Introduction
The disassembly and assembly of a CNC spindle is a job that requires careful operation. The spindle is one of the core components of CNC machine tools. This article will introduce the disassembly and assembly process of a CNC spindle in detail and explain how to measure and adjust the accuracy of the spindle to ensure its normal operation after reinstallation.
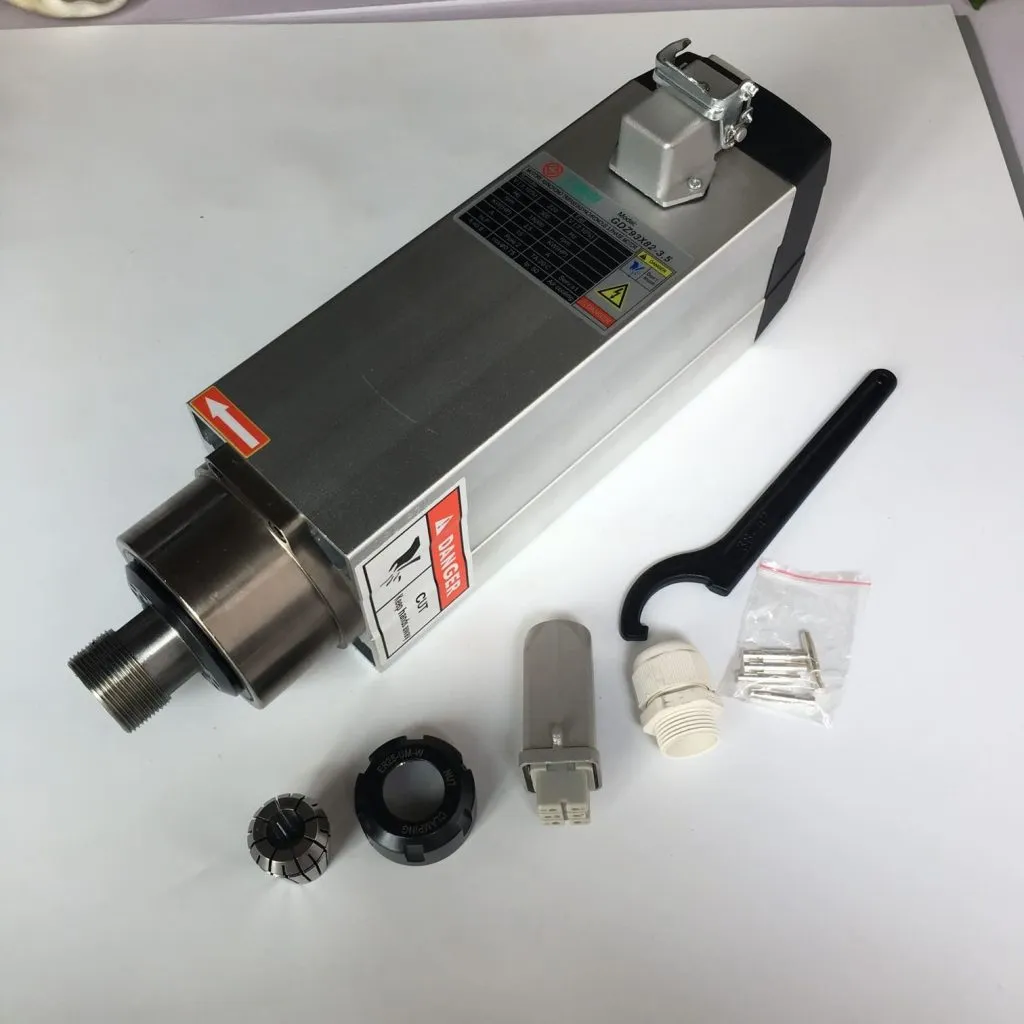
Disassemble the spindle
Disassembling the CNC spindle is not complicated, but you need to be extra careful during the operation, especially paying attention to the connection of the electrical, water, and air circuits.
Unplug the spindle power cord: Before disassembling the spindle, first disconnect the power connection to avoid accidents during the disassembling process.
Unplug the spindle cooling water pipe: Remove the spindle cooling system connection to prevent coolant leakage or affect the operation.
Unplug the spindle air pipe: Remove the air pipe connected to the spindle to ensure no interference from compressed air during the disassembling process.
Loosen the coupling screw: When the spindle is clamped or adequately supported, to prevent the spindle from falling, it is recommended to record the original installation position of the spindle before disassembling. Then loosen the coupling screws on the CNC spindle.
