Understanding CNC Spindle Rotation: Why Does It Matter?
When it comes to CNC spindle operation, spindle direction is a crucial factor that can determine the success or failure of a project. Whether you’re a seasoned machinist or new to CNC machines, understanding the basics of spindle rotation is essential. This article explores everything you need to know about spindle direction, including factors influencing it, tips for optimal performance, and avoiding common mistakes.
So, why is this article worth reading? Spindle rotation can affect everything from material finish to tool lifespan, and knowing how to adjust it can significantly improve your CNC operations. By the end, you’ll have practical insights to enhance precision and efficiency in your projects.
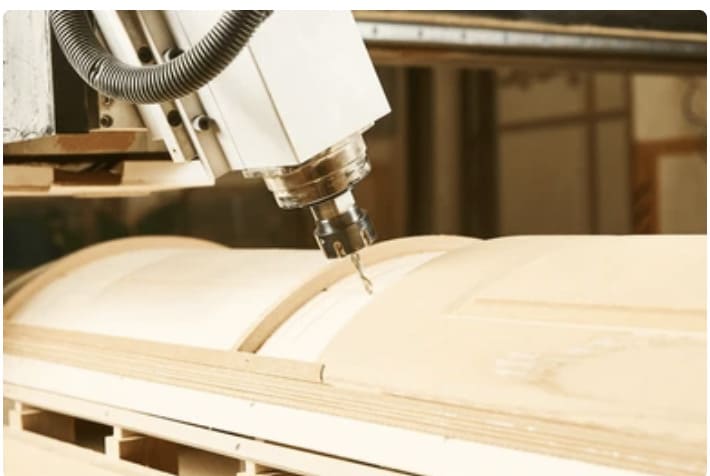
The Basics of Spindle Orientation
Before diving into the intricacies of spindle direction, it’s essential to understand the basics. CNC spindles are responsible for rotating cutting tools and determining the efficiency and precision of the cuts. Spindles can rotate clockwise (CW) or counterclockwise (CCW), and each direction serves specific functions based on the type of tool and material used.
Spindle orientation is one of the first considerations during CNC programming because it directly affects the quality of the cut and the durability of the tool. A general rule of thumb is to match the spindle rotation with the tool’s cutting edge for the best results.
Clockwise vs. Counterclockwise Spinning
So, which way should your CNC spindle spin? Most CNC machines default to clockwise rotation, which is ideal for right-hand cutting tools. However, certain operations and materials may require a counterclockwise rotation for better efficiency.
For example, counterclockwise rotation is preferred for left-hand tools or for reducing tear-out on specific materials. Understanding the appropriate direction for your specific operation can improve both speed and accuracy.
“Always ensure your spindle rotation aligns with the cutting tool’s design. Incorrect orientation can damage tools and compromise project quality.”
Material Type and Its Impact on Spindle Direction
The type of material you’re working with can significantly influence the spindle direction. Softer materials like wood may allow for more flexibility in spindle rotation, whereas harder materials like steel often require specific rotations to ensure precision and avoid damage.
For example, when cutting metal, it’s crucial to use the correct spindle direction to prevent overheating and excessive tool wear. On the other hand, plastics may require counterclockwise spinning to minimize chipping and achieve a smooth finish.
Tooling Considerations for Optimal Spindle Performance
Tooling considerations are closely tied to spindle direction. When selecting tools, always ensure they are designed for the intended spindle rotation. Some tools are built for clockwise motion, while others are specifically designed for counterclockwise.
Additionally, multi-axis machines may involve simultaneous rotations in different directions, depending on the complexity of the cuts. Using the wrong tool or setting can lead to poor results, increased tool wear, and even machine failure.
Tool Type | Recommended Rotation | Materials Best Suited |
---|---|---|
Right-Hand Tools | Clockwise | Wood, Aluminum |
Left-Hand Tools | Counterclockwise | Plastics, Fiberglass |
Multi-Axis Tools | Varies | Complex Metal Projects |
Differentiating Between Edge Banding and CNC Routing
Edge banding and CNC routing are two distinct processes that often require different spindle directions. In edge banding, the goal is to apply a thin strip of material to the edge of a workpiece, and spindle direction plays a crucial role in ensuring a tight bond.
In contrast, CNC routing involves cutting or engraving a material and may require a different spindle orientation based on the tool type and material. In some cases, edge banding uses counterclockwise rotation to minimize tearing, while CNC routing often sticks to a clockwise direction for general cutting.
Adjusting Spindle Direction for Edge Banding Efficiency
Efficiency in edge banding is largely determined by the correct spindle orientation. Since edge banding involves applying thin strips to the edges of materials, the spindle’s rotation affects how well the material adheres. Adjusting spindle direction to match the grain or pattern of the material ensures a clean, durable bond.
For instance, rotating the spindle counterclockwise might reduce the likelihood of fraying or tearing on laminated edges, offering a smoother finish and better adhesion.
How Speed and Torque Affect Spindle Direction
Speed and torque are critical elements that influence spindle direction. When operating a CNC machine, adjusting the spindle speed (measured in RPM) and the torque can affect the efficiency of the cuts. Higher speeds may require different spindle orientations to ensure that the material is cut smoothly without burning or chipping.
For example, when cutting hard materials like metals, a slower spindle speed with a clockwise rotation often produces the best results, whereas higher speeds with counterclockwise rotation might be ideal for softer materials like plastics.
Programming CNC Machines for Desired Spindle Direction
Programming your CNC machine for the correct spindle direction is essential for ensuring optimal performance. CNC programs use commands like M03 (clockwise) and M04 (counterclockwise) to control the spindle’s rotation.
