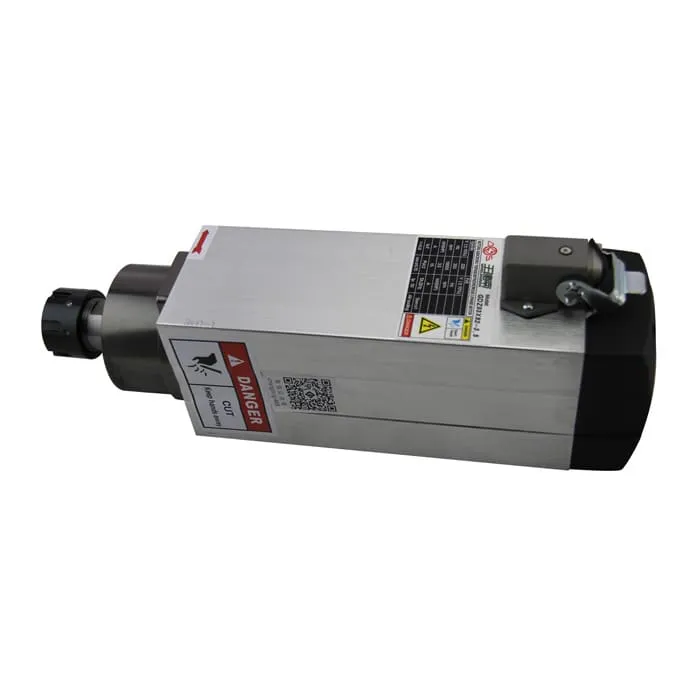
4. Tooling and Setup Costs
Tooling and setup can significantly influence CNC machining costs, especially for short production runs or highly complex parts.
- Custom Tooling: Custom tools are often required for unique shapes or complex designs, which adds to the cost of the project.
- Setup Time: Each new part requires machine setup, which involves calibrating tools, installing fixtures, and configuring software. This is a fixed cost and becomes more economical when amortized across a larger production run.
- Tool Wear and Replacement: Tools used for machining wear out over time, especially when cutting hard materials. The cost of replacing tools must also be factored into the overall expense.
5. Batch Size and Production Costs
The batch size plays a pivotal role in determining the overall cost efficiency of CNC machining.
- Small Batch Production: For smaller batches, the setup costs are distributed over fewer parts, which increases the per-unit cost.
- Large Batch Production: With large batch sizes, setup costs are spread over more parts, decreasing the cost per unit significantly.
- Prototyping vs. Mass Production: CNC machining is particularly suitable for both prototyping and mass production. While prototypes may cost more per unit due to custom tooling and short runs, mass production benefits from economies of scale.
Explore our 800W ER11 Air-Cooled Spindle for CNC lathes to reduce costs for small to medium production runs.
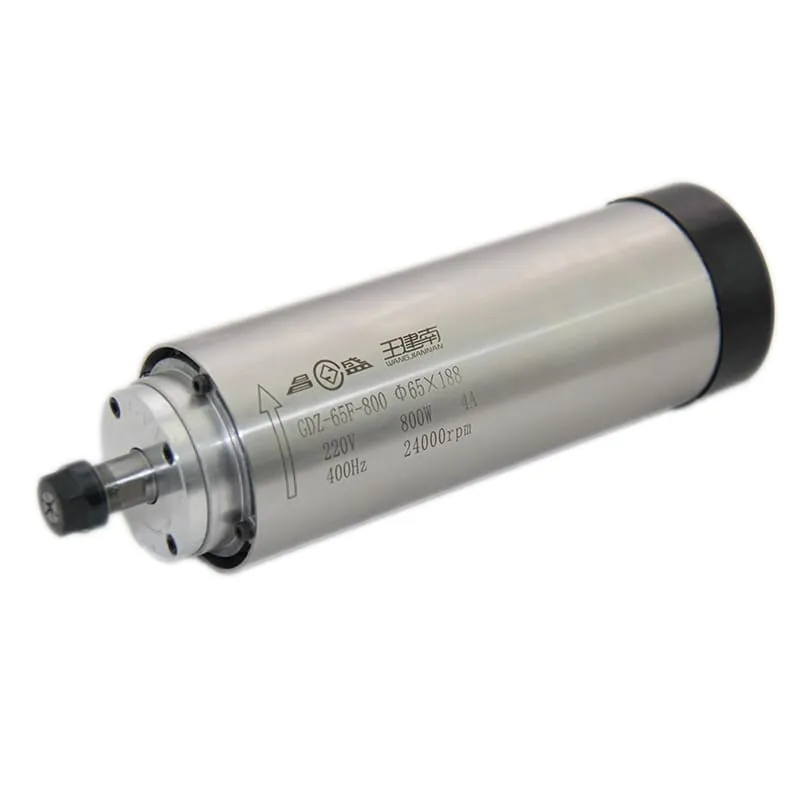
6. Labor Costs in CNC Machining
While CNC machines are automated, labor costs still play a significant role in determining overall machining expenses.
- Programming Labor: Skilled labor is required to program the machines. The more complex the part, the more time it takes to program, which increases costs.
- Machine Operators: Although CNC machines are largely automated, operators are needed to set up, monitor, and inspect the machining process.
