How to Operate a CNC Press Brake
The CNC press brake is a crucial piece of equipment in metalworking, designed to bend sheet metal into different forms using controlled force. Operating a CNC press brake requires skill, precision, and an understanding of both the machine and its programming. In this guide, we’ll take a deep dive into everything you need to know about how to operate a CNC press brake effectively, from the setup process to advanced techniques. Let’s begin.
What is a CNC Press Brake?
A CNC press brake is a type of bending machine that uses Computer Numerical Control (CNC) to shape sheet metal accurately and efficiently. It is equipped with a programmable controller that allows the operator to input precise bending angles, lengths, and tooling sequences. CNC press brakes can bend metal sheets of various thicknesses, making them highly versatile for many industries such as aerospace, automotive, and construction.
The main components of a CNC press brake include:
- Ram: The moving part that applies force to the metal sheet.
- Bed: The base where the metal sheet is positioned.
- Tooling (Punch and Die): The components that physically bend the sheet metal.
- CNC Controller: The interface where the operator programs the machine.
The use of CNC technology ensures repeatability and precision, which are essential when working with intricate metal parts.
Setting Up a CNC Press Brake for Operation
1. Understand the Machine Components
Before starting, it is essential to understand the various components of the press brake. This includes the hydraulic system, tooling, and CNC controller. Each part has a distinct function that contributes to the bending process:
- Hydraulics: Responsible for generating the force required to bend the metal.
- Tooling: The punch and die used in the bending process must be selected carefully based on the material type and thickness.
- CNC Controller: Used to input data regarding bending sequences and angles.
2. Tool Selection and Installation
Choosing the correct tooling is one of the most crucial parts of setting up a CNC press brake. Tooling is divided into two parts: punch and die. The punch presses the material into the die to create a bend. Different types of tools are used for various bending operations, including:
- V-dies: The most common type, used for general bending.
- Gooseneck Punches: Ideal for creating deep or intricate bends.
- Radius Dies: Used to create a bend with a rounded edge.
3. Material Placement and Alignment
Proper alignment of the sheet metal is essential to ensure consistent results. The metal sheet is placed on the bed and held in position using back gauges, which are adjustable components that help guide the material into the correct position. Aligning the metal correctly helps achieve the desired bend angle and length accurately.
- Use the back gauge for consistent alignment.
- Make sure the sheet is flush with the gauge to avoid errors in bending.
For more information on components that might be useful during setup, such as air-cooled spindles, you can visit 1.5KW ER11 Square Air-Cooled Spindle with Flange. This spindle is particularly useful for machining tasks that require precision.
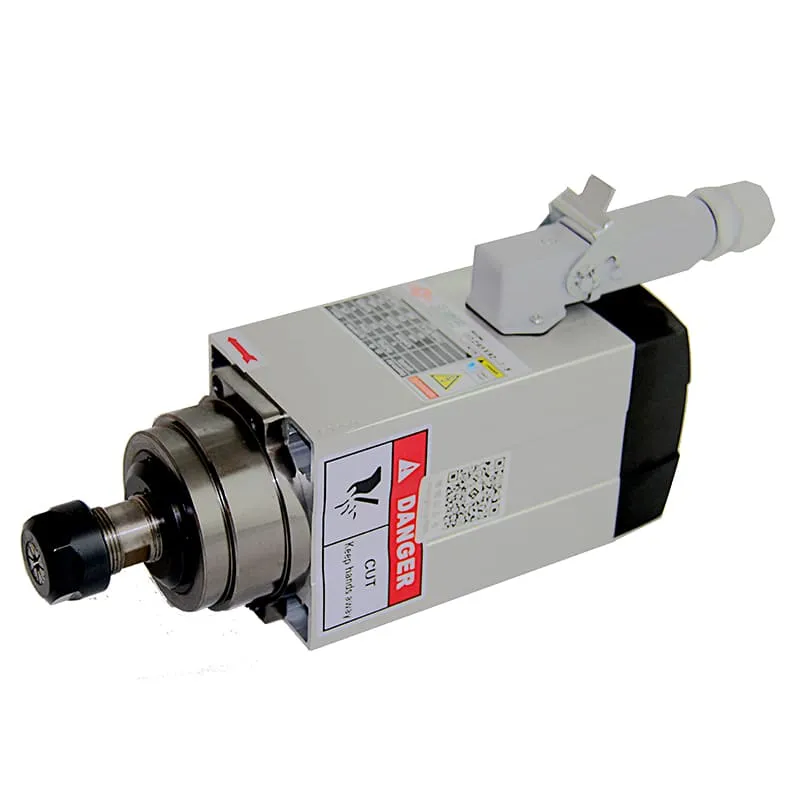
Programming the CNC Press Brake
1. Basics of CNC Programming for Press Brakes
The CNC controller is where all the data about the bending operation is input. The operator must program the following aspects:
- Bending Angle: The angle at which the metal should be bent.
