Learning how to run a CNC milling machine can be a fulfilling journey, especially if you’re interested in the intricacies of modern manufacturing. CNC milling machines are among the most common tools in the manufacturing industry, and understanding their operation can significantly increase your value as a machinist or engineer. This guide will walk you through the essential steps, skills, and best practices for running a CNC milling machine, making it accessible to beginners and experts alike.
Understanding CNC Milling
What is CNC Milling?
CNC Milling stands for Computer Numerical Control Milling, a process used to cut, shape, and engrave various materials into precise designs. Unlike manual milling, CNC milling relies on computer programs to control machinery and produce complex parts with high precision.
- Automation: CNC milling uses G-code to direct the machine’s movements, eliminating the need for manual intervention.
- Versatility: It can work with a wide range of materials, including metals, plastics, and wood, making it ideal for many industries like automotive, aerospace, and electronics.
If you want to understand how spindles contribute to precision in CNC milling, you might find our CNC Spindle Motors page helpful. This page provides more information about the types of spindle motors that are crucial in CNC operations.
Importance of CNC Milling in Modern Manufacturing
The use of CNC milling machines is essential in modern production lines for several reasons. These machines allow for high-speed and high-precision manufacturing, leading to consistent and repeatable results, which is critical for industries that need flawless production.
- Precision: CNC milling machines can achieve precise tolerances, often up to fractions of a millimeter.
- Productivity: Automated processes lead to quicker production runs and allow for larger volumes, without sacrificing quality.
Basic Parts of a CNC Milling Machine
The Structure of a CNC Milling Machine
To operate a CNC milling machine, it’s important to understand its key components. A typical machine consists of the following parts:
- Spindle: The component that rotates the cutting tool. The spindle motor determines the speed and efficiency of milling.
- Table: The surface on which the workpiece is clamped. The CNC table moves in coordination with the spindle to perform precise cuts.
- Control Panel: This is where you input the program that directs the machine. It includes a display screen, keyboard, and emergency stop button for safety.
Milling Tools
CNC milling machines use a wide range of tools for different operations, including:
- End Mills: Used for cutting and shaping materials.
- Face Mills: Ideal for creating a flat surface on the material.
- Ball Nose Cutters: Best for making curved surfaces and contours.
Tool Type | Best Application |
---|---|
End Mill | Cutting and Shaping |
Face Mill | Creating Flat Surfaces |
Ball Nose Cutter | Curved Surfaces and Contours |
For a deeper understanding of how different CNC spindles can optimize milling machine performance, take a look at our CNC Router Spindles page.
Steps to Run a CNC Milling Machine
Step 1: Set Up the Machine
Securing the Workpiece
The first step is to secure the workpiece onto the CNC table. Proper clamping is essential because even slight movements can ruin precision.
- Vise or Clamps: Use either a vise or a set of clamps to secure the material.
- Alignment: Make sure the workpiece is aligned correctly with the X, Y, and Z axes of the machine to ensure proper orientation during the milling process.
Loading the Program
The next step is to load the appropriate program into the control panel. CNC milling machines operate using G-code, which is a series of commands that tells the machine what to do.
- Choose Your G-code File: Load the appropriate G-code file from a USB drive or directly from your computer.
- Verify the Coordinates: Before running the program, it’s crucial to verify that the coordinates are set correctly to avoid mistakes.
Step 2: Set Up the Tools
Tool Selection and Loading
After securing the workpiece and loading the program, it’s time to load the correct cutting tools into the spindle.
- Select Tools Based on Material: Different materials require different types of tools. For example, hard metals need specialized carbide tools.
- Tool Calibration: Always calibrate the tools to make sure they are set at the correct depth and position.
Zeroing the Machine
Zeroing the machine involves calibrating the X, Y, and Z axes to their starting points. This is essential to ensure the machine knows where to begin the milling process.
- Set Zero for All Axes: The zero point serves as the reference for all subsequent operations. Use a touch probe or manually jog the machine to the correct position to set zero.
- Test Run: Always run a test to ensure the machine and tools are correctly set up before full-scale operation.
Step 3: Execute the Milling Operation
Running the G-code Program
Once everything is set up, you can execute the G-code program. Start the operation by pressing the start button on the control panel.
- Monitor the Process: Keep an eye on the machine to watch for any errors or unusual noises that might indicate a problem.
- Emergency Stop: Always be prepared to use the emergency stop button if something goes wrong.
Adjustments During Milling
Sometimes, the machine needs adjustments during the milling operation. This might include changes to spindle speed, feed rate, or tool path to improve accuracy or to respond to material inconsistencies.
- Spindle Speed: Adjusting spindle speed can help achieve smoother finishes or prevent overheating.
- Feed Rate: A lower feed rate can yield more precision, whereas a higher feed rate is used for rapid material removal.
Safety Considerations When Running a CNC Milling Machine
Personal Protective Equipment (PPE)
Safety is of utmost importance when running a CNC milling machine. Always use appropriate PPE, which typically includes:
- Safety Glasses: To protect eyes from flying chips.
- Gloves: To handle sharp materials safely.
- Hearing Protection: Milling can be noisy, and ear protection helps in environments with extended exposure.
Emergency Procedures
The control panel features an emergency stop button, which should be easily accessible at all times. Familiarize yourself with the emergency procedures to stop the machine quickly if needed.
- Machine Guarding: Ensure that all safety guards are in place before beginning the operation.
- Regular Inspections: Regularly inspect the machine and tools for wear and tear to prevent accidents.
