CNC machines are powerful tools that have revolutionized industries, from automotive and aerospace to woodworking and metalworking. The ability to precisely cut, shape, and engrave materials through automation has opened up endless possibilities for creators, inventors, and businesses alike. In this guide, we will explain everything you need to know about CNC machining, including the steps involved, software requirements, and tips on making the most out of your CNC projects. If you’re wondering how to CNC effectively, you’ve come to the right place.
What is CNC?
CNC stands for Computer Numerical Control. It refers to a technology where computer software controls the movement of machinery to carry out a task. Typically, CNC machines work by using commands programmed through a computer. These commands tell the machine how to perform specific tasks, such as cutting, drilling, or milling parts with high precision.
CNC machines come in various forms, including milling machines, lathes, routers, and plasma cutters. Each of these machines can be configured to handle different tasks, depending on the materials and project requirements.
Key Components of a CNC System
A CNC system generally includes the following components:
- CNC Machine: This is the physical machinery that performs the action, whether it’s cutting, drilling, or engraving.
- Controller: The controller is responsible for interpreting the commands and sending signals to the machine to move the tool.
- CAM Software: Computer-Aided Manufacturing (CAM) software generates the G-code (machine language) used by the CNC machine to execute commands.
- Tooling and Spindles: The tool (such as a drill bit) and spindle are the parts that directly interact with the material.
Steps to CNC Successfully
To get started with CNC machining, it’s important to understand the steps involved in taking a project from design to finished product.
1. Choose the Right CNC Machine for Your Project
Before you begin, you need to determine which type of CNC machine is right for your project. CNC machines vary in size and capability:
- CNC Routers: Great for woodworking and creating intricate designs.
- CNC Milling Machines: Best for metalworking and precision cutting.
- CNC Lathes: Ideal for creating cylindrical parts, like rings and shafts.
2. Design Your Part Using CAD Software
The next step is to design your part using CAD (Computer-Aided Design) software. CAD software lets you create a digital 2D or 3D model of the object you wish to manufacture. Popular CAD software includes AutoCAD, Fusion 360, and SolidWorks.
Keep the following tips in mind when designing:
- Simple Designs Are Easier: If you’re new, start with simpler designs. This will make the machining process easier and give you a sense of accomplishment.
- Keep Your Tools in Mind: Consider the size of your CNC machine’s tools, as some intricate details may be impossible to achieve with larger bits.
3. Convert Your Design to G-Code Using CAM Software
Once your design is complete, it needs to be translated into G-code, the language that CNC machines understand. CAM software like Fusion 360 or MasterCAM is used to convert the CAD file into a machine-readable format.
The process involves specifying tool paths, cutting speeds, and the depth of cuts. It’s critical to configure these parameters accurately, as they directly affect the quality of the final product.
4. Set Up Your CNC Machine
After generating the G-code, you need to set up your CNC machine. This step involves:
- Clamping the Material: The raw material should be securely clamped to the machine bed.
- Install Tooling: Attach the correct cutting tool or spindle for your project.
- Load the G-Code: Load the generated G-code file into the machine’s control software.
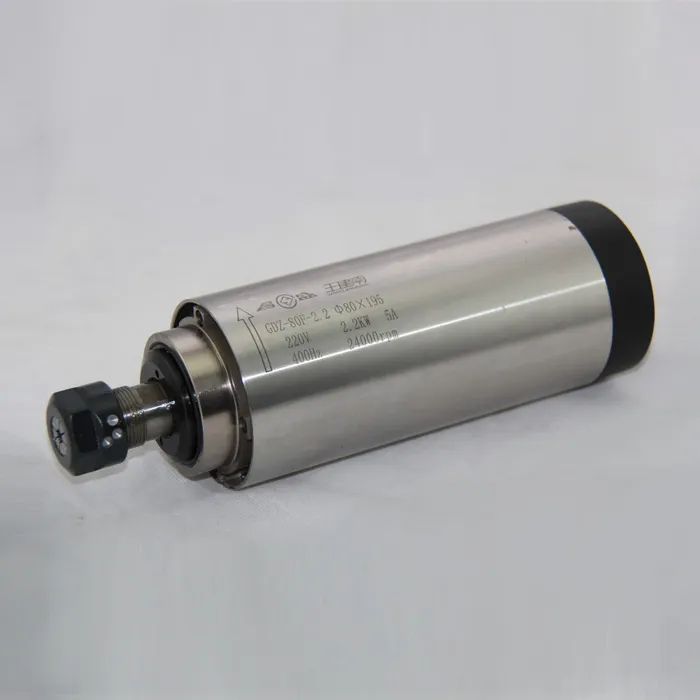
To ensure precise machining, consider using high-quality spindles like our 2.2KW ER20 Air-Cooled Spindle, which can improve your output quality.
5. Run the CNC Machine
Once everything is set up, it’s time to run the CNC machine. Here are some important considerations:
- Test Runs: Run a test piece before using the final material. This ensures the settings are correct and avoids costly errors.
- Monitor the Process: While CNC machines can work autonomously, it’s important to monitor them in case of issues like tool breakage or misalignment.
