What is the Purpose of the CNC Spindle Motor in the Machining Center?
The spindle motor is the heart of any CNC machining center, controlling the rotation of the cutting tool and directly affecting the precision, speed, and quality of machining. But what is its true purpose, and how does it influence your machining outcomes?
In this article, we’ll explore the critical role of the CNC spindle motor, uncover its technical specifications, and examine how advancements in spindle technology are revolutionizing the manufacturing world. Whether you’re a beginner or an experienced machinist, this guide will help you better understand spindle motors and their vital function in CNC machining centers.
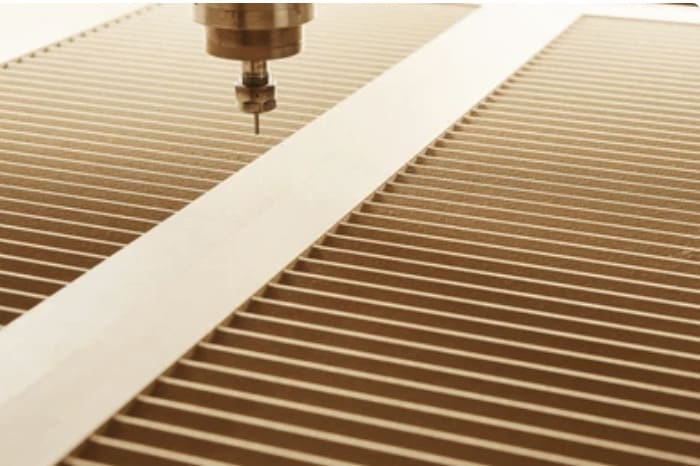
What is the Role of the Spindle Motor in CNC Machining Centers?
The CNC spindle motor serves as the powerhouse of the machining center, driving the tool that cuts and shapes materials. It controls rotational speed and power, ensuring that the cutting tool removes material efficiently while maintaining precision. The motor’s purpose is to convert electrical energy into mechanical motion, which is then transferred to the spindle shaft.
Without a properly functioning spindle motor, the CNC machine loses its ability to process workpieces accurately, resulting in poor finishes and subpar performance.
What are the Key Components of a CNC Spindle Motor?
A CNC spindle motor is made up of several key components that allow it to operate effectively. These include:
- Motor Shaft: The shaft connects to the cutting tool, transferring the rotational force.
- Bearings: These allow for smooth and precise rotation, minimizing friction.
- Cooling Systems: Either air or water-cooled, they maintain an optimal operating temperature.
Understanding these components is essential for maintaining the motor’s performance and longevity.
What Types of CNC Spindle Motors Exist, and What Are Their Applications?
There are multiple types of spindle motors, each suited for different applications:
- Asynchronous Spindle Motors: Commonly used for general-purpose machining, offering high versatility.
- Synchronous Spindle Motors: These are used when precision is critical, as they offer higher efficiency and constant speeds.
Depending on the machining needs, the choice of spindle motor impacts performance, especially when working with specialized materials like aluminum, steel, or composites.
How Do Power Ratings Impact Spindle Motor Performance?
Power ratings of spindle motors directly influence the machine’s ability to handle material removal and sustain heavy-duty operations. Higher power ratings provide:
- Increased Torque: Essential for cutting through hard materials.
- Faster Machining: Higher-rated motors complete tasks quicker without sacrificing quality.
Choosing the right power rating for your CNC machine can enhance productivity while maintaining precision.
Why is Speed Range and Precision Control Essential?
The spindle motor’s speed range determines how fast the cutting tool rotates, directly affecting the precision of cuts. Having a wide speed range allows:
- Flexibility: Adaptable to a variety of materials and machining techniques.
- Precision: Fine-tuning speed ensures that cuts are accurate and clean.
For industries requiring tight tolerances, like aerospace and medical devices, precision control is paramount.
What Role Does Torque Play in Material Removal?
Torque, the rotational force exerted by the spindle motor, is critical for material removal. Higher torque enables the machine to:
- Cut through dense materials like metal or composites with ease.
- Sustain consistent force, reducing the likelihood of tool wear or breakage.
Without sufficient torque, the CNC machine struggles to remove material effectively, leading to poor quality.
What Innovations Are Enhancing Spindle Motor Efficiency and Durability?
Modern spindle motors incorporate numerous innovations to improve efficiency and extend their service life. Some of the most impactful advancements include:
- Integrated Cooling Systems: These prevent overheating, allowing for longer operational hours.
- Advanced Bearing Systems: Reduce friction and wear, increasing motor longevity.
- Smart Sensors: Enable real-time monitoring and predictive maintenance, minimizing downtime.
These innovations reduce operational costs and improve overall performance in a CNC machining center.
Air-Cooled vs. Water-Cooled Spindle Motors: Which is Better?
Cooling systems are crucial for spindle motors, with two primary types available:
- Air-Cooled Spindles: These are low-maintenance and work well for lighter applications.
- Water-Cooled Spindles: Offer better cooling for heavy-duty tasks, making them suitable for high-power CNC machines.
The choice between the two depends on the workload and environment. Heavy-duty, continuous machining operations may benefit more from water-cooled systems due to their superior temperature control.
Cooling System | Benefits | Drawbacks |
---|---|---|
Air-Cooled | Low-maintenance, simple | Less efficient for heavy-duty |
Water-Cooled | Superior cooling performance | Requires more upkeep |
How Are Sensors Integrated for Predictive Maintenance in Spindle Motors?
Predictive maintenance is becoming increasingly important in CNC machining. Many spindle motors now come with integrated sensors that monitor factors such as:
- Vibration Levels
- Temperature
- Motor Load
These sensors provide real-time data, enabling machine operators to anticipate wear and tear, schedule maintenance proactively, and avoid unexpected failures.
