Introduction
The need for increased productivity, precision, and efficiency in manufacturing has led to the widespread adoption of CNC (Computer Numerical Control) multi-spindle machines. Unlike their single-spindle counterparts, CNC multi-spindle machines are equipped with multiple spindles that can work simultaneously, dramatically improving production rates. These machines are used in a variety of industries, but they are particularly beneficial in woodworking, where the high demand for speed, consistency, and precision makes them invaluable.
The purpose of this article is to explore the key functions of CNC multi-spindle machines, their benefits over traditional single-spindle machines, and how they can be optimized for various woodworking tasks. By understanding the full potential of these machines, you can make informed decisions about whether they are right for your manufacturing needs.
Understanding CNC Multi-Spindle Machines
CNC multi-spindle machines are designed to execute multiple tasks simultaneously. Each spindle in the machine can perform independent or synchronized operations, allowing for a higher level of productivity. For instance, a multi-spindle CNC machine used in woodworking can perform tasks such as cutting, drilling, or engraving multiple parts at the same time. This efficiency is especially crucial in industries where high-volume production is required.
The Basics of CNC Multi-Spindle Operations
At its core, a CNC multi-spindle machine uses a central control unit to manage the operations of each spindle. This control allows the machine to execute complex tasks with extreme precision. The spindles, powered by CNC spindle motors, are responsible for the cutting, shaping, or drilling of materials. The number of spindles on a machine can vary, with some machines featuring as many as 12 spindles to handle high-volume tasks.
Key Components and Their Functions
The key components of a CNC multi-spindle machine include the spindles, motors, bed, and control system. The spindles are the central elements, driven by powerful CNC spindle motors that determine the machine’s overall performance. The control unit dictates the movements of each spindle, ensuring precision and accuracy. Finally, the bed provides stability and support, ensuring that materials are held securely during machining.
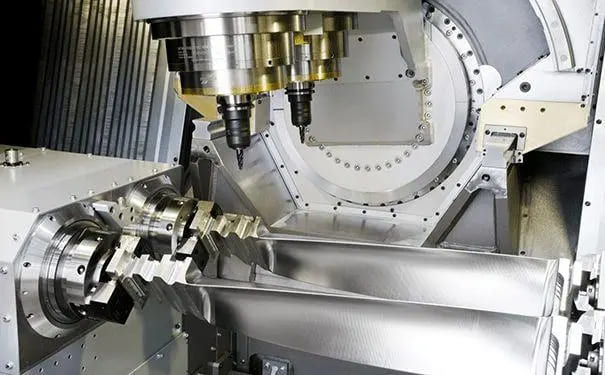
Advantages of Using Multi-Spindle Machines in Woodworking
The benefits of CNC multi-spindle machines in woodworking are numerous. These machines can significantly increase productivity while maintaining high levels of precision. This section outlines some of the key advantages that multi-spindle machines offer over single-spindle machines.
Efficiency and Productivity Gains
One of the primary advantages of CNC multi-spindle machines is their ability to perform multiple operations simultaneously. With multiple spindles working in tandem, manufacturers can reduce production time without compromising on quality. For example, if you need to cut, drill, and sand several parts of a workpiece, a CNC router spindle can be set to perform all these tasks at once, drastically speeding up the production process.
Precision and Consistency in Outputs
In addition to increasing efficiency, CNC multi-spindle machines offer superior precision. The CNC control system ensures that each spindle operates with extreme accuracy, reducing errors and waste. This precision is particularly important in woodworking, where even small deviations can lead to flawed products. CNC multi-spindle machines guarantee consistency across large production runs, making them ideal for high-volume woodworking tasks such as furniture manufacturing.
Types of CNC Multi-Spindle Machines for Woodworking
CNC multi-spindle machines come in various types, each tailored to specific tasks. Understanding the differences between these machines will help you choose the best one for your needs.
Fixed vs. Movable Spindle Configurations
CNC multi-spindle machines are generally available in two configurations: fixed and movable spindle setups. Fixed spindle machines are ideal for repetitive tasks where the spindle remains stationary during machining. These machines are perfect for high-volume production runs where consistency is key. In contrast, movable spindle configurations offer greater flexibility, allowing for more complex tasks where the spindles need to move in different directions to accommodate intricate designs.
