How to Align CNC Spindle for Optimal Performance: A Step-by-Step Guide
Is your CNC machine producing inaccurate parts? Do you want to ensure your CNC spindle is perfectly aligned?
Aligning the CNC spindle is a crucial step in maintaining precision, accuracy, and productivity in any machining operation. Misalignment can lead to poor part quality, increased tool wear, and damage to your machine over time. In this comprehensive guide, we’ll dive into why spindle alignment is important, how to check for misalignment, and provide a detailed, easy-to-follow process to realign your CNC spindle.
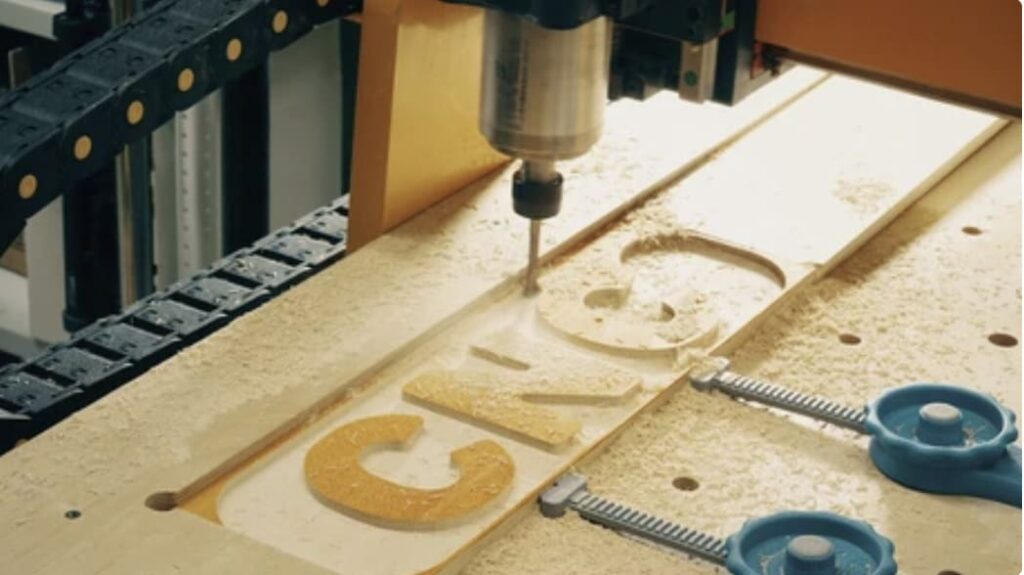
The Importance of Proper Spindle Alignment
What are the consequences of operating with a misaligned spindle?
Operating with a misaligned CNC spindle can cause a range of problems, from poor part quality to costly downtime. A slight deviation from alignment can result in uneven tool wear, chatter, and inaccurate cutting dimensions. This is particularly critical for industries where high-precision parts are required, such as aerospace or automotive.
A perfectly aligned spindle ensures that the cutting tool remains perpendicular to the workpiece, delivering accurate cuts and extending the life of both the spindle and cutting tools. Ultimately, investing time in proper alignment improves the overall productivity and efficiency of your CNC machine.
Basic Concepts of CNC Spindle Alignment
What is CNC spindle alignment?
CNC spindle alignment refers to the process of aligning the spindle so that it is perfectly perpendicular to the machine’s working surface. Misalignment occurs when the spindle is either tilted or shifted, causing inaccuracies during machining. The spindle can move in two key directions: axial (parallel to the Z-axis) and radial (perpendicular to the spindle’s axis).
- Radial alignment ensures the spindle is centered and doesn’t drift during operation.
- Axial alignment focuses on the spindle being perfectly perpendicular to the machine bed or workpiece.
Precision Measurement Tools
Which tools are essential for measuring spindle alignment?
Accurate CNC spindle alignment relies heavily on precision measurement tools. Without the right tools, you run the risk of poor alignment or incomplete measurements. Here are some of the key measurement tools used in the alignment process:
- Dial Indicators: Used to measure small deviations in alignment, dial indicators can detect misalignment within a thousandth of an inch.
- Test Bars: A precision-ground bar used to test the concentricity of the spindle. It’s inserted into the spindle and measured for wobble or runout.
- Feeler Gauges: These help measure small gaps between machine components, useful when checking for spindle deflection.
- Laser Alignment Systems: More advanced systems can offer non-contact alignment, providing high accuracy and reduced error rates.
Specialized Alignment Equipment
Are there any specialized tools that can assist with spindle alignment?
Yes, in addition to standard tools like dial indicators, there are several specialized pieces of equipment designed to streamline the alignment process:
- Spindle Alignment Jigs: These are custom-made tools that help hold the spindle in place during the alignment process.
- Optical Alignment Tools: Using optics, these devices measure deviations from a straight line between the spindle and the machine’s bed.
- Laser Calibration Systems: These provide highly accurate, real-time data, making alignment faster and more precise.
While manual methods still hold value, laser systems can significantly reduce human error, ensuring that alignment is within tighter tolerances.
Preparing Your CNC Machine for Alignment
How should you prepare your CNC machine before attempting spindle alignment?
Preparation is key to accurate spindle alignment. Follow these essential steps before beginning the alignment process:
- Clean the Machine: Dirt, dust, and debris can interfere with precision measurements. Make sure the machine is clean and free from obstructions.
- Warm-Up the Machine: Spindles may shift slightly due to thermal expansion, so running the machine for 20-30 minutes ensures a stable operating temperature.
