When it comes to metalworking and precision manufacturing, a CNC machine is often a vital investment for workshops, small businesses, and large-scale manufacturing facilities. Understanding how much a CNC machine for metal costs is critical before diving into this substantial purchase. This article will explore the factors affecting the pricing, different types of CNC machines, and considerations that will help you make the best choice for your specific needs.
What is a CNC Machine?
A CNC (Computer Numerical Control) machine is a high-precision, computer-controlled tool that is used for manufacturing metal and other materials. By utilizing computer programming, CNC machines can precisely cut, shape, and engrave materials with consistency and accuracy. These machines are pivotal in metalworking sectors such as automotive, aerospace, and industrial manufacturing.
Key Features of CNC Machines for Metal
- Automatic Tool Changer (ATC): Allows the machine to switch between tools automatically, enhancing productivity.
- Spindle Motor: This is the power hub that rotates the cutting tools and is crucial for cutting through tough metals.
- CNC Control Panel: Enables operators to control the machine and execute specific instructions, which are pre-programmed using CAD/CAM software.
- Precision Guide Rails: These ensure that the machine maintains accuracy while performing operations such as cutting, milling, or drilling.
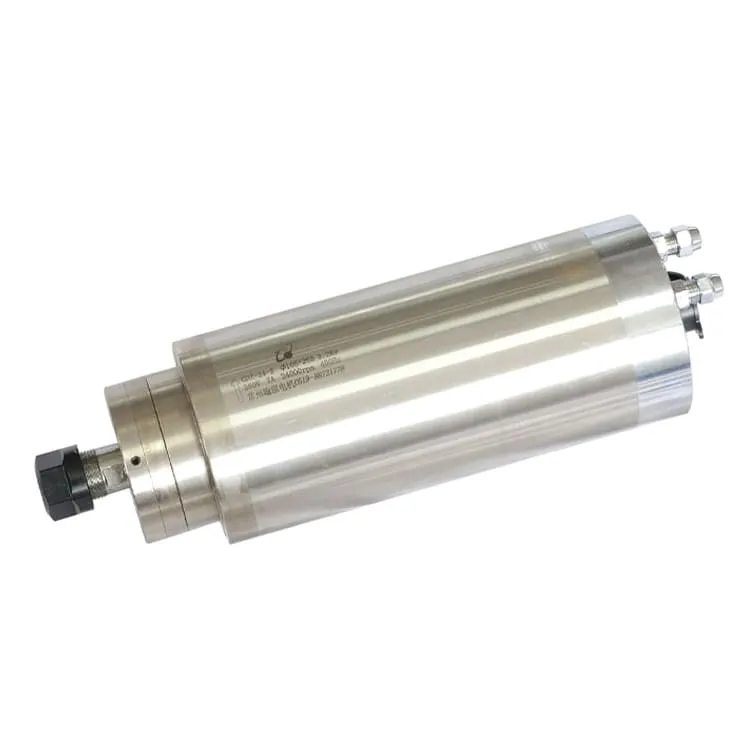
Check out more about spindles that are essential for CNC machine operations here.
Factors Affecting the Cost of CNC Machines for Metal
The price of a CNC machine for metal is determined by several factors, including its size, power, capabilities, and brand. Below, we outline the primary elements that influence CNC machine pricing:
1. Size and Type of Machine
CNC machines come in a variety of sizes to suit different manufacturing needs. Generally, machines that can handle larger metal workpieces are more expensive due to their robust construction and enhanced capabilities.
- Desktop CNC Machines: Smaller machines designed for lighter-duty tasks, often used for jewelry or small parts production. Typically cost between $1,000 to $5,000.
- Mid-Range CNC Machines: These are more robust machines used by small businesses for small-scale production. Prices range from $5,000 to $30,000.
- Industrial-Grade CNC Machines: Large machines capable of handling large metal workpieces. These machines are suitable for production lines, costing anywhere from $50,000 to over $500,000.
2. Spindle Power
The spindle motor is a critical element that affects the cost. Higher power is necessary to cut harder materials like stainless steel or titanium.
- Low Power Spindles: Machines with spindle power below 2 KW are suitable for softer metals and cost less.
- High Power Spindles: Spindle power greater than 5 KW is needed for industrial-grade machines, especially when dealing with tough alloys, which adds to the overall cost.
For example, a 3.2KW ER20 Water-Cooling Spindle is often used in machines that need to work with harder materials, and such machines generally have a price tag of $15,000 – $40,000. Learn more about powerful spindle motors here.
