Introduction
Choosing the right CNC spindle is crucial for professionals and hobbyists alike. Whether you’re working on intricate woodworking designs or heavy-duty machining, the correct spindle determines the precision, speed, and overall efficiency of your CNC machine. This article will delve into the intricacies of selecting the right spindle for your CNC engraving machine, ensuring you understand the technical factors that influence performance and longevity. From spindle types to maintenance tips, this guide will equip you with the knowledge you need to optimize your CNC setup.
Understanding CNC Spindles and Their Importance in Woodworking
At the core of every CNC machine lies the spindle. It powers the cutting tool, dictating the material removal process through rotational motion. In woodworking, CNC spindles play a critical role in delivering the necessary force and precision, especially when working with intricate designs or fragile materials. Whether you’re cutting, engraving, or shaping wood, the spindle’s speed and torque determine the quality and precision of your work. Understanding how spindles function and their key features is essential for any CNC operator looking to optimize their setup.
The Role of Spindles in CNC Engraving Machines
In CNC engraving machines, spindles are responsible for driving the cutting tools, enabling high-speed rotations that allow the machine to carve out intricate details. Unlike handheld routers, CNC spindles are more powerful, durable, and designed for continuous operation, making them perfect for professional applications. The role of the spindle in CNC engraving extends beyond simply turning the tool—it directly influences the accuracy, detail, and finish of the final product.
Key Features of CNC Spindles for Woodworking Projects
When working with wood, certain features in a spindle are indispensable. These include adjustable RPM settings, which provide flexibility depending on the material type, and torque, which ensures the spindle maintains its cutting power even under load. Additionally, spindles with precision bearings reduce vibration, helping to achieve smooth cuts and avoid material warping. For intricate engraving work, CNC spindles with higher speeds (up to 24,000 RPM) are often preferred due to their ability to handle fine details efficiently.
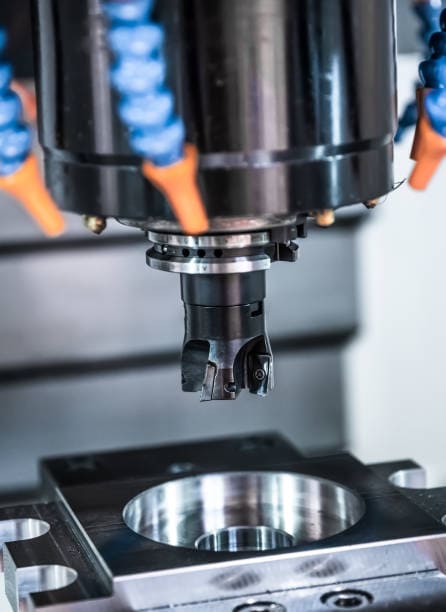
Types of Spindles for CNC Machines
There are several types of spindles available for CNC machines, each with its unique advantages and disadvantages. These spindles vary by size, cooling method, power rating, and intended use. Below, we explore the most common types of CNC spindles used in engraving and woodworking.
High-Speed Electric Spindles: Benefits for Fine Detail Work
High-speed electric spindles are ideal for applications that require extreme precision and fine detail work. These spindles can reach speeds of up to 30,000 RPM, making them perfect for intricate woodworking tasks. Their ability to rotate at such high speeds ensures that the cutting tool can produce smooth finishes without tearing or chipping the material. Additionally, high-speed electric spindles reduce the need for manual adjustments, as they are often equipped with programmable speed controls that automatically adjust to the material type.
Air-Cooled vs. Water-Cooled Spindles: Which Is Better for Your Needs?
The cooling system of a spindle is a crucial consideration for any CNC operator, especially when the machine is expected to run for extended periods. Spindles are typically available in two cooling configurations: air-cooled and water-cooled.
**Air-Cooled Spindles:** These spindles rely on fans to dissipate heat generated during operation. Air-cooled spindles are easier to maintain, more cost-effective, and are ideal for light to moderate workloads. However, they can become noisy and less efficient in heat dissipation when used continuously for long hours.
**Water-Cooled Spindles:** Water-cooled spindles offer superior cooling efficiency and operate more quietly than their air-cooled counterparts. They use a closed-loop system to circulate water around the spindle, effectively keeping the temperature low, even during prolonged use. Water-cooled spindles are better suited for high-volume and industrial applications where continuous operation is required. However, they require more maintenance due to the water cooling setup, which includes pumps, tubing, and potential leak points.
Here is a quick comparison:
Feature | Air-Cooled Spindle | Water-Cooled Spindle |
---|---|---|
Cooling Efficiency | Moderate | High |
Noise Level | Loud | Quiet |
Maintenance | Low | High |
Application | Light to Moderate Workloads | Heavy-Duty, Continuous Work |
Factors to Consider When Choosing a CNC Spindle
Selecting the right CNC spindle involves a careful evaluation of several factors. From the power rating to compatibility with your CNC machine, these considerations will help ensure that your spindle operates efficiently and delivers the desired results.
Determining the Right Size and Power for Your Projects
When selecting a CNC spindle, it’s crucial to choose the right size and power for your specific project. The spindle’s power, typically measured in kilowatts (kW), determines how easily it can cut through materials. For smaller woodworking projects, a spindle with 1.5 kW to 2.2 kW of power may be sufficient. However, larger projects or more demanding materials, such as hardwood or composites, may require spindles with higher power outputs, ranging from 3 kW to 7.5 kW or more.
