What Is Spindle Load in CNC Machines?
CNC machines are known for their precision and efficiency, but one key factor that can make or break their performance is spindle load. Have you ever wondered what exactly spindle load is and why it’s important? Understanding spindle load is essential for maintaining the efficiency and lifespan of your CNC machine. In this article, we’ll explore the intricacies of spindle load, its impact on machining performance, and how you can optimize it for better productivity.
Why Is This Article Worth Reading?
Spindle load directly affects everything from the quality of your workpieces to the lifespan of your cutting tools. By understanding the fundamentals of spindle load, you’ll be better equipped to manage and troubleshoot common issues, boost efficiency, and even extend the life of your CNC machine. This article will guide you through key factors, including how to measure spindle load, interpret the data, and make informed decisions to optimize your machining processes.
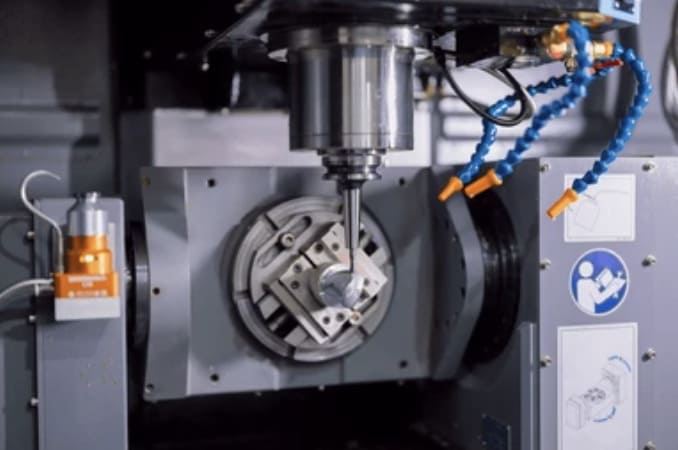
Definition and Importance of Spindle Load
What Is Spindle Load?
Spindle load refers to the amount of force exerted on the spindle during a machining operation. It’s a crucial indicator of how hard the spindle is working, and it is typically measured in percentage relative to the machine’s full power capacity.
Why Is Spindle Load Important?
Spindle load is vital because it reflects the efficiency of a CNC machine’s operation. An overloaded spindle can lead to premature tool wear, poor surface finishes, and even machine damage. Conversely, optimizing spindle load ensures that the machine operates within its limits, enhancing product quality and machining precision.
How Spindle Load Affects CNC Machine Performance
Can Spindle Load Impact the Efficiency of CNC Operations?
Yes, spindle load plays a direct role in the efficiency of CNC machines. An overloaded spindle can cause excessive vibrations, leading to inaccuracies in the workpiece. Conversely, an underloaded spindle may indicate inefficient cutting, wasting valuable machining time.
What Happens When Spindle Load Is Too High or Too Low?
When the spindle load is too high, the machine may experience excessive wear, overheating, or even mechanical failure. On the other hand, a low spindle load might mean that the tool is not cutting efficiently, resulting in longer cycle times and higher operational costs.
Tools and Techniques for Monitoring Spindle Load
How Is Spindle Load Measured?
Modern CNC machines are equipped with spindle load monitors that display real-time data. These monitors help operators assess whether the spindle is under optimal load conditions. Some advanced systems even trigger alarms when the spindle load exceeds safe thresholds.
What Tools Are Available for Monitoring?
Several software and hardware solutions are available to monitor spindle load, including integrated sensor systems and third-party software. Some solutions even allow remote monitoring and provide predictive insights into potential spindle failures.
Interpreting Spindle Load Data for Improved Operations
How Can You Use Spindle Load Data to Optimize Operations?
By regularly analyzing spindle load data, operators can make informed decisions about tool adjustments, feed rates, and cutting strategies. Identifying load patterns can help pinpoint inefficiencies and areas for improvement in the machining process.
What Are the Key Metrics to Watch?
Key metrics include load percentage, cycle time under various loads, and the relationship between spindle load and material removal rate. Anomalies in these metrics may indicate underlying issues such as tool wear or improper setup.
Material Hardness and Cutting Resistance
How Does Material Hardness Affect Spindle Load?
Harder materials exert more resistance on the spindle, leading to higher spindle loads. As a result, cutting harder materials requires a careful balance of spindle speed and feed rate to avoid overloading.
What Role Does Cutting Resistance Play?
