What is a CNC System?
CNC System, or Computer Numerical Control, is a powerful tool used in modern manufacturing that revolutionizes the way machine tools are operated. By integrating computer-aided programming with advanced machine controls, a CNC system enables precise, automated production of complex parts across multiple industries. From aerospace to automotive to consumer electronics, CNC technology has become an essential part of the production process, ensuring high quality and efficiency. In this article, we will explore what a CNC system is, how it works, and the benefits it provides to manufacturers and end-users alike.
Understanding CNC Systems: How They Work
A CNC system is an automated control system for machine tools such as lathes, mills, routers, and grinders. These machines follow programmed instructions, known as G-code, to precisely control the movement of tools. Unlike traditional manually operated machine tools, CNC systems provide a high degree of accuracy and repeatability, which is especially important in industries where precision is critical.
Key Components of a CNC System
- Machine Control Unit (MCU): The MCU is the brain of the CNC system. It processes the G-code, manages the tool paths, and sends commands to the machine tool’s motors.
- CNC Software: The software is used to generate the G-code that dictates the movements of the machine. Programs like CAM (Computer-Aided Manufacturing) help design and translate part geometries into precise cutting instructions.
- Cutting Tools: Various cutting tools, such as end mills and drills, are used to remove material from the workpiece, shaping it into the desired form.
The CNC system communicates with the hardware of the machine to control tool movement along the X, Y, and Z axes. By using CAD designs, the system follows a set of instructions to produce parts with extreme accuracy.
For effective CNC machining, using a suitable spindle motor is crucial. Explore our CNC Spindle Motors for reliable and powerful performance.
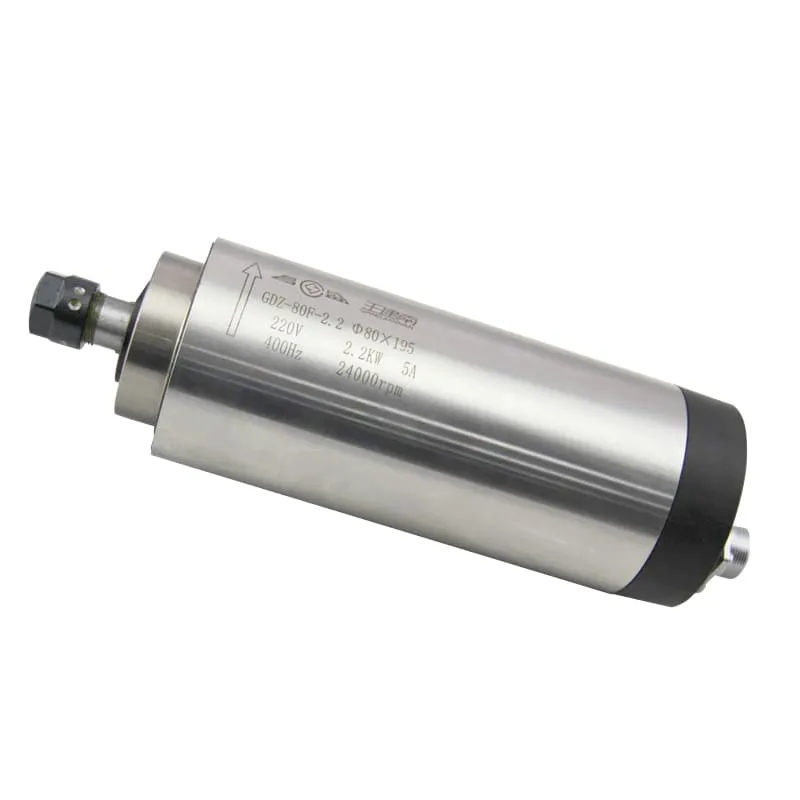
The Evolution of CNC Technology
CNC technology has a rich history, evolving from early numerical control (NC) systems in the 1940s to modern, sophisticated CNC systems. This evolution has involved numerous advances in electronics, computing, and software, all of which have contributed to the incredible accuracy and automation of modern CNC systems.
A Brief History of CNC
- 1940s: The concept of numerical control emerged, driven by the need for precision in aerospace manufacturing. Machines were controlled using punch cards to define tool movements.
- 1950s-1960s: Development of G-code and early numerical control systems began, which allowed machines to follow specific commands.
- 1970s-1980s: The introduction of computers led to Computer Numerical Control, enabling easier programming and more complex operations.
