Introduction
Understanding the power capabilities of CNC spindles is crucial for anyone involved in precision machining or manufacturing. Whether you’re optimizing your existing equipment or investing in new technology, knowing how CNC spindle power affects your operations is essential. This article will delve into the power range of common CNC spindles, exploring factors that influence power needs, and discuss global market trends. By the end, you’ll have a clear grasp of selecting the right CNC spindle power for your needs and insights into future trends.
Defining CNC Spindle and Its Importance in Machining
CNC spindles are critical components in machining processes, serving as the rotating element that holds and drives the cutting tool. CNC spindle motors provide the necessary power to perform various operations such as drilling, milling, and turning. The spindle’s efficiency directly impacts the quality of the finished product and the overall machining time.
Understanding the power of a CNC spindle is vital because it influences everything from the type of materials that can be machined to the speed and precision of the cutting process. Spindles come in various configurations and power ratings, each suited for specific tasks in the machining workflow.
Overview of Power Range for Common CNC Spindles
CNC spindles are available in a wide range of power ratings, typically measured in horsepower (HP) or kilowatts (kW). The power range for common CNC router spindles can vary from about 1.5 kW for smaller machines to over 20 kW for industrial applications.
Spindle motors designed for CNC routers are often less powerful compared to those used in heavy-duty machining centers. This variation in power is driven by the intended application, material hardness, and the desired speed of operation.
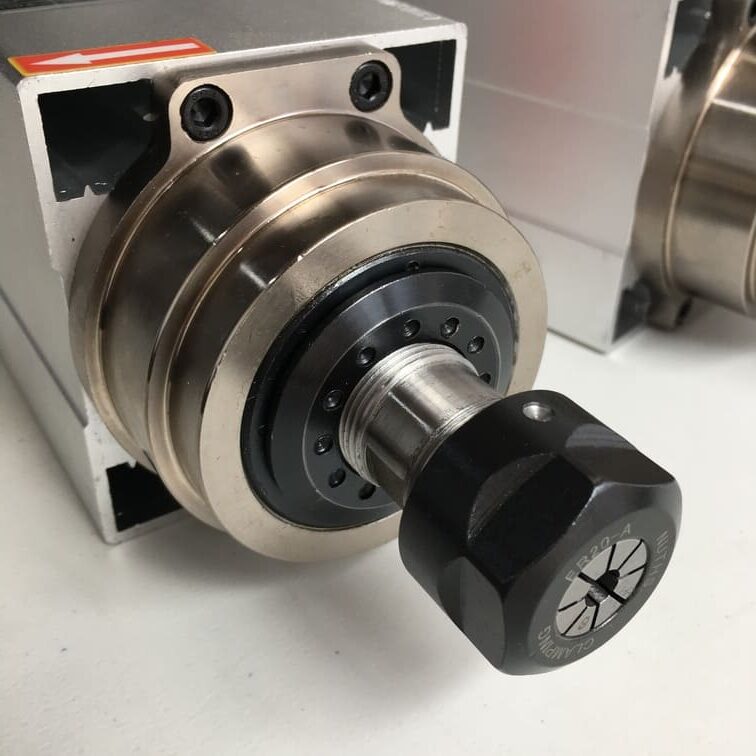
Material Types and Their Impact on Power Needs
Different materials require different levels of spindle power. For instance, machining metals like steel and titanium demands more power compared to softer materials such as plastics or wood. The spindle for CNC must be adequately powered to handle the increased resistance posed by harder materials.
When working with tough materials, it’s crucial to select a spindle motor that provides sufficient torque and stability to maintain precision and avoid tool wear or breakage. Understanding the material you will be machining helps in choosing a spindle with the right power rating.
The Role of Cutting Speed and Feed Rate
Cutting speed and feed rate are significant factors in determining the power requirements of a CNC spindle. Higher cutting speeds and feed rates typically necessitate more power to maintain efficiency and precision.
CNC spindles with higher power ratings can handle faster feed rates and cutting speeds, leading to increased productivity and shorter machining times. However, balancing these parameters is essential to avoid overheating and ensure the quality of the finished product.
Balancing Power and Precision for Optimal Performance
Achieving the right balance between power and precision is crucial for optimal CNC machining performance. A high-power CNC spindle motor can improve productivity but may compromise precision if not used correctly.
Conversely, a spindle with lower power might achieve higher precision but at a slower rate. It’s important to evaluate the specific requirements of your project and choose a spindle that matches both the power needs and the precision requirements.
