Introduction
CNC (Computer Numerical Control) machines are at the heart of modern manufacturing, and one critical feature that ensures precision and efficiency is spindle orientation. But what exactly is spindle orientation, and why does it matter? Understanding the role of spindle orientation in CNC systems can significantly enhance both the performance and the quality of machined parts. In this article, we’ll break down the concept of spindle orientation, how it works, and its relevance in everyday CNC operations.
Why Read This Article?
Spindle orientation is a technical concept that plays a crucial role in CNC machining. Whether you’re a CNC operator or someone curious about how these machines work, knowing the basics of spindle orientation will improve your understanding and troubleshooting capabilities. This article covers the importance of spindle orientation, common challenges, and how modern advancements are shaping the future of CNC technology. By the end, you’ll have a better grasp of how to optimize spindle orientation for better performance.
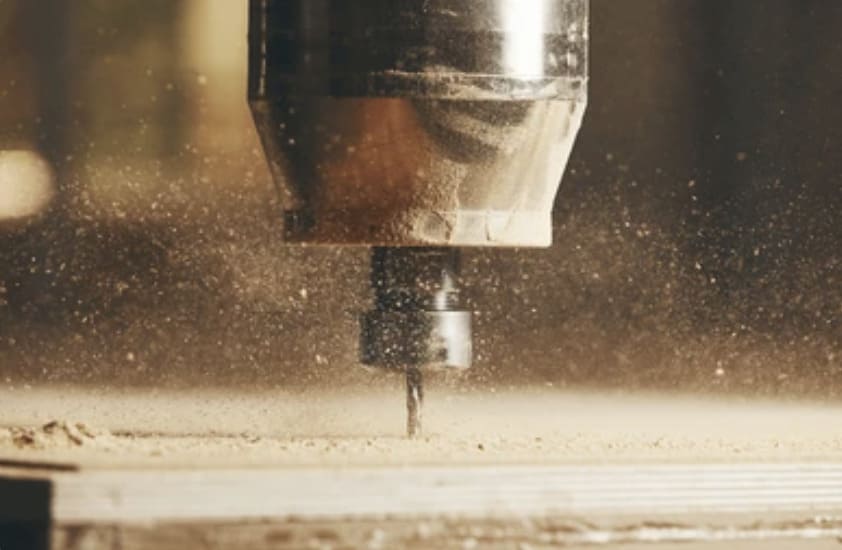
Definition and Importance of Spindle Orientation
What is Spindle Orientation?
Spindle orientation refers to the precise positioning of the spindle to facilitate tool changes or operations that require a specific alignment. In CNC machines, this is particularly critical as the spindle must be correctly oriented to ensure that the tool is placed in the exact desired position.
Why is Spindle Orientation Important?
Proper spindle orientation impacts both the accuracy and efficiency of CNC machining. Incorrect orientation can lead to tool misalignment, causing errors in the final product, poor surface finishes, or even tool breakage. Hence, maintaining correct spindle orientation is vital to ensuring smooth, high-precision operations.
Different Types of Spindle Orientation Mechanisms
How do Spindle Orientation Systems Work?
There are different types of spindle orientation systems, and each has unique mechanisms to achieve precision. These typically include mechanical clutches, sensors, and servo motors. Depending on the machine type, the spindle may orient by using an electronic sensor or a mechanical indexing system.
- Electronic Systems: These utilize a sensor that detects the exact position of the spindle. It’s typically faster and more accurate.
- Mechanical Systems: These use gears or cams to physically position the spindle, often providing a more rugged but slower process.
Which Mechanism is Right for Your CNC?
Choosing between electronic or mechanical systems depends on your application’s needs. High-speed, precision machining often benefits from electronic spindle orientation, while heavy-duty machining might prefer mechanical systems due to their durability.
How Spindle Orientation Affects CNC Operations
Can Spindle Orientation Affect the Accuracy of CNC Machining?
Absolutely. Spindle orientation has a direct impact on the alignment of tools, which influences the precision of your cuts or drilling operations. Misaligned spindles may lead to inaccuracies, wasted material, and reduced part quality.
What are the Consequences of Incorrect Spindle Orientation?
Incorrect spindle orientation can cause:
- Tool misalignment, leading to poor cut quality
- Excessive wear on both tools and the spindle
- Increased downtime due to frequent adjustments or repairs
Anatomy of a CNC Spindle
What are the Key Components of a CNC Spindle?
A CNC spindle consists of several vital components, including:
- Motor: Drives the spindle’s rotation.
- Bearings: Provide smooth rotation while supporting the spindle shaft.
- Housing: Encases the spindle components, protecting them from external contaminants.
Understanding these components helps in diagnosing issues and performing routine maintenance.
Role of Bearings in Spindle Performance
How do Bearings Impact Spindle Performance?
Bearings are essential for spindle operation as they ensure smooth rotation while minimizing friction. Worn-out bearings can cause vibration, noise, and ultimately lead to spindle failure. Therefore, regularly checking the condition of bearings is critical.
What Happens When Bearings Wear Out?