- Modern Day: CNC technology now integrates with CAD/CAM software, creating seamless workflows from design to manufacturing.
The advancements in CNC technology have led to greater automation, efficiency, and complexity, allowing manufacturers to produce parts that were once thought impossible.
Different Types of CNC Machines
There are many different types of CNC machines, each designed for specific tasks and materials. Below are some of the most common types:
1. CNC Milling Machines
CNC milling machines are used to cut and shape materials along multiple axes. They typically use rotating cutting tools to remove material from a workpiece. The versatility of CNC mills makes them suitable for producing a wide variety of parts, from simple plates to complex aerospace components.
- Axes Movement: 3-axis, 4-axis, and 5-axis CNC milling machines allow for more complex cuts, increasing the possibilities for part production.
- Applications: Suitable for aerospace, automotive, and tooling industries.
To enhance the performance of your CNC milling machine, check out our 1.5KW ER11 Round Air-Cooled Spindle.
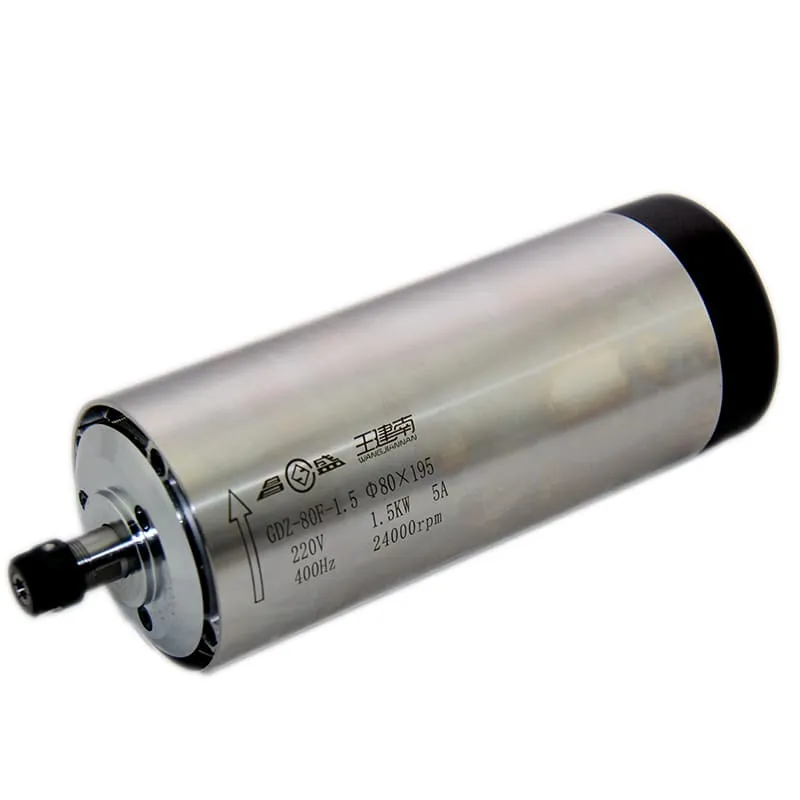
2. CNC Lathes
CNC lathes are used to produce parts with rotational symmetry, such as shafts, cylinders, and bolts. The workpiece rotates while the cutting tool remains stationary, shaping the material through various operations like turning, facing, and threading.
- Axis Control: Typically operate on 2 to 4 axes.
- Applications: Widely used in the automotive, medical, and consumer electronics industries.
3. CNC Plasma Cutting Machines
CNC plasma cutting machines use a high-velocity jet of plasma to cut through electrically conductive materials, such as steel, aluminum, and copper. These machines are ideal for sheet metal fabrication and cutting intricate designs with speed and precision.
- Materials: Can cut a variety of metals.
- Applications: Used in metal fabrication and sign-making industries.
For plasma cutting operations, consider our high-performance 2.2KW ER20 Air-Cooled Spindle.
