What is a CNC Lathe Used For?
What is a CNC Lathe used for? This is a common question for anyone new to the world of CNC machining. CNC Lathes are powerful tools that play an essential role in manufacturing, allowing precise cutting, shaping, and drilling of materials like metals, wood, and plastics. The versatility of CNC lathe machines has made them indispensable in industries ranging from automotive to aerospace and even artistic woodworking. This article will provide a comprehensive overview of the different uses, capabilities, and types of CNC lathes, while also exploring how these incredible machines have transformed modern manufacturing.
Understanding CNC Lathes
1. What is a CNC Lathe?
A CNC Lathe is a machine that is operated using Computer Numerical Control (CNC) to automate the cutting and shaping of materials. Unlike manual lathes, CNC lathes use a computer program to move the tool and workpiece with incredible precision, thereby allowing the production of complex parts with high accuracy.
- Components: A typical CNC lathe consists of a spindle, tool turret, chuck, and bed.
- Automation: With CNC lathes, manufacturers can achieve high levels of repeatability, making them ideal for large production runs.
Check out our selection of CNC Spindles to see how these components contribute to the efficiency of CNC lathes.
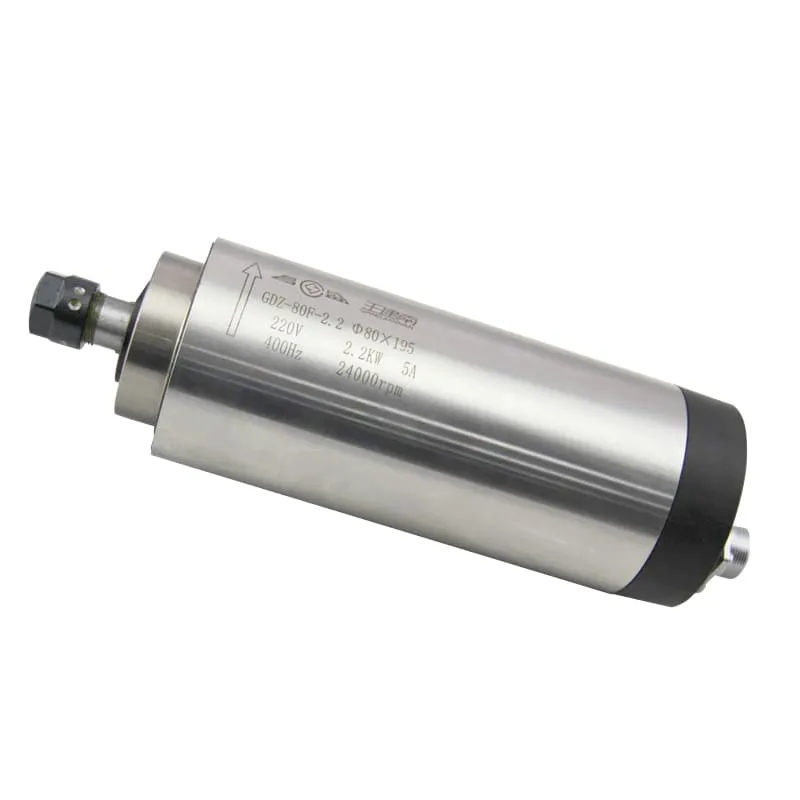
2. The Role of a CNC Lathe in Manufacturing
CNC lathes play a significant role in modern manufacturing by producing parts with high precision and consistency. These machines are essential in industries that require complex components with tight tolerances, such as the automotive, aerospace, and medical sectors.
- Automotive Industry: CNC lathes are used to produce components like engine parts, gear shafts, and steering columns.
- Aerospace Industry: Precision is key, and CNC lathes are used for manufacturing turbine components and aircraft parts.
- Medical Devices: CNC lathes produce medical instruments and implants, which require high accuracy and a smooth finish.
Explore our 1.5KW ER11 Square Air-Cooled Spindle with Flange to see how it can enhance the performance of CNC lathes in such demanding applications.