Bearing wear often manifests as vibration or noise, which can decrease the spindle’s operational lifespan. Poor bearing performance can also reduce machining precision.
The Significance of Spindle Speed and Power
Why is Spindle Speed Important?
Spindle speed plays a crucial role in CNC machining as it determines how fast the tool rotates. Matching the correct speed with the material being machined ensures optimal cutting conditions. Too much speed can cause tool overheating, while too little speed may result in poor cuts.
How Does Spindle Power Affect Performance?
Power defines the spindle’s ability to maintain torque during operations. Higher spindle power allows for more aggressive cuts and faster material removal, which is vital in high-productivity environments.
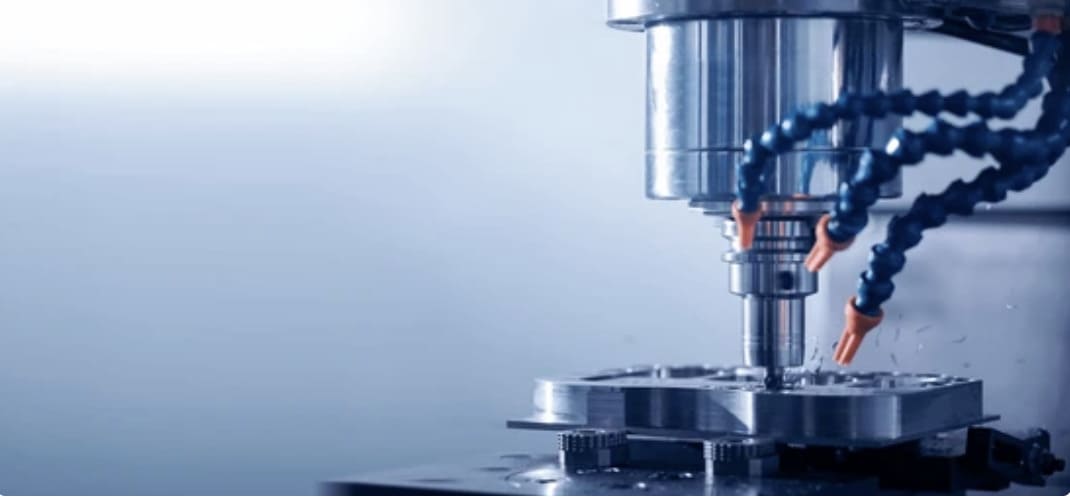
Step-by-Step Guide to Achieving Proper Spindle Orientation
- Shut Down the Machine: Ensure the machine is powered off to prevent accidents.
- Verify Sensor Functionality: Check the sensor or mechanical indexing system for proper functionality.
- Adjust the Spindle: If necessary, manually adjust the spindle using the machine’s control panel or through software.
- Test the Alignment: Run a trial operation to ensure the spindle is oriented correctly.
Common Challenges in Spindle Orientation and Solutions
What are the Common Problems in Spindle Orientation?
Spindle orientation issues can arise from:
- Sensor malfunctions
- Mechanical misalignment
- Software glitches
How Can These Problems Be Fixed?
Regular maintenance, including sensor calibration and alignment checks, can solve most orientation issues. Additionally, updating your machine’s software can prevent glitches that might cause incorrect orientation.
Maintenance Tips for Optimal Spindle Orientation
How Often Should Spindle Orientation Be Checked?
Routine checks are essential to maintain spindle health. Regular inspection of bearing conditions and sensor accuracy can prevent larger issues. Depending on machine usage, a weekly or monthly check might be necessary.
Are There Any Preventative Measures to Take?
Yes, implementing a regular cleaning schedule and ensuring proper lubrication of moving parts will prolong the spindle’s life and reduce downtime caused by misorientation.
Latest Trends in Spindle Technology
What New Developments Are There in Spindle Orientation?
Recent innovations in spindle orientation include AI-driven systems that automatically adjust the spindle in real-time for optimal performance. These systems are equipped with sensors that detect wear and tear, offering predictive maintenance capabilities.
How Is Automation Impacting Spindle Orientation?
Automation is reducing the manual intervention required for spindle alignment. Today’s CNC machines can automatically adjust spindle orientation based on the machining task, reducing downtime and human error.
Impact of Automation on Spindle Orientation
How is Automation Shaping the Future of CNC?
Automation is significantly reducing human error and improving the efficiency of spindle orientation. Modern CNC systems can detect alignment issues and automatically adjust, minimizing downtime and improving overall machine productivity.
Future Outlook: What’s Next for CNC Spindle Orientation?
What Technological Advances Are on the Horizon?
Future spindle orientation systems will likely integrate even more with AI and IoT technologies, allowing machines to self-diagnose and correct orientation issues without operator input. Additionally, advancements in precision sensors will further improve accuracy.
Spindle Orientation in Precision Machining
For industries like aerospace and medical device manufacturing, precision is non-negotiable. Proper spindle orientation ensures that every cut is made to exact specifications, crucial for achieving the high tolerances required in these industries.
Case Studies: Success Stories of Effective Spindle Orientation
Case Study 1: Automotive Industry
An automotive parts manufacturer improved their CNC machine’s productivity by upgrading to a servo-driven spindle orientation system. This resulted in a 15% reduction in downtime and improved part accuracy.
