What kind of spindle is suitable for machining steel?
When it comes to machining steel, selecting the appropriate spindle is crucial for achieving optimal results. The right spindle can significantly impact the efficiency, precision, and overall quality of your machining process. In this comprehensive guide, we’ll explore the key factors to consider when choosing a spindle for steel machining, helping you make an informed decision that will enhance your CNC operations.Whether you’re a seasoned machinist or new to the world of CNC manufacturing, understanding the nuances of spindle selection for steel machining can greatly improve your productivity and output quality. Let’s dive into the essential aspects of spindle technology and how they relate to working with steel.
What Are the Key Considerations for Spindle Selection in Steel Machining?
When choosing a spindle for machining steel, several factors come into play:
- Spindle Power: Steel is a tough material that requires significant cutting force. A high-power spindle is essential for efficient material removal.
- Torque: High torque is crucial for machining steel, especially at lower speeds. Look for spindles that offer good low-end torque characteristics.
- Speed Range: While high speeds are not always necessary for steel, a wide speed range allows for versatility in machining different steel grades and performing various operations.
- Stiffness: A rigid spindle helps minimize vibration and chatter, which is particularly important when working with hard materials like steel.
- Cooling System: Effective cooling is vital to maintain precision and extend tool life when machining steel, as the process generates significant heat.
Considering these factors will help you narrow down your options and select a spindle that’s well-suited for steel machining applications.
How Does Spindle Speed Impact Steel Machining?
Spindle speed plays a crucial role in the machining process, especially when working with steel:
- Cutting Speed: The optimal cutting speed for steel is generally lower than for softer materials. This means that spindle speed needs to be carefully controlled to achieve the right surface feet per minute (SFM) for the specific steel grade being machined.
- Heat Generation: Higher speeds can generate more heat, which can be detrimental when working with steel. Excessive heat can lead to premature tool wear and affect the material properties of the steel.
- Surface Finish: The right combination of spindle speed and feed rate is essential for achieving the desired surface finish on steel parts.
- Tool Life: Operating at the correct speed can significantly extend tool life, which is particularly important given the abrasive nature of steel machining.
While high-speed spindles are often touted for their efficiency, it’s important to remember that steel machining doesn’t always require extremely high speeds. The key is to find a spindle that offers a suitable speed range for the types of steel and operations you’ll be performing.
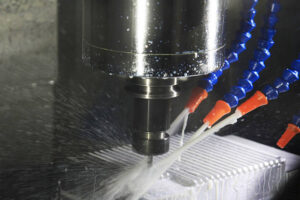
What Role Does Spindle Torque Play in Steel Machining?
Torque is a critical factor when machining steel:
- Material Removal: High torque allows for greater depth of cut and feed rates, enabling efficient material removal even in tough steel alloys.
- Low-Speed Operations: Many steel machining operations, especially with larger tools, require high torque at lower speeds. A spindle with good low-end torque characteristics is essential for these applications.
- Maintaining Cut: Adequate torque helps maintain a consistent cut even when encountering variations in material hardness or when performing interrupted cuts.
- Tool Performance: Higher torque allows for the use of larger diameter tools, which can improve productivity in steel machining operations.
When evaluating spindles for steel machining, pay close attention to the torque curve across the speed range. A spindle with high torque at lower speeds can be particularly advantageous for many steel machining applications.
How Important is Spindle Stiffness for Steel Machining?
Spindle stiffness is a crucial factor in achieving precision and efficiency when machining steel:
- Vibration Reduction: A stiff spindle helps minimize vibration and chatter, which is particularly important when working with hard materials like steel.
- Dimensional Accuracy: Greater stiffness contributes to improved dimensional accuracy of machined parts, as it reduces deflection under cutting forces.
- Surface Finish: A rigid spindle setup helps maintain a consistent tool position, leading to better surface finishes on steel parts.
- Tool Life: Reduced vibration means less stress on cutting tools, contributing to extended tool life in steel machining applications.
When selecting a spindle for steel machining, consider factors such as bearing design, shaft diameter, and overall construction that contribute to spindle stiffness. A robust spindle design can make a significant difference in your machining outcomes.
What Type of Cooling System is Best for Steel Machining Spindles?
Effective cooling is essential for spindles used in steel machining:
- Heat Management: Steel machining generates significant heat, which can affect both the spindle and the workpiece. An efficient cooling system helps maintain thermal stability.
- Precision Maintenance: Consistent temperature control helps maintain the precision of the spindle, ensuring accurate machining results.
- Tool Life Extension: Proper cooling can significantly extend the life of cutting tools, which is particularly important given the abrasive nature of steel machining.
- Coolant-Through Capability: For deep hole drilling and other challenging steel machining operations, a spindle with coolant-through capability can be highly advantageous.
Consider spindles with advanced cooling systems, such as oil-air lubrication or water-cooled designs, for demanding steel machining applications. These systems can provide superior thermal management compared to traditional air-cooled spindles.
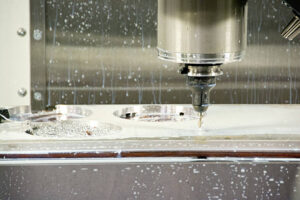
How Does Spindle Power Affect Steel Machining Capabilities?