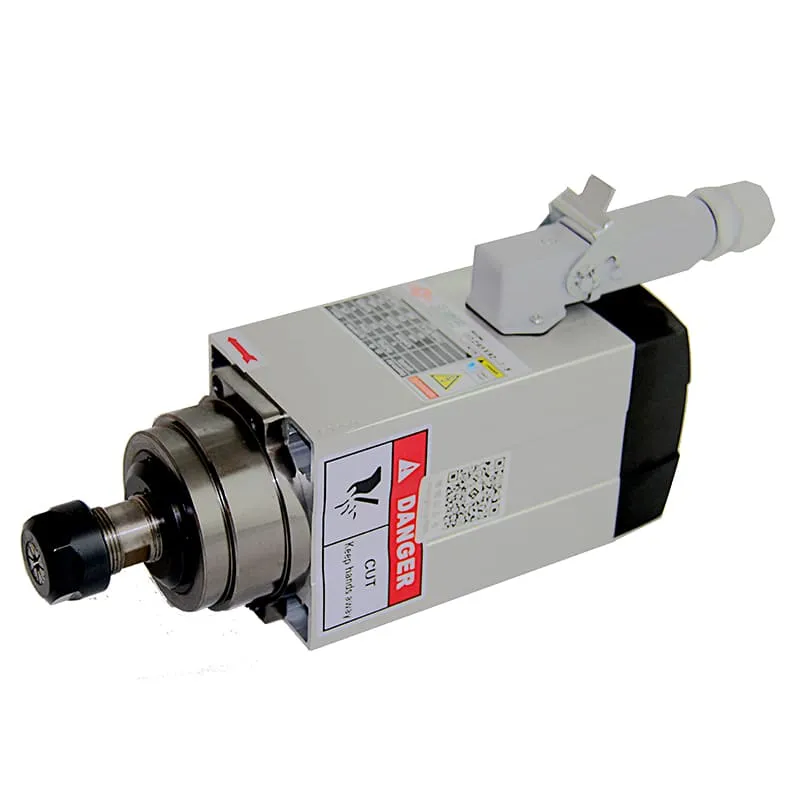
Types of CNC Lathes and Their Uses
1. Horizontal vs Vertical CNC Lathes
Horizontal CNC Lathes and Vertical CNC Lathes are the two most common types used in industry. Each type has its distinct advantages and ideal use cases.
- Horizontal CNC Lathes: The spindle is oriented horizontally, making these lathes ideal for long parts like shafts. Horizontal lathes are commonly used for turning, drilling, and boring operations.
- Vertical CNC Lathes: The workpiece is clamped and rotates on a vertical axis, which makes these lathes excellent for heavy and larger diameter workpieces.
Learn about different CNC Router Spindles that can be used with various CNC lathes.
2. 2-Axis vs Multi-Axis CNC Lathes
2-axis CNC Lathes are the most basic type and involve just the X and Z axes. However, there are more advanced lathes that use multiple axes for increased flexibility.
- 2-Axis CNC Lathes: These are suitable for simple turning tasks where the tool moves in two directions – horizontally and vertically.
- 3-Axis and Multi-Axis CNC Lathes: Allow more complex machining by adding an additional axis of movement, typically a Y-axis, and sometimes a rotary axis for added flexibility.
These multi-axis lathes are capable of producing very complex shapes, often in a single setup, which greatly enhances productivity and precision.
Consider using our 2.2KW ER16 Air-Cooled Spindle for multi-axis operations requiring consistent power and stability.
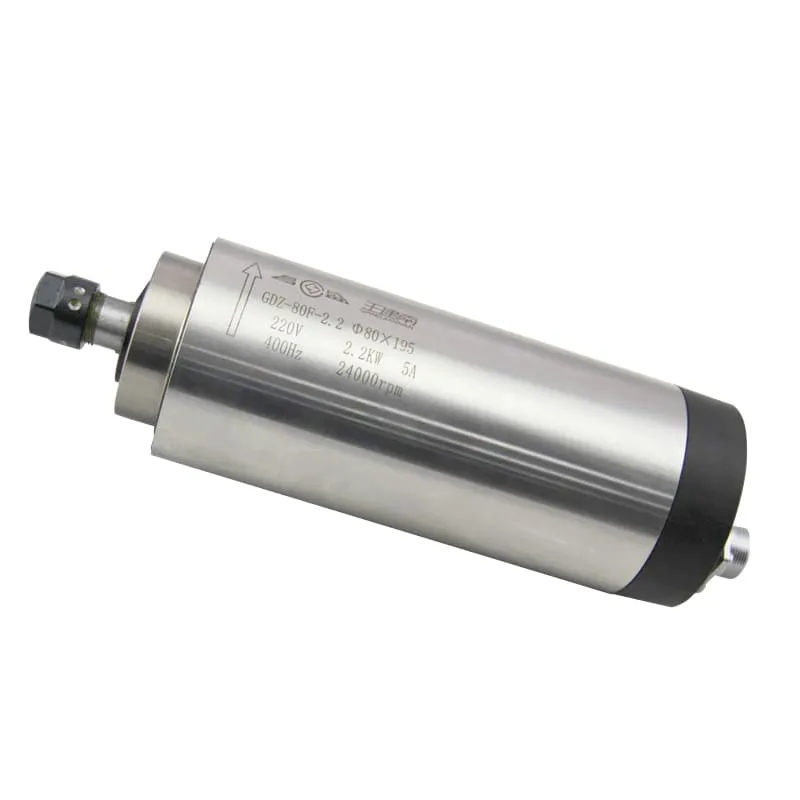
Key Operations Performed by CNC Lathes
1. Turning Operations
The primary function of a CNC lathe is turning, where a cutting tool is brought into contact with a rotating workpiece. This operation is used to remove material to achieve the desired shape and size.
