What Does CNC Lathe Stand For?
What does CNC lathe stand for? This is a question frequently asked by individuals looking to understand the essentials of modern manufacturing technology. CNC lathe machines are pivotal in the manufacturing industry, offering incredible precision, efficiency, and automation. The term CNC lathe stands for Computer Numerical Control lathe, a machine that has revolutionized how parts are produced by automating the process of cutting, drilling, and shaping materials. In this detailed guide, we will delve into the meaning of CNC lathe, how it works, its benefits, and the different types available in the market. Understanding CNC lathe technology can open doors to endless possibilities in both production and design, making it a crucial concept for modern manufacturing.
Understanding the Basics: What is a CNC Lathe?
1. What Does CNC Mean?
The term CNC stands for Computer Numerical Control. CNC is a type of control system that uses computers to operate machinery, which in this case, is the lathe. A CNC machine receives programmed commands that tell it how to move, how fast to move, and in which direction. This allows the machine to perform various tasks with incredible precision, which would be difficult or even impossible with manual operation.
- Automation: One of the most significant advantages of CNC technology is that it eliminates much of the manual labor involved in machining.
- Precision: CNC systems allow for exact control of the machine’s movements, ensuring that every part produced is to exact specifications.
The integration of CNC technology into lathes has transformed manufacturing, allowing for more consistent quality and efficient production processes.
Explore our CNC spindle motors that enhance the accuracy and efficiency of CNC machines.
2. What is a Lathe?
A lathe is a machine tool that rotates a workpiece on its axis to perform various operations, such as cutting, sanding, knurling, drilling, or deformation. This tool is incredibly versatile and can be used on materials such as metal, wood, and plastic to create symmetrical objects.
- Spindle: The spindle is the part of the lathe that holds and rotates the workpiece.
- Tool Post: The tool post holds the cutting tool in place and moves it against the spinning workpiece to shape it.
The combination of a lathe with CNC control allows for the automation of many of these processes, leading to higher precision and productivity.
Consider our 1.5KW ER11 Square Air-Cooled Spindle with Flange to improve the overall performance of your CNC lathe machine.
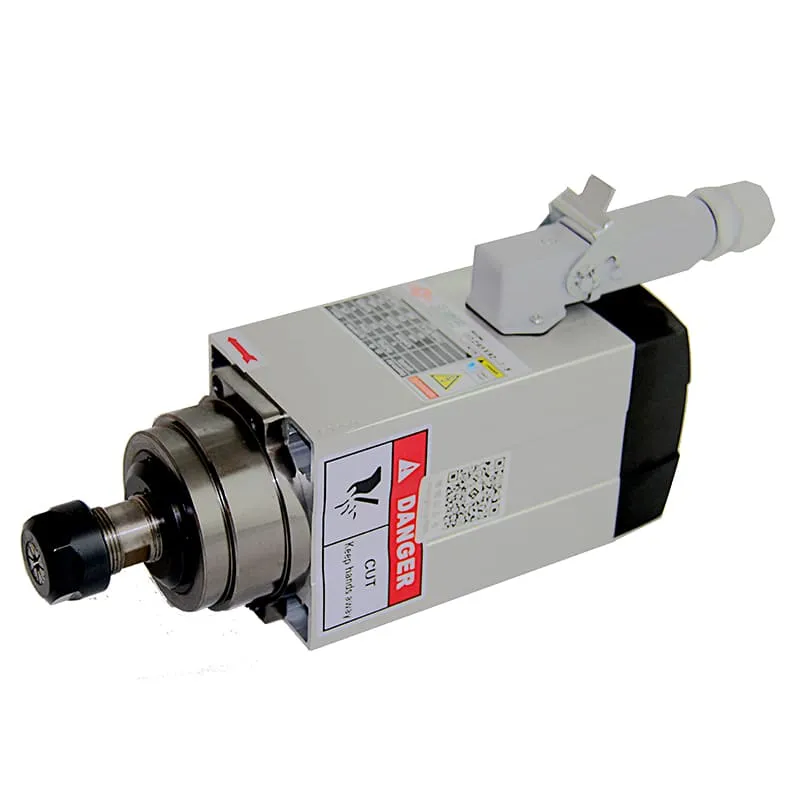
The Core Components of a CNC Lathe
1. Workholding System
The workholding system of a CNC lathe is what secures the workpiece while it is being machined. The most common workholding devices are chucks and collets. The correct workholding device is critical to ensure stability and precision during the cutting process.
