A CNC Plasma Table is an invaluable tool for precision metal cutting, widely used in industries ranging from automotive to metal fabrication. It provides a quick and efficient way to make highly accurate cuts in various metals, such as mild steel, aluminum, and stainless steel. This article will guide you through the process of building a CNC plasma table, providing you with an in-depth understanding of the components, requirements, and considerations involved.
Understanding CNC Plasma Cutting
CNC plasma cutting uses an electrically conductive gas to cut through metal. This gas, which forms plasma, is pushed at high speed from a nozzle, slicing through the metal workpiece with precision. CNC (Computer Numerical Control) systems control the movement of the plasma cutter along the X, Y, and Z axes to achieve precise cuts based on pre-programmed designs.
Key Components of a CNC Plasma Table
- Plasma Torch: The main cutting element that uses plasma to cut through metal.
- Torch Height Control (THC): Ensures the torch maintains the proper distance from the workpiece for optimal cutting performance.
- CNC Controller: This interprets G-code commands and directs the movement of the plasma torch.
- Stepper or Servo Motors: These drive the gantry and torch along the designated axes.
- Water Table or Downdraft Table: Helps minimize smoke and debris during the cutting process.
Benefits of Building Your Own CNC Plasma Table
Building a CNC plasma table offers several benefits, including cost savings, customization, and an improved understanding of how the machine works. It allows you to configure the table specifically for your cutting needs, whether for small projects or larger production runs.
Cost Savings
Purchasing a ready-made CNC plasma table can cost anywhere from $10,000 to $50,000 depending on the features. By building your own, you can reduce costs to around $3,000 to $10,000 depending on the parts and the capabilities you want.
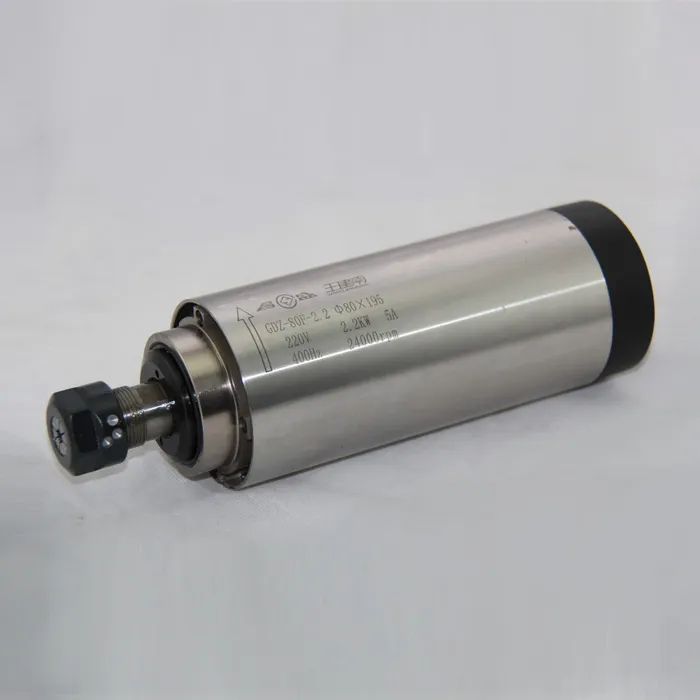
For more options on spindle upgrades that can be integrated into your plasma table for added versatility, check out the 4.5KW ER32 Air-Cooled Spindle.
Steps to Build a CNC Plasma Table
1. Designing Your Plasma Table
The first step is designing the CNC plasma table to fit your workshop’s needs. Computer-Aided Design (CAD) software like Fusion 360 or SolidWorks can be used to draw a blueprint of your table, including dimensions, the cutting area, and component placements.
- Table Size: Determine the size of the table based on your cutting needs. A typical plasma table has dimensions of 4×4 feet or 4×8 feet.
- Frame: Build a sturdy frame using steel tubing for stability.
- Rails and Gantry: Use precision linear rails and a solid gantry for smooth movement of the torch.
2. Acquiring Materials
The materials required for the plasma table include:
- Steel Tubing: To create the frame and legs.
- Guide Rails and Bearings: Used for precise linear motion.
- Stepper or Servo Motors: To control the motion of the gantry and torch.