Remove the spindle screws: Loosen the screws on the spindle in diagonal order and use bolts to push the spindle out. Pay attention to prevent the spindle from falling suddenly during operation.
Clean the oil in the sleeve: After the spindle is disassembled, be sure to clean the oil in the sleeve to ensure that there will be no poor fit due to dirt when reinstalling.
Install the spindle
After the disassembly is completed, it is also critical to install the spindle correctly. The following are the detailed steps for installing the spindle:
Apply anti-rust lubricant: Apply a layer of lubricant inside the new spindle and sleeve to prevent rust. Then, the spindle is installed, paying attention to the installation position recorded during disassembly.
Connect the air pipe, water pipe, and power cord: Follow the reverse order of disassembling the spindle and connect the air pipe, water pipe, and power cord.
Measure the spindle extension length: On some machine tools, it is necessary to measure the position of the spindle when changing the tool, that is, the axial extension length of the spindle from clamping to loosening. The spindle extension length is related to the thickness of the gasket. The thinner the thickness, the longer the spindle extension length, and vice versa. Under normal circumstances, the spindle extension length should be around 0.5mm and cannot exceed 0.8mm.
Tighten the coupling: Tighten the coupling to ensure the coupling runout range is between 0.01 and 0.02 mm.
Measuring the spindle accuracy
After installation, the spindle accuracy must be measured to ensure its stability and reliability at work.
Measuring the runout of the front end of the spindle: Insert the toolbar into the spindle, clamp it, and use the dial indicator to measure the runout of the front end of the spindle.
Measuring the runout of the rear end of the spindle: Also measure the runout of the rear end of the spindle to ensure that it is within the allowable range.
Measure the central axis of the spindle: Measure the central axis and side axis of the spindle to ensure that the accuracy range is within 0.05mm to meet the processing requirements.
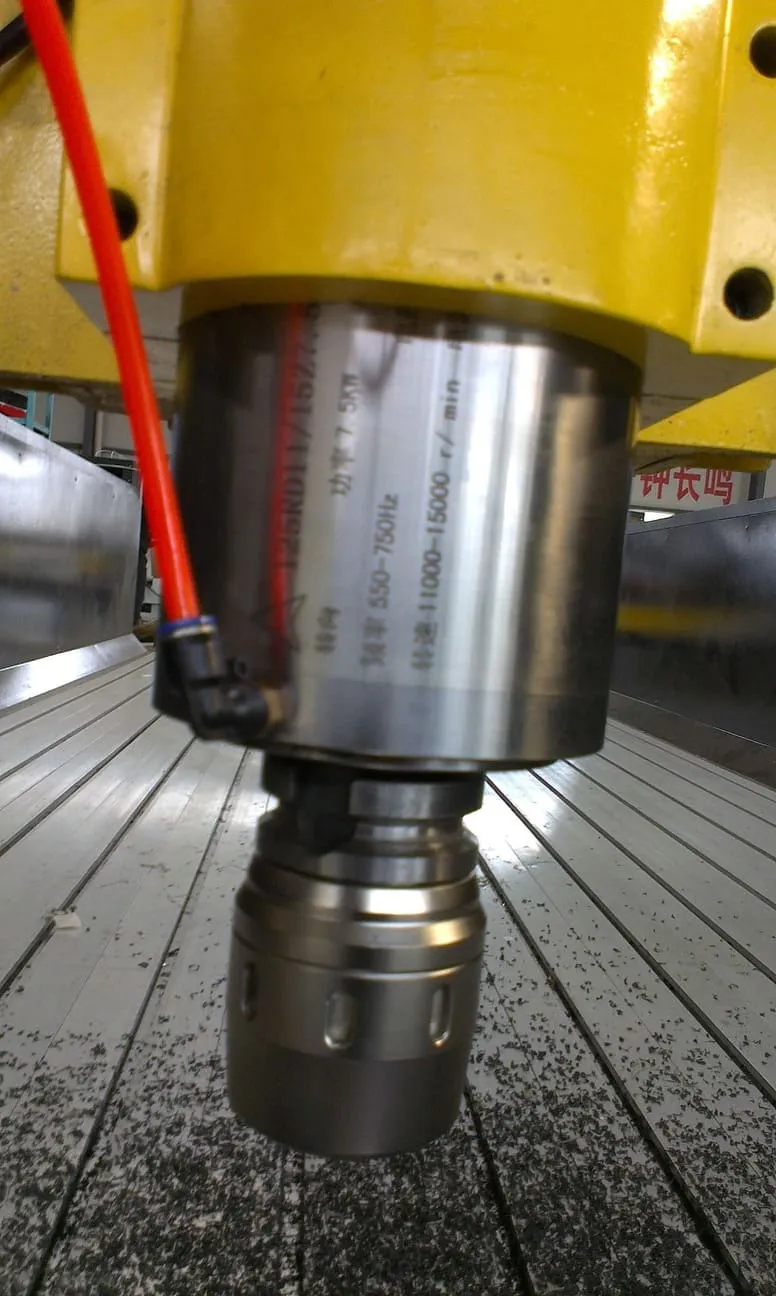
Conclusion
The correct disassembly, assembly steps, and precision measurement can ensure the regular operation and long-term use of the CNC spindle. Regular maintenance and accurate operation can improve the equipment’s working efficiency and avoid equipment damage caused by improper operation. Keeping the above steps in mind can help the operator to be more handy when disassembling the CNC spindle.