- Rough Turning: Used to remove large amounts of material quickly.
- Finish Turning: A finer operation that ensures the workpiece has a smooth finish and accurate dimensions.
2. Drilling and Boring
CNC lathes can also perform drilling and boring operations, which involve making holes into the rotating workpiece.
- Drilling: The tool is fed into the workpiece to create holes of varying diameters.
- Boring: A boring bar is used to enlarge pre-drilled holes to achieve a more precise diameter.
Explore our 3.5KW ER25 Air-Cooled Spindle that can handle the torque requirements for such demanding operations.
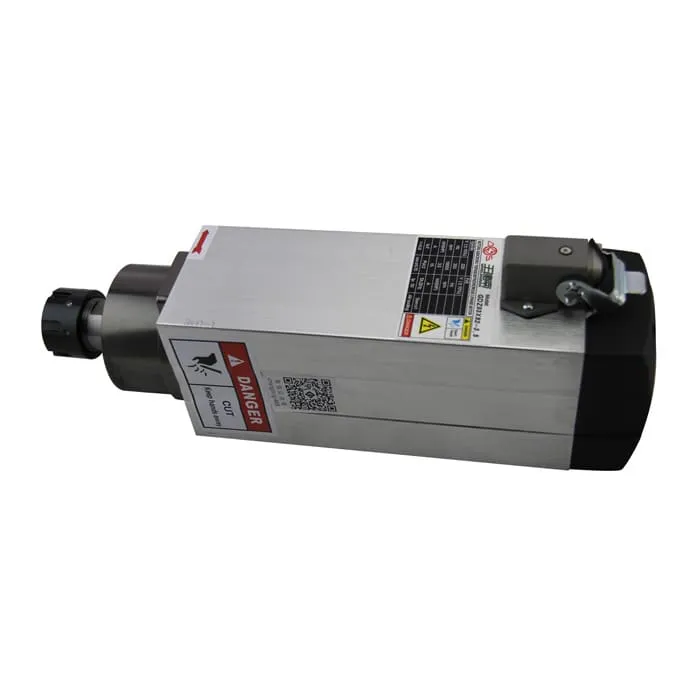
Advantages of Using CNC Lathes
1. Precision and Accuracy
One of the primary advantages of CNC lathes is their ability to produce parts with incredible precision and accuracy. This precision comes from the computer-controlled nature of CNC, which ensures that each cut, drill, and move is performed exactly as programmed.
- Reduced Human Error: Automation removes inconsistencies that arise from manual operations.
- Repeatability: CNC lathes can produce hundreds or even thousands of identical parts, with almost no deviation between them.
2. Increased Production Speed
The automated nature of CNC lathes significantly reduces the time required for production. Complex parts that may take hours to produce manually can be completed in minutes.
- High-Speed Machining: With the help of high-speed spindles, CNC lathes can achieve faster cutting speeds without compromising accuracy.
- Efficiency: The set-and-forget capability of CNC allows operators to focus on other tasks while the machine works, enhancing overall productivity.
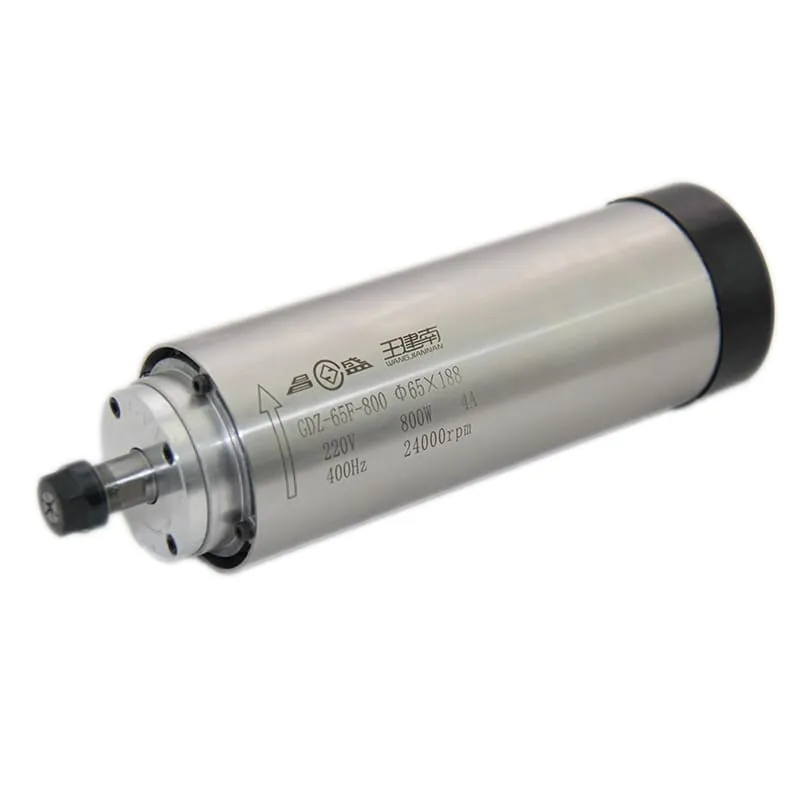
Discover the 800W ER11 Air-Cooled Spindle for high-precision operations where speed and reliability are key.
