Introduction
As one of the core components of CNC machine tools, the CNC spindle is responsible for driving the workpiece or tool to rotate. However, the electro spindle will inevitably have various faults in long-term use. This article will introduce common spindle faults and their solutions in detail.
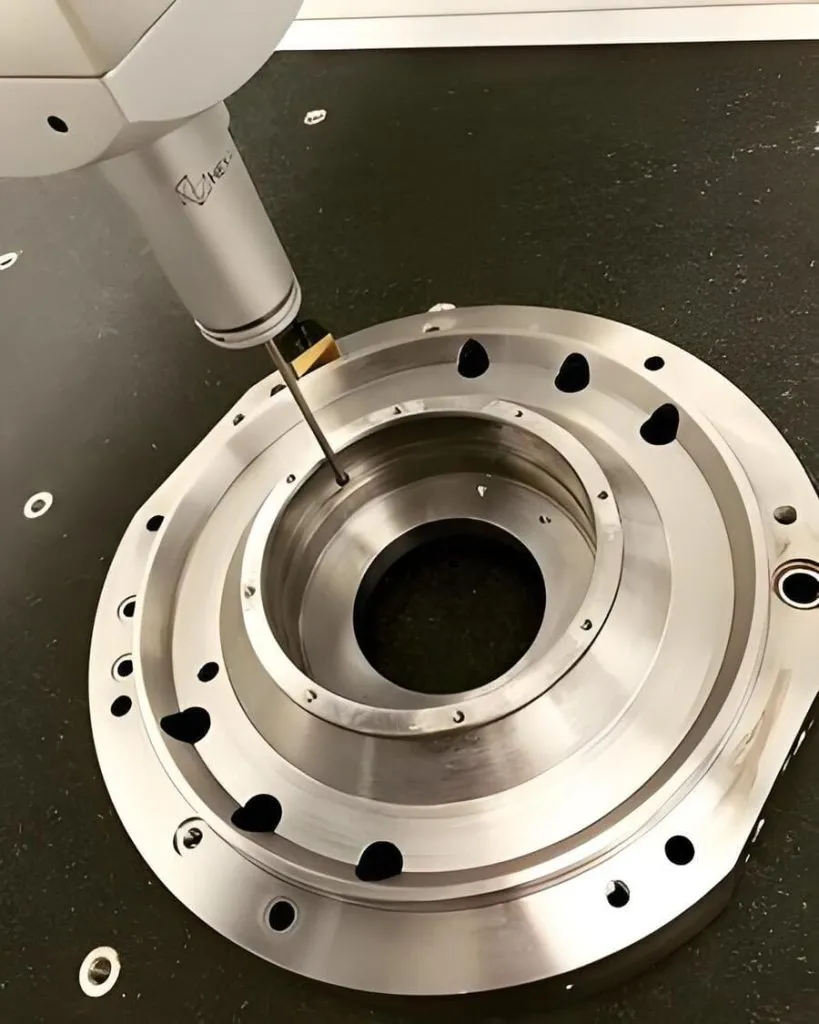
The spindle has no brake
The braking circuit is abnormal, or vital circuit components are damaged
If the spindle cannot brake normally, first check the braking circuit. There may be damage to the bridge pile, fuse, or AC contactor. Check whether these components are damaged and ensure the robust circuit is complete without an open circuit.
The braking time is not long enough
If the braking time is insufficient, adjust the braking time parameters of the system or inverter to ensure that the spindle can complete braking within the predetermined time.
The system has no braking signal output
When the system has no braking signal output, it may be necessary to replace internal components or send the equipment to the factory for repair.
Inverter control parameters are not adjusted properly
If the control parameters of the inverter are not set correctly, it will affect the braking effect of the spindle. The inverter manual should be consulted to ensure all parameters are set correctly.
The spindle stops immediately after starting
System output pulse time is not enough
If the spindle stops immediately after starting, it may be because the system pulse output time is not set enough.
Inverter is in a jog state
If the inverter is in a jog state, refer to the inverter manual and set the correct parameters to solve this problem.
The control components of the spindle circuit are damaged
Check the contact condition of the contacts on the circuit to ensure that the control components, such as DC relays and AC contactors, are working correctly to avoid the spindle stopping due to the non-self-locking of the contacts.
The spindle motor is short-circuited, causing thermal relay protection
The short circuit of the spindle motor will cause thermal relay protection. It is necessary to find the cause of the short circuit and reset the thermal relay to restore the regular operation of the spindle.
The spindle control circuit does not have a self-locking circuit
If the spindle control circuit does not have a self-locking circuit and the parameters are set to pulse signal output, the spindle cannot operate normally. The start and stop parameters of the system control spindle should be changed to level control mode.
The spindle rotation cannot stop.