3. Machine Configuration and Automation
Automation features such as automatic tool changers (ATC) and robotic loaders can significantly increase the cost. A basic manual-operated CNC machine is much cheaper compared to one that includes advanced automation for minimizing manual labor.
- Basic CNC Machines: Have fewer automated features and usually cost between $5,000 and $15,000.
- Fully Automated Machines: Equipped with ATC and robotic assistance, making them perfect for high-volume production. Prices for these machines range from $100,000 to $400,000.
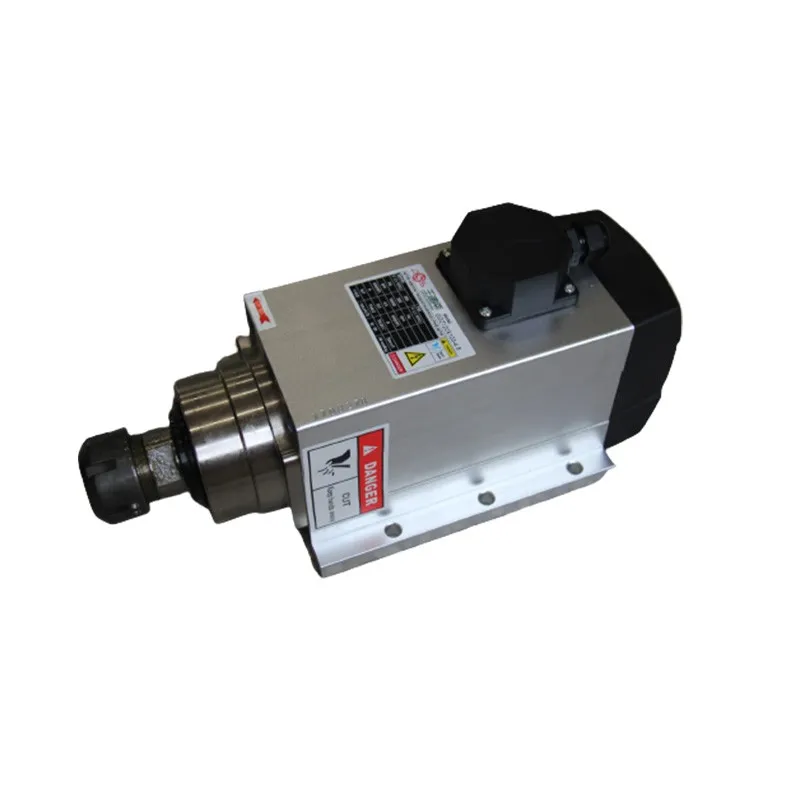
Types of CNC Machines for Metal and Their Costs
1. CNC Milling Machines
These are versatile machines capable of handling many different types of materials, including metal. Milling machines are often used for precision parts production.
- Price Range: $10,000 to $250,000.
- Ideal For: Producing complex geometries, and parts with multiple surface features.
2. CNC Lathes
CNC lathes are used for turning operations—perfect for symmetrical parts like cylinders and shafts.
- Price Range: $15,000 to $100,000.
- Ideal For: Producing rings, cylinders, and parts that require symmetry.
For more information about CNC lathes, visit our section on CNC lathes and spindles.
3. CNC Plasma Cutting Machines
These machines use a plasma torch to cut through metal. Ideal for cutting sheet metal and steel plates with a clean finish.
- Price Range: $15,000 to $200,000.
- Ideal For: Cutting sheet metal, steel plates, and other conductive materials.
4. CNC Routers for Metal
CNC Routers are highly versatile machines and can be used on both wood and metal. These are popular in workshops that need a machine to handle a variety of tasks.
- Price Range: $5,000 to $100,000 depending on the size and spindle power.
- Ideal For: Projects involving multiple materials.