- Material Thickness: The thickness of the sheet metal influences the type of die and the force applied.
- Bending Sequence: The order in which bends are made to avoid collisions and deformation.
The programming process usually starts with importing a CAD file, which contains the design of the part to be bent. The controller then translates this design into G-code, which controls the movement and operation of the press brake.
2. Using the CNC Interface
Most modern CNC press brakes come with a touchscreen interface that makes it easier for operators to input data and adjust parameters as needed. The interface allows for:
- Storing Programs: Frequently used bending sequences can be saved for future use.
- Error Checking: The system can often simulate a bending operation to detect potential issues before actual bending takes place.
For more robust bending operations, you might consider investing in advanced CNC components such as the 2.2KW ER25 Square Air-Cooled Spindle, which provides greater stability and precision.
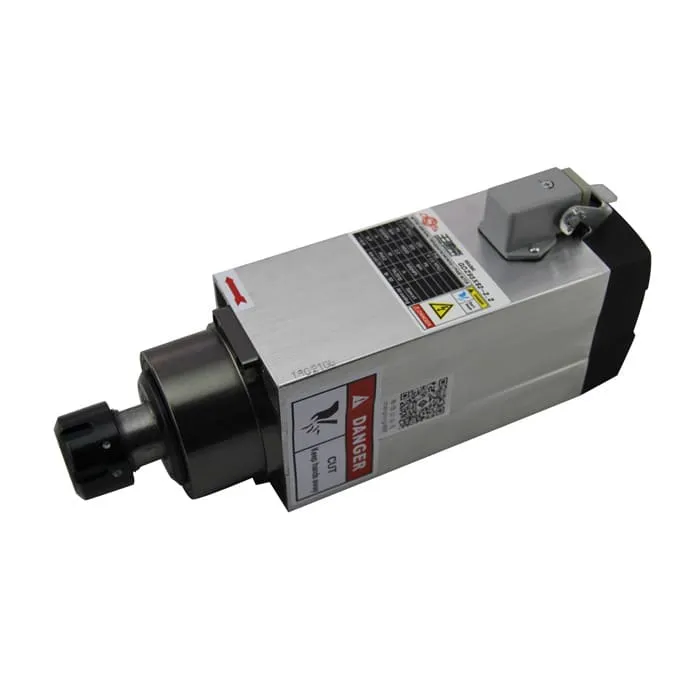
Safety Protocols for CNC Press Brake Operation
Safety is paramount when operating any heavy machinery, especially something as powerful as a CNC press brake. Improper handling can result in serious injury. Below are key safety measures:
1. Wear Appropriate Safety Gear
Always wear appropriate safety gear while operating a CNC press brake. This includes:
- Safety Glasses: To protect your eyes from flying debris.
- Gloves: To protect your hands while handling sheet metal.
- Steel-Toe Boots: To protect your feet from heavy materials.
2. Maintain a Safe Distance
- The operator should always stay clear of the moving ram to avoid injury.
- Use guards and safety devices installed on the press brake to ensure hands and fingers are kept away from the danger zone.
3. Regular Maintenance Checks
Maintenance of the CNC press brake is crucial for both safety and performance. Regular checks include:
- Inspecting Hydraulic Systems: Ensuring there are no leaks and that the pressure is adequate.
- Tooling Inspection: Checking for wear and tear on the punch and die.
- Calibration: Regular calibration helps maintain the accuracy of bends.
Bending Techniques and Methods
Bending techniques can vary depending on the type of material, the desired bend, and the thickness of the sheet metal. Below, we explore some of the most commonly used bending techniques.
1. Air Bending
Air bending is one of the most common techniques used in CNC press brake operation. In air bending, the sheet does not fully contact the die, which allows for different bending angles using the same tooling.
- Pros: Greater flexibility, reduced tooling costs.
- Cons: Less precision compared to bottom bending.
2. Bottom Bending
Bottom bending involves pressing the sheet metal against the bottom of the die, resulting in higher accuracy for bend angles. This technique requires more force but is suitable for high-precision projects.
- Pros: High accuracy and repeatability.
- Cons: Higher tooling wear and more power required.
