Is a CNC Machine Worth It?
The question of whether investing in a CNC machine is worth it is one that many small business owners, hobbyists, and even large manufacturers often ponder. In an era where precision, efficiency, and quality are paramount, CNC machines have become increasingly essential in a variety of industries. From woodworking to metal fabrication, CNC machines promise accuracy, productivity, and the ability to create intricate parts that are otherwise impossible or too costly to manufacture by hand. But is it really worth the investment? Let’s dive into the benefits, costs, and various aspects that determine whether a CNC machine is a valuable addition to your workshop.
What is a CNC Machine?
A CNC machine—which stands for Computer Numerical Control—is a machine that is guided by computers to execute tasks involving cutting, milling, drilling, or any other manufacturing operation. The unique advantage of a CNC machine is its automated control over tools, allowing for extremely precise operations without the need for human intervention after programming. CNC machines can work with various materials such as wood, metal, plastic, and even foam.
The typical components of a CNC machine include:
- Controller: Acts as the brain of the machine and interprets G-code.
- Spindle: The cutting tool that moves to execute the cutting or milling action.
- Table: Where the workpiece is secured.
- Axes: Different axes (X, Y, Z) that determine the direction of the tool movement.
A CNC machine can offer a significant boost in productivity because it reduces the time needed for repetitive tasks and increases consistency in the production of parts. For a more in-depth look at CNC spindle motors, consider exploring options like the 2.2KW ER25 Square Air-Cooled Spindle. This spindle type is ideal for those looking to balance power with precision in their cutting operations.
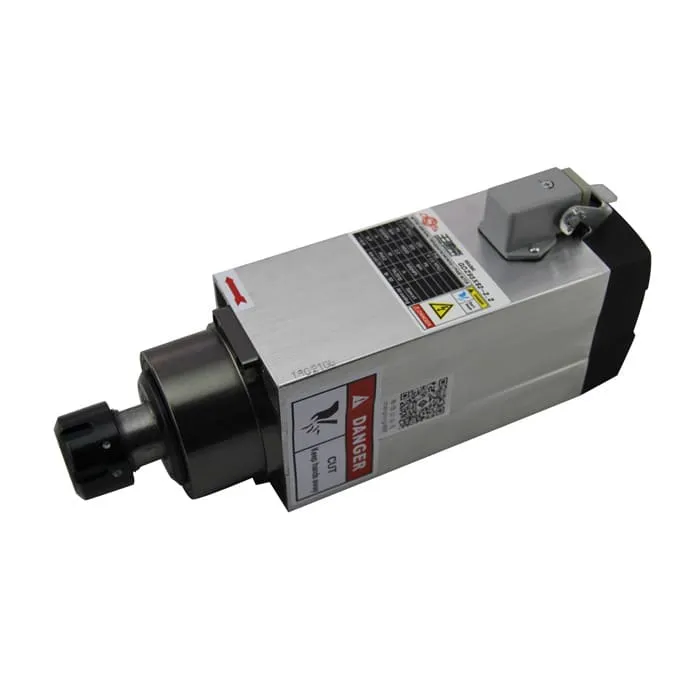
Types of CNC Machines
CNC machines come in various forms, each designed to perform specific functions. Here are some of the most popular types:
1. CNC Router
A CNC router is typically used for woodworking, plastic cutting, and light metalworking. It is perfect for projects that require precision and intricate details, such as creating signs or furniture components.
- Pros: High precision, suitable for softer materials like wood and plastics.
- Cons: Not ideal for heavy metal cutting.
2. CNC Milling Machine
A CNC milling machine is used to cut metal, wood, or other solid materials. It operates by moving both the table and the tool simultaneously to achieve intricate designs and cuts.
- Pros: Ideal for metalworking, capable of making complex parts.
- Cons: Can be expensive and requires a significant learning curve.
3. CNC Plasma Cutter
This machine uses a plasma torch to cut through electrically conductive materials. It’s mainly used for metal fabrication and is especially effective for sheet metal projects.
- Pros: Cuts through thick metal with ease.
- Cons: Requires proper ventilation due to fumes.
For those interested in a powerful spindle for various CNC machines, the 4.5KW ER32 Air-Cooled Spindle is a great choice for more demanding projects.
