CNC machining has transformed the manufacturing industry with its precision, efficiency, and automation. Yet, misconceptions and criticisms arise around CNC that make people question its place and reliability in today’s manufacturing. Is CNC wrong in any way? Or are these criticisms based on myths and misunderstandings? In this comprehensive guide, we’ll explore the common misconceptions surrounding CNC technology, dissect its pros and cons, and understand its role in the future of manufacturing.
What Is CNC and How Does It Work?
CNC Explained
CNC stands for Computer Numerical Control. It refers to the automated control of machining tools (like lathes, mills, and grinders) using a computer. This technology allows the machine to follow pre-programmed instructions to precisely shape and cut materials, ranging from metals to plastics.
- Automation: CNC machines execute a sequence of coded instructions, removing the need for manual intervention.
- Precision: The accuracy of CNC machining is a significant advancement over manual machining, with capabilities to achieve extremely tight tolerances.
- Common Machines: CNC is applied to a variety of tools, including CNC lathes, milling machines, and plasma cutters.
The Process Behind CNC Machining
The CNC process generally involves a few key stages:
- CAD Design: A part is first designed using Computer-Aided Design (CAD) software.
- CAM Programming: The CAD file is then imported into Computer-Aided Manufacturing (CAM) software, where the tool paths are generated.
- Tool Setup: Cutting tools like end mills or drill bits are mounted onto the CNC machine.
- Execution: The program is uploaded to the CNC machine, which performs the machining operation.
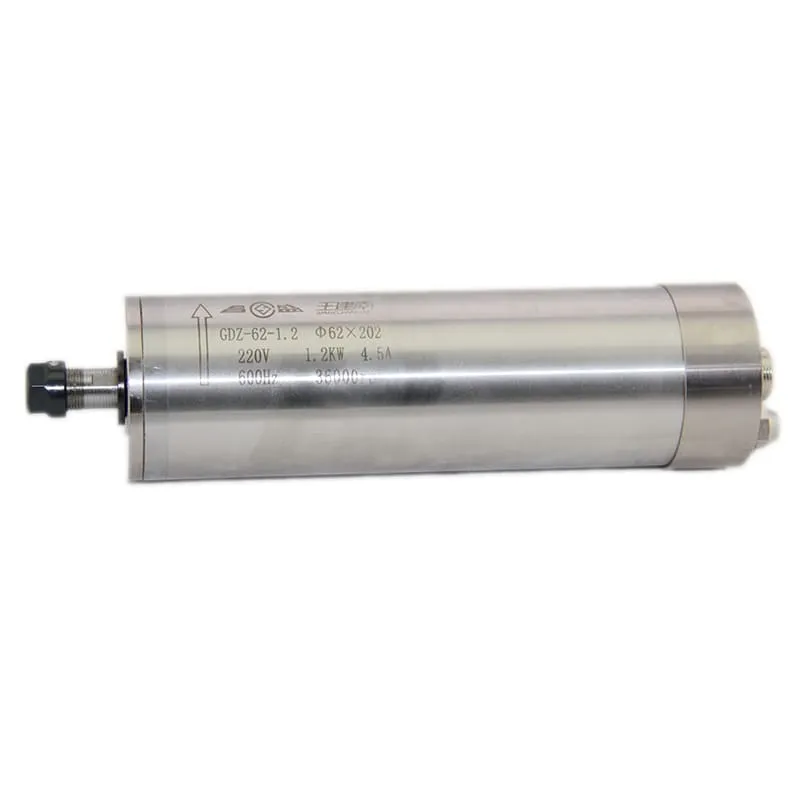
This 60000RPM 1.2KW ER11 Water-Cooled Spindle is a great example of a CNC component used for high-precision machining.
Common Myths and Misconceptions About CNC
1. CNC Machines Are Only for Mass Production
One of the biggest misconceptions is that CNC machines are only suitable for large-scale production. While they are indeed capable of producing thousands of identical parts with remarkable consistency, they are also ideal for prototyping and custom jobs.
- Prototyping: CNC is increasingly used to create prototypes due to its ability to quickly produce high-quality models.
- Customization: Small businesses often use CNC machines for custom orders, such as custom metal or wood engravings.
2. CNC Machines Will Replace All Human Jobs
Another common concern is that CNC machines will eliminate jobs for machinists and craftsmen. However, CNC technology still requires skilled operators and programmers. The role of machinists is evolving rather than disappearing.
- CNC Operators: Skilled workers are needed to set up, program, and maintain these machines.
- Design and Quality Control: Human involvement is crucial in the design phase and quality control of CNC parts.
3. CNC Is Always Expensive
While it’s true that the initial cost of a CNC machine can be high, the return on investment often outweighs these costs in terms of efficiency, precision, and reduced waste.
- Renting Options: Renting CNC machines is also a viable option, offering access to high-tech equipment without massive upfront investment. Check out our guide on How Much Does It Cost to Rent a CNC Machine? to learn more.
- Lower Production Costs: The reduced labor costs and lower material wastage often make CNC cost-effective over time.
CNC vs. Manual Machining: Which Is Better?
Precision and Accuracy
One of the main reasons people favor CNC machining over manual machining is its precision.
- Consistent Results: CNC machines offer the same precision repeatedly without manual errors.
- Tight Tolerances: With CNC, tight tolerances of up to 0.001mm are achievable, which is incredibly difficult to attain manually.