Case Study 2: Aerospace Manufacturing
An aerospace company used automated spindle alignment to achieve the high precision required for turbine blade production. By implementing a regular spindle maintenance program, they extended the life of their machines by 30%.
Choosing the Right Spindle Orientation for Your CNC Machine
How Do You Choose the Right System?
Consider the type of work you are doing and the precision required. For high-speed operations and precision work, electronic systems are generally preferred, while mechanical systems are ideal for heavy-duty tasks.
Key Takeaways
- Spindle orientation is essential for precision and efficient CNC operations.
- Different orientation systems are available, each with specific advantages.
- Routine maintenance and regular checks can prevent common spindle orientation issues.
- Automation and AI are set to revolutionize spindle orientation systems in the future.
This comprehensive understanding of spindle orientation in CNC will help improve your machining accuracy and extend the life of your machine.
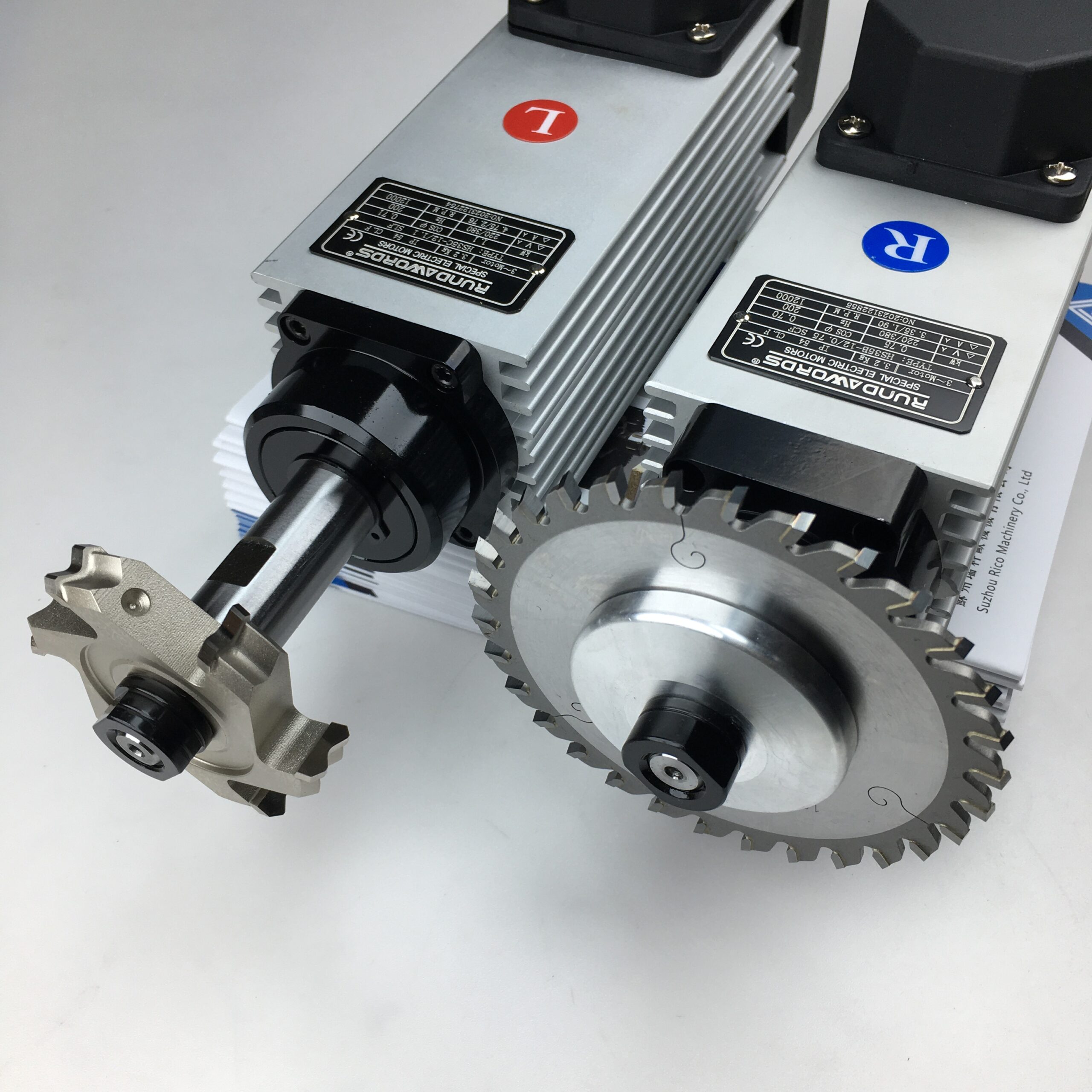
- RicoCNC has a team of professionals who have been engaged in the design, production, sales, and maintenance of electro spindles for many years. Our company accepts the purchase of various types of CNC spindles.
water-cooled CNC spindle motors
Edge banding machine spindle motors.
- If you need any CNC spindle, please contact us.