Introduction
CNC spindle drives play a vital role in precision machining processes, making the choice of motor critical for optimal performance. Selecting the right motor for the rotor axis in CNC spindle drives ensures high accuracy, smooth operation, and long-term durability. However, not all motors are suitable for this application, as certain types may fail to meet the performance demands of high-precision CNC operations. This article explores the characteristics of different motors used in CNC spindle drives and identifies which motors are unsuitable for the rotor axis of these critical systems.
What are CNC Spindle Drives?
CNC spindles are integral to modern machining processes, providing the rotational power needed for tasks such as cutting, milling, and engraving. The spindle drive, which consists of various components, including the motor, is responsible for controlling the speed and torque of the spindle. The motor that powers the spindle must be capable of delivering consistent torque at high speeds, ensuring precision in the cutting or engraving process.
Basics of CNC Spindle Operation
A CNC spindle operates by rotating a cutting tool or other device at varying speeds, depending on the material being worked on. The spindle motor is essential for achieving the desired cutting speed and torque. Whether working with wood, metal, or plastic, the spindle’s performance directly impacts the quality of the finished product. Motors designed for CNC spindles must handle varying loads, respond quickly to speed adjustments, and maintain smooth rotation.
Key Components of CNC Spindle Drives
CNC spindle drives consist of several components working together to provide precise control. Key elements include the spindle motor, motor driver, sensors for feedback control, and the mechanical transmission system. These components ensure that the spindle operates at the correct speed and torque for the specific machining task.
Types of Motors Used in CNC Spindles
CNC spindles utilize a variety of motors, each with unique characteristics that affect performance. The most common types include stepper motors, servo motors, and AC induction motors. While each motor type has its advantages, certain motors are less suited for use in CNC spindle drives due to limitations in precision, torque, or speed control.
Stepper Motors and Their Characteristics
Stepper motors are widely used in CNC applications due to their simplicity, affordability, and ability to provide precise control. They move in discrete steps, making them ideal for applications where low to moderate precision is acceptable. However, stepper motors can struggle with maintaining torque at high speeds, which may limit their suitability for high-performance CNC spindles.
Servo Motors and Their Advantages
Servo motors are preferred for CNC spindles because they offer higher precision and faster response times compared to stepper motors. They operate using feedback loops, ensuring accurate position control and smooth operation, even at high speeds. Servo motors also provide more consistent torque, making them ideal for demanding applications such as CNC milling or engraving.
Limitations of AC Induction Motors
AC induction motors are commonly used in industrial machinery due to their robustness and efficiency. However, they have limited precision control and may not respond quickly to changes in load or speed. These limitations make AC induction motors less suitable for CNC spindle applications, where high precision and responsiveness are critical.
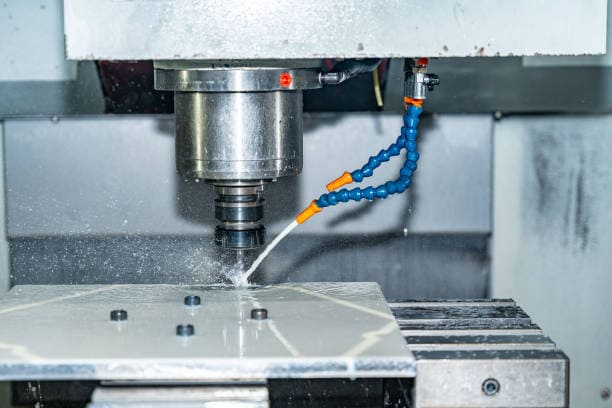
The Unsuitability of Certain Motors for CNC Spindle Drives
While several motor types can be used in CNC spindles, not all are equally effective. Some motors lack the necessary control over speed, torque, and precision, making them unsuitable for high-performance CNC spindle applications. Universal motors, for example, are often excluded from CNC spindle designs due to their inability to provide consistent, high-precision performance.
Why Universal Motors Are Not Preferred
Universal motors, which can operate on either AC or DC power, are typically used in consumer appliances and tools. Although they offer high-speed operation, they are not suitable for CNC spindles due to their lack of precision control. Universal motors generate significant heat and wear out quickly under continuous use, making them unreliable for the rigorous demands of CNC machining.
Characteristics of Unsuitable Motors
Motors that are unsuitable for CNC spindle drives typically lack the necessary torque, speed control, or precision required for high-accuracy applications. Motors with slow response times or those that cannot maintain consistent performance at high speeds often struggle in CNC environments. This is especially true for tasks involving detailed engraving or milling, where any deviation in motor performance can result in poor-quality finishes.
Factors to Consider When Choosing a Motor for CNC Spindle Drives
Choosing the right motor for a CNC spindle drive involves evaluating several key factors, including speed, torque, precision, and compatibility with the CNC machine. Selecting the wrong motor can lead to inefficiencies, poor-quality work, and even damage to the spindle.
Speed Requirements and Precision Control
One of the most important factors to consider when selecting a motor for a CNC spindle drive is the speed range required for your application. High-speed operations, such as engraving or fine cutting, require motors capable of maintaining consistent performance across a wide range of RPMs. Precision control is equally important, as it ensures that the motor can make minute adjustments to maintain accuracy during the machining process.
Torque and Power Output Considerations
The torque output of the motor is another critical factor. Motors used in CNC spindle drives must provide sufficient torque to handle various materials without stalling or losing speed. Power output, measured in kilowatts (kW), is also important, as it determines how effectively the motor can drive the spindle under load. For example, a multi-spindle CNC machine will require a motor with higher power output compared to a smaller CNC router spindle motor.
