Understanding Rotary Tool Milling Spindle in CNC Turn-Mill
The CNC (Computer Numerical Control) industry has rapidly evolved, giving manufacturers innovative solutions for more efficient machining. A central component of this evolution is the rotary tool milling spindle in CNC turn-mill machines. This article will provide an in-depth look at what a rotary tool milling spindle is, how it functions, and why it plays a crucial role in CNC turn-mill operations. If you’re a manufacturer or an enthusiast curious about the intricacies of CNC spindles, this article is a must-read.
The rotary tool milling spindle in CNC turn-mill centers allows for versatile machining operations, providing a balance between speed, precision, and efficiency. With this guide, you’ll understand the features that make it an indispensable part of modern CNC systems.
Definition and Basics of Rotary Tool Milling Spindle
A rotary tool milling spindle in CNC turn-mill operations is essentially the workhorse that drives the cutting tool. It holds and rotates the cutting tool, enabling it to machine parts by removing material with extreme precision. Spindles come in various designs and can be powered by different mechanisms, such as cnc spindle motors and multi spindle CNC machines.
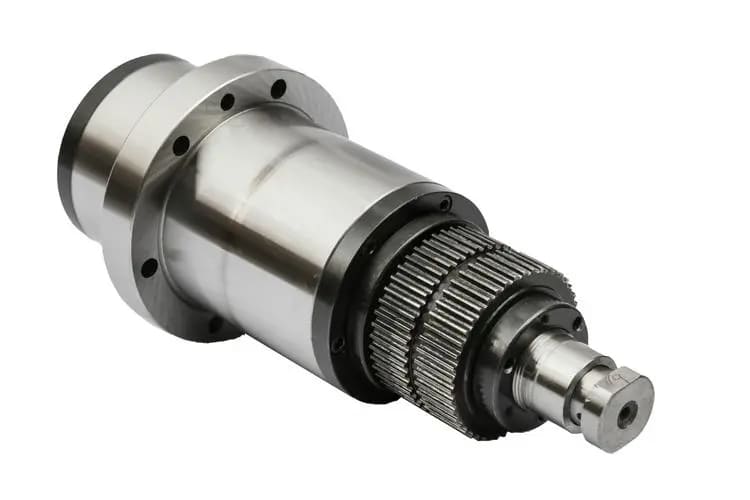
How Does a Rotary Tool Milling Spindle Work?
The rotary spindle is driven by an electric motor that allows it to reach high speeds, typically ranging from several hundred to thousands of revolutions per minute (RPM). Whether belt-driven or gear-driven, these spindles can rotate in both directions, providing a versatile range of motion essential for turn-mill operations. In CNC turn-mill machines, a single setup handles both turning and milling, and the spindle is a critical component that bridges these two processes.
The Role of Rotary Tool Milling Spindle in CNC Turn-Mill Operations
The rotary tool milling spindle is the core component that allows a turn-mill machine to perform its dual functions. It facilitates operations like turning, drilling, and milling—all within one setup, thereby increasing efficiency and reducing the need for multiple machine tools.
Why is the Spindle So Important?
The spindle ensures that machining tasks are executed with high precision. By maintaining consistent speed and torque, the spindle ensures optimal cutting conditions. This is particularly crucial when working with tough materials like steel, where the cnc spindle motor needs to sustain high torque for extended periods. In short, the spindle is the key to achieving flexibility and precision in machining.
The Basics of Turn-Milling
Turn-milling is a hybrid process that combines turning and milling operations within one machine tool. The spindle cnc plays an integral role in making this possible. Unlike traditional CNC machines where a single process is carried out at a time, turn-milling allows for multiple cutting processes, improving efficiency and reducing overall production time.
Why Combine Turning and Milling?
Combining these processes enables manufacturers to perform complex tasks in a single machine setup. The rotary tool milling spindle allows the machine to rotate the cutting tool at high speeds for milling while the workpiece rotates for turning. This synergy significantly enhances productivity and reduces the risk of misalignment or human error between setups.
Evolution of CNC Technology
The evolution of CNC technology has allowed machines to become smarter, faster, and more efficient. The cnc router spindle motor has also undergone significant advancements, making them capable of handling more challenging tasks with greater precision.
The Impact of Technology on CNC Spindles
With the advancement of CNC spindle technology, machines today can perform intricate milling tasks with high repeatability. Innovations such as high-speed electric spindles and cooling systems have improved spindle longevity, ensuring that machines can operate at peak performance without overheating or frequent maintenance.
Types of Rotary Tool Milling Spindles
Not all rotary tool milling spindles are created equal. Depending on the application, the spindle design may vary. Understanding the different types is crucial for selecting the right spindle for your turn-mill operations.
High-Speed Electric Spindles
These spindles are ideal for precision work that requires high RPMs. They are driven by electric motors and can handle high-speed applications like micro-milling.
Gear-Driven Spindles
Gear-driven spindles offer higher torque, making them suitable for heavy-duty applications. They can withstand larger cutting forces, which makes them perfect for machining tougher materials.
Belt-Driven Spindles
If you’re looking for a cost-effective solution, belt-driven spindles are a popular choice. These spindles rely on a belt system to transfer power from the motor to the cutting tool, offering a balance between power and affordability.
Key Features and Advantages
When choosing a rotary tool milling spindle for a CNC turn-mill machine, it’s important to consider the key features that will impact performance.
Power and Torque
The spindle’s power and torque directly affect the material removal rate and cutting speed. For demanding applications, you’ll need a spindle with higher torque.
