In today’s ever-evolving world of manufacturing, technology plays a crucial role in enhancing efficiency, accuracy, and overall productivity. One such technology that has revolutionized the industrial landscape is CNC machining. But what exactly does CNC stand for? Understanding the answer is the key to unlocking the benefits and applications of this technology. In this comprehensive guide, we will explore the ins and outs of CNC machining, from its basic principles to its advanced applications, with plenty of practical insights. Let’s dive in!
What Does CNC Stand For?
CNC stands for Computer Numerical Control. It refers to a technology used in the manufacturing industry where a computer is used to control the movement and operation of machinery and tools. CNC machines automate complex processes that were traditionally performed manually by machinists. In simple terms, CNC machines use computers to precisely execute commands for cutting, shaping, drilling, or milling materials, making production faster, safer, and more accurate.
A CNC system relies on a combination of hardware and software to translate a CAD (Computer-Aided Design) file into actions that control the physical movement of the tool or machine. G-codes and M-codes are used to command the machine’s movements and functions.
The process offers significant advantages in terms of precision, repeatability, and the ability to create complex parts, which is why CNC machining is prevalent in industries like automotive, aerospace, and consumer electronics.
A Brief History of CNC Technology
Evolution from Manual Machining to CNC
CNC technology evolved from manual machining techniques, where machinists would manually control tools to shape raw materials into finished products. In the early 1950s, Numerical Control (NC) was developed, which used punch cards or tapes to control machine tools automatically.
By the late 1970s and early 1980s, CNC emerged as an upgrade to NC, introducing computer control that could store and execute programs without physical tapes. This technological leap improved flexibility, efficiency, and accuracy. With CNC, machinists could make more complex parts, requiring fewer manual interventions.
Today, CNC machines have become highly advanced, offering features like multi-axis machining, automatic tool changers, and software integration for high-precision manufacturing.
Major Milestones in CNC Development
- 1952: The first NC machine was developed at MIT.
- 1967: Introduction of computer controls for enhanced accuracy and repeatability.
- 1980s: Adoption of CAD/CAM software to control CNC machines and simplify programming.
- 1990s to Today: Advancements in multi-axis control, automation, and integration with Industry 4.0.
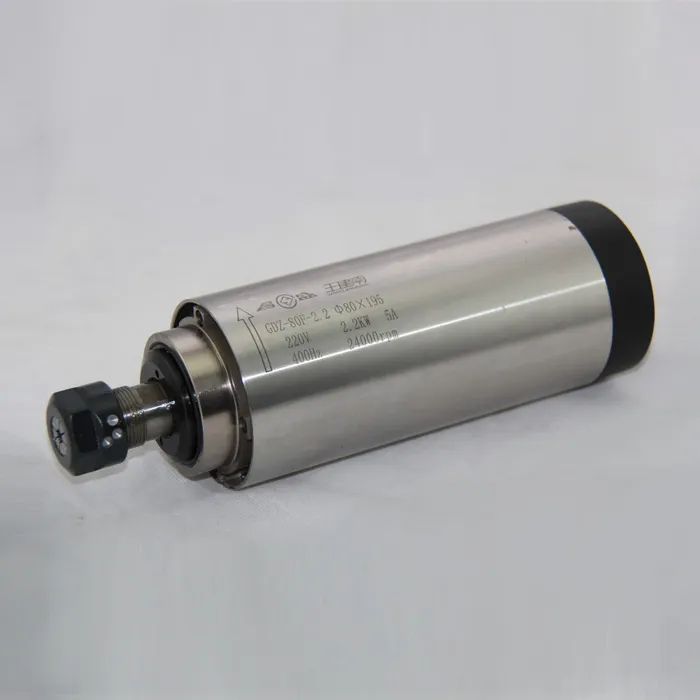
If you’re considering upgrading your machine for more advanced capabilities, take a look at our 2.2KW ER20 Air-Cooled Spindle, perfect for achieving high speeds and enhancing efficiency.
Types of CNC Machines
CNC machines come in different types and configurations, each designed for specific purposes in manufacturing. Below, we will take a detailed look at some of the popular types of CNC machines.
1. CNC Milling Machines
Milling machines use rotating cutting tools to remove material from a workpiece. CNC milling machines are highly versatile and used for cutting, drilling, and shaping materials like metal, plastic, and wood.
- Vertical Milling Machines: In these machines, the spindle axis is vertical, making them suitable for flat surfaces.
- Horizontal Milling Machines: Horizontal machines are used for operations where cutting tools are parallel to the workpiece.
- Multi-Axis Milling Machines: CNC milling machines with more than three axes, like 4-axis or 5-axis mills, enable complex geometries and precision parts production.
2. CNC Lathes
CNC Lathes rotate the workpiece while the cutting tool remains stationary. This type of machine is used primarily for turning operations, which produce cylindrical parts.
- Single-Turret Lathes: Suitable for most standard turning operations.
- Multi-Spindle Lathes: Useful for high-volume production where multiple parts can be machined simultaneously.
