How to Set Up a CNC Lathe
Setting up a CNC lathe can seem like a daunting task for beginners, but once you break it down into simple steps, it becomes much easier to understand. Whether you’re a machinist just getting started, or an experienced operator looking to streamline your workflow, properly setting up your CNC lathe is the foundation for efficient, precise, and productive work. This article provides a comprehensive guide on how to set up a CNC lathe, including crucial tips and insights to help you maximize efficiency.
Understanding the CNC Lathe Machine
A CNC lathe is a type of machine that cuts, drills, and shapes materials, usually metal or plastic, with a rotating spindle while a cutting tool moves along the material. CNC, which stands for Computer Numerical Control, automates this process using precise control systems. This type of machine is widely used in manufacturing due to its precision and ability to work with complex geometries.
Components of a CNC Lathe
Before diving into the setup process, it’s essential to understand the major components of a CNC lathe machine:
- Spindle: The spindle holds and rotates the workpiece.
- Chuck: This part grips the workpiece, holding it securely in place.
- Tool Turret: Holds multiple tools that the machine switches between during operations.
- Tailstock: Provides additional support to the workpiece during machining.
- Control Panel: The interface where the operator inputs the necessary commands.
The Importance of Proper Setup
Setting up a CNC lathe is crucial for efficient machining and to ensure the safety of both the operator and the machine. Incorrect setup can lead to tool damage, part defects, or even machine crashes. It also affects the quality of the finished product, directly impacting surface finish, dimensional accuracy, and production speed.
Discover our selection of CNC Spindle Motors for various machining needs.
Step-by-Step Guide to CNC Lathe Setup
The process of setting up a CNC lathe involves several steps, from preparing the machine to configuring the software. Let’s explore these steps in detail:
1. Preparing the Machine
Preparation is key. Start by inspecting the CNC lathe to ensure it’s in good working order. Clean any residual material from previous jobs and confirm that all parts are properly lubricated. Also, make sure the work area is clean and free of obstructions.
- Check Machine Calibration: Verify the calibration of the machine. This ensures that the tools and spindle are aligned and ready for precision work.
- Lubrication: Proper lubrication of moving parts is vital. Refer to the machine’s manual for lubrication points and frequency.
- Tool Inspection: Check the tools in the turret for any wear or damage. Worn-out tools can compromise the quality of the finished product.
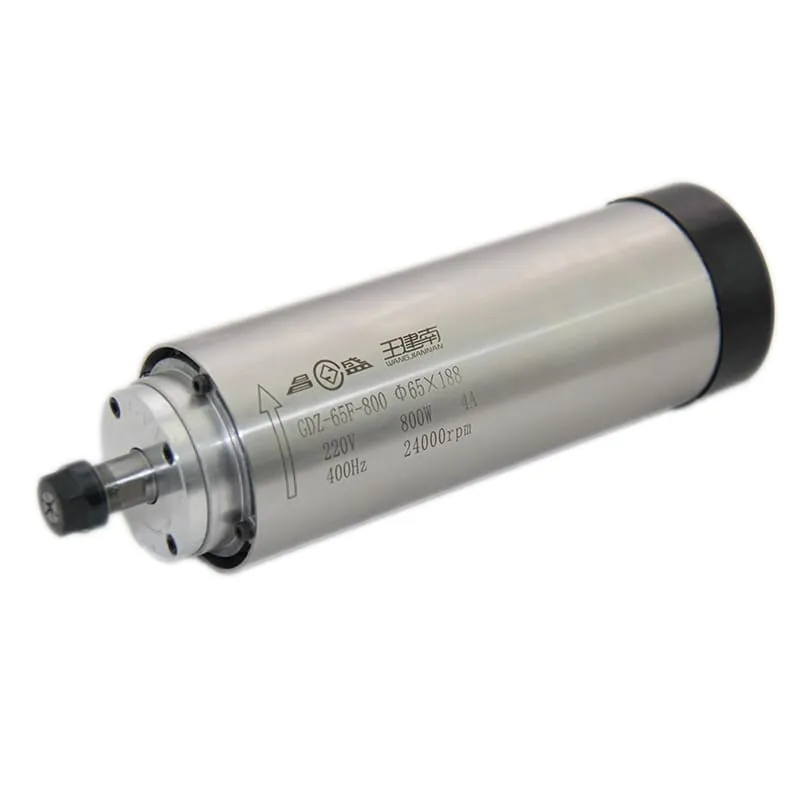
For accurate and smooth operations, consider using a high-quality spindle like our 800W ER11 Air-Cooled Spindle.