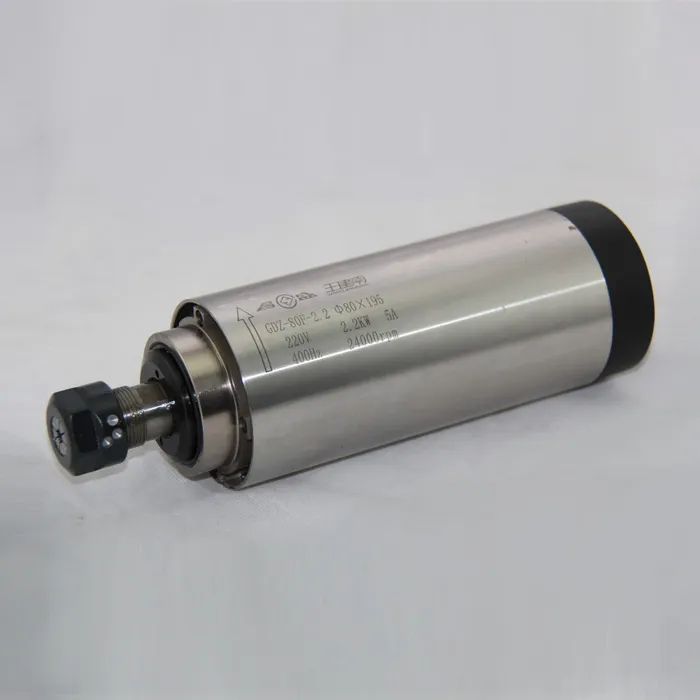
Components of a CNC Machine
A typical CNC machine comprises several components that work in tandem to produce precision parts. Here are the main components and their functions:
1. Machine Bed
The machine bed forms the foundation of the CNC machine, providing structural support for all other components. It is usually made from cast iron or a similar sturdy material to ensure stability during operation.
2. Spindle Motor
The spindle motor is a critical component responsible for rotating the cutting tool. The power and speed of the spindle motor determine the type of materials the machine can effectively cut and how fine the finish will be.
For a range of spindle options for your CNC machine, explore our Spindles for CNC Router.
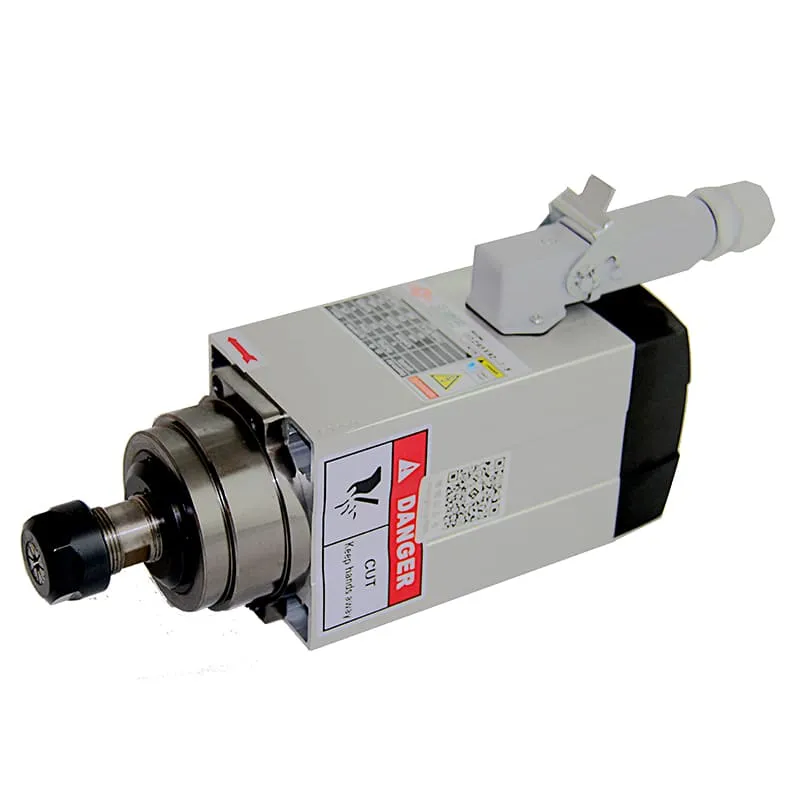
3. Machine Control Unit (MCU)
The MCU processes the G-code and converts it into electrical signals, which control the motors and other moving parts of the CNC machine. The MCU is essentially the control hub of the entire system.
4. Worktable
The worktable holds the workpiece in place during machining. It can be moved in multiple directions to ensure the cutting tool can reach all areas of the part. Some CNC machines use a vacuum zone to secure lighter materials during cutting.
Advantages of Using CNC Systems
1. High Precision and Accuracy
CNC systems offer an unparalleled level of precision, allowing manufacturers to create parts with extremely tight tolerances. This is particularly beneficial in industries where small discrepancies can result in performance issues or safety risks, such as in aerospace or medical device manufacturing.
