Introduction
When it comes to CNC spindle operation, spindle direction is a crucial factor that can determine the success or failure of a project. Whether you’re a seasoned machinist or new to CNC machines, understanding the basics of spindle rotation is essential. This article explores everything you need to know about spindle direction, including factors influencing it, tips for optimal performance, and avoiding common mistakes.
So, why is this article worth reading? Spindle rotation can affect everything from material finish to tool lifespan, and knowing how to adjust it can significantly improve your CNC operations. By the end, you’ll have practical insights to enhance precision and efficiency in your projects.
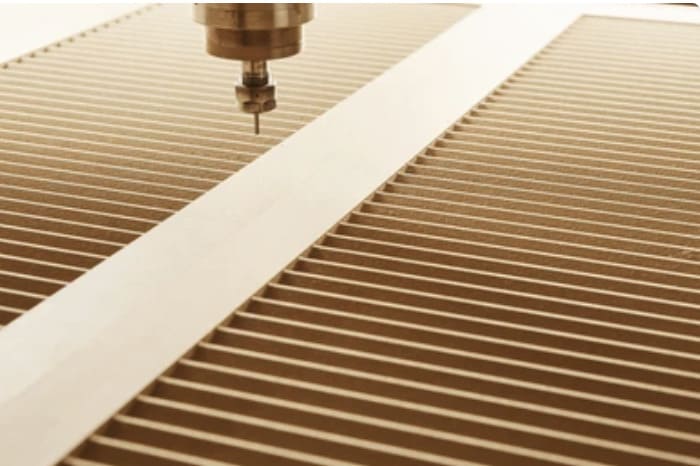
Common Symptoms of Spindle Failure
What are the signs of a failing spindle?
A failing spindle often shows warning signs before a complete breakdown. Recognizing these symptoms early can save you both time and money. Some of the most common indicators include:
- Excessive Vibration: Increased vibration in your CNC machine is one of the earliest signs of spindle failure. This can lead to poor machining quality and accelerated wear on other components.
- Strange Noises: Grinding or squealing noises can indicate bearing wear or alignment issues within the spindle.
- Inconsistent Speed: Spindle speed fluctuations can affect the quality of your cuts and may be a sign of motor or electrical issues.
- Poor Surface Finish: A deteriorating spindle often results in rough or uneven surfaces on your machined parts.
The Impact of Spindle Problems on CNC Operations
How do spindle problems affect CNC machine performance?
A malfunctioning spindle can severely disrupt CNC operations. The effects may include:
- Decreased Precision: Misalignment or worn-out bearings can cause inaccuracies in the final product, leading to rejects or rework.
- Increased Downtime: A failed spindle can bring production to a standstill, causing unplanned downtime and delays in fulfilling orders.
- Higher Operating Costs: Spindle repairs can be expensive, and ignoring the issue may result in more extensive damage to the machine.
Electrical vs. Mechanical Failures
Is your spindle suffering from an electrical or mechanical failure?
Understanding whether the problem is mechanical or electrical is key to effective troubleshooting.
- Electrical Failures: These include issues like inconsistent power supply, motor malfunctions, or faulty wiring. Common signs include erratic spindle speeds and frequent tripping of safety breakers.
- Mechanical Failures: Mechanical issues, on the other hand, involve worn-out bearings, alignment problems, or spindle housing damage. You might notice excessive noise or vibration, and the spindle may struggle to maintain speed under load.
Environmental Factors Affecting Spindle Performance
How do environmental factors influence spindle health?
The surrounding environment plays a significant role in the lifespan of your CNC spindle. Factors to consider include:
- Temperature: Excessive heat can damage the spindle motor and bearings, leading to performance issues.
- Humidity: Moisture can lead to rust and corrosion, especially in the spindle bearings.
- Dust and Debris: Contaminants can clog moving parts, leading to increased friction and wear.
Routine Checks and Balancing
How often should CNC spindles be serviced?
Routine maintenance is key to preventing spindle failure. For most machines, spindles should be checked every 6 to 12 months, but high-precision operations may require more frequent inspections. Regular checks should include:
- Spindle Alignment: Misalignment can cause rapid wear and reduce machining accuracy.
- Bearing Wear: Bearings should be inspected for signs of wear or damage.
- Vibration Analysis: Periodic vibration tests can help detect early signs of spindle imbalance or bearing wear.
Lubrication and Cleaning Protocols
What are the best practices for spindle lubrication and cleaning?
Proper lubrication and cleaning are vital for spindle performance. Follow these guidelines:
- Lubrication: Apply the recommended lubricants at regular intervals to prevent friction and overheating. Over-lubrication can cause leaks, while under-lubrication can lead to bearing failure.
- Cleaning: Regularly clean the spindle to remove dust, debris, and other contaminants. Use non-abrasive materials to avoid damaging sensitive components.
Initial Diagnosis: What to Look For
What are the first steps in diagnosing spindle problems?
Initial diagnosis is crucial in pinpointing the cause of spindle issues. Here’s a step-by-step approach:
- Inspect the Bearings: Worn-out bearings are a common cause of spindle failures.
- Check for Misalignment: Misalignment can lead to uneven wear and vibration issues.
- Test the Spindle Motor: Fluctuations in spindle speed may indicate motor problems.
