Control CNC Spindle for Optimal Performance: A Complete Guide
Are you struggling with controlling your CNC spindle for precision and performance? Wondering how to calculate the optimal spindle speed or troubleshoot common spindle issues?
Controlling a CNC spindle is at the heart of successful machining. Ensuring that your spindle runs at the correct speed, maintain accuracy, and is well-maintained can lead to high-quality parts, reduced wear, and overall operational efficiency. This guide will walk you through the essentials of spindle control, from the basics of operation to advanced troubleshooting and maintenance techniques.
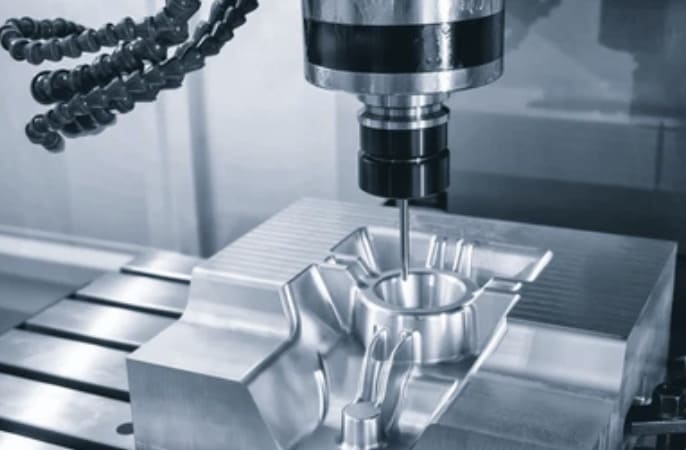
The Basics of CNC Spindle Operation
What exactly is a CNC spindle, and how does it work?
At its core, the CNC spindle is the driving force behind the cutting tool. It rotates the tool at the correct speed, ensuring that each cut is precise and efficient. A spindle consists of several components, including a motor, bearings, and a spindle shaft that holds the cutting tool.
When a CNC machine is running, the spindle’s rotation speed (measured in RPM) and feed rate (how fast the cutting tool moves through the material) must work together for the best results. If not controlled properly, the spindle could overheat, damage the tool, or produce poor-quality cuts.
Key Components of a CNC Spindle System
What are the critical parts of a CNC spindle system?
A CNC spindle system is composed of various interconnected parts that work together for smooth operation. Understanding these components can help in identifying potential issues or ways to improve your spindle control. The main components include:
- Motor: The spindle motor powers the spindle’s rotation. The type of motor (AC or DC) influences torque and speed.
- Spindle Bearings: Bearings reduce friction and allow smooth rotation, impacting the spindle’s performance and lifespan.
- Spindle Shaft: The shaft holds the cutting tool and transfers the motor’s energy to the material being machined.
- Control System: This component manages spindle speed, acceleration, and braking, typically through digital or manual inputs.
Each part plays a role in maintaining spindle stability and accuracy, which is essential for high-quality machining.
Factors Affecting Spindle Speed Selection
How do you determine the right spindle speed for different materials?
Choosing the right spindle speed is critical for efficient machining. Several factors influence the speed at which the spindle should operate, including:
- Material Type: Softer materials like plastic require lower spindle speeds, while harder materials like steel demand higher speeds.
- Tool Diameter: Larger tools need slower speeds to maintain stability, whereas smaller tools can run at higher RPMs.
- Cutting Depth: A deeper cut usually requires a lower spindle speed to prevent tool wear and overheating.
When machining, it’s crucial to balance these factors to avoid poor part quality or damage to both the spindle and the workpiece.
Material | Recommended Speed (RPM) |
---|---|
Aluminum | 8,000 – 12,000 |
Steel | 2,000 – 4,000 |
Plastic | 10,000 – 18,000 |
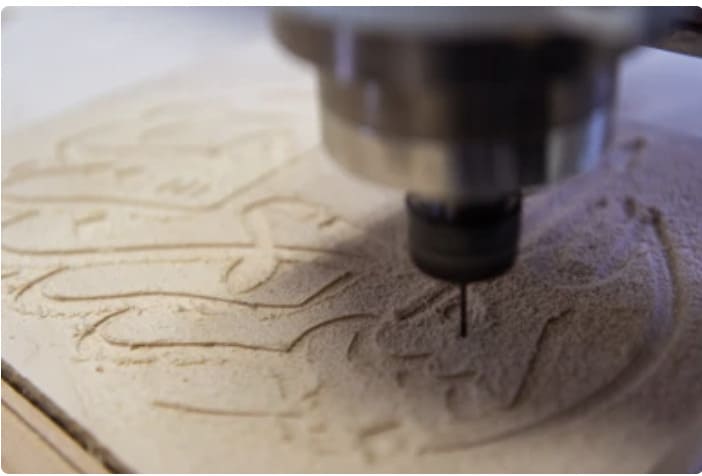
Step-by-Step Guide to Calculating Spindle Speed
How do you calculate the optimal spindle speed?