3. CNC Routers
CNC Routers are typically used for cutting wood, plastics, and soft metals. They are popular in woodworking and cabinetry.
- Tabletop Routers: Smaller versions ideal for prototyping or hobbyist projects.
- Industrial Routers: Larger, more powerful routers used for commercial manufacturing.
4. CNC Plasma Cutters
These machines use a plasma torch to cut through electrically conductive materials like steel and aluminum. Plasma cutting is ideal for making sharp cuts in metal.
5. CNC Grinders
CNC Grinders use abrasive wheels to achieve extremely fine finishes on materials. They are mainly used in the tool and die industry.
The Role of CAD and CAM in CNC Machining
Computer-Aided Design (CAD) and Computer-Aided Manufacturing (CAM) are integral parts of the CNC machining process. Let’s break down their roles.
CAD (Computer-Aided Design)
CAD software is used to create a digital model of the part to be manufactured. Designers and engineers utilize CAD programs to create precise, 3D designs that guide the CNC machine’s operations. Popular CAD software includes AutoCAD, SolidWorks, and Fusion 360.
CAM (Computer-Aided Manufacturing)
CAM software converts CAD models into machine-readable instructions, usually G-code or M-code, which CNC machines understand. CAM software helps ensure that the production process follows precise paths, feeds, and speeds for optimal cutting efficiency.
Using both CAD and CAM, engineers can take a product from concept to production with minimal manual effort, allowing them to optimize efficiency, reduce waste, and shorten production times.
If you need a new spindle that’s ideal for integrating with CAD/CAM for precision control, you might want to check out the 60000RPM 1.2KW ER11 Water-Cooled Spindle, which offers both high speed and accuracy for various applications.
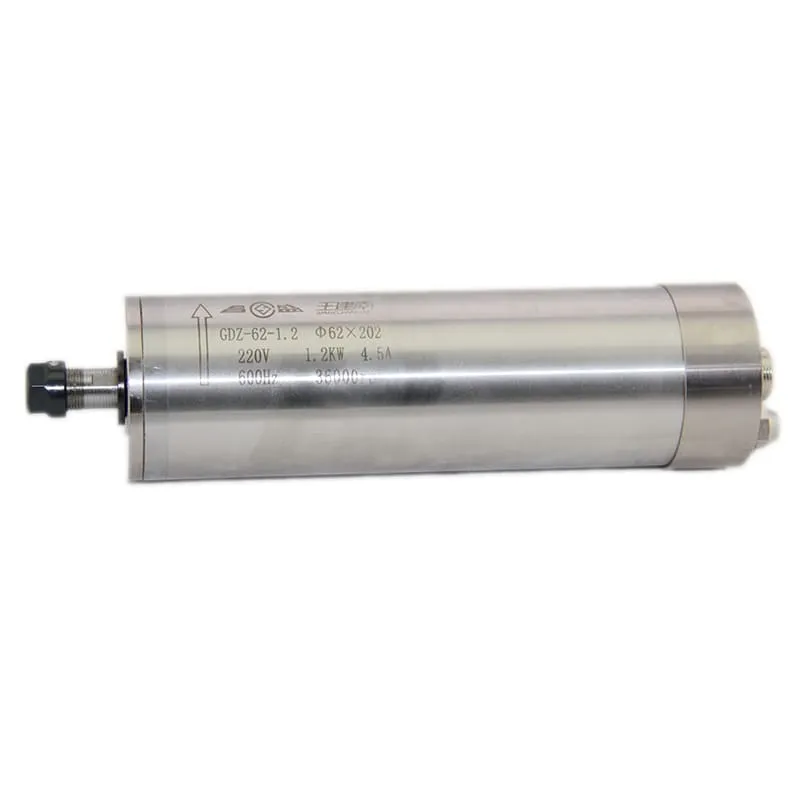
How CNC Machines Work
CNC machines function through precise instructions that come in the form of G-code. This code tells the machine where to move, at what speed, and what actions to take, such as cutting, drilling, or milling.
Step-by-Step Overview of CNC Machining
- Design Phase: A part is designed using CAD software, which provides detailed dimensions and requirements.
- Programming: The CAD file is imported into CAM software, which converts the model into G-code or M-code.
- Setup: The CNC machine is set up with the correct tools, materials, and work-holding devices.
- Operation: The machine uses the code to move and perform the necessary operations, cutting or shaping the material as per the design.
- Inspection: After the machining is complete, the part is inspected to ensure that it matches the required specifications.
Advantages of CNC Machining
CNC machining offers numerous advantages, which have made it an essential part of the modern manufacturing industry.
- Precision: CNC machines follow programmed instructions precisely, resulting in parts that are accurate to within microns.
- Repeatability: The same part can be produced consistently with no variations, making CNC machining ideal for mass production.
- Complex Designs: CNC machines are capable of making intricate cuts and complex geometries that would be impossible or difficult manually.
- Automation: The entire process is automated, requiring less manual intervention and reducing the risk of human error.