- Consistent Quality: CNC systems can produce hundreds or thousands of parts with consistent accuracy.
- Reduced Human Error: The automation reduces the likelihood of mistakes that can occur with manual machining.
2. Efficiency and Automation
CNC systems automate the production process, meaning fewer operators are needed, and machines can run 24/7 without fatigue.
- Lower Labor Costs: Because CNC systems can run unattended, labor costs are reduced significantly.
- Higher Production Rates: CNC machines are capable of rapid movements and fast processing speeds, increasing overall production rates.
For high-quality production efficiency, consider our 3.5KW ER25 Air-Cooled Spindle.
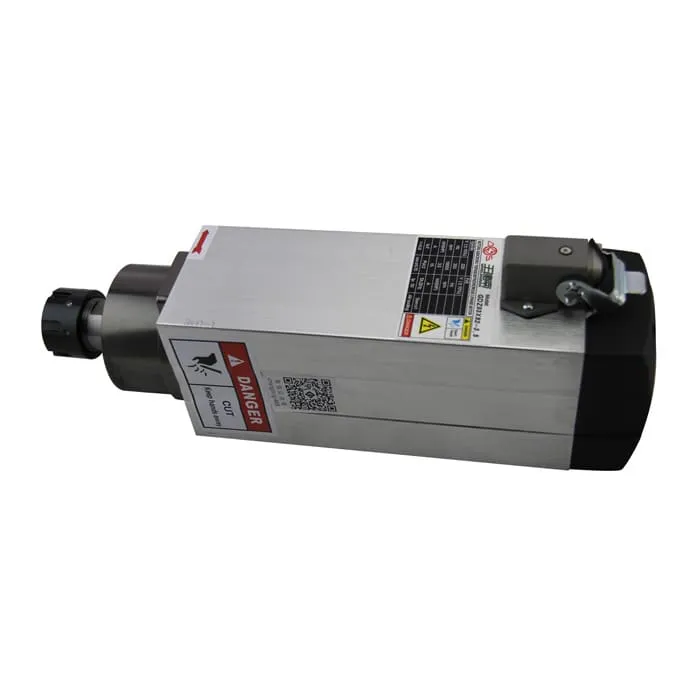
CNC Software and Programming
The software used in CNC systems is responsible for converting CAD designs into the G-code that controls the machine. There are various software programs, each offering different features for specific tasks.
1. CAD/CAM Software
- CAD (Computer-Aided Design): CAD software is used to design the parts. Popular programs include SolidWorks, AutoCAD, and Fusion 360.
- CAM (Computer-Aided Manufacturing): CAM software converts CAD models into G-code, providing the tool paths that the CNC system will follow.
2. G-Code Programming
G-code is the language that CNC machines understand. It provides the specific commands for tool movement, speed, feed rate, and other essential functions. Learning G-code can help operators troubleshoot issues and make adjustments directly in the code.
For a smoother operation, having a reliable spindle is key. Visit our CNC Spindle Motor collection for high-quality options.