- Plasma Cutter: Choose a reliable plasma cutter that suits your needs, such as one with 60 amps for cutting through mild steel up to 1/2 inch thick.
Recommended Components:
Component | Description |
---|---|
Plasma Cutter | Hypertherm Powermax45 or similar |
CNC Controller | Mach3 or LinuxCNC for G-code interpretation |
Torch Height Control | Proma THC 150 |
Motors | NEMA 23 or NEMA 34 stepper motors |
3. Building the Frame
Building the frame is the first major construction step. The frame must be stable and strong enough to hold the gantry, torch, and workpiece.
- Cut Steel Tubing: Cut the steel tubing to length based on your design.
- Weld the Frame: Ensure all pieces are welded securely. Double-check measurements to make sure the table is level.
- Mount Guide Rails: Attach the guide rails along the X and Y axes for the gantry.
4. Installing the Motors and Gantry
Next, install the stepper motors or servo motors that will move the gantry. Mount the gantry on the guide rails and attach the motors to drive the movement.
- Stepper Motors: These are more affordable but might lack precision for some high-end applications.
- Servo Motors: Offer better accuracy and speed, suitable for professional-level cutting tasks.
You may also want to consider adding a torch height controller (THC) to maintain a consistent distance between the plasma torch and the workpiece. This ensures cleaner cuts and extends the life of consumables.
Choosing the Right Plasma Cutter
The plasma cutter is at the heart of your CNC plasma table. Choosing the right cutter depends on the types of materials you plan to work with and their thickness.
- Entry-Level Plasma Cutters: Suitable for cutting mild steel up to 1/4 inch. Cost ranges from $300 to $1,000.
- Professional-Grade Plasma Cutters: Capable of cutting 1/2 inch to 1 inch thick materials. Prices range from $1,500 to $5,000.
Torch Height Control (THC)
Torch Height Control is crucial for maintaining cut quality. THC automatically adjusts the height of the plasma torch based on the material’s surface, preventing the torch from crashing and ensuring consistent results.
- Benefits: Improves cutting quality and extends the life of consumables.
- Recommended Model: Proma THC 150 is a popular choice for DIY plasma tables.
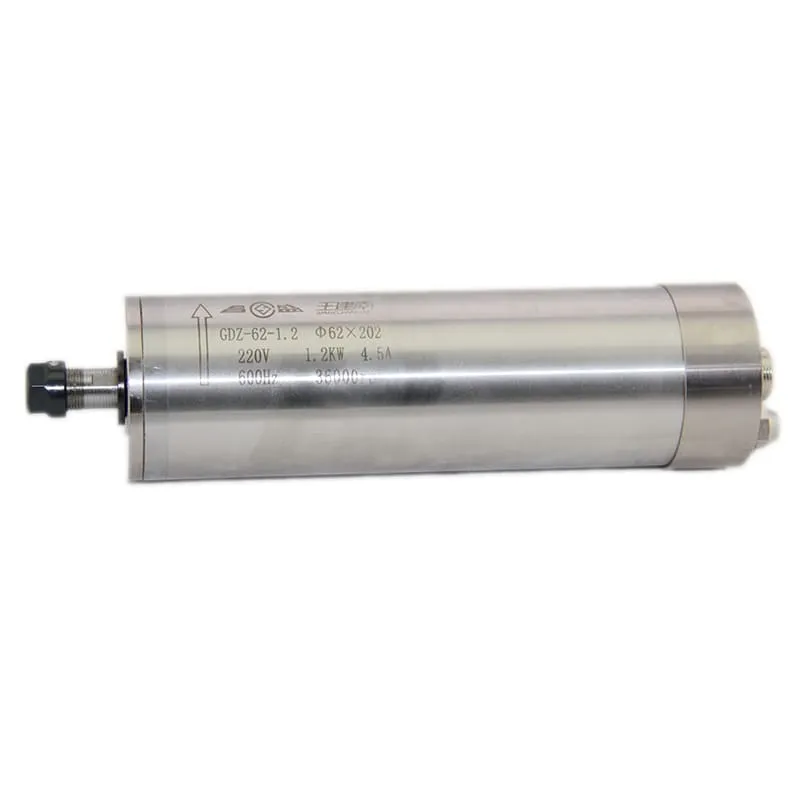
Software Considerations
1. CAD and CAM Software
To create designs, you will need CAD software (such as Fusion 360 or SolidWorks) to draft the part and CAM software to generate G-code that tells the machine how to move.