Cutting resistance, which varies based on the material’s hardness and composition, directly impacts the spindle’s load capacity. Softer materials may allow higher speeds and feeds, while harder materials require slower, more precise machining to avoid damage.
Spindle Speed and Feed Rate
How Do Spindle Speed and Feed Rate Influence Load?
Spindle speed and feed rate are two of the most important factors influencing spindle load. High speeds combined with improper feed rates can lead to excessive loads, while low speeds may not fully utilize the machine’s capabilities, wasting time and energy.
How Can You Adjust These for Optimal Performance?
To optimize spindle load, it’s important to match spindle speed and feed rate to the specific material and tooling being used. Balanced adjustments can reduce the risk of spindle overload, improve surface finish, and enhance overall machining efficiency.
Tool Wear and Maintenance Schedules
How Does Tool Wear Impact Spindle Load?
Worn-out tools require more force to cut through materials, increasing spindle load. This additional load not only degrades machining accuracy but also shortens tool life and increases machine downtime.
Why Is a Maintenance Schedule Critical?
A well-planned maintenance schedule ensures that tools are replaced or sharpened before they affect spindle load. By monitoring tool wear and sticking to regular maintenance, you can avoid unnecessary strain on the spindle, leading to longer machine and tool life.
Adjustments for Optimal Spindle Load
What Adjustments Can You Make to Maintain Optimal Load?
Several adjustments can help maintain an optimal spindle load, including modifying feed rates, changing tool paths, and upgrading to better-suited cutting tools. These adjustments not only reduce load but also improve cutting efficiency.
Can Software Assist in Optimizing Spindle Load?
Yes, many CNC machines come with built-in load monitoring software that adjusts cutting parameters in real-time. By using these tools, you can ensure that your spindle load stays within safe limits, even under changing conditions.
Role of Coolants in Managing Spindle Load
How Do Coolants Help Manage Spindle Load?
Coolants play an essential role in reducing spindle load by minimizing heat and friction during cutting. Proper use of coolants allows for higher cutting speeds and longer tool life, as well as improved surface finishes.
Are There Best Practices for Using Coolants?
Using the right coolant type, application method, and flow rate can dramatically affect spindle load. It’s also important to regularly check coolant levels and make sure the system is functioning properly to prevent overheating and excessive spindle load.
Impact of Spindle Load on Product Precision
Can Spindle Load Affect the Quality of the Final Product?
Yes, spindle load has a direct effect on the precision and surface quality of machined parts. Excessive spindle load can lead to inaccuracies, poor surface finishes, and dimensional deviations.
How Can Operators Minimize Precision Issues?
By carefully controlling spindle load, particularly during high-tolerance operations, operators can maintain better control over the final product’s precision. Regularly adjusting feed rates, spindle speeds, and monitoring load are essential for achieving optimal results.
Case Studies: Success Stories of Spindle Load Optimization
Real-World Example #1
A machining shop implemented real-time spindle load monitoring and reduced their tool wear by 15%. By analyzing load data, they adjusted their feed rates and improved the overall precision of their parts.
Real-World Example #2
In another case, a manufacturer was able to cut production time by 10% through optimizing spindle speed and feed rates, reducing load without sacrificing part quality.
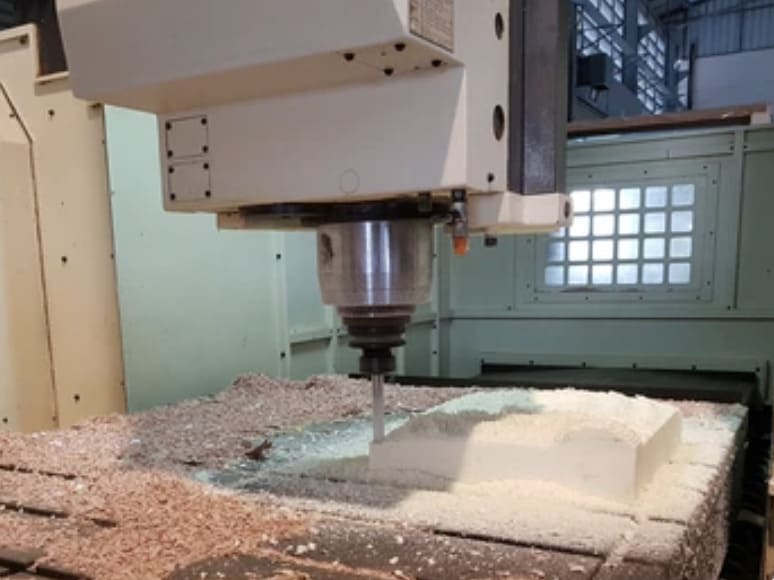
Identifying Symptoms of Overloaded Spindles
What Are the Warning Signs of an Overloaded Spindle?
