Introduction
In recent years, with the continuous progress of CNC spindles, the performance has gradually developed towards high speed, high precision and high rigidity. This trend has put forward higher requirements for the design, material selection and bearing manufacturing process of CNC spindles. In order to meet the needs of modern efficient processing, machine tool spindles have shown many new features in design, especially in the selection and material application of spindle bearings, which provide a solid foundation for achieving high-precision and high-speed processing.
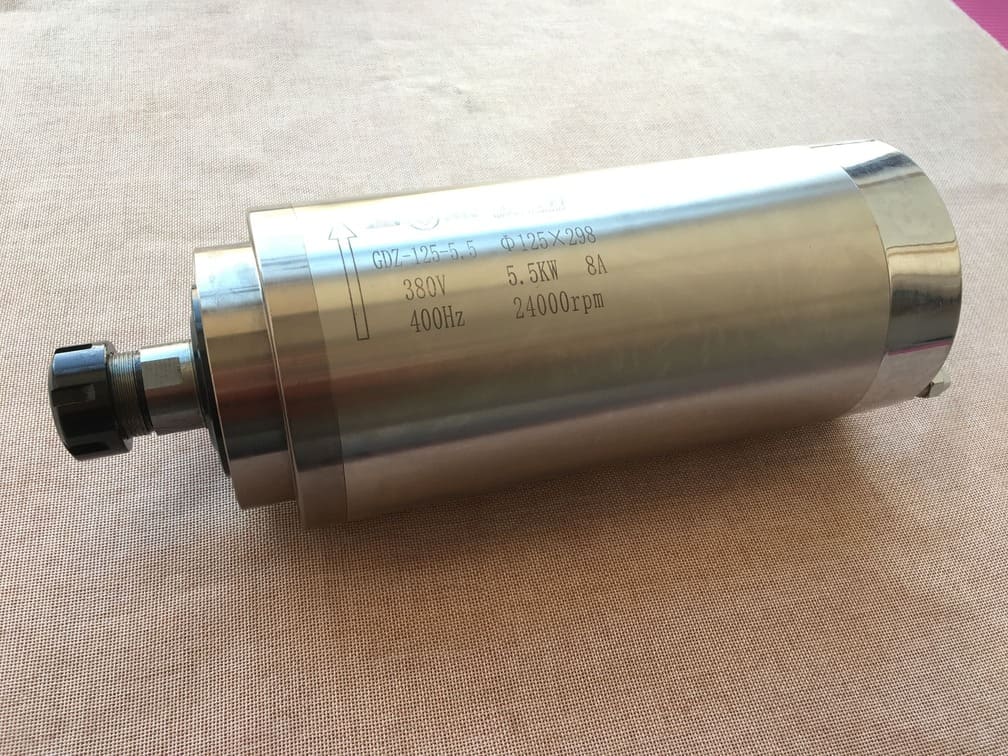
Special features of the design
The accuracy of the machine tool spindle is directly affected by the bearing’s radial runout, end face runout, and rolling element diameter inconsistency. To ensure the accuracy of the spindle system and its workpieces, the bearing accuracy used in the precision machine tool spindle should reach P5 or higher. For high-speed, high-precision machine tools like CNC machines and machining centers, ultra-precision bearings of P4 or above are required.
High-speed adaptability is also essential for spindle bearings. With the continuous improvement of processing speed, especially in the development and improvement of high-speed spindles such as electric spindles, higher requirements are placed on the high-speed adaptability of bearings. Suppose the high-speed adaptability of the bearing is not good. In that case, the spindle system will cause the bearing to burn out and fail due to excessive temperature rise, affecting the processing accuracy and the service life of the equipment.
Research on materials
Regarding material selection, the high precision, high speed, and high-reliability requirements of machine tool spindle bearings make it difficult for traditional materials to meet the needs of modern machine tools. The ring is usually made of high-quality refined steel, while the cage material is copper, plastic, and special self-lubricating. Rolling element materials include bearing steel and ceramic materials.
Due to their excellent performance, ceramic materials, primarily silicon nitride ceramics, are increasingly valued in manufacturing high-speed precision bearings. Compared with traditional bearing steel, the specific gravity of silicon nitride ceramics is only one-third of steel, significantly reducing the stress level of rolling elements on the rings during high-speed operation, thereby significantly improving the bearing’s limit speed.