- Adjust Feed Rate: You may need to adjust the feed rate to get the best quality or finish.
6. Post-Processing and Finishing
Once your part is complete, there are usually additional steps involved in finishing the product. This may include:
- Sanding and Polishing: If you’re working with wood or metal, some sanding and polishing may be necessary to achieve a smooth finish.
- Painting or Coating: Adding a protective coating or paint can improve the durability and appearance of your CNC project.
Common CNC Tools and Their Uses
When working with a CNC machine, it is essential to use the correct tooling for your project. Here is a table highlighting common CNC tools and their uses:
Tool Type | Common Use |
---|---|
End Mill | Cutting slots, contours, and edges |
Ball Nose Bit | Curved and rounded carvings |
V-bit | Engraving letters and intricate details |
Drill Bit | Creating holes of different sizes |
Face Mill | Flattening surfaces |
Using the right tool can make a significant difference in both the quality and speed of your project. Quality CNC spindle motors like our 60000RPM 1.2KW ER11 Water-Cooled Spindle can help maintain precision during your milling process.
Tips for Successful CNC Projects
Successfully working with CNC machines requires more than just technical knowledge. Here are some helpful tips to improve your CNC projects:
1. Start with Simple Projects
If you are a beginner, start with simpler projects to build your confidence. Creating small, simple shapes will help you understand the machine, software, and workflow before moving on to more complex parts.
2. Keep Your Tools Sharp
Sharp tools are crucial for precision machining. Dull tools can lead to inaccuracy, rough finishes, and tool breakage. Regularly inspect and replace any worn tools to ensure the best results.
3. Understand Your CNC Software
Invest time to learn the ins and outs of your CAD and CAM software. Proper understanding allows you to utilize advanced features like toolpath optimization, which can reduce machining time and improve quality.
CNC Milling vs. CNC Routing
Both CNC milling and CNC routing are popular CNC machining techniques, but they serve different purposes:
- CNC Milling: Typically used for metals, involving cutting materials with a rotary cutter.
- CNC Routing: Mostly used for woodworking and plastic, using high-speed tools to carve out designs.
The main difference is in the materials used and the level of detail achieved. CNC milling provides higher precision, making it suitable for industrial applications.
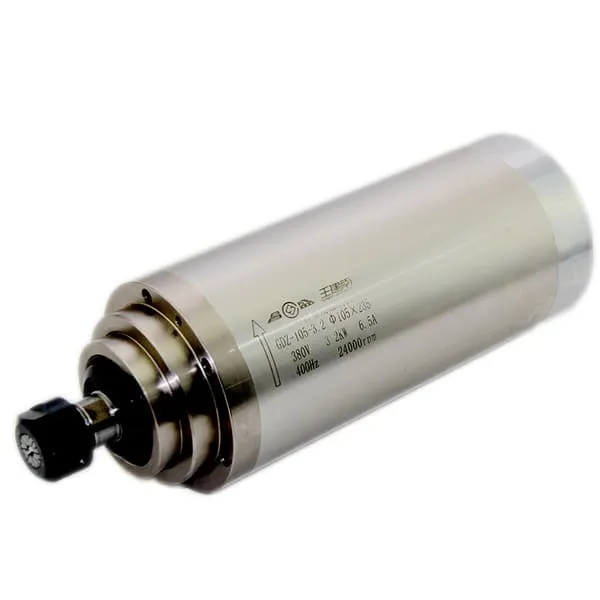
For advanced routing needs, consider investing in our 24000RPM 3.2KW ER20 Water-Cooled Router Spindle.
FAQs
1. How do I choose the right CNC machine for my project?
The choice depends on the material you plan to work with and the level of detail needed. CNC routers are great for wood and plastic, while CNC milling machines are ideal for metals and detailed precision work.
2. What software is needed for CNC machining?
You need both CAD software (like Fusion 360 or AutoCAD) for designing and CAM software for generating G-code. There are many options, and it often comes down to personal preference.
3. Can I use a CNC router for metals?
Yes, CNC routers can work on soft metals like aluminum. However, for harder metals like steel, it’s best to use a CNC milling machine.
4. How long does it take to learn CNC machining?
Learning CNC machining can take anywhere from a few weeks to several months, depending on your prior experience and the complexity of projects you plan to undertake.
5. Why is spindle quality important in CNC machining?
A high-quality spindle ensures precision, reduces vibration, and allows for longer run times. It’s a crucial component for achieving accurate and high-quality results in CNC machining.
Conclusion
CNC machining offers a world of opportunities for creators, businesses, and manufacturers. Understanding the process—from choosing the right machine, designing with CAD software, generating G-code, to setting up your CNC machine and running it—can help you create detailed, intricate, and beautiful projects. By investing in high-quality tools like our 2.2KW ER20 Air-Cooled Spindle, you can take your CNC machining capabilities to the next level.
Whether you’re a hobbyist looking to create custom projects or a professional wanting to improve production efficiency, CNC technology is the tool that can bring your ideas to life. Start with simple designs, learn the software, and gradually build up to complex creations. The journey of CNC machining is filled with learning, creativity, and endless potential for success.