Spindle power is a key determinant of machining capabilities, especially when working with tough materials like steel:
- Material Removal Rate: Higher power allows for increased material removal rates, improving overall productivity in steel machining operations.
- Cutting Parameters: More powerful spindles enable the use of more aggressive cutting parameters, such as higher feed rates and depths of cut.
- Tool Options: Greater power allows for the use of larger diameter tools or more complex cutting geometries, expanding your machining possibilities.
- Consistent Performance: A high-power spindle can maintain consistent performance even under heavy cutting loads, which is often necessary when machining steel.
When selecting a spindle for steel machining, consider the power requirements of your typical operations. While higher power generally offers more capabilities, it’s important to balance this with other factors such as speed range and torque characteristics.
What Are the Benefits of High-Speed Spindles in Steel Machining?
While steel machining often doesn’t require extremely high speeds, high-speed spindles can offer several advantages:
- Versatility: A high-speed spindle with a wide speed range allows for machining various steel grades and performing different operations on the same machine.
- Finishing Operations: Higher speeds can be beneficial for finishing operations on steel, allowing for improved surface finishes and tighter tolerances.
- Smaller Tools: When working with smaller diameter tools, higher speeds may be necessary to achieve optimal cutting conditions.
- Productivity: In some cases, higher speeds can lead to increased productivity, especially when combined with appropriate feed rates and cutting strategies.
It’s important to note that while high-speed capabilities can be advantageous, they should be balanced with other factors such as torque and stiffness when choosing a spindle for steel machining.
How Do Different Steel Grades Affect Spindle Requirements?
Various steel grades can have different machining characteristics, impacting spindle requirements:
- Hardness Variations: Harder steel grades may require spindles with higher torque and power to maintain cutting efficiency.
- Thermal Considerations: Some steel alloys generate more heat during machining, necessitating spindles with robust cooling systems.
- Speed Adjustments: Different steel grades may have varying optimal cutting speeds, making a spindle with a wide speed range advantageous.
- Tool Wear: Certain steel grades are more abrasive, potentially requiring spindles that can accommodate frequent tool changes or specialized tooling.
When selecting a spindle, consider the range of steel grades you’ll be working with and choose a model that offers the flexibility to handle various material characteristics.
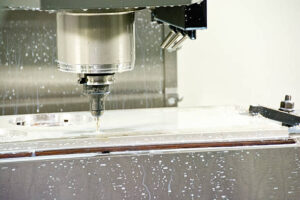
What Maintenance Considerations Are Important for Spindles Used in Steel Machining?
Proper maintenance is crucial for spindles used in steel machining:
- Regular Inspections: Frequent checks for wear, vibration, or unusual noises can help prevent unexpected breakdowns.
- Lubrication: Ensuring proper lubrication is critical, especially given the high forces involved in steel machining.
- Cooling System Maintenance: Regular cleaning and maintenance of the cooling system is essential to maintain thermal stability.
- Alignment Checks: Periodic alignment checks can help maintain precision, which is particularly important when working with steel.
- Bearing Replacement: Timely replacement of bearings can prevent catastrophic failures and maintain spindle performance.
Implementing a proactive maintenance schedule can significantly extend the life of your spindle and ensure consistent performance in steel machining applications.
How Can You Optimize Spindle Performance for Steel Machining?
Optimizing spindle performance for steel machining involves several strategies:
- Proper Tool Selection: Choose tools specifically designed for steel machining and ensure they’re compatible with your spindle’s capabilities.
- Cutting Parameter Optimization: Fine-tune your cutting speeds, feed rates, and depths of cut to match your spindle’s performance characteristics.
- Vibration Monitoring: Implement a vibration monitoring system to detect and address issues before they impact machining quality.
- Thermal Management: Use appropriate coolant strategies and monitor spindle temperature to maintain thermal stability.
- Regular Calibration: Perform regular calibration checks to ensure your spindle maintains its precision over time.
By focusing on these aspects, you can maximize the performance of your spindle in steel machining applications, leading to improved productivity and part quality.In conclusion, selecting the right spindle for machining steel requires careful consideration of various factors. Here are the key points to remember:
- Consider spindle power, torque, speed range, stiffness, and cooling capabilities when choosing a spindle for steel machining.
- Balance high-speed capabilities with low-end torque for versatile steel machining operations.
- Spindle stiffness is crucial for reducing vibration and maintaining precision in steel machining.
- Effective cooling systems are essential for managing heat generation in steel machining processes.
- Different steel grades may require adjustments in spindle selection and machining parameters.
- Regular maintenance and optimization strategies can significantly enhance spindle performance and longevity in steel machining applications.
By keeping these factors in mind, you can select a spindle that will excel in your steel machining operations, improving both productivity and part quality.
- RicoCNC has a team of professionals who have been engaged in the design, production, sales, and maintenance of electro spindles for many years. Our company accepts the purchase of various types of CNC spindles.
water-cooled CNC spindle motors
Edge banding machine spindle motors.
- If you need any CNC spindle, please contact us.