Command | Function |
---|---|
M03 | Clockwise Spin |
M04 | Counterclockwise |
M05 | Stop Spindle |
Routine Checks to Ensure Correct Spindle Direction
Routine checks are essential to ensure that your CNC machine’s spindle is operating in the correct direction. One of the easiest ways to verify spindle direction is by conducting a manual test before starting a project. This simple step can prevent catastrophic tool failures and costly material wastage.
Checking the spindle direction as part of your maintenance routine also helps to spot potential issues early on. Regularly inspecting the machine and testing spindle rotation can reduce downtime and improve overall project efficiency.
Safety Measures to Prevent Accidents During Spindle Reversal
Safety should always be a priority when working with CNC machines. Reversing spindle direction mid-operation can lead to accidents or damage if not done carefully. Before adjusting the spindle direction, ensure the machine is fully stopped, and always follow manufacturer guidelines to avoid injury.
Additionally, implementing safety features like automatic shutoff systems and spindle locks can help prevent accidents during spindle reversal, especially in complex projects where multiple spindle orientations are required.
“Safety isn’t optional—it’s essential. Always double-check spindle direction settings and stop the machine before making adjustments.”
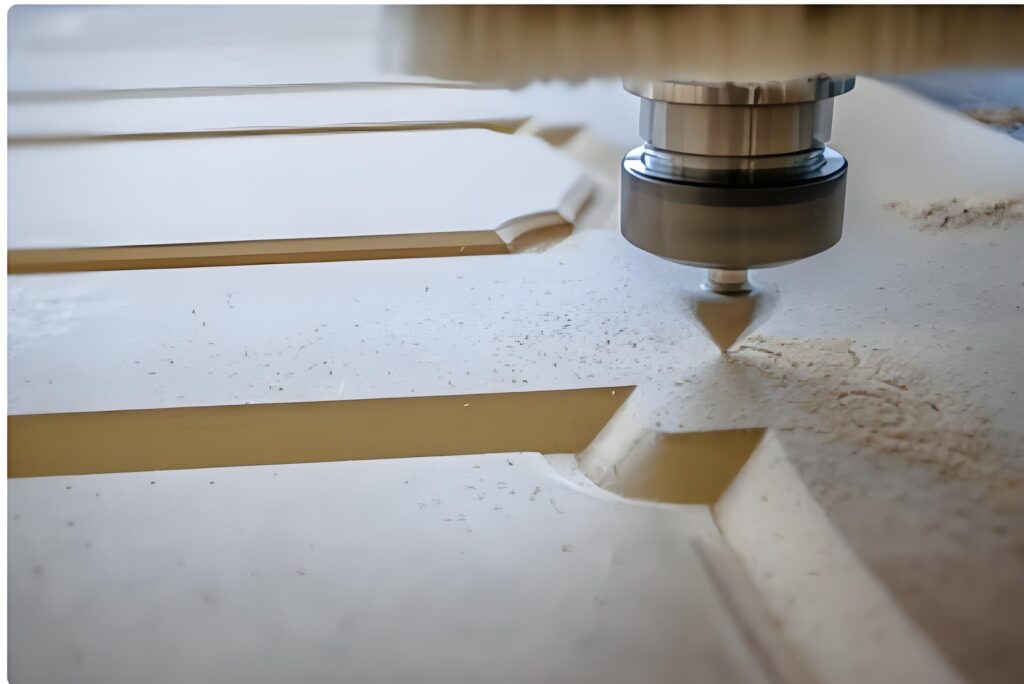
Key Takeaways:
- Spindle direction plays a significant role in tool life, material finish, and overall project quality.
- Clockwise rotation is generally used for right-hand tools, while counterclockwise rotation suits left-hand tools and certain materials.
- Material type and tooling considerations are crucial in determining the appropriate spindle orientation.
- Regular maintenance checks and following safety protocols can prevent accidents and ensure optimal spindle performance.
- Proper CNC programming using commands like M03 and M04 is necessary to achieve the desired spindle direction.
By understanding the intricacies of spindle direction, you’ll not only improve the efficiency of your CNC machine but also achieve better results in your projects.
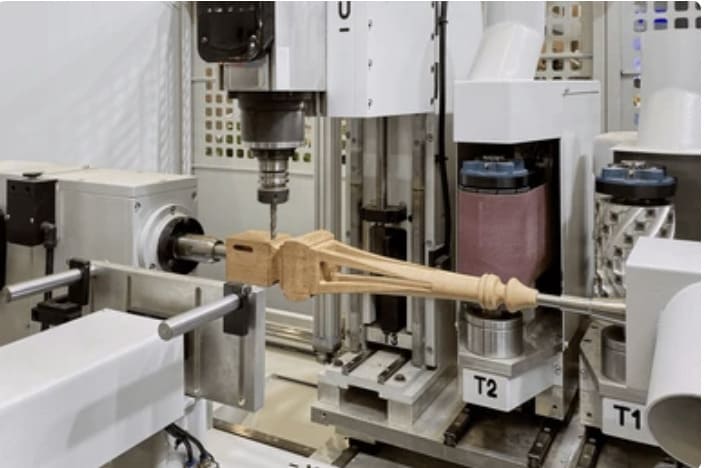
- RicoCNC has a team of professionals who have been engaged in the design, production, sales, and maintenance of electro spindles for many years. Our company accepts the purchase of various types of CNC spindles.
water-cooled CNC spindle motors
Edge banding machine spindle motors.
- If you need any CNC spindle, please contact us.