If the spindle cannot stop after rotation, it may be due to damage to the AC contactor or DC relay, resulting in long-term pull-in. These damaged parts need to be replaced to solve the problem.
The spindle rotates immediately as soon as the system is powered on
The AC contactor or DC relay is damaged
The spindle rotates as soon as it is powered on, possibly due to damage to the AC contactor or DC relay. These parts need to be replaced to solve the spindle control problem.
The spindle does not rotate when the inverter is connected
The three-phase power supply to the spindle is missing a phase
If the spindle does not rotate after the inverter is connected, it may be due to the three-phase power supply missing a phase. Check the power supply and swap two power lines to restore regular operation.
The inverter control parameters of the CNC system are not turned on
You must consult the system manual to understand and change the inverter control parameters to ensure the spindle can rotate normally.
The line connection between the system and the inverter is wrong
Ensure that the line connection between the system and the inverter is correct, and refer to the wiring manual for inspection and correction.
The analog voltage output is abnormal
Use a multimeter to check whether the analog voltage output by the system is standard, and ensure that the analog voltage signal line is well connected and the analog voltage received by the inverter matches.
The vital power control part is broken, or the components are damaged
Please check whether the contacts of the spindle power supply line are connected reliably, whether there is a circuit breaker in the line, whether the DC relay and fuse are damaged, etc.
.
The system analog voltage has no output, or there is a circuit break in the connection with the inverter.
Check whether the system has analog voltage output. If not, it is a system fault; if yes, check whether the line is broken.
System and inverter connection error
Refer to the connection manual to check whether the connection between the system and the inverter is correct.
System parameters or inverter parameters are not set properly
Open the system frequency conversion parameters and adjust the inverter parameters to ensure the spindle speed is usually controlled.
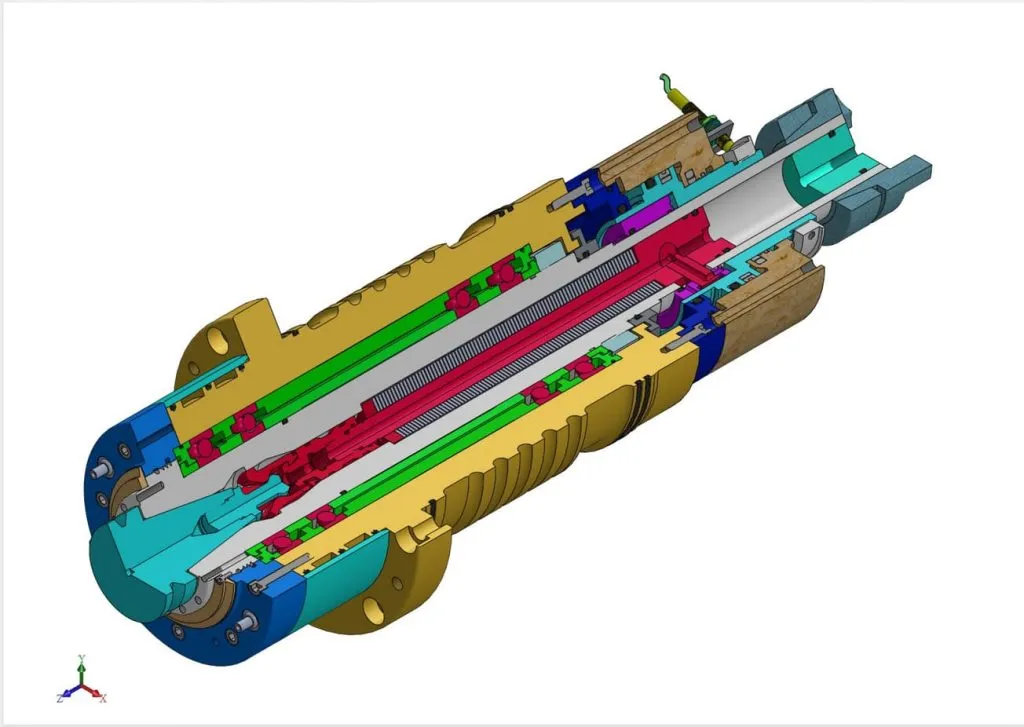
Conclusion
When repairing CNC machine tools, due to the complexity of the causes of the faults, the repair process needs to be checked step by step according to the causes of the faults. First, the possible causes of the faults should be listed, and a detailed troubleshooting plan should be formulated. Secondly, targeted repairs should be carried out after determining the fault location. In general, CNC machine tool spindle failures are more common. By mastering the mechanical structure of the spindle, analyzing the cause of the fault, and performing effective repairs, it can be ensured that the spindle returns to normal and the machine tool runs smoothly. Mastering this knowledge helps improve maintenance efficiency and ensure the stable operation of the production line.