Common symptoms include increased vibrations, overheating, tool wear, and poor surface finish. Operators may also hear abnormal sounds coming from the spindle, signaling excessive load.
How Can You Address These Issues Early?
Regular monitoring of spindle load using integrated systems can alert operators to issues before they become serious. Quick adjustments in feed rates and spindle speeds also prevent unnecessary strain on the spindle.
Preventive Measures and Solutions
What Are Common Solutions to Spindle Overload?
Operators can implement various solutions, including reducing cutting speeds, using sharper tools, and incorporating coolants to decrease friction and heat. These steps will reduce the risk of spindle overload.
Are There Any Long-term Solutions?
Yes, investing in load management software and predictive maintenance systems can provide long-term solutions to spindle load issues. These systems offer real-time feedback, allowing operators to make adjustments before problems arise.
Innovations in Spindle Design and Load Management
What Are the Latest Innovations?
Recent innovations include smart spindle technology, which integrates AI and IoT systems to monitor load in real-time. These spindles automatically adjust their operation to minimize overload and improve efficiency.
How Will These Innovations Change CNC Operations?
These technologies promise to reduce downtime, improve precision, and lower maintenance costs, making CNC operations more efficient and cost-effective.
Predictive Analytics and Its Role in Spindle Maintenance
How Can Predictive Analytics Help?
Predictive analytics can forecast potential spindle load issues before they occur by analyzing historical data and trends. This allows operators to take preventive measures, reducing machine downtime and enhancing operational efficiency.
Key Takeaways
- Spindle load is critical for CNC machine performance, affecting both precision and efficiency.
- Monitoring spindle load regularly can prevent machine downtime and tool wear.
- Adjusting feed rates, spindle speed, and using coolants are key to managing load.
- Innovations like AI-driven spindles and predictive analytics are revolutionizing spindle load management.
- Following best practices ensures longer machine life, better precision, and enhanced productivity.
By mastering spindle load management, you’ll ensure that your CNC operations run smoothly, efficiently, and with minimal downtime.
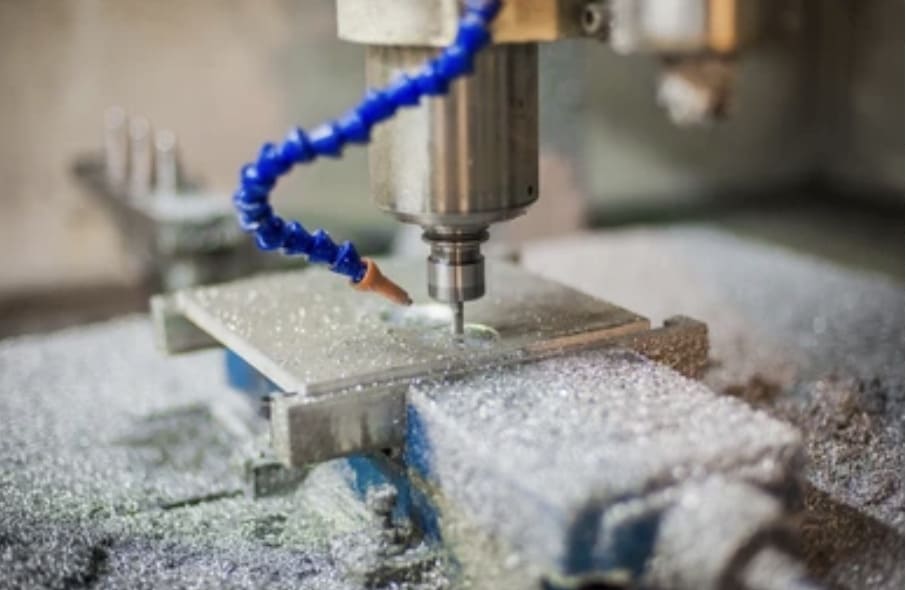
- RicoCNC has a team of professionals who have been engaged in the design, production, sales, and maintenance of electro spindles for many years. Our company accepts the purchase of various types of CNC spindles.
water-cooled CNC spindle motors
Edge banding machine spindle motors.
- If you need any CNC spindle, please contact us.