Speed and Efficiency
CNC machines work faster than their manual counterparts, especially for large production runs.
- Automation: A CNC machine can work 24/7 without fatigue, reducing the time required to complete projects.
- Reduced Setup Time: CNC machines require less time to set up compared to manual machining, thanks to the programming software that calculates the optimal path for cutting.
The Limitations of CNC Machines
1. Initial Cost
The cost of CNC machines is one of their biggest limitations. High-quality CNC machines with advanced features can be quite expensive, which could be prohibitive for small-scale businesses.
- Alternative: Renting or leasing CNC machines can be an option to offset high upfront costs. Smaller machines like a CNC Router are often more affordable.
2. Complexity in Programming
The programming aspect of CNC machining can be complex and requires a specialized skill set.
- G-Code: Writing G-code, the programming language for CNC machines, can be challenging for beginners.
- Software: Using CAM software makes it easier, but it still requires training to efficiently operate.
3. Not Ideal for All Materials
Although CNC is highly versatile, it isn’t suitable for all types of materials. Brittle materials, for instance, can sometimes crack under high-speed machining.
- Materials like Ceramics: High-speed CNC cutting can cause brittle materials like ceramics to shatter, making manual machining more suitable for such applications.
Real-World Applications of CNC Machines
1. Automotive Industry
CNC machining is extensively used in the automotive industry for producing components like gears, engine blocks, and transmission parts.
- Precision: Achieving high-precision cuts ensures that the parts fit perfectly, which is crucial for vehicle safety.
- Rapid Production: CNC helps in creating multiple units with the exact same measurements, a necessity in mass production.
2. Aerospace Industry
In aerospace, the precision and reliability offered by CNC machining are vital. Components must meet strict safety and performance standards.
- Complex Shapes: CNC allows the creation of complex geometries that are often required in aircraft parts.
- Special Materials: CNC can work with lightweight materials like aluminum and titanium, which are commonly used in the aerospace sector.
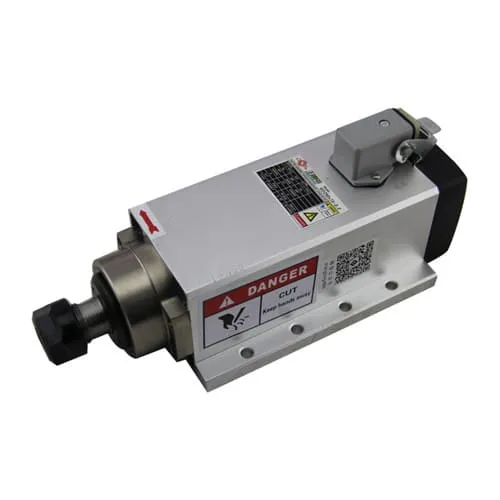
This 2.2KW ER20 Square Air-Cooled Spindle showcases the kind of precision and power that aerospace machining demands.
3. Medical Devices
CNC machining is also crucial in the medical sector for manufacturing surgical instruments, implants, and even prosthetics.
- High Precision: The level of accuracy required in medical device manufacturing makes CNC an ideal choice.
- Custom Parts: Implants and prosthetics often require a high degree of customization, which CNC can handle efficiently.
Is CNC Worth the Investment?
Pros of Investing in CNC
- Increased Productivity: CNC machines operate continuously and significantly reduce production times.
- Accuracy and Repeatability: Whether it’s a batch of 1 or 1,000 parts, CNC machines deliver consistent results.
- Reduced Waste: The high accuracy of CNC machines means less material waste, saving on costs.
Cons of Investing in CNC
- High Initial Costs: As mentioned earlier, purchasing a CNC machine requires substantial investment.
- Maintenance: Regular maintenance is required to keep the machine running smoothly, which can be costly over time.
How CNC Fits into the Future of Manufacturing
Smart Manufacturing
The integration of IoT and AI with CNC technology is transforming the concept of smart manufacturing. Machines can now predict maintenance needs, optimize tool paths, and communicate data in real time.
Prototyping with CNC
The rise of rapid prototyping has solidified CNC’s place in modern manufacturing. CNC allows manufacturers to create prototypes quickly and efficiently, shortening the development cycle.
- Versatility: CNC is versatile, capable of working on a wide variety of materials, making it ideal for prototyping across multiple industries.
FAQs
1. Is CNC better than 3D printing?
It depends on the application. CNC machining is better for high-precision metal components, while 3D printing excels in producing complex plastic parts.
2. Can CNC machines be used for wood?
Yes, CNC routers are frequently used for cutting and engraving wood, often employed by carpenters and cabinet makers for precise cuts.
3. Do CNC machines require manual programming?
Not necessarily. While manual G-code programming is possible, most CNC setups today use CAM software to automate the process.
4. What are the main components of a CNC machine?
Key components include spindle motors, control systems, axes (usually X, Y, and Z), and the cutting tool.
Conclusion
So, is CNC wrong? The short answer is no. CNC is not wrong, but it might not be the perfect solution for every manufacturing scenario. The key is understanding when and where CNC fits best. It excels in precision, efficiency, and automation, but there are scenarios where other machining methods may be better suited. Despite the initial investment, the long-term benefits—such as high-quality parts, low production errors, and scalability—make CNC a vital component of modern manufacturing.
If you’re considering CNC for your business, it’s essential to weigh its advantages against the costs and choose a solution that fits your production needs. Visit CNC Spindle Motors for more information on how to find the right spindle for you.