CNC machines are some of the most versatile and efficient tools in the world of manufacturing, allowing operators to create complex shapes and designs with incredible precision. If you’re new to CNC machines and wondering how to use a CNC machine, this guide is designed to provide you with everything you need to get started, from the fundamentals of CNC technology to the specifics of tool selection and machine operation. Let’s break it down step by step so that by the end of this article, you’ll have a good understanding of how to operate a CNC machine and execute projects with confidence.
What is a CNC Machine?
Understanding CNC Machines
A CNC (Computer Numerical Control) machine is a tool used for cutting, shaping, and drilling materials by following pre-programmed commands. CNC machines automate the movement of various cutting tools, such as end mills, routers, and lathes, which makes it possible to produce complex parts with high accuracy.
The primary benefit of CNC machines is their ability to reproduce precise results across multiple runs. Whether you are making 3D shapes out of wood, metal, or plastic, CNC machines ensure each part meets exact specifications.
Key Components of a CNC Machine
To effectively use a CNC machine, it is important to understand the main components:
- Control Panel: Where you input and control your programs.
- Spindle: Holds the cutting tool and rotates at various speeds to cut the material.
- Cutting Tools: These include end mills, drills, and routers used to shape the material.
- Work Table: The surface where the material is clamped for machining.
- Axes (X, Y, Z): These determine the directions in which the cutting tool moves. More advanced CNC machines may have additional axes for more complex operations.
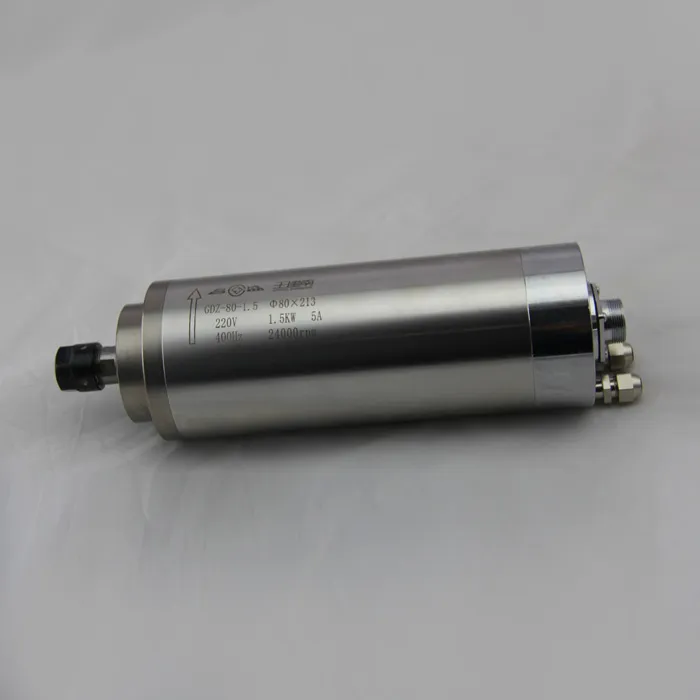
Using a quality spindle like the 24000RPM 1.5KW ER16 Water-Cooled Spindle helps ensure consistent cutting performance, which is essential for both beginners and experienced operators.
Setting Up Your CNC Machine
1. Prepare Your Workspace
Before operating your CNC machine, it’s crucial to prepare your workspace. Make sure you have:
- Adequate Space: Ensure that the CNC machine is placed in an area that allows free movement around it.
- Safety Gear: Wear protective glasses and gloves, as CNC operations often involve flying debris and sharp tools.
- Stable Surface: The CNC machine should be placed on a stable workbench to minimize vibrations.
2. Install the Cutting Tool
The cutting tool you choose will depend on the material and type of job. Most CNC routers require end mills or router bits for cutting and shaping.
- End Mills: Perfect for a variety of materials, ranging from wood to metal.
- Router Bits: Best suited for woodworking projects.
Tip: Use the middle mouse button to adjust the positioning of the tool in many software programs, ensuring the tool is aligned correctly before running the CNC machine.
3. Secure the Workpiece
To get a good outcome, the workpiece must be securely clamped to the worktable. Loose material can shift, which can ruin the project or damage the machine.
- Vices or Clamps: Use these to keep the material firmly in place.
- Double-Sided Tape: Sometimes used for lightweight or delicate materials.
CNC Machine Software and Programming
1. CAD/CAM Software
Using CAD (Computer-Aided Design) and CAM (Computer-Aided Manufacturing) software is an essential part of the CNC machining process. These tools allow you to design parts and convert those designs into a language that the CNC machine can understand, known as G-code.
- Fusion 360: One of the most popular software programs, suitable for beginners and professionals.