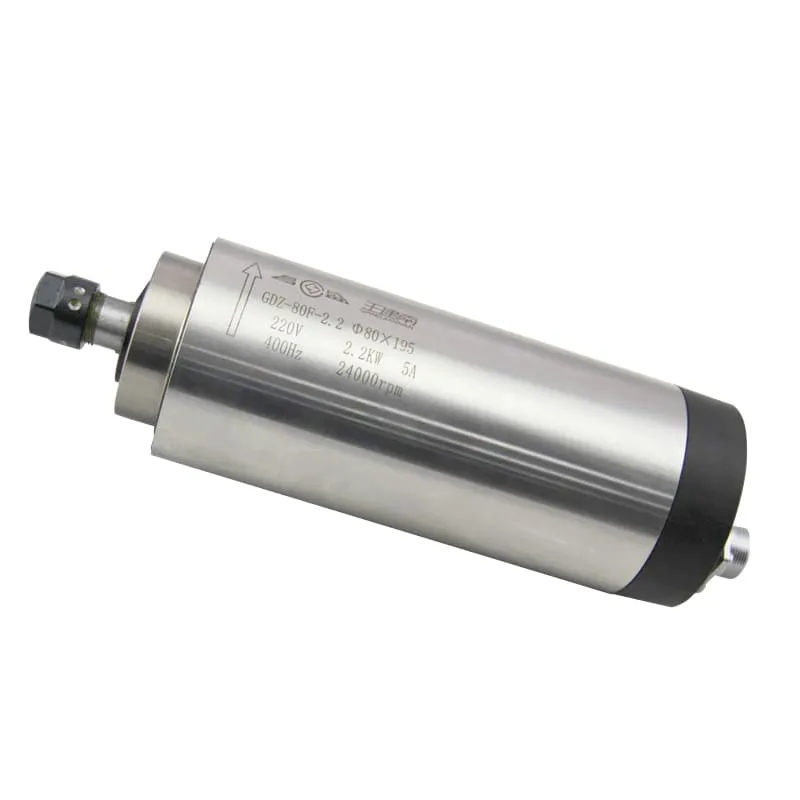
FAQs About CNC Systems
1. What are the main advantages of using a CNC system?
CNC systems provide high precision, consistent quality, and increased production efficiency. They reduce the need for manual intervention and minimize the potential for human errors.
2. What types of materials can be machined with CNC systems?
CNC systems can machine a wide range of materials, including metals (aluminum, steel, titanium), plastics, wood, and composites. The type of material often depends on the application and the capabilities of the CNC machine.
3. How is CNC programming done?
CNC programming is done using CAD/CAM software to design the part and generate G-code, which provides detailed instructions for the CNC machine to follow.
4. What industries use CNC technology?
Industries such as aerospace, automotive, healthcare, electronics, and metal fabrication use CNC technology due to its ability to create complex, high-precision parts consistently.
Conclusion: The Future of CNC Systems in Manufacturing
CNC systems have revolutionized the manufacturing industry by providing precise, automated solutions for producing complex parts. From the first numerical control systems to today’s sophisticated CNC machines, the technology has evolved significantly, allowing for increased production efficiency, accuracy, and automation. Whether you’re looking to produce detailed aerospace components or manufacture custom products on a large scale, CNC systems offer the flexibility and reliability needed to meet today’s demanding manufacturing standards.
To further enhance your CNC experience, make sure to use the right spindle for your needs. Visit our CNC Spindle Motor page to find the ideal spindle for your machine.
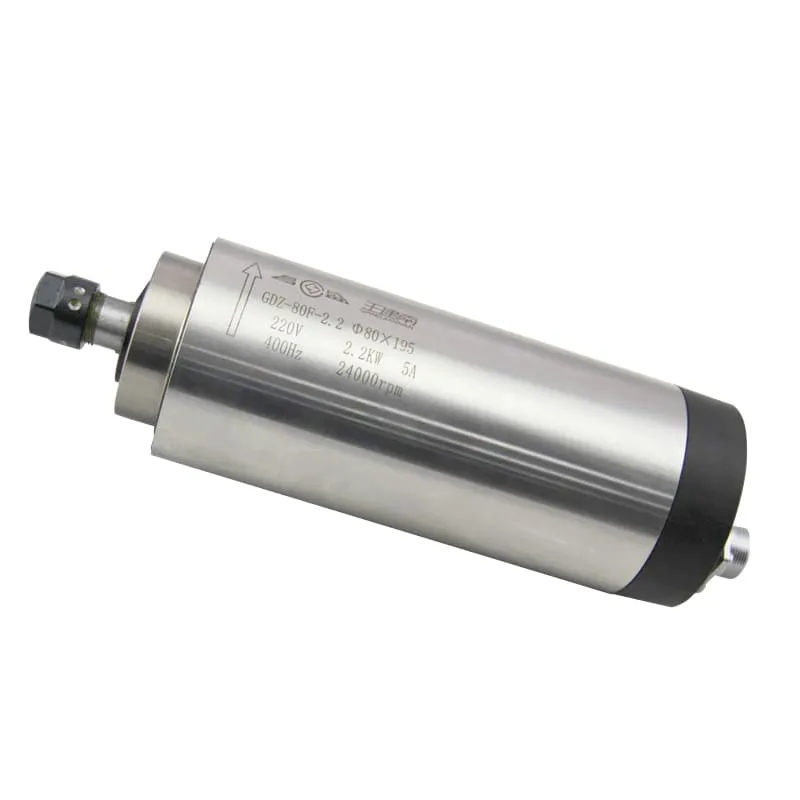
With continued advancements in CNC technology, the potential for automation, precision, and high-quality production will only continue to grow. Now is the perfect time to leverage CNC systems to meet and exceed manufacturing needs while staying ahead in a competitive industry.