Its hardness is as high as 1500HV, twice that of bearing steel, and its high-temperature resistance is as high as 1200℃, greatly expanding the application range of bearings.
The application of ceramic materials opens up a new world of rolling bearing materials and dramatically promotes the development of high-speed and high-precision machine tools.
Ceramic bearings have become ideal for manufacturing high-speed precision bearings due to their low density, high elastic modulus, low thermal expansion coefficient, wear resistance, high temperature resistance, and corrosion resistance.
Realization of highly high guiding accuracy and speed
In electro-spindle applications, the bearing temperature is uneven due to the large gradient of the spindle temperature field, which causes an imbalance in axial and radial loads. This uneven load will affect the stiffness of the bearing and the service life of the tandem bearing group. Therefore, it is crucial to use suitable materials and designs to ensure the stability and accuracy of the bearings during high-speed operation.
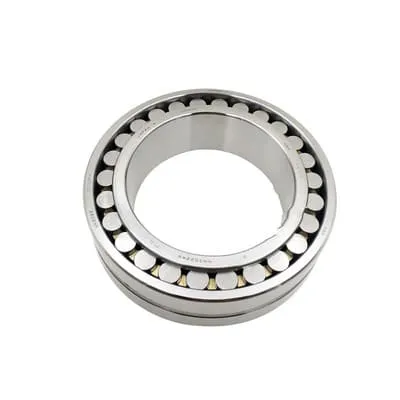
Conclusion
As machine tool spindles develop towards high speed and high precision, spindle bearings have higher requirements in design and materials. The introduction of ceramic materials provides new possibilities for the development of high-performance bearings, which help to achieve higher processing accuracy and speed. With the continuous advancement of technology, machine tool spindles will continue to move towards higher speeds, higher precision, and longer service life.
Summary FAQ based on the article
1. What is the development trend of modern machine tool spindles?
CNC spindles develop towards high speed, precision, and rigidity.
2. Why is high-speed adaptability important for spindle bearings?
High-speed adaptability determines the bearing’s stability and temperature rise control ability at high speed, affecting the accuracy and life of the spindle system.
3. What are the advantages of ceramic materials in spindle bearings?
Ceramic materials have low density, high rigidity, and low thermal expansion coefficient, which can improve the limit speed and rigidity of bearings, reduce heat generation, and improve wear resistance and high-temperature resistance.
4. What is the impact of uneven bearing temperature on spindle performance in electro spindles?
The uneven bearing temperature will lead to unbalanced axial and radial loads, affecting the rigidity and service life of the bearing and further affecting the machining accuracy of the spindle.
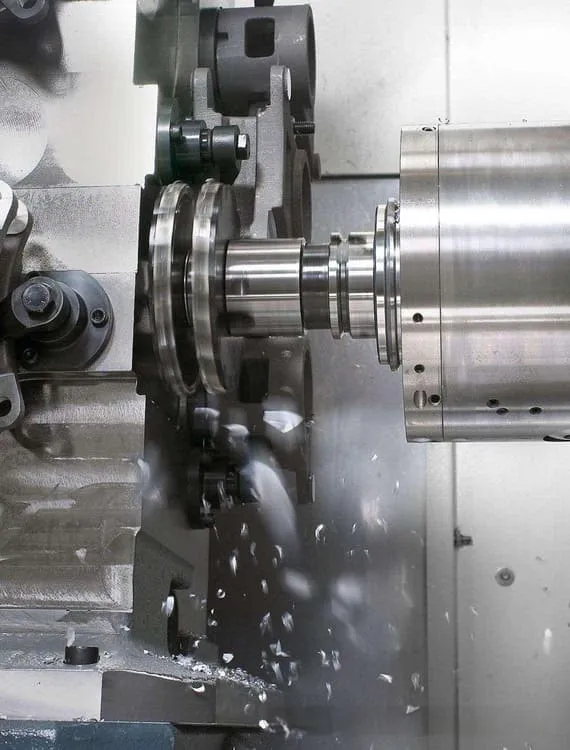
- RicoCNC has a team of professionals who have been engaged in the design, production, sales, and maintenance of electro spindles for many years. Our company accepts the purchase of various types of CNC spindles.
water-cooled CNC spindle motors
Edge banding machine spindle motors.
- If you need any CNC spindle, please contact us.