- Mastercam: Known for its advanced capabilities, but a bit more complex for beginners.
2. Writing G-Code
G-code is the programming language that controls CNC machines. It tells the machine where to move, how fast, and what path to follow. For beginners, you can start with basic commands:
- G00: Rapid movement of the cutting tool.
- G01: Linear cutting movement.
- G02/G03: Circular interpolation (clockwise and counterclockwise).
3. Uploading and Running the Program
After writing or generating your G-code, you need to upload it to the CNC machine via the control panel or through USB. Once uploaded, make sure to simulate the process using software to catch any potential issues before cutting the actual material.
Step-by-Step Machining Process
1. Run a Test Cut
Running a test or dry run allows you to observe the movement of the CNC machine without cutting into the material. This helps you check if the toolpaths are correct and ensures no unexpected collisions.
- Simulate the Process: Use your CNC software to simulate the movement before actually cutting.
- Z-Axis Height Check: Make sure the height of the cutting tool is correct.
2. Perform the First Cut
Once the test cut is successful, begin the actual cutting process. Observe the CNC machine carefully to ensure:
- The cutting depth is correct.
- The tool is not overheating or wearing out too quickly.
- The workpiece remains firmly clamped.
3. Coolant and Lubrication
Using coolants helps to keep the tool from overheating, especially when working with metals. Different materials may require specific cooling solutions, so always consult the material manual.
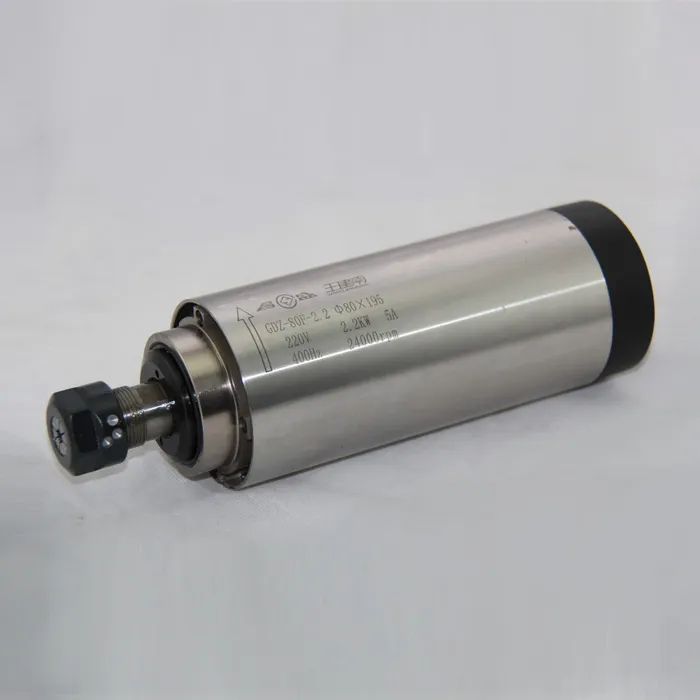
The 2.2KW ER20 Air-Cooled Spindle is an excellent option for keeping the tool cool during intense machining operations, especially when working with harder materials.
Types of CNC Machines and Their Uses
1. CNC Router Machines
CNC routers are commonly used for cutting wood, plastic, and soft metals. They are versatile and ideal for sign-making, furniture production, and even 3D carvings.
- Beginner-Friendly: Great for hobbyists and beginners looking to start projects in woodworking.
- Key Tools: Router bits, V-bits, and end mills are used to create intricate designs.
2. CNC Milling Machines
CNC milling machines are used for cutting and shaping harder materials like metals. They use rotating tools to remove material and produce components that require high precision.
- 3-Axis Milling: Moves in X, Y, Z directions for flexibility in cutting.
- 5-Axis Milling: Provides more angles, ideal for producing complex parts like aerospace components.
3. CNC Lathes
CNC lathes are ideal for creating cylindrical parts, such as shafts, bushings, and fittings. They rotate the workpiece around a central axis while applying a cutting tool to shape it.
- Applications: Used heavily in automotive and aerospace industries for precision parts.
- Tools Required: Boring bars, drill bits, and threading tools.
Safety Tips When Operating a CNC Machine
1. Always Wear Protective Gear
Safety gear is essential when working with CNC machines. Wear safety goggles, gloves, and hearing protection to avoid injury.
2. Keep Your Hands Away
Never reach into the cutting area while the machine is operating. Even if the machine seems to be at a safe distance, unexpected movements can lead to serious injuries.
3. Avoid Loose Clothing
Loose clothing or jewelry can easily get caught in a CNC machine, leading to dangerous situations. Always secure long hair and avoid wearing loose items.