Emerging Technologies and Their Influence on Power Capabilities
Recent advancements in spindle technology have led to significant improvements in power capabilities and efficiency. Innovations such as dual spindle CNC machines and multi-spindle CNC machines offer enhanced power and versatility for complex machining tasks.
Emerging technologies also include spindle motors that incorporate advanced cooling systems and smarter control algorithms, improving performance and extending spindle life. Staying updated with these technological advancements helps in making informed decisions about CNC spindle investments.
Geographic Hotspots for CNC Spindle Manufacturing and Use
CNC spindles are manufactured and used globally, with notable hotspots including countries like Germany, Japan, and the United States. These regions are known for their high-quality spindle production and advanced machining technologies.
Understanding regional trends can provide insights into the latest developments and innovations in CNC spindle technology. These geographic areas often lead the way in setting industry standards and adopting new technologies.
How Environmental Regulations Shape Spindle Power Innovations
Environmental regulations play a significant role in shaping the development of CNC spindles. Stricter regulations on energy consumption and emissions drive manufacturers to develop more energy-efficient and environmentally friendly spindle solutions.
CNC router spindles and other spindle types are increasingly incorporating eco-friendly technologies to meet regulatory requirements and reduce operational costs. Keeping an eye on these trends ensures that your spindle choices align with both industry standards and environmental goals.
Breaking Down the Highest Power CNC Spindles Available
The market offers several high-power CNC spindles designed for heavy-duty applications. Spindles with power ratings exceeding 20 kW are used in industries such as aerospace and automotive for machining large and tough components.
These high-power spindle motors are designed to handle rigorous tasks while maintaining high precision and efficiency. Reviewing specifications and performance metrics of these spindles helps in selecting the best option for your needs.
Case Studies: Applications Requiring Maximum Spindle Power
Case studies highlight the practical applications of high-power CNC spindles in various industries. For instance, aerospace manufacturing requires spindles with high power to machine complex parts from tough materials like titanium.
By examining these case studies, you can gain insights into how high-power spindles contribute to achieving precise results and improving overall productivity in challenging machining environments.
Future Prospects: Where is Spindle Power Heading?
The future of CNC spindle power is marked by advancements in technology and increasing demands for higher performance. Trends such as the integration of AI and IoT in spindle technology are expected to enhance power capabilities and operational efficiency.
Keeping abreast of these developments helps anticipate future needs and make strategic decisions about spindle investments.
Assessing Your Project’s Requirements
Before selecting a CNC spindle, it’s crucial to assess your project’s specific requirements. Consider factors such as material type, desired cutting speed, and precision to determine the appropriate spindle power.
CNC spindle motors come in various power ratings and configurations, so aligning your project’s needs with the right spindle ensures optimal performance and efficiency.
Compatibility with Machine and Materials
Ensure that the spindle you choose is compatible with both your CNC machine and the materials you plan to work with. Compatibility affects performance, precision, and the longevity of the spindle and machine.
Selecting a spindle that matches your machine’s specifications and material requirements helps in achieving the best results and avoiding operational issues.
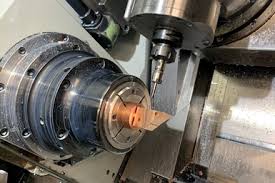
Cost-Benefit Analysis of High-Power vs Standard CNC Spindles
Performing a cost-benefit analysis is essential when deciding between high-power and standard CNC spindles. High-power spindles offer increased performance but come at a higher cost.
Evaluate the potential benefits in terms of productivity, precision, and material handling against the additional investment required for high-power spindles. This analysis helps in making a well-informed decision based on your budget and project requirements.
Summary of Key Points
- Understanding CNC spindle power is vital for optimizing machining processes.
- Power ratings for CNC spindles vary widely depending on application and material.
- Factors such as cutting speed, feed rate, and material type influence power needs.
- Emerging technologies and environmental regulations impact spindle power innovations.
- Assessing your project’s requirements and performing a cost-benefit analysis ensures you select the right spindle for your needs.
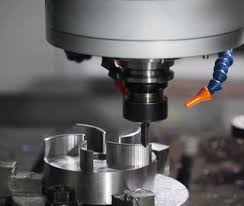
- RicoCNC has a team of professionals who have been engaged in the design, production, sales, and maintenance of electro spindles for many years. Our company accepts the purchase of various types of CNC spindles.
water-cooled CNC spindle motors
Edge banding machine spindle motors.
- If you need any CNC spindle, please contact us.