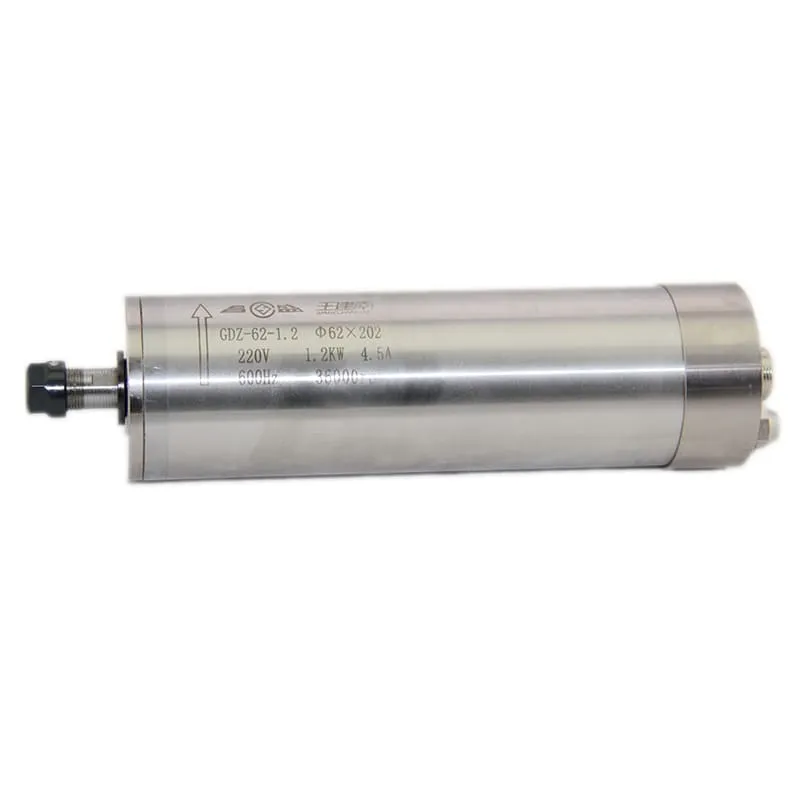
Additional Costs to Consider
1. Software
To operate a CNC machine, you’ll need CAD (Computer-Aided Design) and CAM (Computer-Aided Manufacturing) software. Such software allows you to design the parts and generate the necessary code to run the machine. Prices for CAD/CAM software can range from $1,500 to $10,000 depending on the features you need.
- Popular Options: Fusion 360, SolidWorks, and AutoCAD.
2. Tooling and Accessories
Purchasing a CNC machine is only part of the cost. You will also need tool holders, clamps, cutting tools, and coolant systems to operate the machine efficiently. Prices for these accessories vary greatly.
- Cutting Tools: Prices range from $20 to $1,000 depending on the material and quality.
- Clamping Kits: A good quality set will cost around $100 to $500.
3. Training and Operator Skill Level
Operating a CNC machine requires specific skills, and training is often needed for operators. Training programs range from $500 to $3,000 depending on the depth of the course. Additionally, if you’re employing skilled CNC machinists, the annual salaries can be significant.
Tips for Reducing CNC Machine Costs
1. Buy a Used Machine
One way to reduce costs is to purchase a used CNC machine. These machines are often available at a much lower price—sometimes half of the original price.
- Price Reduction: Used machines can be purchased from $10,000 to $50,000 depending on their age and condition.
2. Consider Leasing
Leasing can help reduce upfront costs. Lease payments are typically monthly or quarterly and are more manageable for small businesses.
3. Optimize Production Efficiency
Make sure to utilize the CNC machine to its maximum capacity by optimizing tool paths, using high-efficiency machining strategies, and reducing setup times. This reduces per-part cost and allows you to get the most out of your CNC machine.
4. Upgrade Instead of Replace
Instead of buying a new CNC machine, you can often upgrade components like the spindle motor to meet new production needs. Upgrading components is usually more cost-effective.
For more options on spindle upgrades, you can view products like the 4.5KW ER32 Air-Cooled Spindle.
FAQs About CNC Machines for Metal
1. How much does a CNC machine for metal cost?
The cost of a CNC machine for metal can range from $5,000 for basic desktop models to over $500,000 for industrial-grade machines with advanced automation features. The final price depends on the machine’s size, spindle power, level of automation, and brand.
2. What types of CNC machines are used for metal?
The common types of CNC machines used for metal include CNC milling machines, CNC lathes, CNC plasma cutters, and CNC routers. Each machine type has different capabilities and price ranges, making them suitable for different types of metalworking tasks.
3. Is buying a used CNC machine a good idea?
Yes, buying a used CNC machine can be a cost-effective option. Used machines can often be purchased for 50% less than the original price. However, it’s essential to verify the condition and maintenance history to ensure you’re getting a reliable machine.
4. What are the additional costs involved in owning a CNC machine?
Additional costs include CAD/CAM software, tooling and accessories, and maintenance. These can add up to several thousand dollars, depending on the complexity and type of machine. Training for operators is another important cost to consider.
5. How much does CNC training cost?
Training costs for CNC operators can vary between $500 to $3,000 per course. The cost depends on the depth and length of the training required to operate the CNC machine effectively.
6. What is the best CNC machine for beginners?
For beginners, a desktop CNC machine or an entry-level CNC lathe costing between $1,000 to $15,000 is a good starting point. These machines are simpler to use, and training requirements are generally lower compared to larger industrial machines.