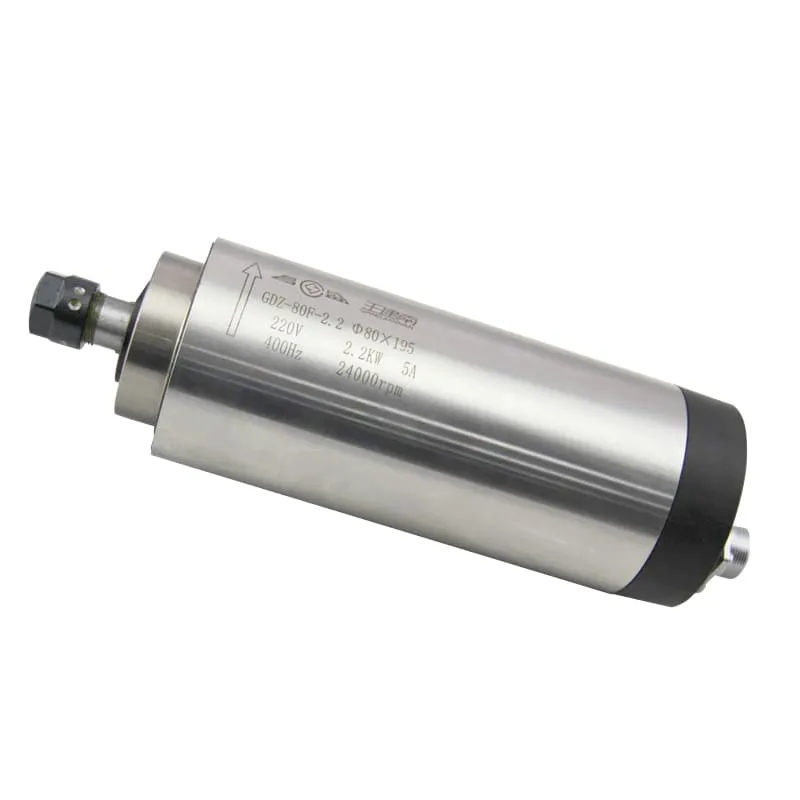
Benefits of Using a CNC Machine
Investing in a CNC machine can offer numerous benefits that may justify the cost. Here are some of the key advantages:
1. Precision and Consistency
One of the most significant benefits of CNC machines is their ability to produce highly accurate and consistent parts. Human error is significantly minimized, making CNC machining particularly useful for projects requiring tight tolerances.
- Repeatability: Once a program is set, the machine can produce identical parts without variation.
- Accuracy: CNC machines can achieve accuracies down to a fraction of a millimeter, making them ideal for precision components.
2. Efficiency
CNC machines drastically reduce production times by automating tasks. What might take a skilled artisan hours to carve by hand can be done in minutes by a CNC machine. This is particularly advantageous for small businesses that want to scale production.
- Multi-Tasking: CNC machines can perform multiple types of operations, from cutting to drilling, in a single run, increasing efficiency.
- High Speed: The machines can operate at high speeds, translating into increased productivity.
3. Cost-Effectiveness Over Time
Though the initial investment in a CNC machine can be considerable, it often pays off in the long run. By reducing labor costs and minimizing material wastage, the overall return on investment can be substantial.
- Reduced Labor Costs: Once the machine is set up, minimal supervision is required.
- Minimized Waste: CNC machines are efficient in material usage, reducing scrap and unnecessary wastage.
For increased precision and efficiency, the 3.5KW ER25 Air-Cooled Spindle is an excellent choice for those aiming for a balance between power and control.
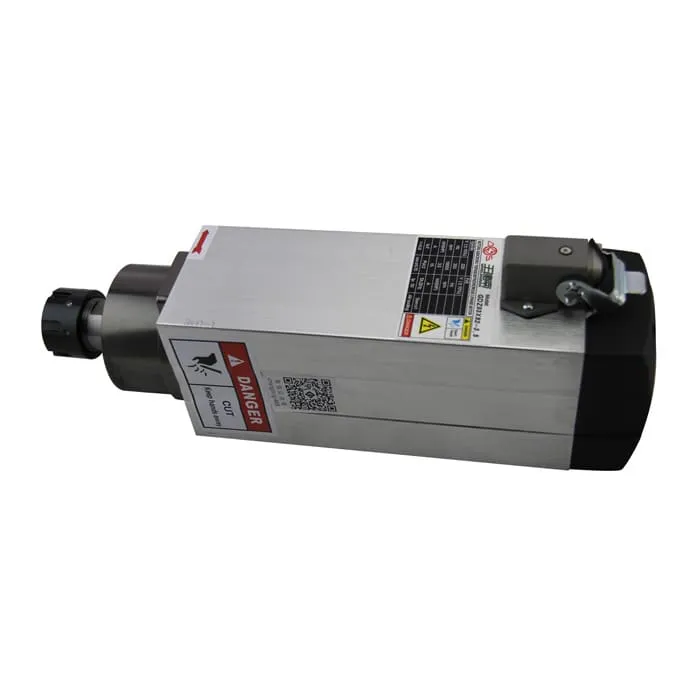
Factors to Consider Before Buying a CNC Machine
1. Cost vs. Budget
The cost of a CNC machine can range from a few thousand dollars to over a hundred thousand, depending on the type and features. It’s crucial to evaluate your budget and compare it with the expected benefits.
- Entry-Level: Basic CNC routers for woodworking can start at around $2,000.
- Industrial Level: Advanced CNC milling machines can cost $50,000 or more.
2. Application Type
Identify the type of work you intend to do with the CNC machine. For hobbyists, a small CNC router may suffice. However, for a metalworking business, an industrial-grade CNC mill might be necessary.
- Woodworking: CNC routers are perfect for wood projects.
- Metalworking: A CNC milling machine is better suited for tougher materials.
3. Space Requirements
CNC machines vary in size. Ensure you have enough space to accommodate the machine and any accessories you may need, such as cooling systems or dust extractors.