Summary FAQ based on the article
1. Why must you record the original installation position when disassembling the spindle?
Recording the original installation position of the spindle ensures that the position of the spindle can be accurately restored when reinstalled to avoid operation problems caused by installation deviation.
2. Why do you need to clean the oil in the sleeve after the spindle is disassembled?
Cleaning the oil in the sleeve can prevent the dirt from affecting the fit between the spindle and the sleeve during reinstallation, thereby ensuring the quality of installation and the stability of the spindle operation.
3. Why is it important to measure the spindle extension length?
The spindle extension length directly affects the position accuracy during tool change. Accurate measurement can ensure the stability and accuracy of the spindle during processing and avoid processing errors.
4. What precision measurements are required after the spindle is installed?
After the spindle is installed, the front and rear runout of the spindle and the accuracy of the central and side busbar need to be measured to ensure that they meet the processing requirements.
5. How to ensure that the runout range of the coupling is within the allowable range?
By tightening the coupling and using precision measuring tools such as a micrometer, measure the runout range of the coupling to ensure that it is between 0.01 and 0.02 mm, thereby ensuring the smooth operation of the spindle.
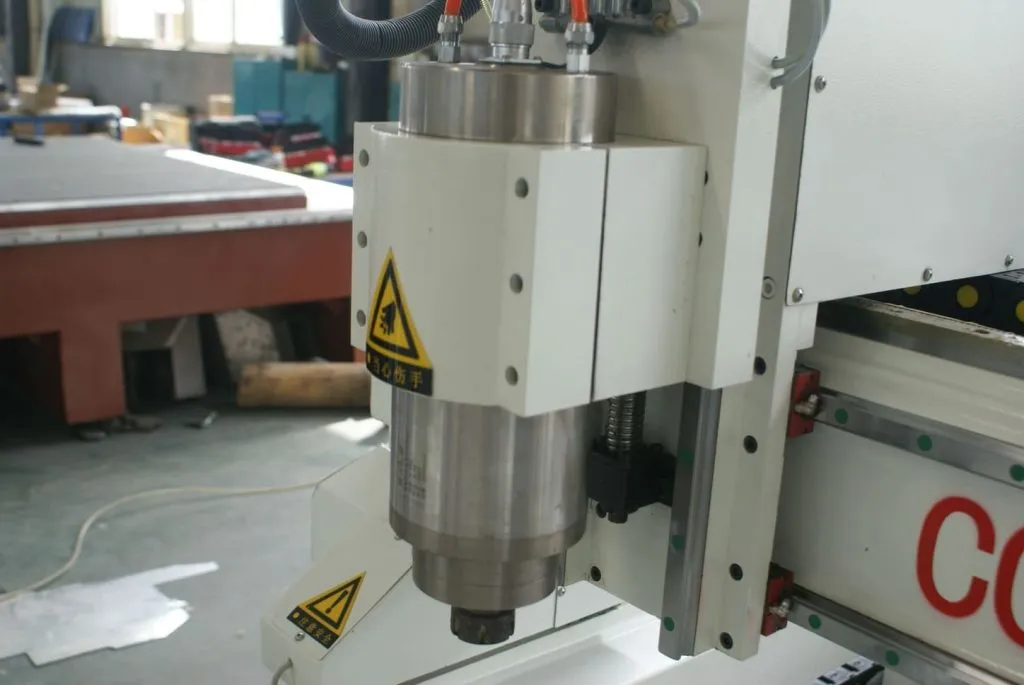
- RicoCNC has a team of professionals who have been engaged in the design, production, sales, and maintenance of electro spindles for many years. Our company accepts the purchase of various types of CNC spindles.
water-cooled CNC spindle motors
Edge banding machine spindle motors.
- If you need any CNC spindle, please contact us.