Choosing the Right Machine for Your Project
Selecting the appropriate CNC multi-spindle machine depends on your specific project requirements. For instance, if you need to handle high-volume tasks, a machine with more spindles will be ideal. On the other hand, if you’re working on more detailed projects, a CNC router spindle motor configuration may provide the precision and control you need.
Optimizing Your CNC Machine Setup
Properly setting up and maintaining your CNC multi-spindle machine is crucial for maximizing its performance. This section will cover the best practices for ensuring that your machine operates at peak efficiency.
Best Practices for Maintenance and Longevity
Maintaining your CNC multi-spindle machine is key to ensuring long-term reliability. Regularly lubricating the spindles and CNC spindle motor is essential to preventing overheating and ensuring smooth operation. Additionally, routine checks for alignment and wear on the spindles will help prevent costly breakdowns. Implementing a maintenance schedule will also minimize downtime and extend the life of your machine.
Troubleshooting Common Issues
CNC multi-spindle machines, while highly efficient, can encounter issues such as spindle misalignment, overheating, or motor failure. Monitoring spindle temperatures and performing regular inspections will help you catch these problems early. Proper troubleshooting can save you time and money, ensuring that your machine continues to operate efficiently.
Essential Functions of CNC Multi-Spindle Machines
CNC multi-spindle machines are designed to perform a variety of essential tasks in the woodworking industry, from cutting and drilling to engraving and finishing. The versatility of these machines makes them indispensable in high-volume manufacturing environments.
Synchronous Processing for Efficiency
One of the standout features of CNC multi-spindle machines is their ability to perform synchronous processing. This means that the spindles can work on different parts of a workpiece at the same time, drastically reducing production time. Synchronous processing is especially useful in woodworking, where large projects often require multiple operations to be performed simultaneously.
Precision and Accuracy in Repetitive Tasks
CNC multi-spindle machines are known for their precision and accuracy, which is particularly important in woodworking. The CNC system ensures that each spindle operates within tight tolerances, allowing for highly accurate and consistent results. This precision is crucial in tasks that require repetitive operations, such as cutting multiple pieces of wood to the same dimensions.
Comparing Single-Spindle to Multi-Spindle CNC Machines
Choosing between a single-spindle and multi-spindle CNC machine can be challenging, especially if you’re unfamiliar with the key differences between the two. This section will compare the advantages and disadvantages of each type of machine.
Advantages of Multi-Spindle Over Single Spindle
While single-spindle machines are more affordable and easier to operate, multi-spindle machines offer several distinct advantages. Multi-spindle machines are faster, more efficient, and capable of handling larger workloads. For high-volume production environments, multi-spindle machines provide superior performance and productivity.
Ideal Use Cases for Multi-Spindle Machines
Multi-spindle machines are ideal for large-scale woodworking projects that require speed and precision. They are commonly used in industries such as furniture manufacturing, cabinetry, and mass production of wooden components. In contrast, single-spindle machines are better suited for small-scale projects or custom work where precision and flexibility are more important than speed.
Impact of CNC Multi-Spindle Machines on Woodworking
The introduction of CNC multi-spindle machines has had a profound impact on the woodworking industry. These machines have increased production speeds, improved the quality of finished products, and reduced labor costs.
Enhancements in Production Speed and Quality
CNC multi-spindle machines have revolutionized woodworking by automating many of the tasks that were once done manually. This automation has resulted in faster production times and higher-quality outputs. The consistent performance of CNC spindles ensures that each piece is machined to the same specifications, reducing errors and waste.
Case Studies: Successful Integrations in the Industry
Many woodworking companies have successfully integrated CNC multi-spindle machines into their production processes. For example, a furniture manufacturer that switched from manual processes to CNC machining saw a 30% increase in production speed and a significant reduction in material waste. These success stories highlight the tangible benefits of investing in CNC multi-spindle technology.
