Introduction
CNC machines are revolutionizing industries, and their spindle is one of the most crucial components. In particular, the torque generated by the bearings inside CNC spindles directly influences the machine’s performance and precision. Understanding how to calculate the torque of bearings in CNC spindles ensures optimal performance and longevity. This article provides a detailed step-by-step guide to calculating bearing torque, selecting the right spindle for woodworking, and key parameters that affect torque performance in CNC machines.
Understanding CNC Spindle Mechanics
A CNC spindle is essentially the heart of the machine, responsible for rotating the cutting tool. The spindle’s performance is influenced by various factors, but one of the most significant is torque. Torque plays a crucial role in determining the cutting efficiency and quality of the spindle. Additionally, bearings within the spindle support the rotational motion and are critical in maintaining smooth operation.
The Role of Bearings in CNC Spindles
Bearings are integral to the smooth rotation of CNC spindles. They support the weight of the spindle and help to reduce friction between moving parts. In CNC spindles, bearings are responsible for maintaining precision and ensuring smooth cutting motion. A bearing failure can lead to poor machining accuracy and a drop in productivity.
Types of Bearings Used in CNC Spindles
There are several types of bearings used in CNC spindles, including:
- Angular contact bearings: These are the most common types of bearings used in CNC spindles due to their ability to withstand both radial and axial loads.
- Ceramic bearings: Known for their high precision, ceramic bearings are often used in high-speed spindles.
- Hydrostatic bearings: These bearings provide excellent damping characteristics and are ideal for heavy-duty CNC machining.
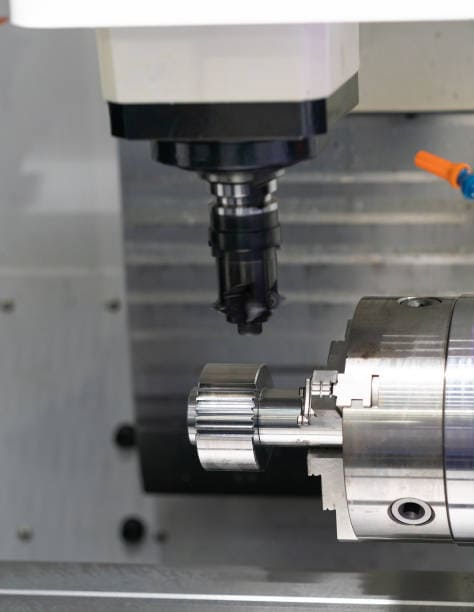
Fundamentals of Torque Calculation for CNC Spindle Bearings
Defining Torque and Its Importance
Torque, in simple terms, is the force that causes an object to rotate. In the context of CNC spindles, torque determines the spindle’s ability to cut through materials. If the torque is insufficient, the spindle may not be able to handle tougher materials, leading to decreased performance and wear on the spindle components.
The general formula for calculating torque is:
T = F × r
Where:
- T = Torque (Nm)
- F = Force (N)
- r = Radius (m)
Key Parameters Influencing Torque in Bearings
Several parameters influence the torque in CNC spindle bearings, including:
- Rotational speed (RPM): The faster the spindle rotates, the more torque is required to maintain performance.
- Bearing friction: The type and condition of the bearings used in the spindle significantly impact the overall torque. Worn or poorly lubricated bearings will increase friction, thus increasing the torque required.
- Load on the spindle: The material being worked on and the cutting force will affect the torque demands on the spindle.
Calculating the Torque
Let’s consider a real-world example. Assume a CNC spindle uses angular contact bearings with a radial load Fr of 500 N and a radius of 0.1 meters. Using the torque formula:
T = Fr × r
T = 500 N × 0.1 m = 50 Nm
This means the spindle needs 50 Nm of torque to rotate efficiently under this load.
Step-by-Step Guide to Calculating Bearing Torque
Calculating bearing torque for CNC spindles requires you to follow these steps:
- Identify the bearing type: Determine whether your spindle uses angular contact, ceramic, or hydrostatic bearings.
- Determine the load (force): Calculate the radial and axial load on the spindle. This can be derived from the material being cut and the machine’s operation parameters.
- Measure the spindle radius: The distance from the spindle center to the point where the force is applied.
- Use the torque formula: Apply the formula T = F × r to get the torque value.
Selecting the Right Spindle for CNC Machines
The selection of a spindle for woodworking or any other CNC machining application is influenced by several factors, such as the spindle’s torque output, the type of bearings used, and the spindle’s speed range.
Factors to Consider When Choosing a CNC Spindle
- Material type: Different materials (like wood, metal, or plastic) require different levels of spindle torque. A multi-spindle CNC machine may be necessary for heavier materials to distribute the workload.