What Machining Needs and Workpiece Materials Determine Spindle Motor Compatibility?
The type of workpiece materials and the machining requirements heavily influence spindle motor selection. For example:
- Soft Materials like wood or plastic require lower power and speed.
- Harder Materials such as steel or titanium demand higher torque and power ratings.
Understanding these factors ensures that the chosen spindle motor can handle the specific machining tasks efficiently.
How Do Budget Considerations Affect Spindle Motor ROI?
Choosing a spindle motor requires balancing performance and cost. Higher-end motors may offer:
- Greater Efficiency
- Longer Lifespan
- Lower Maintenance Costs
However, the initial investment is higher. Performing a thorough ROI analysis can help justify the cost of advanced spindle motors by demonstrating long-term savings.
Step-by-Step Guide to Installing a CNC Spindle Motor
Installing a CNC spindle motor correctly ensures optimal performance. Here’s a simple step-by-step guide:
- Disconnect Power: Always turn off the machine before installation.
- Position the Motor: Align the motor with the spindle housing.
- Secure Mounting Bolts: Ensure the motor is firmly secured.
- Connect Power and Cooling: Attach the necessary electrical and cooling connections.
- Run Initial Tests: Power the machine and run tests to verify the installation.
What are Routine Maintenance Tips to Prolong Spindle Motor Life?
Proper maintenance can extend the life of your spindle motor. Key maintenance practices include:
- Lubricating Bearings: Reduces friction and wear.
- Cleaning the Motor: Prevents debris buildup.
- Monitoring Cooling Systems: Ensures they are functioning correctly.
Regular maintenance not only prevents costly repairs but also ensures consistent performance.
How to Troubleshoot Common Spindle Motor Issues?
Spindle motors may experience issues such as:
- Overheating: Caused by inadequate cooling or overuse.
- Vibration: Could indicate worn bearings.
- Loss of Power: Often due to electrical issues or wear.
By addressing these problems early, you can prevent downtime and costly repairs.
Case Studies: Real-World Applications of CNC Spindle Motors
Spindle motors are used in a variety of industries, including:
- Automotive Manufacturing: For precision parts like gears and engines.
- Aerospace: Where high-precision machining is essential.
- Furniture Production: For detailed woodworking and design.
These case studies highlight the versatility and importance of spindle motors in various manufacturing sectors.
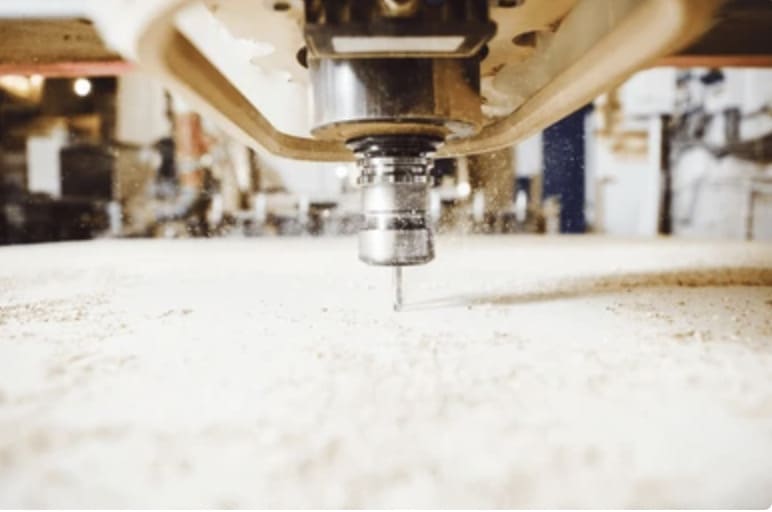
Key Takeaways
- The CNC spindle motor is the powerhouse of machining centers, affecting precision and speed.
- Different types of spindle motors exist, each suited for specific tasks.
- Torque and power ratings are critical for material removal and machining efficiency.
- Cooling systems and innovations like smart sensors improve spindle motor performance.
- Proper maintenance and installation ensure long spindle motor life.
- Real-world applications demonstrate the spindle motor’s importance across various industries.
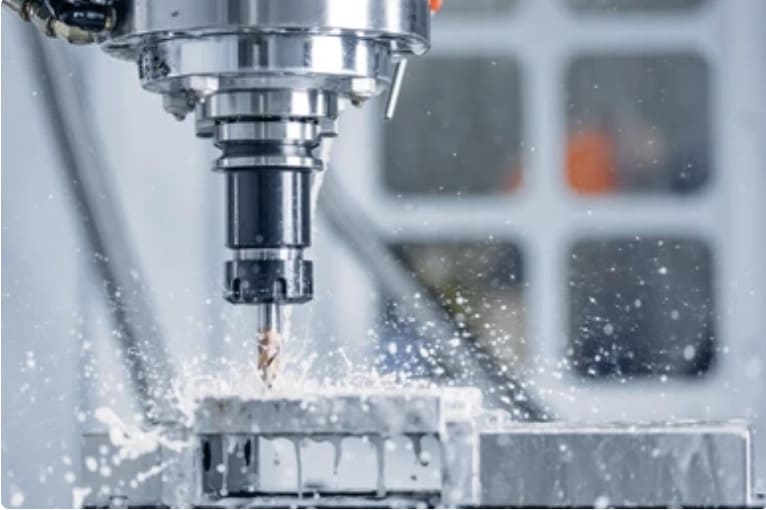
- RicoCNC has a team of professionals who have been engaged in the design, production, sales, and maintenance of electro spindles for many years. Our company accepts the purchase of various types of CNC spindles.
water-cooled CNC spindle motors
Edge banding machine spindle motors.
- If you need any CNC spindle, please contact us.