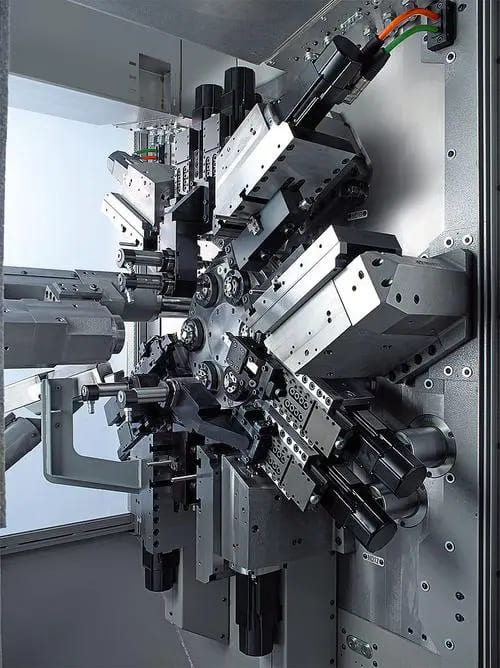
Maintenance Tips for CNC Multi-Spindle Machines
Proper maintenance is essential for ensuring that your CNC multi-spindle machine operates at peak performance. This section will provide tips for keeping your machine in top condition.
Routine Maintenance Checklist
To keep your CNC multi-spindle machine running smoothly, it’s important to follow a routine maintenance checklist. This checklist should include tasks such as lubricating the spindles, checking for wear and tear, and ensuring that the CNC spindle motor is functioning properly. Regularly cleaning the machine and inspecting the control system for errors will also help prevent unexpected breakdowns.
Troubleshooting Common Issues
Even with regular maintenance, CNC multi-spindle machines can experience issues. Some common problems include spindle misalignment, overheating, and motor failure. By troubleshooting these issues early, you can prevent more serious problems from occurring. Regularly monitoring the machine’s performance and addressing any anomalies will help you keep your machine in good working order.
Conclusion
CNC multi-spindle machines are an essential tool for woodworking professionals looking to improve efficiency, precision, and productivity. By understanding the key components, functions, and maintenance requirements of these machines, you can make informed decisions about how to optimize your production process. Whether you’re working on large-scale projects or smaller, custom jobs, a CNC multi-spindle machine can help you achieve your goals.
Summary
- CNC multi-spindle machines significantly improve productivity and precision in woodworking.
- They offer several advantages over single-spindle machines, including increased speed and efficiency.
- Proper maintenance is key to ensuring the longevity and performance of these machines.
- Multi-spindle machines are ideal for high-volume production tasks in woodworking.
- Investing in a CNC multi-spindle machine can lead to long-term savings in labor and material costs.
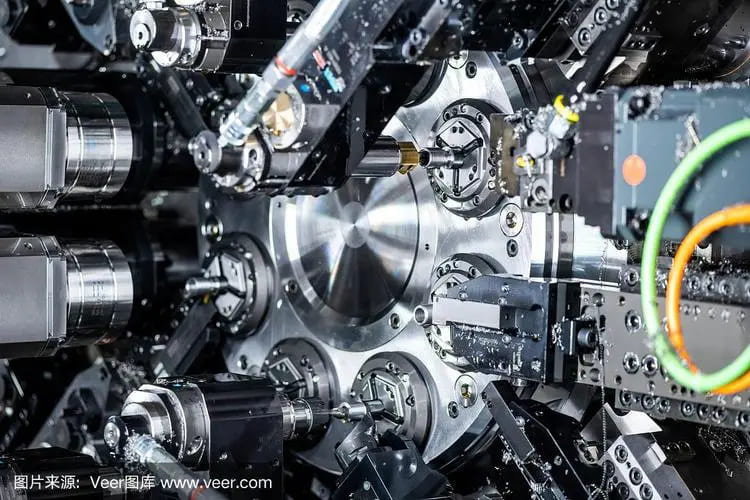
- RicoCNC has a team of professionals who have been engaged in the design, production, sales, and maintenance of electro spindles for many years. Our company accepts the purchase of various types of CNC spindles.
water-cooled CNC spindle motors
Edge banding machine spindle motors.
- If you need any CNC spindle, please contact us.