- Quality Assurance: Precision machining often requires labor for quality assurance, such as measuring dimensions, checking tolerances, and ensuring that parts meet specifications.
7. Cost Breakdown by Project Type
The type of project can also influence the cost of CNC machining significantly.
- Prototype Projects: These are generally more expensive per unit because they require unique setups, and the time to program the machine is not amortized across many units.
- Production Projects: For larger production runs, the cost per unit decreases as programming, tooling, and setup costs are spread across a greater number of parts.
8. Surface Finishing and Post-Processing
Surface finishing and post-processing operations, such as anodizing, polishing, or powder coating, add to the overall cost of CNC machining.
- Polishing: Polishing improves the appearance and function of a machined part but requires additional labor and materials.
- Heat Treatment: Parts that need to be heat-treated for increased strength or durability will incur extra costs.
Consider our 6KW Air-Cooled Spindle with Flange to handle more intricate finishing tasks efficiently.
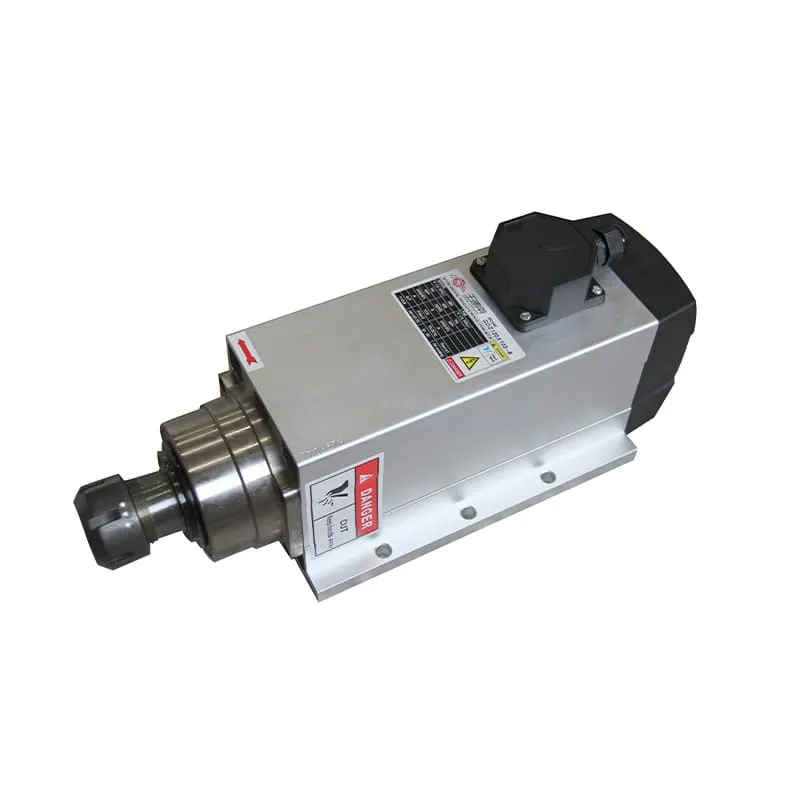
9. Reducing CNC Machining Costs
There are several strategies manufacturers can employ to reduce CNC machining costs without compromising on quality.
- Simplify Design: Reducing complexity in the part’s design can save machining time, tooling, and materials, ultimately reducing costs.
- Material Selection: Opting for materials that are easier to machine can help lower overall expenses.
- Increase Production Volume: The per-unit cost can be reduced significantly by increasing the volume of production, thereby spreading setup and programming costs.
10. Is CNC Machining Cost-Effective?
Considering all the variables, CNC machining is a cost-effective solution for high-precision parts, particularly in industries like aerospace, automotive, and medical device manufacturing. While upfront costs may be higher due to tooling and setup, the consistency, accuracy, and quality delivered by CNC machining provide long-term savings.
FAQs About CNC Machining Costs
1. What factors contribute most to CNC machining costs?
Material selection, machining time, part complexity, and batch size are the key factors that influence CNC machining costs.
2. How can I reduce the cost of my CNC machining project?
Simplify your design, select machinable materials, and consider larger production runs to reduce overall costs.
3. Does the type of CNC machine affect the cost?
Yes, different CNC machines, like mills, lathes, and 5-axis machines, have varying costs depending on their capabilities and the project requirements.
4. Why are prototypes generally more expensive than mass-produced parts?
Prototypes are more expensive due to unique setup requirements, custom tooling, and the lack of economies of scale.
5. Are there hidden costs in CNC machining?
Hidden costs can include tooling wear and replacement, labor for quality checks, and additional finishing processes such as polishing or anodizing.
6. How much can surface finishing add to the overall cost?
Surface finishing can add significantly to the cost depending on the type of finish required, the material being finished, and the labor involved.
Conclusion: Evaluating CNC Machining Costs
How much does CNC machining cost? The answer depends on various factors, including material choice, machine type, complexity of design, and batch size. Understanding these variables allows for a more accurate cost estimate and helps in making informed decisions. Whether you are a business seeking to produce high-quality components or a hobbyist looking to create a small batch, knowing the cost implications of CNC machining can save you time and money. CNC machining remains a valuable method for producing precision parts, and while costs may initially seem high, the reliability and quality delivered make it worthwhile for countless applications.