Introduction
In the modern industrial field, spindle and servo motors are common and important motors. They play a key role in CNC machine tools, automation equipment, and robots. However, many people do not know the difference between these two motors. This article will discuss the difference between spindle motors and servo motors in detail from three aspects: principle, configuration, and working range, to help readers better understand and apply these two motors.
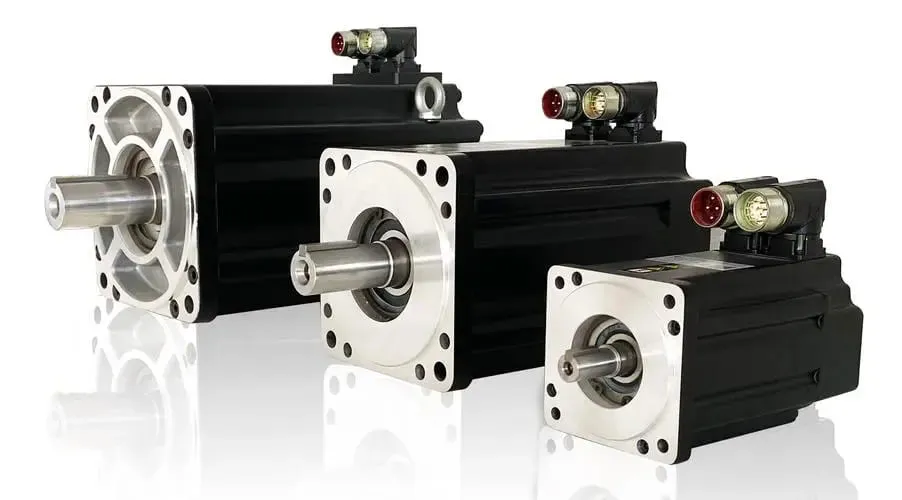
Difference in principle
The spindle motor is a high-precision asynchronous motor designed to meet the needs of various types of CNC machine tools. It has excellent dynamic characteristics and can achieve a wide range of speed regulation functions while providing precise position control. This enables the spindle motor to stably and efficiently drive the spindle to rotate during the processing process, meeting the requirements of different processing speeds and precisions.
In contrast, servo motors are mainly used to control position, speed, and torque to ensure that the mechanical system runs according to the predetermined trajectory and speed. Its core function is to move the workpiece toward the tool or the tool toward the workpiece to ensure the accuracy and stability of the processing process. The servo motor receives control signals and adjusts its output to achieve precise motion control. This high responsiveness and precision make it indispensable in high-precision positioning applications.
Differences in configuration
There are also significant differences between spindle and servo motors in structure and configuration. Spindle motors are usually used in AC servo systems, and their stator winding structure is designed to be close to a sine waveform to ensure the smoothness and stability of the current waveform. This design helps to reduce vibration and noise during motor operation and improve operating efficiency and life.
On the other hand, servo motors are mainly used in digital servo systems, and their stator winding structure is significantly different from that of spindle motors. The winding structure of servo motors is optimised to achieve fast response and high-precision control and can respond quickly and accurately to changes in control signals. This structural design gives servo motors excellent positioning and speed control performance and is suitable for various precision control occasions.
Differences in the working range
The working range of spindle motors is mainly concentrated in the constant power area between rated speed and high speed. To achieve a broader range of speed regulation functions, the rated speed of spindle motors is usually designed in a lower range. This allows the motor to maintain a stable output power at high speeds to meet the needs of different processing conditions.
Servo motors mainly operate in the constant torque area between low and rated speeds. Within this range, servo motors can provide constant torque output and maintain stable performance regardless of speed changes. This characteristic makes servo motors perform well in applications that require precise torque control and stable speed, ensuring smooth operation and high-precision control of mechanical systems.