- Inspect the Spindle: Check for signs of wear, damage, or debris that may affect the alignment.
Proper preparation minimizes the risk of errors during the alignment process, allowing for more accurate results.
Measuring Spindle Alignment Errors
How can you detect and measure spindle misalignment?
Measuring spindle alignment errors requires high precision and careful observation. Start by inserting a test bar into the spindle and checking for runout. Runout refers to the amount of wobble or deviation in the rotation of the spindle. This can be measured using a dial indicator placed at various positions along the test bar.
- Axial Runout: Place the dial indicator against the top of the test bar. If the reading changes as the spindle rotates, it indicates axial misalignment.
- Radial Runout: Place the indicator along the side of the test bar. Changes in the reading show radial misalignment.
Adjusting the Spindle for Optimal Alignment
How do you adjust a CNC spindle to achieve perfect alignment?
Once errors have been detected, the spindle needs to be adjusted to correct any misalignment. Depending on the machine, this could involve:
- Loosening the Spindle Mount: Many CNC machines allow for minor adjustments to be made by loosening the spindle mounts and making small shifts until alignment is achieved.
- Using Shims: In some cases, thin shims can be placed between the spindle mount and the machine to adjust for slight misalignment.
- Software Calibration: Some modern CNC machines come with software tools that allow for spindle calibration through the machine interface, automatically compensating for misalignment.
Formulas for Calculating Spindle Speed
Understanding spindle speed is key to machining efficiency. To calculate spindle speed, use this simple formula:
Spindle Speed (RPM) = (Cutting Speed × 1000) / (π × Tool Diameter)
For example, if you’re machining aluminum with a cutting speed of 150 meters per minute and using a tool with a 10mm diameter, the spindle speed would be:
Spindle Speed = (150 × 1000) / (π × 10) ≈ 4774 RPM
Calculating spindle speed ensures you’re machining at the optimal rate for both the material and tool, reducing wear and improving accuracy.
Solutions for Common Alignment Problems
What are common alignment issues, and how can you fix them?
- Runout: Caused by worn bearings or an uneven tool holder, runout can lead to poor cuts. Solutions include replacing bearings or using a different tool holder.
- Thermal Expansion: This occurs when the spindle heats up during operation, causing expansion. To minimize this, ensure the spindle is warmed up before alignment.
- Mechanical Wear: Over time, components such as ball screws and linear rails can wear, leading to alignment issues. Routine inspection and replacement of worn components are key.
Routine Checks for Spindle Alignment
How often should CNC spindle alignment be checked?
Routine checks should be performed every 6 to 12 months, depending on the machine’s usage and the precision requirements of your operations. High-precision jobs, especially those in aerospace or medical industries, may require more frequent alignment checks.
Advanced Techniques in CNC Spindle Alignment
Laser alignment and software-assisted techniques offer the most accurate and efficient ways to align your CNC spindle. These technologies allow for real-time monitoring and adjustments, ensuring that spindle alignment remains within tight tolerances.
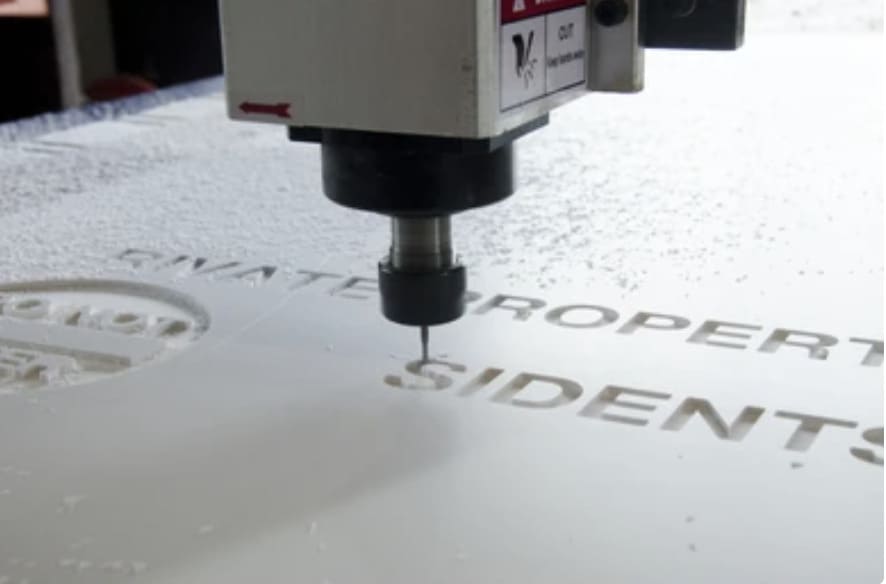
Conclusion
- Proper spindle alignment is critical for maintaining accuracy and extending tool life.
- Use precision tools like dial indicators and test bars for manual alignment, or opt for laser systems for increased accuracy.
- Regular checks and maintenance prevent costly downtime and improve machining performance.
Incorporating spindle alignment into your regular CNC maintenance routine will save you time, money, and frustration in the long run. Whether you’re a seasoned operator or new to CNC machining, understanding how to align your spindle is essential for delivering high-quality parts every time.

- RicoCNC has a team of professionals who have been engaged in the design, production, sales, and maintenance of electro spindles for many years. Our company accepts the purchase of various types of CNC spindles.
water-cooled CNC spindle motors
Edge banding machine spindle motors.
- If you need any CNC spindle, please contact us.