Summary FAQ based on the article
1. What should I do if the spindle has no brake?
Check whether the braking circuit components are damaged, adjust the braking time parameters, and ensure the inverter control parameters are set correctly.
2. What is the reason for the spindle to stop immediately after starting?
It may be that the system output pulse time is not set enough, the inverter is in the jog state, or the spindle circuit control components are damaged.
3. What should I do if the spindle cannot stop rotating?
Checking and replacing the damaged AC contactor or DC relay is necessary.
4. What should I do if the spindle rotates immediately after powering the system?
Check and replace the damaged AC contactor or DC relay.
5. What are the reasons and solutions for the spindle not rotating when the inverter is connected?
Check whether the power supply is missing phase, confirm that the inverter control parameters have been opened correctly, and ensure the line connection is correct.
6. How to deal with the uncontrolled spindle speed controlled by the inverter?
Replace the motherboard with a frequency conversion function, check the system analog voltage output, ensure that the system and the inverter are correctly connected, and adjust the relevant parameters.
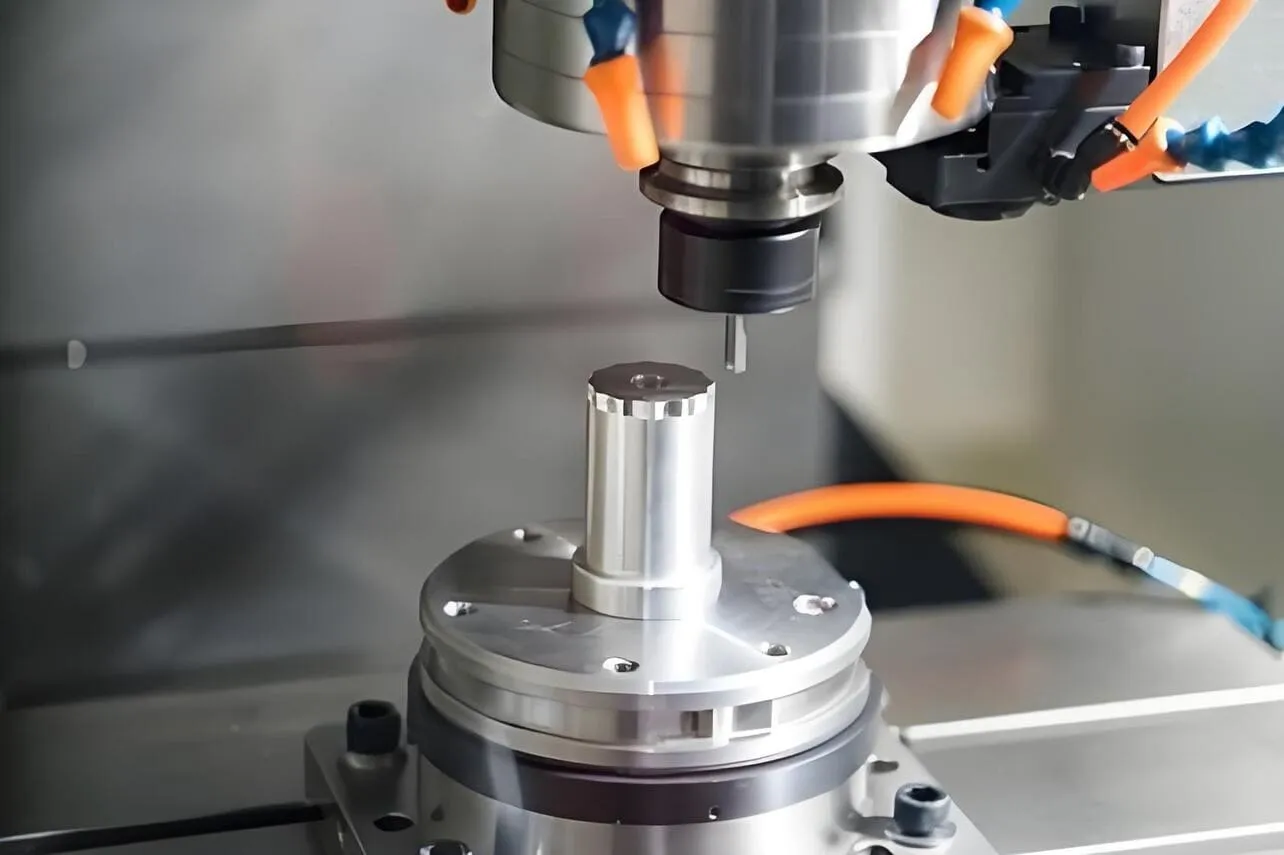
- RicoCNC has a team of professionals who have been engaged in the design, production, sales, and maintenance of electro spindles for many years. Our company accepts the purchase of various types of CNC spindles.
water-cooled CNC spindle motors
Edge banding machine spindle motors.
- If you need any CNC spindle, please contact us.