Calculating spindle speed is vital for efficient machining. Use this simple formula to determine the correct RPM (Revolutions Per Minute):
Spindle Speed (RPM) = (Cutting Speed × 1000) ÷ (π × Tool Diameter)
For example, if you’re cutting aluminum with a cutting speed of 300 m/min and using a tool with a 10mm diameter, the calculation would look like this:
Spindle Speed = (300 × 1000) ÷ (3.14 × 10) = 9,549 RPM
This ensures that the spindle is running at an optimal speed, reducing tool wear and improving surface finish.
The Role of Feed Rate in Spindle Control
How does feed rate influence spindle performance?
The feed rate refers to how fast the cutting tool moves through the material, and it directly affects spindle control. An overly high feed rate can cause the spindle to overload, leading to tool breakage, while a low feed rate can reduce productivity.
To calculate the ideal feed rate, consider these factors:
- Material Hardness: Harder materials require a slower feed rate to prevent tool damage.
- Tool Size: Larger tools can handle faster feed rates compared to smaller tools.
- Spindle Speed: The feed rate must complement the spindle speed for smooth operation.
Always ensure that the feed rate and spindle speed are balanced for the material and tool being used.
Techniques for Improving Spindle Speed Accuracy
What are the best practices for ensuring precise spindle speed control?
Precision in spindle speed control is critical for producing high-quality parts. To improve accuracy, consider implementing the following techniques:
- Regular Calibration: Periodically check your CNC machine’s spindle calibration to ensure that the speed matches the programmed settings.
- Use Advanced Controllers: Modern CNC controllers often have features that allow for more accurate speed adjustments, such as closed-loop feedback systems.
- Monitor Thermal Expansion: Spindles can expand slightly due to heat, which can affect speed accuracy. Use sensors to monitor temperature and adjust spindle speed accordingly.
By keeping these techniques in mind, you can significantly enhance the precision and efficiency of your CNC operations.
Recommended Software for Spindle Control
What software tools are available to control CNC spindle speed?
Several software programs help optimize CNC spindle speed and enhance overall control. These tools can automatically adjust speeds based on material properties and tool data. Some popular options include:
- Mach3: A highly customizable software that allows real-time adjustments to spindle speed and feed rates.
- CNC Simulator Pro: Ideal for simulating and controlling spindle speed before running the actual program.
- Fusion 360: Combines CAD/CAM functionality with tools for spindle speed control, enabling you to plan and test machining strategies digitally.
Using these software tools can greatly enhance your control over spindle speed and machining accuracy.
Utilizing Digital Tools for Precise Speed Adjustments
How can digital tools improve spindle speed control?
Digital tools, such as digital tachometers and CNC control software, make precise spindle speed adjustments easier and more reliable. These tools provide real-time feedback, allowing you to monitor the spindle’s performance and make adjustments instantly.
- Digital Tachometers: Measure the actual RPM of the spindle, ensuring the machine runs at the programmed speed.
- CNC Software Integration: Many CNC programs now offer integrated control options for spindle speed, making it easy to fine-tune performance during machining.
By leveraging digital tools, you can increase accuracy, reduce human error, and boost machining efficiency.
Identifying Symptoms of Spindle Malfunction
What are the signs of a failing CNC spindle?
Identifying a spindle malfunction early can save you from costly repairs or machine downtime. Some common symptoms of spindle problems include:
- Increased Vibration: Excessive vibration may indicate bearing wear or an unbalanced spindle.
- Inconsistent Speed: If the spindle speed fluctuates during operation, this could be a sign of motor or control system failure.
- Poor Surface Finish: A deteriorating spindle may lead to rough or uneven surface finishes on the machined part.
If you notice any of these symptoms, it’s important to troubleshoot immediately to avoid further damage.
Step-by-Step Troubleshooting Guide
How do you troubleshoot common spindle issues?
Here’s a simple step-by-step guide to troubleshooting spindle problems:
- Check Bearings: Inspect spindle bearings for wear or damage. Replace if necessary.