- Chucks: These are used for gripping irregularly shaped materials, usually made of metal.
- Collets: Typically used for round materials, they provide better centering and are ideal for high-precision tasks.
Correctly setting up the workholding system ensures that the workpiece is machined with minimal vibration, leading to a better surface finish.
2. Tool Turret
The tool turret is a rotating component that holds multiple cutting tools. The CNC system can automatically switch between these tools during the machining process, allowing the CNC lathe to perform a variety of operations without manual intervention.
- Automatic Tool Changing: The turret automatically rotates to bring the required tool into position, streamlining the machining process.
- Tool Offset: Each tool in the turret has a specific offset that tells the CNC system where the tool tip is, ensuring precise movements during operations.
Learn more about our 2.2KW ER16 Air-Cooled Spindle to further enhance the capabilities of your CNC machines.
The Types of CNC Lathes
1. 2-Axis CNC Lathes
2-axis CNC lathes are the most basic type of CNC lathes, operating on two axes: X and Z. These machines are suitable for straightforward turning operations where the main goal is to create cylindrical parts, such as shafts or bolts.
- X Axis: Controls the radial movement of the tool, determining the diameter of the workpiece.
- Z Axis: Controls the longitudinal movement of the tool, determining the length of the workpiece.
2-axis CNC lathes are excellent for beginners or for production lines that need to produce simple parts consistently.
2. 3-Axis CNC Lathes
3-axis CNC lathes add an additional Y axis to the mix, enabling more complex operations. The extra axis allows the machine to perform off-center machining, which is useful for parts that require slots, grooves, or drilling at different angles.
- Enhanced Capabilities: With the Y axis, a 3-axis CNC lathe can perform milling-like operations, making it a versatile choice for more complex projects.
- Applications: Commonly used in industries like aerospace and automotive where complex, high-precision parts are needed.
Discover our 3.5KW ER25 Air-Cooled Spindle for achieving superior performance in demanding CNC applications.
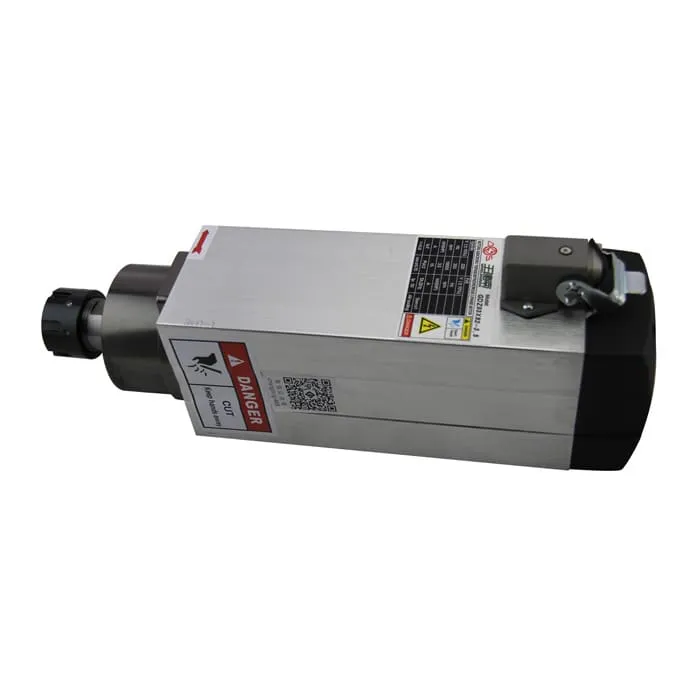
How Does a CNC Lathe Work?
1. Programming and G-Codes
A CNC lathe uses a specific set of codes called G-codes and M-codes to operate. These codes tell the machine how to move, at what speed, and when to change tools. The G-code primarily controls movement, while the M-code manages auxiliary functions like turning on the spindle or coolant.
- G00: Rapid movement of the tool without cutting.
- G01: Controlled movement used during the cutting process.
- M03: Spindle on in a clockwise direction.