The Role of Motors in CNC Spindle Functionality
The motor in a CNC spindle drive is responsible for translating electrical energy into mechanical motion, powering the cutting tool. The motor’s ability to handle varying loads, maintain precise speed control, and deliver consistent torque is essential for achieving high-quality machining results. Motors that fail to meet these criteria are unsuitable for CNC spindle drives.
Why Certain Motors Fail in High-Precision Applications
High-precision CNC applications, such as engraving intricate designs or milling complex parts, place extreme demands on the spindle motor. Motors that cannot provide the necessary accuracy, response time, or torque output will fail to deliver the desired results. Motors that exhibit excessive vibration, overheating, or poor feedback control are particularly prone to failure in these environments.
Stepper Motors: Affordable but Limited in Performance
While stepper motors are an affordable option for CNC spindles, they have several limitations that make them less suitable for high-precision applications. Stepper motors lack the ability to provide feedback on their position, making them less accurate than servo motors. Additionally, stepper motors lose torque at higher speeds, which can result in inconsistent performance during demanding machining tasks.
Servo Motors and Their Advantages for Precision Control
Servo motors are the preferred choice for high-precision CNC spindle drives due to their superior performance and accuracy. They provide real-time feedback on position and speed, allowing for precise adjustments during operation. Servo motors also maintain consistent torque across a wide range of speeds, making them ideal for both light and heavy-duty CNC applications.
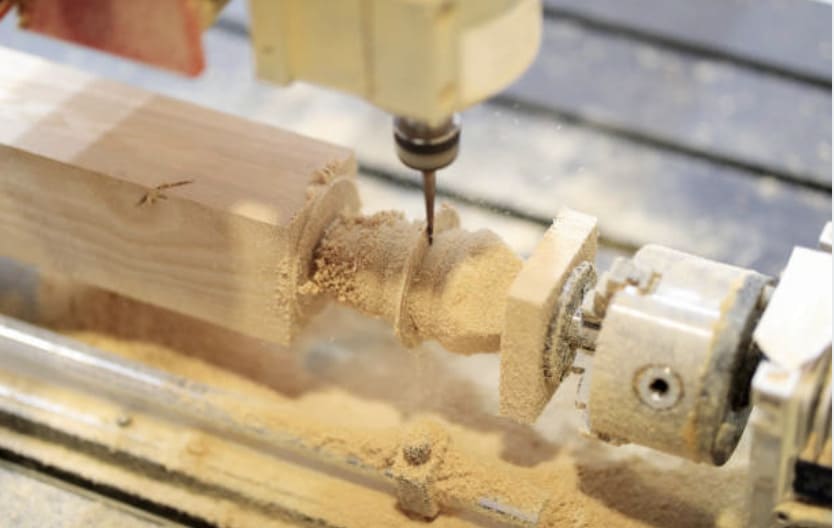
Conclusion
Selecting the right motor for a CNC spindle drive is crucial for ensuring optimal performance, precision, and longevity. While several motor types are available, not all are suitable for high-precision CNC applications. Universal motors, for example, are typically unsuitable for CNC spindles due to their lack of precision and durability. When choosing a motor, factors such as speed control, torque, and power output must be considered to ensure that the spindle can handle the demands of the specific machining task. By selecting the right motor, CNC operators can achieve smoother operation, higher-quality finishes, and greater overall efficiency.
FAQ
- What makes a motor unsuitable for the rotor axis of CNC spindle drives? Motors that lack precision control, such as universal motors, are unsuitable for CNC spindle drives due to their inability to maintain accurate speed and torque.
- Can stepper motors be used for any CNC spindle applications? Stepper motors can be used in low to moderate precision applications, but they may struggle with maintaining torque at high speeds, making them less suitable for demanding tasks.
- How do servo motors enhance CNC spindle performance? Servo motors provide real-time feedback on position and speed, allowing for precise adjustments and consistent torque, making them ideal for high-precision CNC applications.
- Are there alternatives to conventional motors for CNC spindles? Yes, direct-drive motors and linear motors are alternatives that offer higher precision and responsiveness, but they can be more expensive and complex to implement.
- What should be considered when choosing a motor for CNC spindle drives? Key considerations include speed control, torque output, power requirements, and compatibility with the CNC machine’s spindle system.
Key Takeaways
- Select a motor that meets the speed, torque, and precision requirements of your CNC spindle drive.
- Avoid universal motors for high-precision applications due to their lack of control and durability.
- Consider servo motors for superior precision and consistent performance across a wide range of speeds.
- Ensure that the motor is compatible with the specific CNC machine and the materials being worked on.
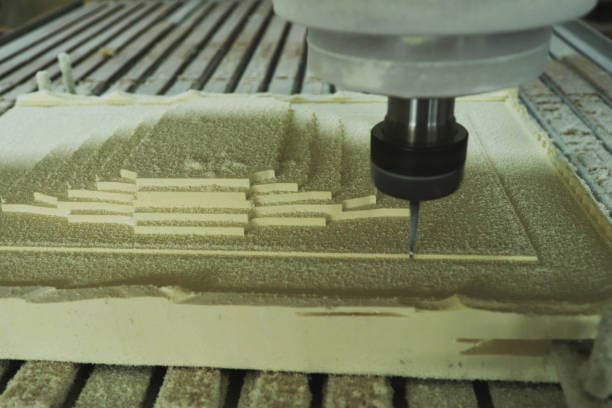
- RicoCNC has a team of professionals who have been engaged in the design, production, sales, and maintenance of electro spindles for many years. Our company accepts the purchase of various types of CNC spindles.
water-cooled CNC spindle motors
Edge banding machine spindle motors.
- If you need any CNC spindle, please contact us.