- Examine the Motor: Ensure the motor is providing consistent power. Test for electrical issues that could affect spindle speed.
- Look for Loose Components: Vibrations can be caused by loose components in the spindle assembly.
- Test Spindle Runout: Use a dial indicator to check for spindle runout, which may indicate misalignment or wear.
Following these steps will help you identify and fix most spindle issues, keeping your machine running smoothly.
Routine Maintenance Checklist for CNC Spindles
How often should spindle maintenance be performed?
Routine checks should be performed every 6 to 12 months, depending on the machine’s usage and the precision requirements of your operations. High-precision jobs, especially those in aerospace or medical industries, may require more frequent alignment checks.
Best Practices for Long-Term Spindle Care
What are the best practices for maintaining CNC spindles over the long term?
To ensure long-term spindle performance, follow these best practices:
- Regular Cleaning: Keep the spindle clean and free of debris to prevent contamination.
- Lubrication: Apply the recommended lubricant to bearings and other moving parts to reduce friction and wear.
- Monitor Performance: Continuously monitor spindle performance using digital tools to catch issues before they become serious problems.
By adhering to these practices, you can extend the lifespan of your spindle and maintain its performance.
When to Consider Upgrading Your Spindle
How do you know when it’s time to upgrade your CNC spindle?
Consider upgrading your spindle if:
- Performance Issues: If you frequently encounter performance problems or cannot achieve desired accuracy, a new spindle may be necessary.
- Technological Advancements: Newer spindles often come with improved features and efficiency. Upgrading can enhance your machine’s capabilities.
- Increased Workload: If your production needs have increased, a more robust spindle may be required to handle higher demands.
Selecting the Right Spindle for Your CNC Machine
What should you consider when selecting a new spindle for your CNC machine?
When choosing a spindle, consider:
- Compatibility: Ensure the spindle is compatible with your CNC machine’s specifications.
- Performance Requirements: Match the spindle’s speed and power capabilities with your machining needs.
- Budget: Balance performance features with your budget constraints to find the best spindle for your needs.
Careful selection will ensure you get a spindle that enhances your machining capabilities and meets your operational requirements.
Conclusion
- Proper spindle control is essential for maintaining accuracy and extending tool life.
- Use precise calculations for spindle speed and consider digital tools for improved control.
- Regular maintenance and timely upgrades can prevent issues and improve performance.
Incorporating spindle control into your CNC maintenance routine will save you time, money, and frustration in the long run. Whether you’re a seasoned operator or new to CNC machining, understanding how to control your spindle is essential for delivering high-quality parts every time.
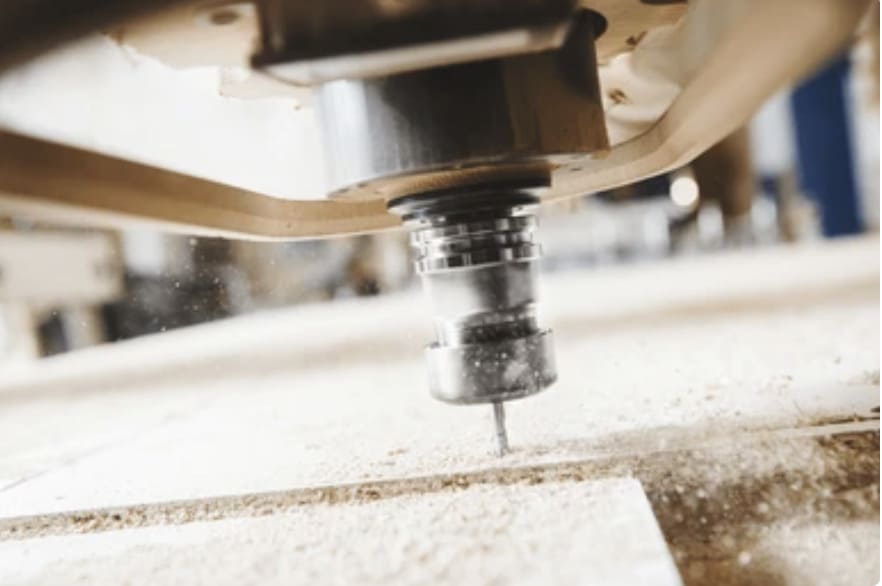
- RicoCNC has a team of professionals who have been engaged in the design, production, sales, and maintenance of electro spindles for many years. Our company accepts the purchase of various types of CNC spindles.
water-cooled CNC spindle motors
Edge banding machine spindle motors.
- If you need any CNC spindle, please contact us.