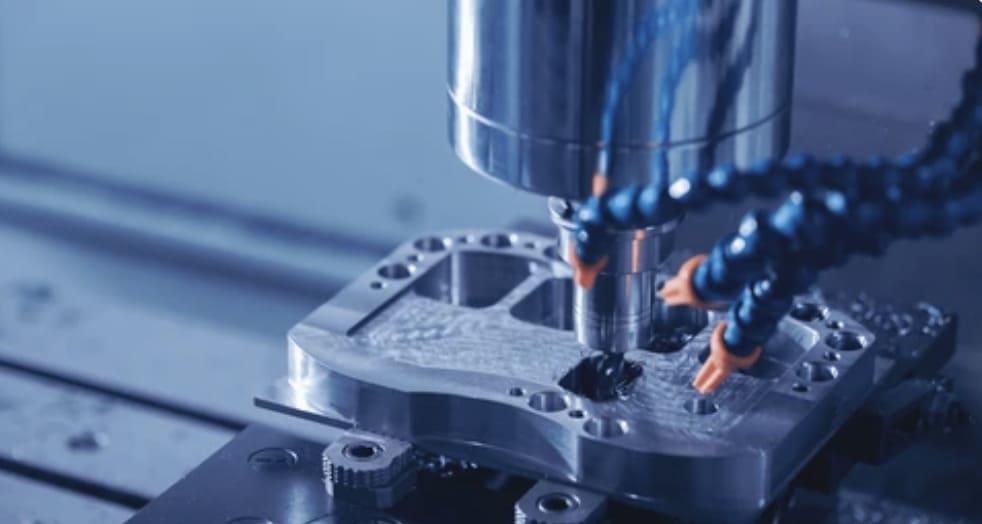
Advanced Diagnostic Tools and Techniques
What advanced tools are available for diagnosing spindle problems?
When basic inspection isn’t enough, advanced diagnostic tools can provide more accurate results:
- Vibration Analyzers: These tools help detect imbalances or misalignment in the spindle.
- Thermal Imaging Cameras: These can identify overheating in bearings or motors.
- Runout Testers: A runout tester measures the accuracy of spindle rotation, helping detect alignment issues.
When to Call in the Experts
When should you seek professional help for spindle issues?
While DIY repairs are possible for minor issues, professional help is recommended in these cases:
- Complex Electrical Issues: Problems with wiring, motors, or controllers often require a qualified technician.
- Severe Mechanical Damage: If the spindle has significant wear or physical damage, it’s best to consult a specialist.
- Repeated Failures: If you’re facing recurring issues, a professional can help diagnose and resolve the underlying problem.
DIY Fixes for Minor Spindle Problems
Can a damaged CNC spindle be repaired, or must it be replaced?
Not all spindle problems require professional repair or replacement. Minor issues such as misalignment or small bearing wear can often be fixed in-house. Here are some common DIY fixes:
- Aligning the Spindle: Adjusting the spindle alignment can resolve accuracy issues.
- Replacing Worn Bearings: Bearings are a common wear item and can often be replaced without expert help.
- Cleaning and Lubrication: Thorough cleaning and applying the correct lubrication can resolve many performance issues.
When to Consider an Upgrade
What improvements can be expected with a spindle upgrade?
If your spindle is outdated or frequently failing, it may be time to consider an upgrade. Upgraded spindles offer:
- Increased Speed: Modern spindles often provide higher RPMs for faster machining.
- Greater Precision: Newer models feature improved accuracy, which is essential for high-precision work.
- Longer Lifespan: Enhanced materials and technology can extend the life of your spindle, reducing downtime and costs.
Selecting the Right Spindle for Your CNC Machine
How do you select the right spindle for your CNC machine?
Choosing the right spindle for your CNC machine depends on several factors:
- Compatibility: Ensure the spindle is compatible with your machine’s specifications.
- Speed and Torque Requirements: Match the spindle’s capabilities to the type of materials and machining tasks you handle.
- Budget: Balance performance features with cost to find the best spindle within your price range.
Key Takeaways
- Regular maintenance and early diagnosis are crucial for avoiding costly spindle failures.
- Electrical and mechanical issues require different troubleshooting approaches.
- DIY fixes can be effective for minor problems, but professional help may be necessary for more serious issues.
- Upgrading your spindle can improve machining performance and reduce downtime.
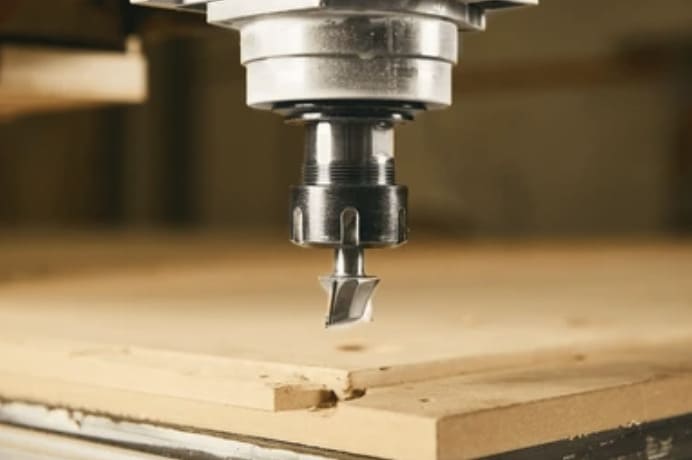
- RicoCNC has a team of professionals who have been engaged in the design, production, sales, and maintenance of electro spindles for many years. Our company accepts the purchase of various types of CNC spindles.
water-cooled CNC spindle motors
Edge banding machine spindle motors.
- If you need any CNC spindle, please contact us.