Optimizing CNC Milling Performance
Choosing the Right Spindle
The spindle motor plays a critical role in the overall performance of a CNC milling machine. Different spindles have varying RPMs and torque, which can impact the precision and speed of the milling operation.
- Air-Cooled Spindles: Ideal for short, intermittent milling jobs.
- Water-Cooled Spindles: Better for extended milling operations, as they stay cool and maintain consistent performance.
You can find more detailed information about different types of spindles on our CNC Spindle Options page.
Tool Path Optimization
One way to improve the performance of your CNC milling machine is through tool path optimization. Optimized tool paths reduce machining time and improve the finish quality of the workpiece.
- CAM Software: Use CAM (Computer-Aided Manufacturing) software to create optimized tool paths.
- Efficient Moves: Avoid unnecessary moves that can waste time and reduce the life of the cutting tool.
Regular Maintenance
Regular maintenance is essential for keeping the CNC milling machine in peak condition.
- Lubrication: Ensure that all moving parts are adequately lubricated to reduce friction and wear.
- Tool Inspection: Inspect cutting tools for wear regularly and replace them if necessary.
Advanced Tips for CNC Milling
Utilizing Advanced CNC Features
Most modern CNC milling machines come with advanced features like probing systems, automatic tool changers (ATC), and high-speed machining capabilities.
- Automatic Tool Changer: Speeds up operations by quickly switching between different tools.
- Probing Systems: Useful for setting up the workpiece and performing in-process measurements to improve accuracy.
CAM Software Integration
To take your CNC milling to the next level, integrating CAM software is almost indispensable. Programs like Fusion 360 and MasterCAM provide you with the ability to simulate milling operations, thus reducing the chances of error.
- Simulation Tools: These allow you to visualize the entire milling operation before making actual cuts, minimizing the risk of errors.
- Adaptive Tool Paths: CAM software can also create adaptive tool paths that increase efficiency by maximizing material removal rates.
Monitoring Spindle Health
The spindle is one of the most critical components in any CNC milling machine, and maintaining its health ensures both productivity and quality.
- Vibration Analysis: Monitor spindle vibrations to detect imbalances that could affect the machining quality.
- Temperature Monitoring: Excess heat can be detrimental to the spindle, especially during extended milling operations.
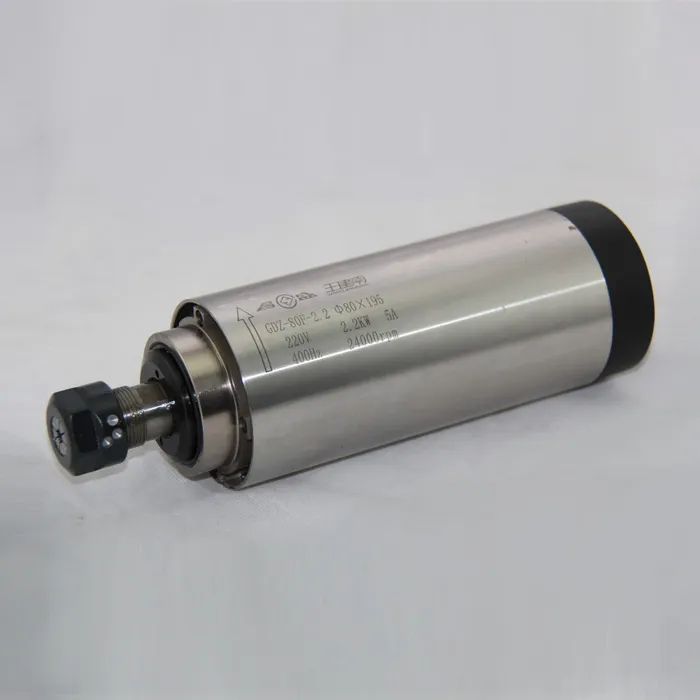
Frequently Asked Questions
1. What are the essential steps to set up a CNC milling machine?
Setting up a CNC milling machine involves securing the workpiece, loading the G-code program, selecting and calibrating tools, and zeroing the axes.
2. How can I optimize the speed of my CNC milling machine?
Optimizing the speed involves selecting the right spindle motor, adjusting feed rates, and using optimized tool paths designed by CAM software.
3. Why is spindle maintenance important in CNC milling?
Spindle maintenance ensures that your CNC milling machine operates efficiently, reduces downtime, and maintains precision by preventing spindle overheating or imbalances.
4. Is it necessary to know G-code to operate a CNC milling machine?
While basic knowledge of G-code is beneficial for troubleshooting, many machines today use user-friendly interfaces that make it easier for operators to work without in-depth G-code knowledge.
5. How often should I perform maintenance on a CNC milling machine?
Regular maintenance, such as lubrication and tool inspection, should be carried out weekly, while more extensive checks should be done monthly.
Conclusion
Operating a CNC milling machine can seem challenging at first, but with the right knowledge, tools, and practices, it becomes a rewarding skill that opens doors to numerous career opportunities. From learning the basics of G-code to understanding spindle selection and tool calibration, every step in the process is crucial for achieving precision and efficiency. With advancements in technology, integrating features like CAM software and automatic tool changers makes the process even more streamlined. To learn more about essential tools and get high-quality CNC spindles that enhance your milling machine’s performance, be sure to explore our CNC Spindle Options. Becoming proficient in CNC milling is not just about operating a machine; it’s about mastering a blend of technology, precision, and creativity.