2. Mounting the Workpiece
The workpiece must be mounted securely in the chuck. The chuck grips the material, ensuring stability during the machining process. When mounting the workpiece:
- Select the Right Chuck: Depending on the size and type of material, select a suitable chuck. Three-jaw chucks are versatile for cylindrical parts, while four-jaw chucks provide more customization.
- Centering the Workpiece: Ensure that the workpiece is centered to avoid vibrations during machining. You can use a dial indicator to verify the concentricity.
- Secure Tightening: Make sure the workpiece is tightened securely in the chuck, but avoid over-tightening, which can deform the part.
3. Tool Setup and Calibration
Setting up the tools correctly is vital for accurate machining. The tool turret holds the various cutting tools, and it’s crucial to ensure that each tool is properly calibrated.
- Insert Tools in the Tool Holders: Place the tools in their respective holders, ensuring that each tool is aligned correctly with the spindle.
- Tool Calibration: Use a touch probe or dial indicator to set each tool’s position accurately. Calibration will ensure that the machine knows the exact location of each tool.
- Offset Adjustment: Input the tool offsets into the control panel. Tool offsets determine how far each tool is from the workpiece and help the machine make precise cuts.
4. Loading the CNC Program
A CNC lathe operates based on a G-code program, which tells the machine exactly how to move and cut. Loading the correct program is essential for the desired output.
- Load the Program via Control Panel: Use the control panel to load the G-code file, either from a USB drive or through the network.
- Verify G-Code: Before starting the machining, verify the G-code by running a simulation. This helps in identifying any errors or areas where adjustments may be required.
- Dry Run: Performing a dry run (without cutting) is often a good idea to ensure there are no collisions between the tools and workpiece.
Explore more about setting up your CNC Router Spindle here.
Tips for Effective CNC Lathe Setup
1. Workpiece Material Considerations
Different materials require different machining parameters. For example, aluminum can be machined at higher speeds compared to stainless steel, which requires more conservative settings.
- Adjust Speeds and Feeds: Based on the material type, adjust the spindle speed and feed rate accordingly. This helps to optimize tool life and ensure a good surface finish.
- Coolant Use: Depending on the material, coolant may be required to dissipate heat and improve the cutting performance. Always check if the workpiece material requires coolant.
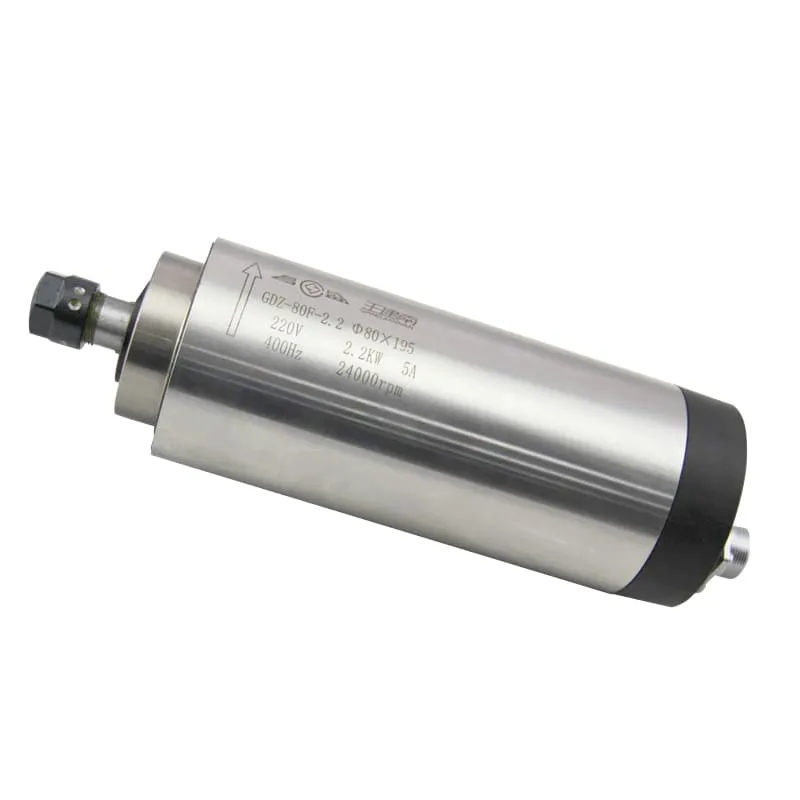
Our 2.2KW ER16 Air-Cooled Spindle is ideal for various materials, providing both versatility and power.
2. Safety Precautions During Setup
Safety should always be a priority during any machine setup:
- Personal Protective Equipment (PPE): Always wear protective gear, including gloves, safety glasses, and steel-toed boots, to avoid injuries.
- Check the Emergency Stop: Ensure the emergency stop button is functioning correctly. This is crucial in case of a malfunction.