To calculate the required spindle power, the following formula is often used:
Spindle Power (kW) = Torque (Nm) x Speed (RPM) / 9550
In this formula, torque is measured in Newton-meters (Nm) and speed in revolutions per minute (RPM). This equation provides a simple method to estimate the spindle power necessary for your specific application.
Compatibility with Your CNC Machine and Materials
Compatibility is another critical factor to consider when choosing a spindle. Not all spindles are designed to fit every CNC machine, so it’s important to verify that your chosen spindle is compatible with your machine’s frame and controller. Additionally, certain spindles are better suited for specific materials. For example, softwood and plastic may require a high-speed spindle, while harder materials, like aluminum or hardwood, may need a spindle with more torque and lower RPM.
Maintenance Tips for CNC Spindles
Proper maintenance of CNC spindles is essential for their longevity and continued performance. Regular maintenance prevents breakdowns, ensures consistent output, and extends the life of your machine. Below are several essential maintenance practices.
Routine Maintenance Practices to Extend Spindle Life
- Lubrication: Ensure that spindle bearings are regularly lubricated. Proper lubrication reduces friction and prevents the bearings from overheating, which can lead to premature failure.
- Cleaning: Dust and debris can accumulate in the spindle housing and bearings, leading to wear and tear. Regular cleaning with compressed air or a vacuum helps to remove debris and keep the spindle operating smoothly.
- Temperature Monitoring: Overheating is a common issue with spindles, particularly in heavy-duty applications. Regularly monitor the spindle’s temperature during operation to ensure it stays within safe operating limits.
Troubleshooting Common Spindle Problems
Despite proper maintenance, spindles may occasionally experience problems, including excessive vibration, overheating, or tool run out. Addressing these issues early can prevent costly repairs or replacements.
- Vibration: Excessive vibration is often caused by worn bearings or misalignment. Ensure that the spindle is properly aligned and that bearings are replaced if worn.
- Overheating: If a spindle frequently overheats, check the cooling system (air or water-cooled). Ensure that airflow is unobstructed in air-cooled spindles and that water is flowing correctly in water-cooled spindles.
- Tool Runout: Tool runout, or wobbling of the cutting tool, can lead to inaccurate cuts. This issue is often due to spindle wear or improper tool installation. Check the spindle and re-align or replace any worn components.
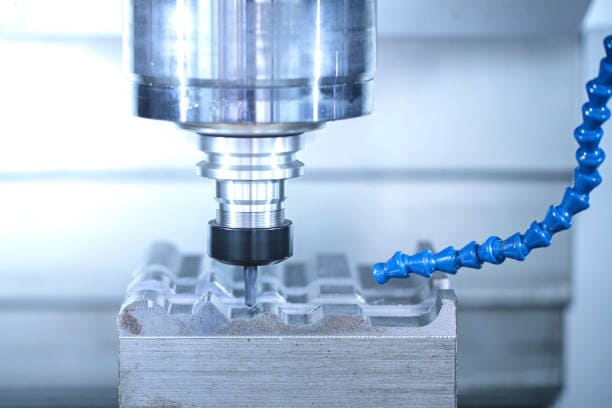
Conclusion
Selecting the right CNC spindle for your engraving or woodworking projects is a critical decision that impacts the quality, speed, and efficiency of your work. By understanding the different spindle types, considering factors such as power, cooling methods, and compatibility with your CNC machine, and maintaining your spindle properly, you can optimize your CNC machine’s performance. Whether you’re working on small, intricate designs or large-scale machining projects, choosing the right spindle ensures that your machine operates at its full potential.
FAQ
- What size spindle do I need for intricate woodworking projects? A high-speed spindle with 1.5kW to 2.2kW of power is usually sufficient for intricate woodworking projects.
- How do I know if a spindle is compatible with my CNC machine? Check the machine’s manual for the recommended spindle size, RPM range, and tool compatibility before making a purchase.
Key Takeaways:
- Choose a spindle that suits your project’s material and complexity.
- Maintain your spindle regularly to ensure long-lasting performance.
- Understand the differences between air-cooled and water-cooled spindles to make an informed decision.
- Ensure spindle compatibility with your CNC machine before purchasing.
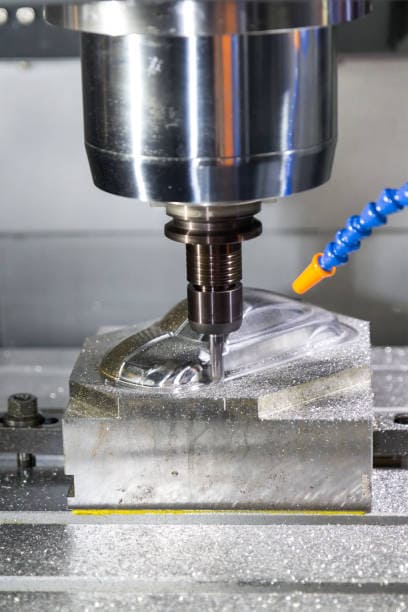
- RicoCNC has a team of professionals who have been engaged in the design, production, sales, and maintenance of electro spindles for many years. Our company accepts the purchase of various types of CNC spindles.
water-cooled CNC spindle motors
Edge banding machine spindle motors.
- If you need any CNC spindle, please contact us.