For more detailed work involving multiple bends, it’s recommended to use a reliable spindle such as the 3.5KW ER25 Air-Cooled Spindle. This provides high performance and precision for more complex parts.
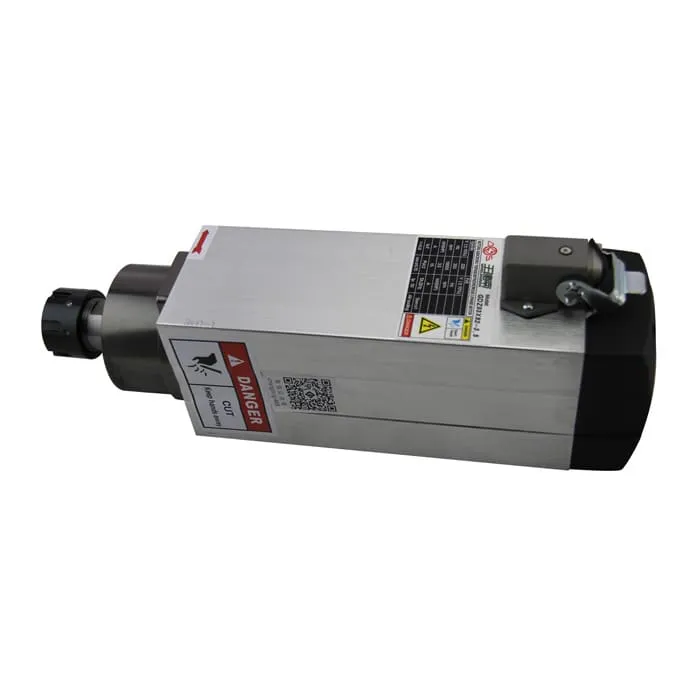
Common Mistakes and Troubleshooting Tips
Operating a CNC press brake can come with its own set of challenges, especially for those new to the process. Here are some common mistakes and how to avoid them:
1. Incorrect Tool Selection
Selecting the wrong tooling can lead to poor bends or even damage to the press brake. Always ensure that the punch and die are suitable for the material thickness and bend type.
2. Improper Material Positioning
Failing to align the metal sheet correctly can lead to inaccurate bends. Always use the back gauge and ensure that the sheet is flush against it before initiating a bend.
3. Inadequate Maintenance
Neglecting regular maintenance checks can lead to breakdowns or inconsistent performance. Regularly inspect the hydraulics, tooling, and CNC controller to ensure optimal performance.
Benefits of Using a CNC Press Brake
Using a CNC press brake offers several advantages that make it indispensable in modern metalworking. Here are some of the key benefits:
1. Precision and Accuracy
CNC press brakes provide unmatched precision, which is crucial for parts that require tight tolerances. The ability to program precise angles and bending sequences ensures consistency across multiple production runs.
2. Flexibility
With the programmable CNC controller, changing from one job to another is relatively easy. The operator can quickly load a new G-code program, change the tooling, and start a different bending sequence without lengthy setup times.
3. Reduced Waste
Automation reduces the potential for human error, leading to fewer scrapped parts. This translates into cost savings, especially in high-volume production runs.
Frequently Asked Questions (FAQs)
1. What safety precautions should be taken while operating a CNC press brake?
Always wear appropriate safety gear, stay clear of the moving ram, and regularly inspect the machine for potential safety hazards.
2. What is the difference between air bending and bottom bending?
Air bending uses less force and allows for more flexibility with different angles, while bottom bending offers higher precision but requires more force and specific tooling.
3. How do I choose the right tooling for a CNC press brake?
Choose the tooling based on the material thickness, the type of bend required, and the desired precision. For example, gooseneck punches are ideal for intricate bends.
4. How can I improve the accuracy of my bends?
Ensure proper alignment of the metal sheet, use the correct tooling, and regularly calibrate the CNC press brake to maintain accuracy.
5. What kind of materials can be bent using a CNC press brake?
A CNC press brake can bend various materials including steel, aluminum, brass, and copper. The type of material determines the tooling and the amount of force needed.
Conclusion
Operating a CNC press brake requires not only technical skill but also a deep understanding of the machinery and its components. From setting up the machine, selecting the right tooling, to programming the CNC controller, every step requires attention to detail to ensure optimal performance. By following the guidelines mentioned in this article, you can operate a CNC press brake efficiently and safely, producing high-quality bent parts for a wide range of applications. Remember, safety and precision are key elements in this process.
For more detailed insights into CNC spindle motors and other accessories, visit SpindleMotorShop, where you will find a variety of high-quality CNC components suitable for all your machining needs.