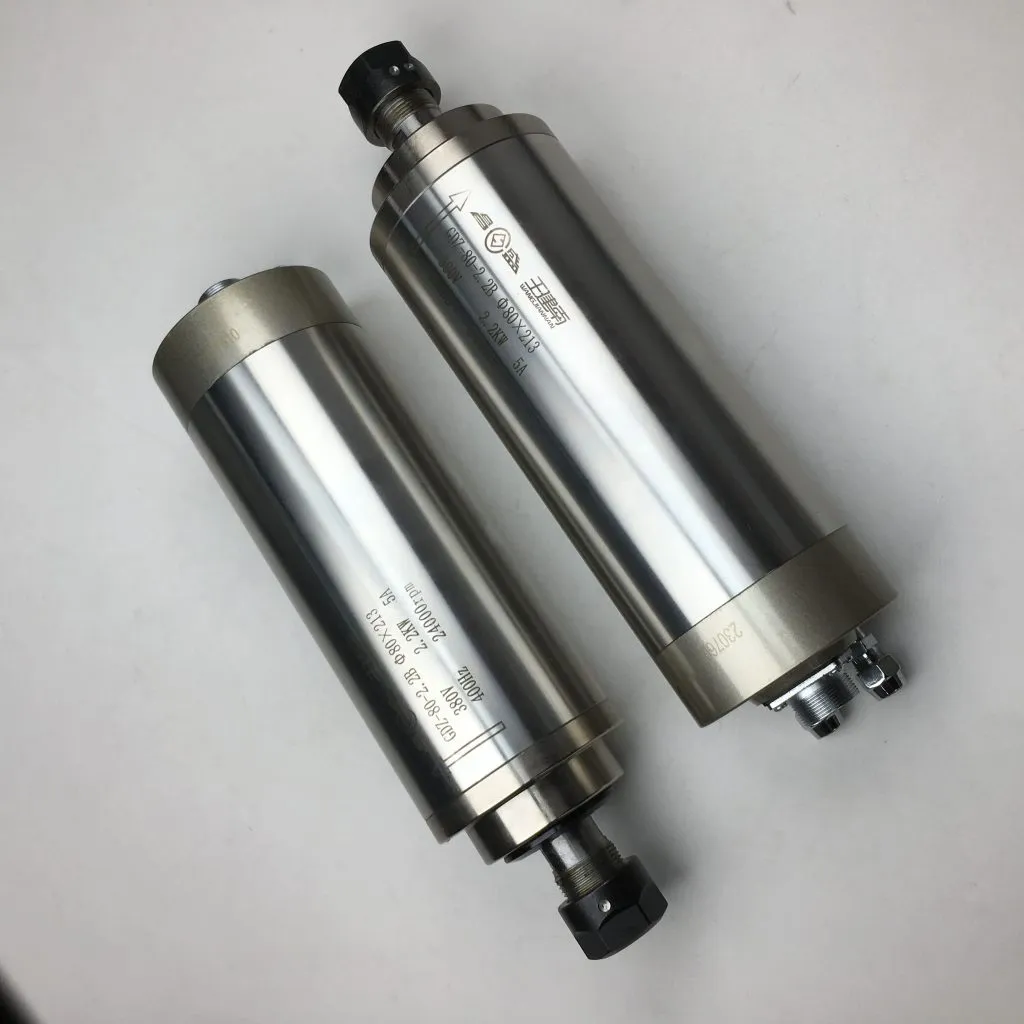
Conclusion
In summary, spindle and servo motors differ in principle, configuration, and working range. Spindle motors provide stable and efficient rotational power suitable for various processing speeds and precision requirements; servo motors focus on precise motion control to ensure that mechanical systems run according to predetermined trajectories and speeds. Understanding and correctly applying the characteristics of these two motors is essential to improving the performance and efficiency of industrial equipment.
Summary FAQ based on the article
1. What are the differences between spindle and servo motors in application areas?
Spindle motors are mainly used to drive machine tool spindles to meet different processing speed and precision requirements; servo motors are used primarily to accurately control mechanical systems’ position, speed, and torque and are widely used in automation control and robotics.
2. Why are the rated speeds of spindle motors designed to be in a lower range?
Designing the rated speed of the spindle motor within a lower range can ensure that the output power can be kept constant at high speed, thereby achieving a more comprehensive range of speed regulation functions and meeting the needs of different processing conditions.
3. How does the servo motor achieve high-precision motion control?
The servo motor accurately adjusts its output position, speed, and torque by receiving and responding to control signals. Its optimized winding structure and highly responsive design enable it to quickly and accurately execute control instructions and achieve high-precision motion control.
4. Why is the stator winding structure of the spindle motor designed to be close to a sine waveform?
This design helps to generate a smooth and stable current waveform, reduce vibration and noise during motor operation, and improve operating efficiency and equipment life.
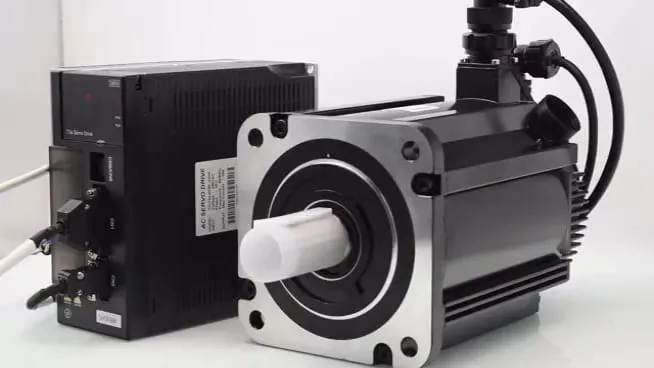
- RicoCNC has a team of professionals who have been engaged in the design, production, sales, and maintenance of electro spindles for many years. Our company accepts the purchase of various types of CNC spindles.
water-cooled CNC spindle motors
Edge banding machine spindle motors.
- If you need any CNC spindle, please contact us.