- Small Workshops: Compact CNC routers are ideal.
- Larger Manufacturing Spaces: Industrial CNC mills require ample room.
Costs Associated with CNC Machines
While the initial cost of a CNC machine is a significant consideration, there are additional costs associated with owning and operating one:
1. Tooling and Accessories
CNC machines require specialized tooling to perform various operations. This includes end mills, drill bits, and spindle motors. Tooling costs can add up, especially if your projects require different types of tools.
- Spindle Motors: Spindles are crucial components, and choosing the right one is important. For example, the 1.5KW ER11 Round Air-Cooled Spindle offers a good balance of power for smaller CNC routers.
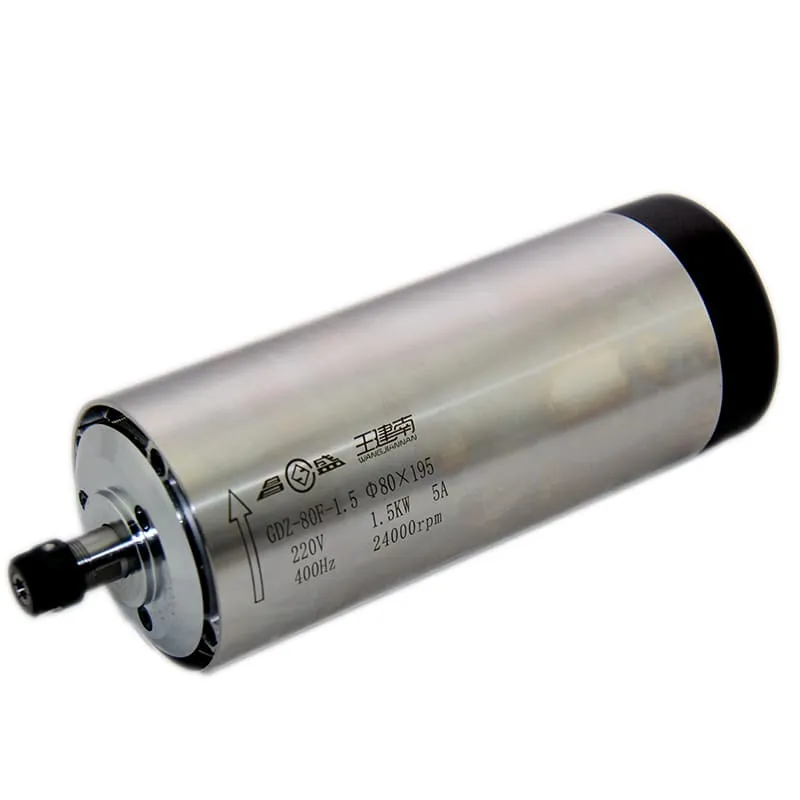
2. Maintenance Costs
Regular maintenance is essential for keeping a CNC machine in good working order. This includes lubrication, cleaning, and occasional part replacements.
- Hydraulic Systems: If your CNC machine uses hydraulics, these systems require periodic inspections and servicing.
- Software Updates: CNC software must be updated regularly to ensure smooth and efficient operation.
3. Training and Skill Development
Operating a CNC machine isn’t as simple as flipping a switch. It requires knowledge of G-code, the programming language used to control the machine, as well as the CAD/CAM software used to design parts.
- Training Courses: Investing in training is important if you’re new to CNC programming.
- Learning Curve: Be prepared for a learning period where productivity may be lower as you familiarize yourself with the machine.
When is a CNC Machine Worth It?
1. Small Businesses and Startups
For small businesses or startups, the ability to produce parts in-house can be invaluable. A CNC machine allows you to create prototypes, small batches, or even custom orders without relying on third-party suppliers.
- Faster Turnaround: Producing parts in-house cuts down on lead times.
- Customization: Small businesses can easily make modifications to products to meet customer needs.
2. Large-Scale Production
For manufacturers who produce thousands of parts, a CNC machine is invaluable for maintaining consistency and meeting high demand.
- Automated Production: CNC machines can run 24/7, increasing output without the need for constant manual oversight.
- Scalability: The ability to replicate parts precisely makes scaling production simpler.
3. Hobbyists and Tinkerers
For hobbyists, buying a CNC machine may be more about passion than necessity. If you enjoy working with materials like wood or plastic and want to create intricate designs, a CNC router can bring your projects to life.
- Creativity: A CNC router allows hobbyists to work on projects that require intricate detailing.
- Skill Building: Operating a CNC machine teaches valuable skills in CAD/CAM software and programming.
Conclusion
Whether a CNC machine is worth it depends largely on your specific needs, budget, and the type of work you want to accomplish. If you are in an industry that demands precision, scalability, and high repeatability, the benefits far outweigh the costs. While the initial investment may seem steep, the long-term savings in labor, increased efficiency, and the ability to produce custom components justify the expense for many businesses and even some passionate hobbyists.
For more detailed insights and to explore the best spindle options for your CNC machine, visit SpindleMotorShop. They offer a wide range of spindles that cater to different needs, ensuring you get the best performance out of your CNC machine.