Spindle Speed Range
The spindle’s speed range is also critical for achieving the desired surface finish. Lower speeds are needed for tough materials, while higher speeds are ideal for finishing operations on softer materials.
Cooling Systems
Spindles generate heat, especially when running at high speeds. Integrated cooling systems can extend the life of the spindle and ensure consistent performance by maintaining an optimal temperature during operation.
Precision and Flexibility
In modern manufacturing, precision and flexibility are essential. The rotary tool milling spindle provides both by allowing the CNC machine to adapt to various machining tasks, whether it’s high-speed milling or heavy-duty turning.
How Does Precision Affect Quality?
Precision is critical when machining intricate components. A high-quality spindle for CNC ensures that every movement is executed as planned, leading to parts with exact tolerances. Flexibility in spindle performance allows for quick changes between operations, optimizing production times and enhancing output quality.
Speed and Efficiency in Production
One of the main benefits of using a rotary tool milling spindle in CNC turn-mill machines is the ability to produce parts faster and with greater accuracy. As manufacturers move towards more automated solutions, the spindle’s role becomes even more important.
Reducing Production Time
The efficiency of a multi-spindle CNC machine can dramatically reduce production time. By performing multiple machining operations in one setup, these machines eliminate the need for tool changes or multiple workstations, speeding up production and lowering labor costs.
Enhancing Turn-Mill Capabilities
Turn-mill machines equipped with high-quality spindles can perform a wide range of tasks, from drilling and cutting to threading and tapping, all within one setup. This enhances the machine’s overall capabilities and opens up opportunities for more complex part production.
Rotary Tool Milling Spindle vs. Fixed Spindle
While rotary tool milling spindles offer flexibility, fixed spindles provide stability for simpler tasks. Choosing between the two depends on the complexity and precision required for the job.
Considerations for Selecting the Right Spindle
When selecting the right spindle for your CNC machine, several factors should be considered, including speed, torque, and application requirements.
Matching the Spindle to the Application
Different spindles serve different purposes. For high-precision tasks, a high-speed electric spindle might be more suitable. For heavy-duty machining, a gear-driven spindle may provide better results. Understanding the specific needs of your application will help you make the best choice.
Routine Maintenance Tips to Ensure Performance
Proper maintenance is essential to keep the spindle running at optimal performance. Here are a few tips for spindle maintenance:
- Regular Inspection: Check for any signs of wear, such as unusual noise or heat buildup.
- Lubrication: Ensure the spindle bearings are properly lubricated to reduce friction and wear.
- Cooling: Always monitor the spindle’s cooling system to prevent overheating.
By adhering to these maintenance practices, you can extend the life of your CNC router spindle and avoid costly downtime.
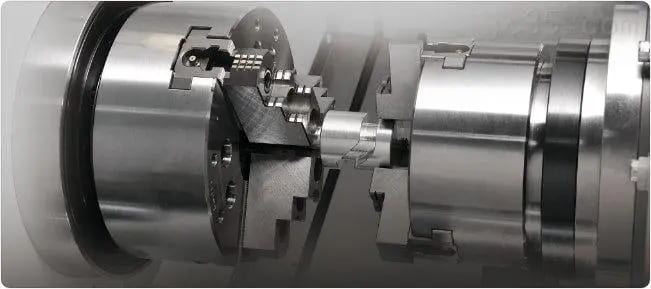
Frequently Asked Questions
- What determines the choice between a router and a spindle in CNC?
The choice depends on the application. Routers are typically used for lighter tasks, while spindles offer more power and precision for heavy-duty machining. - How does spindle speed affect machining quality?
Spindle speed directly impacts surface finish and material removal rates. Higher speeds lead to smoother finishes, while lower speeds are used for tougher materials. - Can I upgrade my CNC machine with a more powerful spindle?
Yes, many CNC machines can be upgraded with more powerful spindles to improve performance and extend their capabilities. - What are the signs that a CNC spindle needs maintenance or replacement?
Common signs include excessive noise, vibration, inconsistent speed, and poor surface finishes on machined parts. - How does the spindle affect overall CNC machining efficiency?
The spindle plays a crucial role in determining how efficiently a CNC machine operates. A high-performance spindle reduces machining time and improves accuracy, leading to increased productivity.
Key Takeaways
- Rotary tool milling spindles are critical components of CNC turn-mill operations.
- High-quality spindles enhance machining precision, flexibility, and efficiency.
- Understanding spindle types and features ensures better application and machine performance.
- Regular maintenance of the spindle is essential for ensuring longevity and consistent operation.
- Advances in CNC spindle technology continue to revolutionize machining capabilities.
By leveraging the power and precision of the rotary tool milling spindle, manufacturers can streamline their production processes, ensuring high-quality output and reducing overall costs.
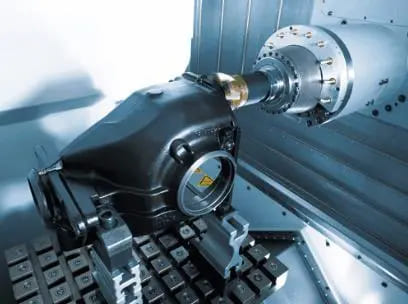
- RicoCNC has a team of professionals who have been engaged in the design, production, sales, and maintenance of electro spindles for many years. Our company accepts the purchase of various types of CNC spindles.
water-cooled CNC spindle motors
Edge banding machine spindle motors.
- If you need any CNC spindle, please contact us.