- Flexibility: CNC machines can switch between different tasks easily by changing the program, making them suitable for prototyping and custom manufacturing.
Disadvantages of CNC Machines
While CNC machines are beneficial, they do come with certain limitations.
- High Initial Cost: CNC machines are more expensive compared to conventional machines.
- Training Requirement: Operators need specialized training to program and operate CNC machines effectively.
- Maintenance: Proper maintenance is essential to keep CNC machines in good working condition, which can be costly.
However, these disadvantages are often outweighed by the increased production capabilities and quality that CNC machines offer.
CNC Programming Languages: G-Code and M-Code
The languages of CNC machining are G-code and M-code, which control different aspects of machine movement and functionality.
G-Code
G-code commands are primarily used to control linear movements like cutting and drilling. For example, G01 is used for linear interpolation, which tells the machine to move in a straight line from one point to another at a specific speed.
M-Code
M-codes are used to control miscellaneous functions of the machine, such as spindle rotation and coolant control. For instance, M03 is a command to turn the spindle on in a clockwise direction.
Understanding these codes is crucial for machinists to manually adjust or write CNC programs when needed.
Common Applications of CNC Machining
1. Automotive Industry
CNC machining is widely used in the automotive industry for creating precision parts like engine components, brake rotors, and gearboxes. The ability to produce complex designs ensures high quality and performance.
2. Aerospace Industry
In the aerospace industry, CNC machining is essential due to the need for precision and reliability. Parts like turbine blades and structural frames are often produced using CNC technology to meet stringent safety standards.
3. Consumer Electronics
Many consumer electronics like smartphones, laptops, and gaming consoles use CNC-machined parts. These machines create the precise and intricate enclosures, connectors, and other components needed.
Frequently Asked Questions
1. What industries use CNC machining?
CNC machining is used across many industries, including automotive, aerospace, medical, and electronics.
2. What is the main benefit of CNC machining?
The main benefit of CNC machining is its ability to produce high-precision parts consistently with minimal manual intervention.
3. What is G-code?
G-code is a programming language used to control CNC machines, telling them where to move and what operations to perform.
4. What materials can be machined with CNC?
CNC machining can work with a variety of materials, including metals, plastics, wood, and composites.
5. Are CNC machines suitable for mass production?
Yes, CNC machines are highly suitable for mass production due to their repeatability and precision.
Conclusion
In conclusion, CNC machining is a powerful technology that has reshaped the manufacturing industry. It offers unparalleled precision, speed, and flexibility, making it the go-to solution for creating complex parts across various industries. From the initial design to the final inspection, CNC machining ensures that each part is made to the highest standards, reducing errors and increasing efficiency.
If you’re looking to expand your CNC setup or upgrade your existing machine, consider exploring our extensive collection of CNC spindles to maximize your capabilities. The right spindle can dramatically enhance your machine’s performance and ensure you meet all your production demands efficiently.
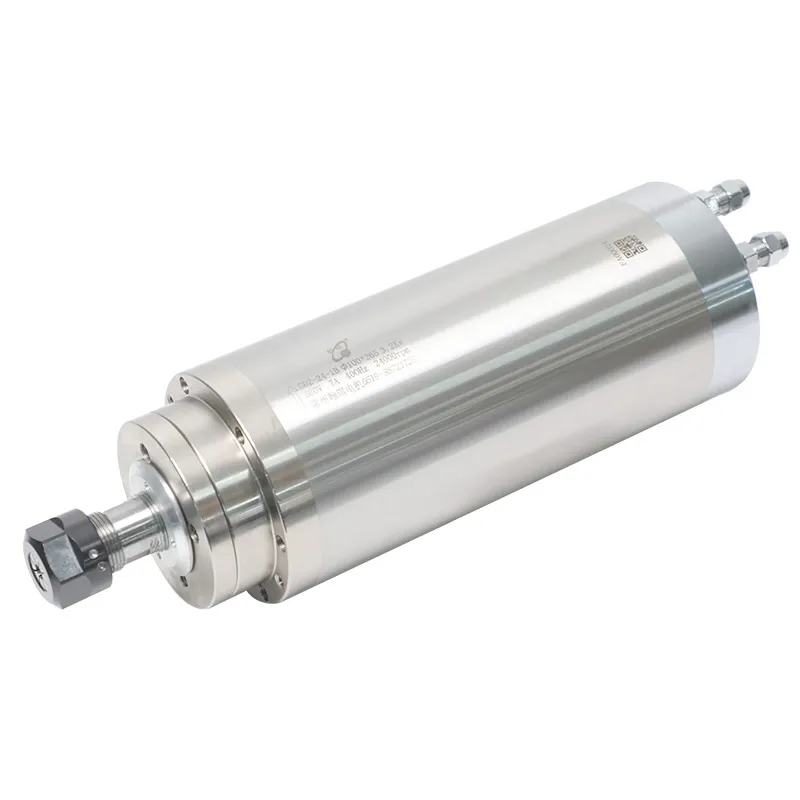