- Avoid Loose Clothing: Loose clothing or accessories can get caught in the machine, so always secure anything that could potentially be a hazard.
3. Checking Part Dimensions
Once you’ve run the CNC program, check the first part to ensure all dimensions meet the specifications. Use a micrometer or calipers to measure the dimensions of the machined part.
- First Article Inspection: Perform a thorough inspection of the first part to confirm it matches the desired dimensions. This helps catch any errors early before moving on to mass production.
- Adjust Offsets if Necessary: If the dimensions are off, adjust the tool offsets on the control panel to fine-tune the cuts.
Fine-Tuning and Optimization
Once the initial setup is complete, there may be opportunities to fine-tune the process to achieve better performance. Optimization can include improving tool paths, adjusting speeds and feeds, or even selecting different tools for a better finish.
1. Tool Path Optimization
The efficiency of a CNC lathe can often be enhanced by optimizing the tool path. A good tool path minimizes air cutting time and improves the overall cycle time.
- Software Simulation: Use CNC simulation software to determine the most efficient tool path. This helps in identifying areas where you can reduce cycle times without compromising on quality.
- Reduce Air Time: Focus on reducing air time—moments where the tool is moving without cutting material. Shorter air time directly correlates with increased productivity.
2. Using the Right Spindle for Efficiency
The choice of spindle significantly impacts the quality and efficiency of machining. Different CNC spindle motors have varied specifications, such as torque and RPM, which should be selected based on the material and complexity of the task.
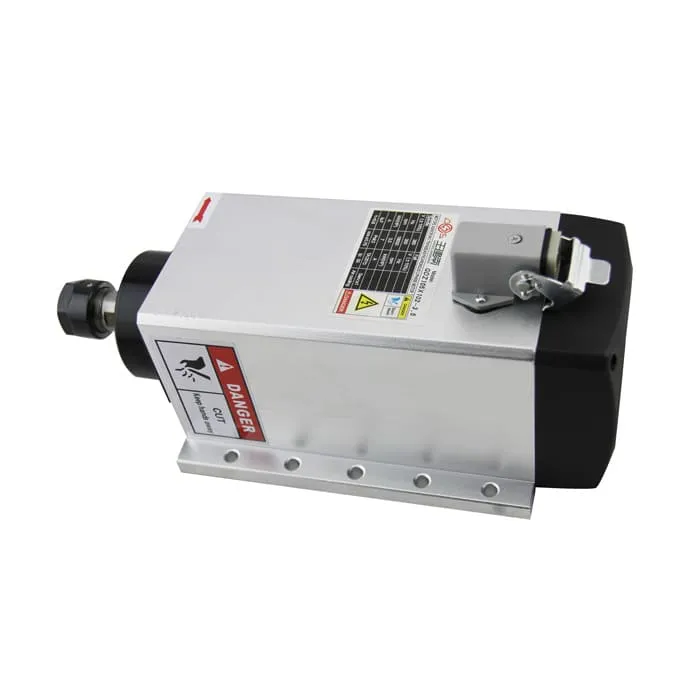
For high-performance CNC operations, consider using our 3.5KW ER20 Air-Cooled Spindle, which offers excellent efficiency and precision.
Conclusion: Mastering CNC Lathe Setup
Setting up a CNC lathe may initially seem complicated, but with careful attention to each step, it becomes a manageable and rewarding process. A successful setup involves preparation, secure workpiece mounting, accurate tool calibration, proper program loading, and careful inspection of finished parts. By following these steps and considering additional optimization techniques, you can achieve efficient and high-quality results.
CNC lathes are powerful tools that, when set up correctly, can produce incredibly precise and complex parts. If you’re ready to enhance your setup or require more information on the best spindle motors for your machine, explore our extensive CNC spindle selection.
FAQs
1. What is the first step in setting up a CNC lathe?
The first step is preparing the machine. This includes inspecting the CNC lathe, ensuring it is properly lubricated, and verifying machine calibration.
2. How do I ensure the workpiece is mounted correctly?
Make sure to select the right chuck, center the workpiece accurately, and secure it firmly to prevent any movement during machining.
3. Why is tool calibration important in CNC lathe setup?
Tool calibration ensures that the machine knows the exact position of each tool, which is crucial for accurate and precise cuts.
4. How can I optimize CNC lathe setup for better efficiency?
You can optimize setup by adjusting the tool path to reduce air time, using suitable speeds and feeds for the material, and selecting the right spindle for your machine.
5. What safety precautions should be followed during CNC lathe setup?
Always wear appropriate PPE, check that the emergency stop button is functional, and avoid wearing loose clothing that could get caught in the machine.