Materials Processed Using CNC Lathes
1. Metals
CNC lathes are commonly used to cut and shape a wide variety of metals, including steel, aluminum, copper, and titanium. These metals are used in everything from automobile engines to aircraft components.
- Stainless Steel: Widely used for parts that need strength and corrosion resistance.
- Aluminum: Lightweight and often used in aerospace and automotive applications.
2. Plastics and Other Materials
In addition to metals, CNC lathes can process plastics and composite materials. These materials are often used for specialized applications where weight or flexibility is a factor.
- ABS Plastic: Used for lightweight components and prototypes.
- Composites: Such as carbon fiber, often used in aerospace for lightweight but strong parts.
Check out our CNC Router Spindles for processing a range of materials with precision.
Tips for Operating CNC Lathes Effectively
1. Regular Maintenance
Proper maintenance is crucial to ensure that a CNC lathe functions optimally. This includes regular cleaning, lubrication, and inspection of key components like the spindle and tool turret.
- Lubrication: Ensure all moving parts are properly lubricated to minimize wear.
- Tool Inspection: Regularly check cutting tools for wear and replace them as necessary to maintain precision.
2. Proper Programming
The accuracy of a CNC lathe depends significantly on the G-code that drives it. Incorrect code can lead to errors in the machining process, leading to wastage of material.
Consider using the 24000RPM 0.8KW ER11 Water-Cooled Spindle to help maintain high precision during CNC operations.
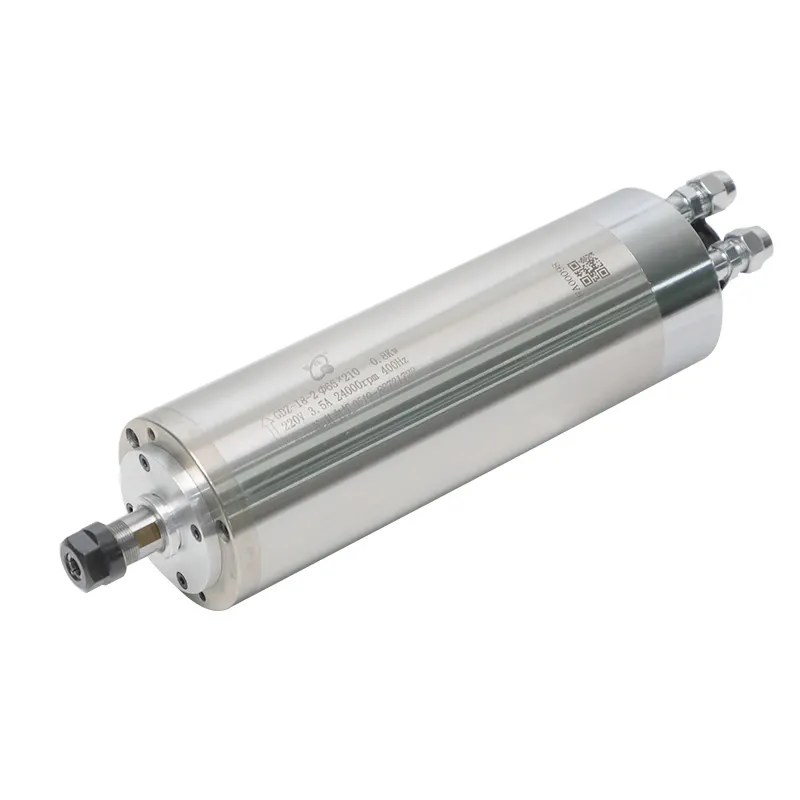