- Spindle speed: Higher spindle speeds are necessary for precision and fine cuts, while lower speeds may be used for roughing operations.
- Cooling system: The type of cooling system used (air or water-cooled) will impact the spindle’s durability and its ability to maintain optimal torque levels.
Case Studies: Successful Spindle Selections in Woodworking
In woodworking applications, CNC routers often use spindles with high torque and angular contact bearings to achieve fine cuts. For example, a multi-spindle CNC machine used in furniture manufacturing might utilize a water-cooled spindle to maintain optimal torque under high-speed operations. This results in increased productivity and consistent quality of finished products.
Table: CNC Spindle Specifications for Different Materials
CNC Spindle Type | Material Compatibility | Typical RPM | Cooling System |
---|---|---|---|
Air-cooled spindle | Wood, plastic | 18,000-24,000 RPM | Air-cooled |
Water-cooled spindle | Metal, wood | 12,000-20,000 RPM | Water-cooled |
High-torque spindle | Hard metals, stone | 8,000-12,000 RPM | Water-cooled |
Preventative Maintenance for CNC Spindle Bearings
Routine Inspection and Cleaning
Bearings should be inspected regularly for signs of wear or damage. Cleaning the spindle housing and applying proper lubrication to bearings can significantly reduce friction and prolong bearing life.
Replacing Worn-Out Components
Worn-out bearings should be replaced promptly to prevent damage to the spindle. Using high-quality bearings, such as ceramic bearings, can further improve torque performance and reduce downtime.
Troubleshooting Common Spindle Motor Issues
Identifying Symptoms of Spindle Motor Failure
Common symptoms of spindle motor failure include excessive noise, overheating, and inconsistent torque output. Early identification of these issues can prevent further damage and reduce repair costs.
Quick Fixes vs. Professional Repairs
While some issues can be resolved with basic maintenance and part replacement, complex spindle motor failures often require professional repair services to restore optimal torque levels.
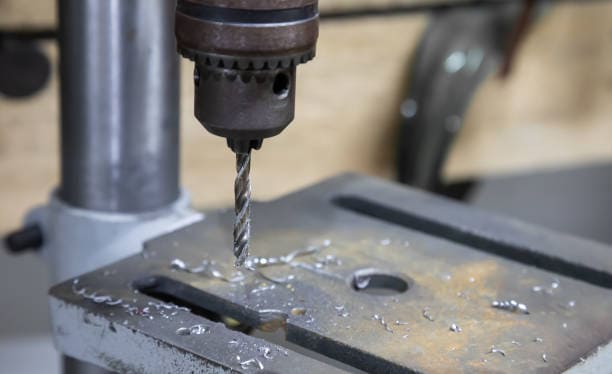
Conclusion
In conclusion, the torque of CNC spindle bearings plays a vital role in the overall performance of CNC machines. Calculating the torque accurately involves understanding key parameters such as load, speed, and bearing friction. By following proper maintenance routines and selecting the right spindle for your specific machining application, you can ensure that your CNC machine operates efficiently and delivers precise results.
FAQ
- What is the significance of torque in CNC spindles? Torque is crucial for determining the cutting efficiency and accuracy of a CNC spindle.
- How often should bearings be replaced in CNC spindles? Bearings should be inspected regularly and replaced if signs of wear, such as noise or vibration, are detected.
- What are the signs of a failing CNC spindle motor? Common signs include overheating, noise, and inconsistent performance.
Key Takeaways:
- Torque is essential for the optimal performance of CNC spindles.
- Regular maintenance and lubrication of bearings extend spindle life.
- Selecting the right spindle depends on material, speed, and cooling system.
- Professional repair is recommended for complex spindle motor issues.
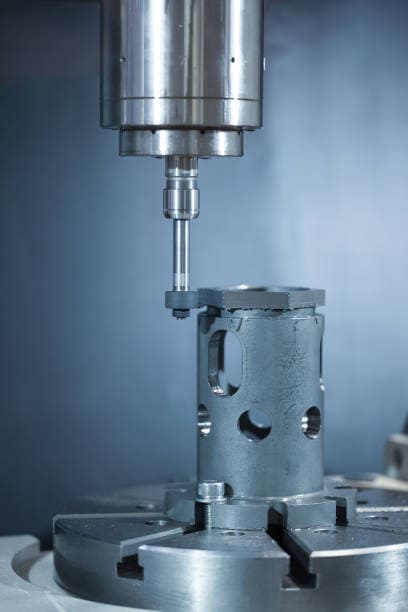
- RicoCNC has a team of professionals who have been engaged in the design, production, sales, and maintenance of electro spindles for many years. Our company accepts the purchase of various types of CNC spindles.
water-cooled CNC spindle motors
Edge banding machine spindle motors.
- If you need any CNC spindle, please contact us.