- Fusion 360: Easy to use and versatile, ideal for beginners and professionals.
- SheetCAM: Commonly used for plasma cutting as it is designed specifically for sheet metal operations.
2. CNC Controller Software
To run the plasma table, CNC controller software is required. Popular options include:
- Mach3: User-friendly and suitable for a wide variety of CNC applications.
- LinuxCNC: An open-source alternative, ideal for those who prefer customization.
Water Table vs. Downdraft Table
A water table or downdraft system is crucial for managing the dust and fumes generated during plasma cutting.
Water Table
A water table absorbs much of the heat generated during cutting, reducing warping of the workpiece and helping to suppress the smoke.
- Benefits: Reduces noise and helps prevent the warping of thin materials.
- Drawbacks: Requires regular maintenance to keep the water clean.
Downdraft Table
A downdraft table uses suction to draw smoke and debris away from the cutting area.
- Benefits: Better air quality in the workshop.
- Drawbacks: Requires a powerful ventilation system and can be noisy.
Safety Considerations
Safety is critical when building and using a CNC plasma table.
- Protective Gear: Always wear gloves, safety goggles, and appropriate clothing.
- Ventilation: Ensure proper ventilation in your workshop to prevent exposure to harmful fumes.
- Emergency Stop: Install an emergency stop button to immediately cut power in case of malfunction.
Conclusion
Building a CNC plasma table is a rewarding project that can save money and give you a better understanding of CNC technology. The key is careful planning, acquiring the right components, and using appropriate software for design and control. Whether you are cutting mild steel, aluminum, or stainless steel, a well-built CNC plasma table can enhance your metalworking capabilities and open new opportunities.
For more information on spindles, cutting tools, and other CNC components, visit Spindle Motorshop.
FAQs
1. How much does it cost to build a CNC plasma table?
The cost of building a CNC plasma table can vary significantly based on the type of components you choose and the table size. Generally, the cost ranges from $3,000 to $10,000. This price range includes the plasma cutter, frame materials, CNC controller, and other necessary parts such as stepper motors, guide rails, and software. Opting for higher quality or professional-grade components will increase the overall cost, while budget-friendly options can help reduce expenses.
2. What software do I need for a CNC plasma table?
To operate a CNC plasma table, you need both CAD (Computer-Aided Design) and CAM (Computer-Aided Manufacturing) software. CAD software, like Fusion 360 or SolidWorks, allows you to create designs, while CAM software, like SheetCAM, generates the G-code necessary to guide the CNC controller. Additionally, you need CNC controller software, such as Mach3 or LinuxCNC, to execute the cutting commands.
3. What materials can a CNC plasma table cut?
A CNC plasma table can cut a variety of electrically conductive metals, including mild steel, stainless steel, and aluminum. The thickness that can be cut depends on the power of the plasma cutter. Entry-level cutters can handle up to 1/4 inch, while more powerful models can cut through materials up to 1 inch thick.
4. Is a water table necessary for CNC plasma cutting?
While not strictly necessary, a water table is highly recommended for CNC plasma cutting. It helps reduce smoke, debris, and warping by absorbing the heat generated during the cutting process. It also reduces noise and improves the overall working environment. Alternatively, a downdraft table can be used, which uses suction to remove smoke and particles.
5. What is Torch Height Control (THC) and why is it important?
Torch Height Control (THC) is a system that automatically adjusts the height of the plasma torch based on the surface of the material. THC is crucial for maintaining consistent cut quality, preventing the torch from crashing, and prolonging the life of consumables. Without THC, variations in the material surface could lead to inconsistent cuts and excessive wear on the cutting nozzle.
6. Can I add a spindle to my CNC plasma table?
Yes, you can add a spindle to your CNC plasma table to increase its versatility, allowing you to perform both plasma cutting and milling or routing tasks. For example, you can integrate spindles such as the 2.2KW ER20 Air-Cooled Spindle or the 60000RPM 1.2KW ER11 Water-Cooled Spindle for enhanced functionality.