Programming a CNC lathe requires a solid understanding of these codes and their application. Most modern CNC lathes also support CAM software, which can generate G-code automatically from a CAD drawing.
2. The Machining Process
Once the program is ready, the machining process begins by loading the workpiece onto the lathe, usually held in place by a chuck. The CNC system then controls the rotation of the workpiece and the movement of the cutting tool, which removes material until the desired shape is achieved.
- Turning: The most common operation, which involves rotating the workpiece while the tool moves along the X and Z axes to cut away material.
- Facing: This involves moving the cutting tool across the face of the workpiece to create a flat surface.
- Drilling: Drills can also be mounted on a CNC lathe to create holes along the axis of the workpiece.
Find our high-quality CNC Router Spindles for optimized lathe and router operations.
Advantages of Using CNC Lathes
1. Precision and Consistency
One of the most significant advantages of using CNC lathes is their precision and consistency. Unlike manual machining, where there is a risk of human error, CNC lathes operate based on pre-programmed instructions, ensuring every part produced is identical to the last.
- Repeatability: CNC lathes can perform the same operation multiple times with high precision, which is ideal for mass production.
- Complex Shapes: The ability to precisely control the movement of the tool allows for the creation of intricate shapes that would be difficult or impossible to achieve manually.
2. Increased Production Speed
CNC lathes also increase production speed by automating the process and minimizing downtime between operations. Since CNC lathes can automatically switch between tools and continuously run, they can complete jobs faster than manual lathes.
- Less Manual Intervention: Once the machine is programmed and set up, it requires minimal manual intervention, freeing up machinists to work on other tasks.
- Quick Changeovers: CNC lathes can be reprogrammed quickly, allowing manufacturers to switch from producing one part to another with minimal setup time.
Learn about our Spindles for CNC Routers to further enhance the efficiency of your production process.
Common Applications of CNC Lathes
1. Automotive Industry
In the automotive industry, CNC lathes are used to produce a variety of parts, such as shafts, gears, and bushings. The high precision of CNC lathes is crucial in ensuring these parts meet the stringent quality requirements of automotive manufacturers.
- Engine Components: Parts such as crankshafts and camshafts are commonly machined using CNC lathes.
- Suspension Components: CNC lathes are also used to create components that make up the suspension system, which needs to be both strong and precisely manufactured.
2. Aerospace Industry
The aerospace industry requires parts that are lightweight, strong, and manufactured to extremely tight tolerances. CNC lathes are ideal for this kind of work, as they can achieve the precision needed for aerospace components.
- Landing Gear Parts: CNC lathes are used to create many of the cylindrical components that make up the aircraft’s landing gear.
- Engine Parts: Many parts of the aircraft’s engine, including turbines and shafts, are manufactured using CNC lathe technology.
Conclusion: The Meaning and Importance of CNC Lathes
So, what does CNC lathe stand for? It stands for Computer Numerical Control lathe, a machine tool that has revolutionized the world of manufacturing by combining the age-old lathe with the power of computer control. CNC lathes are capable of producing complex parts with high precision, repeatability, and efficiency, making them an indispensable tool in industries like automotive, aerospace, and general manufacturing. Whether you are a hobbyist or run a full-scale production shop, understanding the role of CNC lathes is key to taking advantage of the latest advancements in machining technology.
To boost your machining capabilities, check out our CNC spindle motors for enhanced performance, precision, and productivity.
FAQs
1. What does CNC lathe mean?
A CNC lathe is a machine tool controlled by a computer, used to perform various operations like turning, facing, and drilling on materials like metal, wood, and plastic.
2. How does a CNC lathe differ from a manual lathe?
A CNC lathe is controlled by programmed instructions, allowing for automation and precision, while a manual lathe requires hands-on operation by a machinist.
3. What industries use CNC lathes?
CNC lathes are used across many industries, including automotive, aerospace, medical, and general manufacturing for producing precise and complex parts.
4. What are the different types of CNC lathes?
The main types of CNC lathes include 2-axis lathes for basic operations, 3-axis lathes for more complex parts, and multi-axis lathes that offer advanced machining capabilities.
5. What are the advantages of using a CNC lathe?
The main advantages of CNC lathes include increased precision, repeatability, and production speed, as well as reduced manual intervention, making them ideal for high-volume production.